Juniper, spruce, cranberry, cottonwood and rose. Most people think of pine trees and berries amid beautiful country fields. But for one contractor based just below the Arctic Circle in the US state of Alaska, the names represent a successful job completed using machine control. Valley General Construction recently finished a US$350,000 contract for the upgrading of country roads in the local borough of Matanuska-Susitna. The colourful names belong to roads in a heavily wooded residential subdivision located
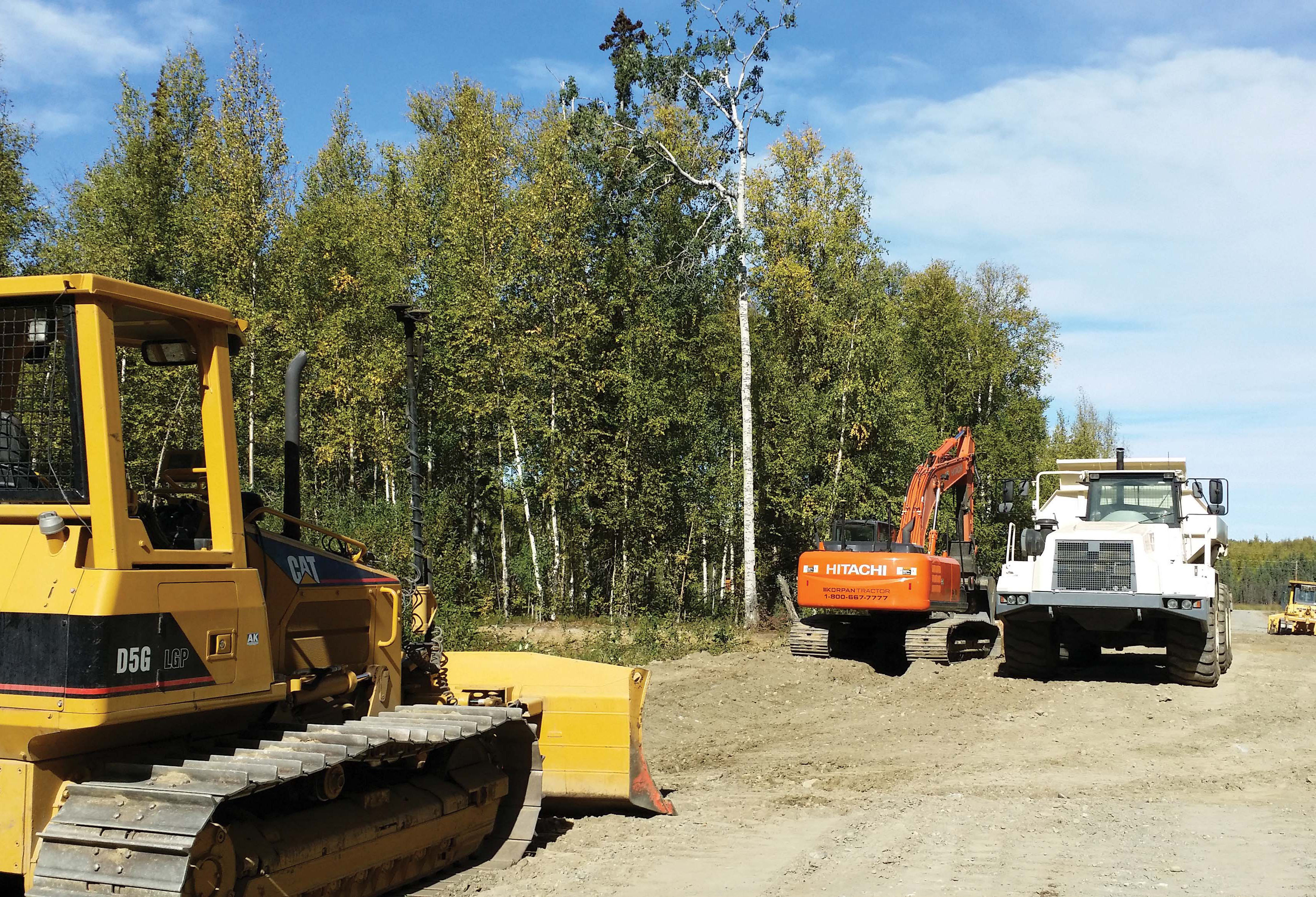
Machine control systems helped boost project quality in Alaska
Juniper, spruce, cranberry, cottonwood and rose. Most people think of pine trees and berries amid beautiful country fields. But for one contractor based just below the Arctic Circle in the US state of Alaska, the names represent a successful job completed using machine control
Valley General Construction recently finished a US$350,000 contract for the upgrading of country roads in the local borough of Matanuska-Susitna. The colourful names belong to roads in a heavily wooded residential subdivision located in the borough, not far from the town of Palmer, population about 6,500.
Valley is a medium-to-small size contractor – up to eight employees – based in Palmer. Local roadwork and commercial projects are the bulk of the business but the company also works at times in Anchorage, only about 70km away and – with a population of about 300,000 –is the state’s largest city.
In 2014, the Matanuska-Susitna Borough decided on a two-year plan to upgrade the subdivision’s dirt roads that are laid out in a grid pattern, roughly square and with a total length of 1.5km. The objective for year one is to raise the embedded dirt roads to grade and then let them “winter over” – settle down – so that in year two they can be paved.
