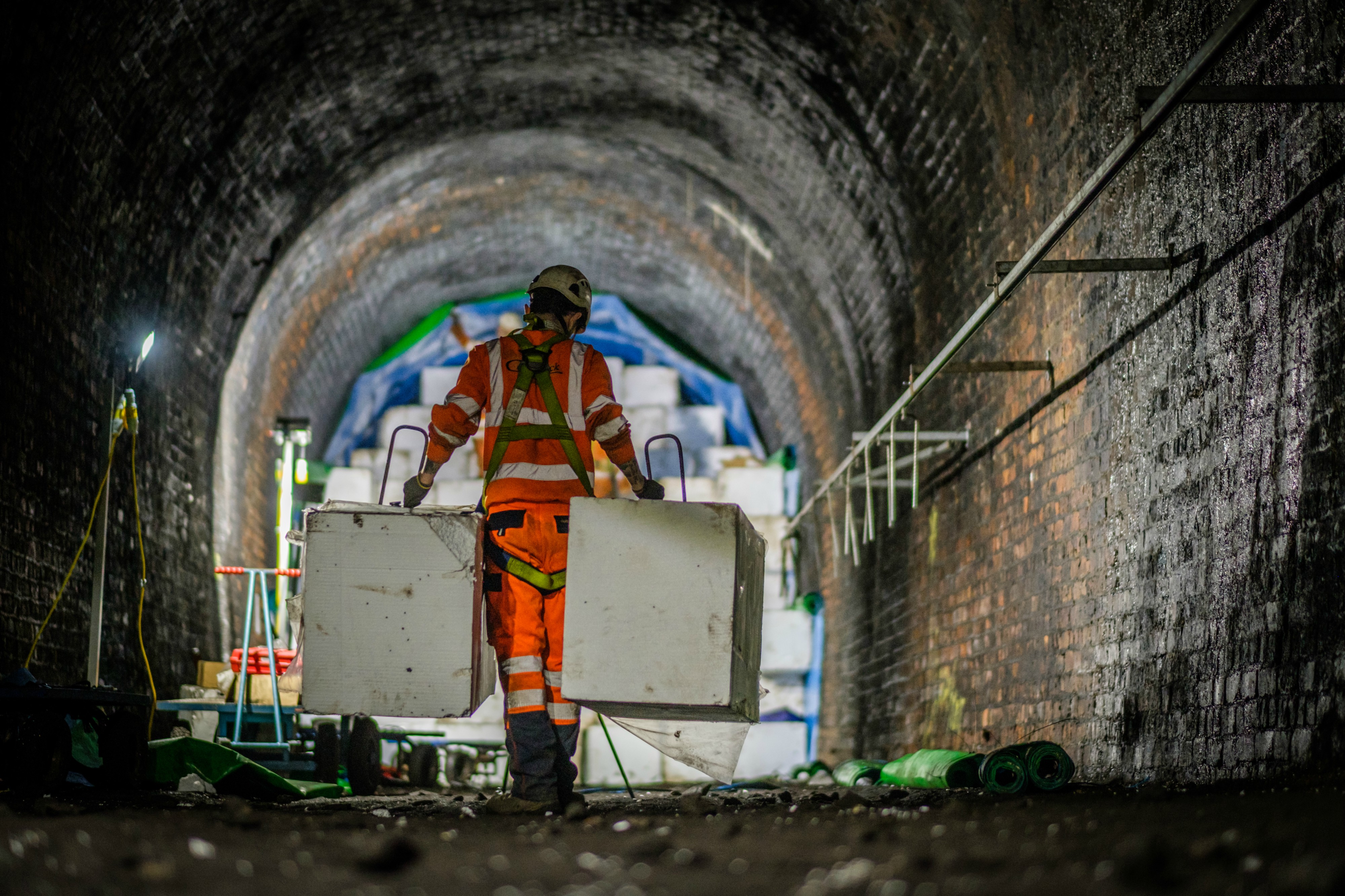
The 420m tunnel was part of the Dunfermline to North Queensferry railway line that provided a link to the ferry service until the opening of the Forth Bridge in 1890. The 4.3m-wide and 5.1m-high tunnel with vaulted roof and brick lining continued in use for freight until 1954.
The tunnel runs underneath the A9000 and B981 on the northern approach to the Forth Road Bridge. Both tunnel ends had been sealed and the adjacent cuttings filled in, leaving a vertical shaft at each end as the only access points.
An
Two options were considered: an ongoing programme of inspection and maintenance or a one-off project to infill the tunnel with a low-cost material. The infill option was chosen because it would eliminate the need for future inspections or maintenance making it the more cost-effective solution in the long term.
After considering workforce safety, overall cost and the need to avoid disruption to the local community, it was decided to fill the tunnel with expanded polystyrene (EPS) blocks. These were manufactured to a specific compressive strength capable of resisting the weight of rock and tunnel lining in the event of a localised structural failure.
The EPS blocks were pre-cut to a size and weight to facilitate easy manual handling on-site. This allowed work to be carried out from the access shaft at the north end of the tunnel which would keep construction traffic out of the village of North Queensferry for the majority of the work.
Another advantage of the lightweight blocks was that they could be delivered in large lorryloads, significantly reducing the number of required vehicle movements.
Once offloaded, the blocks were passed down the access shaft and transported along the tunnel to the work face hooked onto a specially designed sliding monorail system.
The tunnel was first lined with a hydrocarbon-resistant membrane. Then 21,342 EPS blocks were literally walked into place and arranged to allow safe working at height.
Once the tunnel was infilled, the access shafts were filled with concrete to seal the tunnel and prevent damage to the blocks.
The job was completed by late March, said Mark Arndt, Amey’s operating company representative for the Forth Bridges Unit. “This has been an unusual project,” he said. “It’s a real measure of success that most local residents were not even aware this work was taking place, despite the tunnel emerging within metres of homes in North Queensferry.”
Before sealing the access shafts, local primary schoolchildren filled two time capsules with items of their choice which were then buried among the blocks. Unlike concrete or aggregate material, EPS blocks are easily removed if the tunnel needs to be reopened.