Weigh-in-motion technology is ensuring increasingly accurate, and flexible, weighing stations. Weigh-in-motion specialist manufacturer Axtec says that its space-saving dynamic weighbridge is accurate to within ±0.5% and is the most precise system in the world. From its Runcorn, UK manufacturing facility, Axtec undertakes research and development of new technologies, as well as software testing, fabrication, construction and installation of WIM products.
Axtec’s axle weighing platform design is intended f
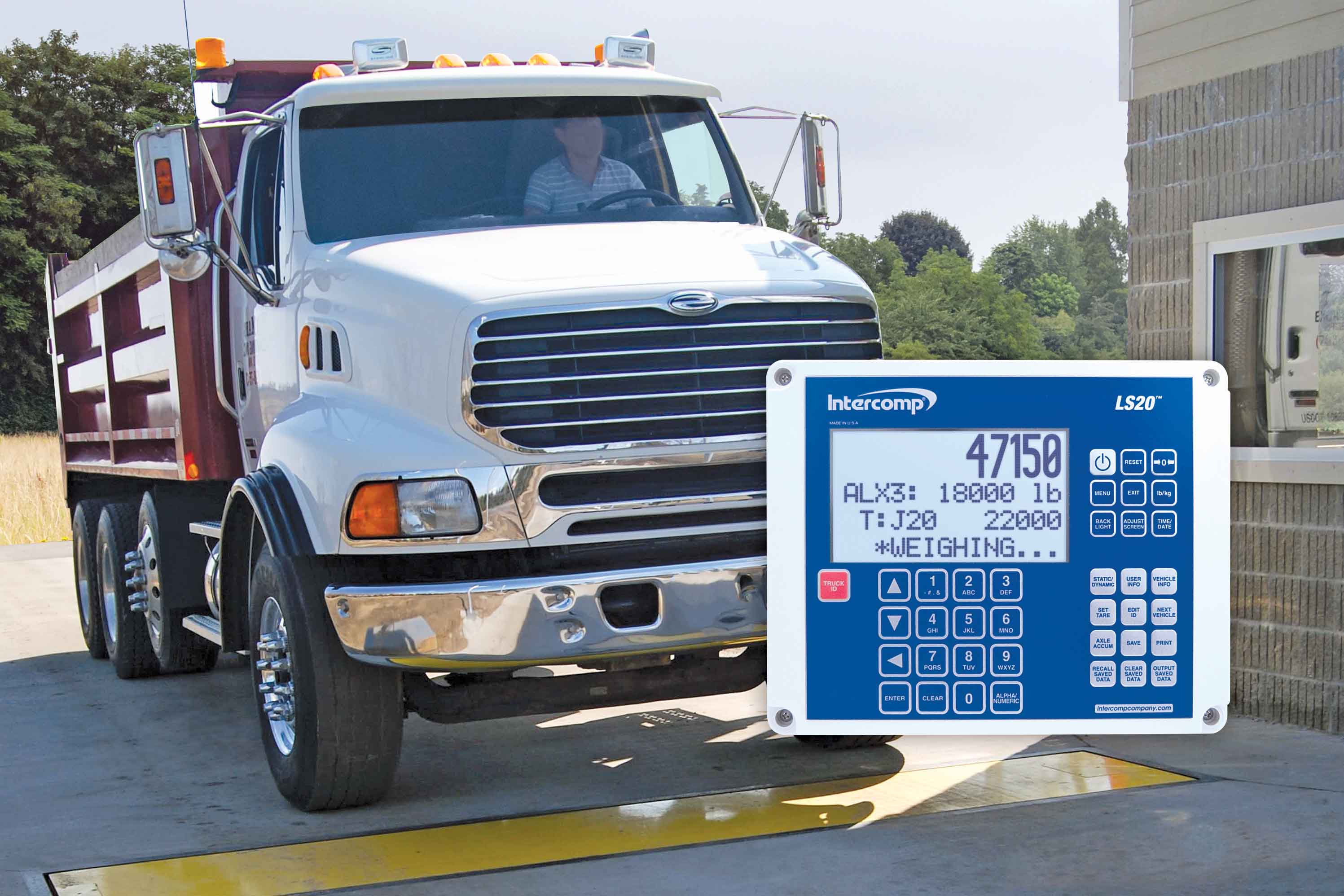
The complete WIM package from Intercomp
Weigh-in-motion technology is ensuring increasingly accurate, and flexible, weighing stations
Weigh-in-motion specialist manufacturer7542 Axtec says that its space-saving dynamic weighbridge is accurate to within ±0.5% and is the most precise system in the world.
From its Runcorn, UK manufacturing facility, Axtec undertakes research and development of new technologies, as well as software testing, fabrication, construction and installation of WIM products.
Axtec’s axle weighing platform design is intended for 40 years or more of operation, according to the company. The dynamic weighbridge weighs vehicles as they drive slowly over the platform to remove the weight transfers that stopping and starting can have on compensating axles. Axtec’s dynamic weighbridge produces results to within ± 0.5 per cent accuracy in less than 40 seconds.
