A US contractor has employed equipment from Guntert & Zimmerman to help carry out a runway rebuild at Detroit Metro Airport
The busy airport handles around 30 million passengers/year and the project had to be carried out in a tight timeframe as a result, with the paving crew working 16 hours/day to meet the schedule.
Ajax Construction has been using its G&Z S850 paver for the work, which was needed as the existing concrete surface on runway 4L/22R had suffered from an alkali silica reaction (ASR). The
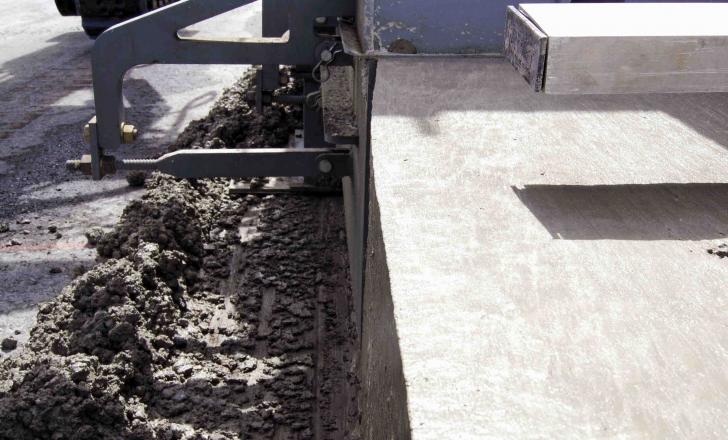
Equipment from G&Z has been used to rebuild a runway suffering from alkali silica reaction
A US contractor has employed equipment from 225 Guntert & Zimmerman to help carry out a runway rebuild at Detroit Metro Airport
The busy airport handles around 30 million passengers/year and the project had to be carried out in a tight timeframe as a result, with the paving crew working 16 hours/day to meet the schedule.
Ajax Construction has been using its G&Z S850 paver for the work, which was needed as the existing concrete surface on runway 4L/22R had suffered from an alkali silica reaction (ASR). The 3km long by 46m wide runway had to be replaced, using a total of 170,438m3 of PCC concrete. The 457mm of crushed aggregate base for the concrete runway was retained however as the base for the new concrete surface. The paver was used along with texture cure equipment from218 GOMACO and Guntert & Zimmerman for the project as well as 2122 Trimble stringless machine control technology, so as to ensure the surface would meet the tight specifications of the runway project.
The runway was closed for the work and the old concrete was milled out to a depth of 432mm, along with 75mm of the 228m bituminous base underneath, leaving the 457mm crushed aggregate base untouched. Paving was carried out in multiple passes to a width of 5.7m, with 510mm dowel bars also being used. The project also called for full depth reclamation of the asphalt shoulders and their aggregate base structures, and their replacement with new layers. New 127mm deep asphalt shoulders were constructed on top of 228mm aggregate base structures on either side of the runway, along with underdrain improvements to optimise water removal after heavy rain showers.
Other work included installing new, high efficiency LED runway lighting for the resurfaced runway as well as new markings and security fencing.
There is still a portion of the work for the airport to be carried out in 2017 and this will involve additional paving for some taxiways and parking areas.
The busy airport handles around 30 million passengers/year and the project had to be carried out in a tight timeframe as a result, with the paving crew working 16 hours/day to meet the schedule.
Ajax Construction has been using its G&Z S850 paver for the work, which was needed as the existing concrete surface on runway 4L/22R had suffered from an alkali silica reaction (ASR). The 3km long by 46m wide runway had to be replaced, using a total of 170,438m3 of PCC concrete. The 457mm of crushed aggregate base for the concrete runway was retained however as the base for the new concrete surface. The paver was used along with texture cure equipment from
The runway was closed for the work and the old concrete was milled out to a depth of 432mm, along with 75mm of the 228m bituminous base underneath, leaving the 457mm crushed aggregate base untouched. Paving was carried out in multiple passes to a width of 5.7m, with 510mm dowel bars also being used. The project also called for full depth reclamation of the asphalt shoulders and their aggregate base structures, and their replacement with new layers. New 127mm deep asphalt shoulders were constructed on top of 228mm aggregate base structures on either side of the runway, along with underdrain improvements to optimise water removal after heavy rain showers.
Other work included installing new, high efficiency LED runway lighting for the resurfaced runway as well as new markings and security fencing.
There is still a portion of the work for the airport to be carried out in 2017 and this will involve additional paving for some taxiways and parking areas.