“Since the roads are embedded below grade, there have been major drainage problems,” stated Brian Hooks, project manager and co-owner of Valley General Construction. “We needed to bring the road not only up to grade but also build in a culvert to address the water run off.”
The borough’s engineers produced CAD drawings showing the 3.6m-wide roads, culverts almost a metre wide and the cut-ins for 50 driveway approaches.
“I took the engineers’ drawings and used342 Topcon MAGNET Office Site to create a site model and files that could control the excavator and dozer we used on the project,” said Hooks.
But Hooks first needed to upgrade an older and limited machine control system so he consulted GPS Alaska, based in Anchorage, and received additional training and help to select a robust system for the company’s178 Caterpillar dozer. Valley General purchased the Topcon 3D-MC2 machine control designed to access all satellites and provide position updates up to 100 times per second.
The 3D-MC2 sensor combines a gyro, compass and inertial sensor to measure the X, Y and Z positions as well as the roll, pitch, yaw and acceleration of the dozer. The Topcon system connects to both GPS and GLONASS satellites.
Additionally, Valley purchased a Topcon X62 excavator grade control system for its233 Hitachi ZX210-6 hydraulic excavator that has an operating weight of 21,900kg and a bucket force of 158kN. The project was also the first job where Valley had used machine control technology on an excavator.
The embedded roads were already several inches below grade. Excavation brought each road to a uniform 10 inches below grade before lifts of fill soil, crushed stone and a binder-layer of reclaimed asphalt pavement – RAP – were added.
Once completed, the roads will winter over until next spring. Alaskan winters are long so the borough wants to adjust the roads after the several freeze-thaw cycles that can occur during a winter season before a finished asphalt surface is paved.
The subdivision project required about 3,060m3 of fill dirt and nearly 6,120m3 of #5 crushed stone. Additionally, 76m of culvert pipe was laid down. “We completed in two weeks,” said Hooks. “Our accuracy is spot on, so we’ve eliminated wasted time with rework.”
Without machine control technology, the job would have taken twice as long and had more risks of delays.
Hooks said Valley’s machine operators can literally go out on to the job and know, by looking at their monitors, what needs to be done. “The project is stake-less, so we don’t need surveyors or have delays when a stake is run over. Plus, we also eliminated the need for a worker to walk along with the excavator for spotting and checks,” he said.
“We’ve been using the technology for so long, it’s hard to imagine running a project without it. If someone took it away, people would walk out the door…probably following me, it’s that important.”
Valley General Construction recently finished a US$350,000 contract for the upgrading of country roads in the local borough of Matanuska-Susitna. The colourful names belong to roads in a heavily wooded residential subdivision located in the borough, not far from the town of Palmer, population about 6,500.
Valley is a medium-to-small size contractor – up to eight employees – based in Palmer. Local roadwork and commercial projects are the bulk of the business but the company also works at times in Anchorage, only about 70km away and – with a population of about 300,000 –is the state’s largest city.
In 2014, the Matanuska-Susitna Borough decided on a two-year plan to upgrade the subdivision’s dirt roads that are laid out in a grid pattern, roughly square and with a total length of 1.5km. The objective for year one is to raise the embedded dirt roads to grade and then let them “winter over” – settle down – so that in year two they can be paved.
“Since the roads are embedded below grade, there have been major drainage problems,” stated Brian Hooks, project manager and co-owner of Valley General Construction. “We needed to bring the road not only up to grade but also build in a culvert to address the water run off.”
The borough’s engineers produced CAD drawings showing the 3.6m-wide roads, culverts almost a metre wide and the cut-ins for 50 driveway approaches.
“I took the engineers’ drawings and used
But Hooks first needed to upgrade an older and limited machine control system so he consulted GPS Alaska, based in Anchorage, and received additional training and help to select a robust system for the company’s
The 3D-MC2 sensor combines a gyro, compass and inertial sensor to measure the X, Y and Z positions as well as the roll, pitch, yaw and acceleration of the dozer. The Topcon system connects to both GPS and GLONASS satellites.
Additionally, Valley purchased a Topcon X62 excavator grade control system for its
The embedded roads were already several inches below grade. Excavation brought each road to a uniform 10 inches below grade before lifts of fill soil, crushed stone and a binder-layer of reclaimed asphalt pavement – RAP – were added.
Once completed, the roads will winter over until next spring. Alaskan winters are long so the borough wants to adjust the roads after the several freeze-thaw cycles that can occur during a winter season before a finished asphalt surface is paved.
The subdivision project required about 3,060m3 of fill dirt and nearly 6,120m3 of #5 crushed stone. Additionally, 76m of culvert pipe was laid down. “We completed in two weeks,” said Hooks. “Our accuracy is spot on, so we’ve eliminated wasted time with rework.”
Without machine control technology, the job would have taken twice as long and had more risks of delays.
Hooks said Valley’s machine operators can literally go out on to the job and know, by looking at their monitors, what needs to be done. “The project is stake-less, so we don’t need surveyors or have delays when a stake is run over. Plus, we also eliminated the need for a worker to walk along with the excavator for spotting and checks,” he said.
“We’ve been using the technology for so long, it’s hard to imagine running a project without it. If someone took it away, people would walk out the door…probably following me, it’s that important.”