Their systems use touchscreen and wireless technology.
Axtec is also the sole contractor to the UK’s DVSA – Driver and Vehicle Standards Agency – for the calibration, certification and maintenance of its national network of enforcement axle weighbridges. The majority of the DVSA weighbridges are Axtec dynamic weighbridges, according to the company.
Complimentary products from the company include its axle load indicator. Multidrop loads, with their constantly changing weight distribution, can easily catch drivers out leaving them at risk of an overloaded axle.
The firm's OnBoard Axle Load Indicators solve this problem by constantly displaying axle and gross weights throughout the day. This allows drivers to distribute their loads safely and legally at all times.
From light vans to 32tonne vehicles, the simple colour-coded display has no manual controls which means no driver training is needed and there is no chance of accidental breakage. Optional outputs are available, such as vehicle tracking systems and data storage.
In Canada, International Road Dynamics has upgraded its SAW wheel load scale for dynamic weighing.
The SAW III portable dynamic scale system has user-friendly software making it possible to efficiently pre-select overloaded trucks.
Two SAW scales are paired and connected with a PC via Bluetooth. The vehicle drives over the scales at slow speed and the weighing result - wheel/axle weights and gross vehicle weight - is displayed on the screen.
For weight enforcement with the highest accuracy the system can be switched to static operation mode.
The system guarantees high vehicle throughput, especially when using two sets of SAW scales. One is set in dynamic mode for preselection and one is in static mode for weight enforcement.
Features of the rugged and corrosion-resistant lightweight system include a low physical profile, twin-tyre weighing and a flex frame for higher accuracy. It is also designed to meet OIML R134 applications – Organisation Internationale de Métrologie Légale/International Organisation of Legal Metrology.
248 IRD, based in Saskatoon in western Canada, showcased the SAW III, as well as its latest VectorSense sensor technology, at the Intertraffic Exhibition in Amsterdam in April.
The VectorSense tyre sensor suite is an in-road sensor technology that provides vehicle position and individual tyre footprint data for use in traffic data collection programmes, commercial vehicle operations and toll road operations. It provides previously unavailable vehicle and traffic data including lane position information, single/dual and super single tyre measurement and identification of low pressure tyres, all at highway speed.
Recent contract wins for IRD include a five-year, US$4.8 million traffic data collection maintenance and upgrade deal with the New York State Department of Transportation.
IRD is installing, upgrading, repairing, operating and maintaining the state’s permanent data collection sites in Metro New York City, Nassau, Suffolk, Rockland and Westchester Counties.
Permanent data collection sites are comprised of fixed in-road instrumentation used to monitor traffic. The majority of the sites have IRD data collection equipment. The department of transportation uses these sites to collect, summarise and interpret information about the traffic travelling on the highways. The data is used to assess transportation needs and infrastructure performance, as well as to develop planning and programming recommendations. Data is required for route planning, safety programmes, the designation of evacuation routes and their management and the design of highway projects.
Terry Bergan, IRD president and chief executive, said the company has participated in similar traffic data services agreements with New York State in the past decade.
Over in the US, the American-made LS-WIM axle scale systems from1315 Intercomp are now NTEP Certified, making them legal for trade when weighing in static mode.
The US’s National Conference on Weights and Measures issues an NTEP Certificate of Conformance following successful completion of an evaluation of a device. That means the device can meet all the requirements in Handbook 44 from the National Institute of Standards and Technology.
Intercomp says that its LS-WIM Axle Scale Systems are known for being more efficient and cost-effective alternative to older full-size truck scales.
Intercomp has also released a purpose-built indicator, the LS20, for its WIM scale systems. The company said that a key factor in designing the new LS20 was the LS-WIM scale’s ability to weigh axle-by-axle dynamically - in-motion – and statically.
The LS20 features an easy-to-read LCD display and intuitive keypad design. It can be mounted where it allows drivers to enter and save 250 unique truck IDs complete with tare weights, individual axle weights and total gross weight. Internal memory stores up to 3,000 weigh records and the data can be exported via a USB drive or RS232 serial output creating a complete, automated manned or unmanned weigh station.
LS-WIM axle scales have been successfully used around the world for over 10 years and feature NTEP certified strain gauge load cell technology; the same type of load cells used in full length truck scales, but require a much smaller footprint and are far more cost-effective to purchase, maintain and install. Additionally, the compact American-made axle scale systems feature a removable deck for ease of maintenance.
“A key benefit of this system is that it allows users to collect individual axle weights to identify overweight axles or monitor inventory levels in entry/exit gate applications,” said Aaron Van Heel, marketing manager at Intercomp. “Intercomp’s Axle Scale System can also be tied in with an optional outdoor wireless printer and a LED display scoreboard with an integrated stop and go light.
IntercompWIM software is available to further automate the weighing process for long term data collection and analysis.
Weigh-in-motion specialist manufacturer
From its Runcorn, UK manufacturing facility, Axtec undertakes research and development of new technologies, as well as software testing, fabrication, construction and installation of WIM products.
Axtec’s axle weighing platform design is intended for 40 years or more of operation, according to the company. The dynamic weighbridge weighs vehicles as they drive slowly over the platform to remove the weight transfers that stopping and starting can have on compensating axles. Axtec’s dynamic weighbridge produces results to within ± 0.5 per cent accuracy in less than 40 seconds.
Their systems use touchscreen and wireless technology.
Axtec is also the sole contractor to the UK’s DVSA – Driver and Vehicle Standards Agency – for the calibration, certification and maintenance of its national network of enforcement axle weighbridges. The majority of the DVSA weighbridges are Axtec dynamic weighbridges, according to the company.
Complimentary products from the company include its axle load indicator. Multidrop loads, with their constantly changing weight distribution, can easily catch drivers out leaving them at risk of an overloaded axle.
The firm's OnBoard Axle Load Indicators solve this problem by constantly displaying axle and gross weights throughout the day. This allows drivers to distribute their loads safely and legally at all times.
From light vans to 32tonne vehicles, the simple colour-coded display has no manual controls which means no driver training is needed and there is no chance of accidental breakage. Optional outputs are available, such as vehicle tracking systems and data storage.
In Canada, International Road Dynamics has upgraded its SAW wheel load scale for dynamic weighing.
The SAW III portable dynamic scale system has user-friendly software making it possible to efficiently pre-select overloaded trucks.
Two SAW scales are paired and connected with a PC via Bluetooth. The vehicle drives over the scales at slow speed and the weighing result - wheel/axle weights and gross vehicle weight - is displayed on the screen.
For weight enforcement with the highest accuracy the system can be switched to static operation mode.
The system guarantees high vehicle throughput, especially when using two sets of SAW scales. One is set in dynamic mode for preselection and one is in static mode for weight enforcement.
Features of the rugged and corrosion-resistant lightweight system include a low physical profile, twin-tyre weighing and a flex frame for higher accuracy. It is also designed to meet OIML R134 applications – Organisation Internationale de Métrologie Légale/International Organisation of Legal Metrology.
The VectorSense tyre sensor suite is an in-road sensor technology that provides vehicle position and individual tyre footprint data for use in traffic data collection programmes, commercial vehicle operations and toll road operations. It provides previously unavailable vehicle and traffic data including lane position information, single/dual and super single tyre measurement and identification of low pressure tyres, all at highway speed.
Recent contract wins for IRD include a five-year, US$4.8 million traffic data collection maintenance and upgrade deal with the New York State Department of Transportation.
IRD is installing, upgrading, repairing, operating and maintaining the state’s permanent data collection sites in Metro New York City, Nassau, Suffolk, Rockland and Westchester Counties.
Permanent data collection sites are comprised of fixed in-road instrumentation used to monitor traffic. The majority of the sites have IRD data collection equipment. The department of transportation uses these sites to collect, summarise and interpret information about the traffic travelling on the highways. The data is used to assess transportation needs and infrastructure performance, as well as to develop planning and programming recommendations. Data is required for route planning, safety programmes, the designation of evacuation routes and their management and the design of highway projects.
Terry Bergan, IRD president and chief executive, said the company has participated in similar traffic data services agreements with New York State in the past decade.
Over in the US, the American-made LS-WIM axle scale systems from
The US’s National Conference on Weights and Measures issues an NTEP Certificate of Conformance following successful completion of an evaluation of a device. That means the device can meet all the requirements in Handbook 44 from the National Institute of Standards and Technology.
Intercomp says that its LS-WIM Axle Scale Systems are known for being more efficient and cost-effective alternative to older full-size truck scales.
Intercomp has also released a purpose-built indicator, the LS20, for its WIM scale systems. The company said that a key factor in designing the new LS20 was the LS-WIM scale’s ability to weigh axle-by-axle dynamically - in-motion – and statically.
The LS20 features an easy-to-read LCD display and intuitive keypad design. It can be mounted where it allows drivers to enter and save 250 unique truck IDs complete with tare weights, individual axle weights and total gross weight. Internal memory stores up to 3,000 weigh records and the data can be exported via a USB drive or RS232 serial output creating a complete, automated manned or unmanned weigh station.
LS-WIM axle scales have been successfully used around the world for over 10 years and feature NTEP certified strain gauge load cell technology; the same type of load cells used in full length truck scales, but require a much smaller footprint and are far more cost-effective to purchase, maintain and install. Additionally, the compact American-made axle scale systems feature a removable deck for ease of maintenance.
“A key benefit of this system is that it allows users to collect individual axle weights to identify overweight axles or monitor inventory levels in entry/exit gate applications,” said Aaron Van Heel, marketing manager at Intercomp. “Intercomp’s Axle Scale System can also be tied in with an optional outdoor wireless printer and a LED display scoreboard with an integrated stop and go light.
IntercompWIM software is available to further automate the weighing process for long term data collection and analysis.