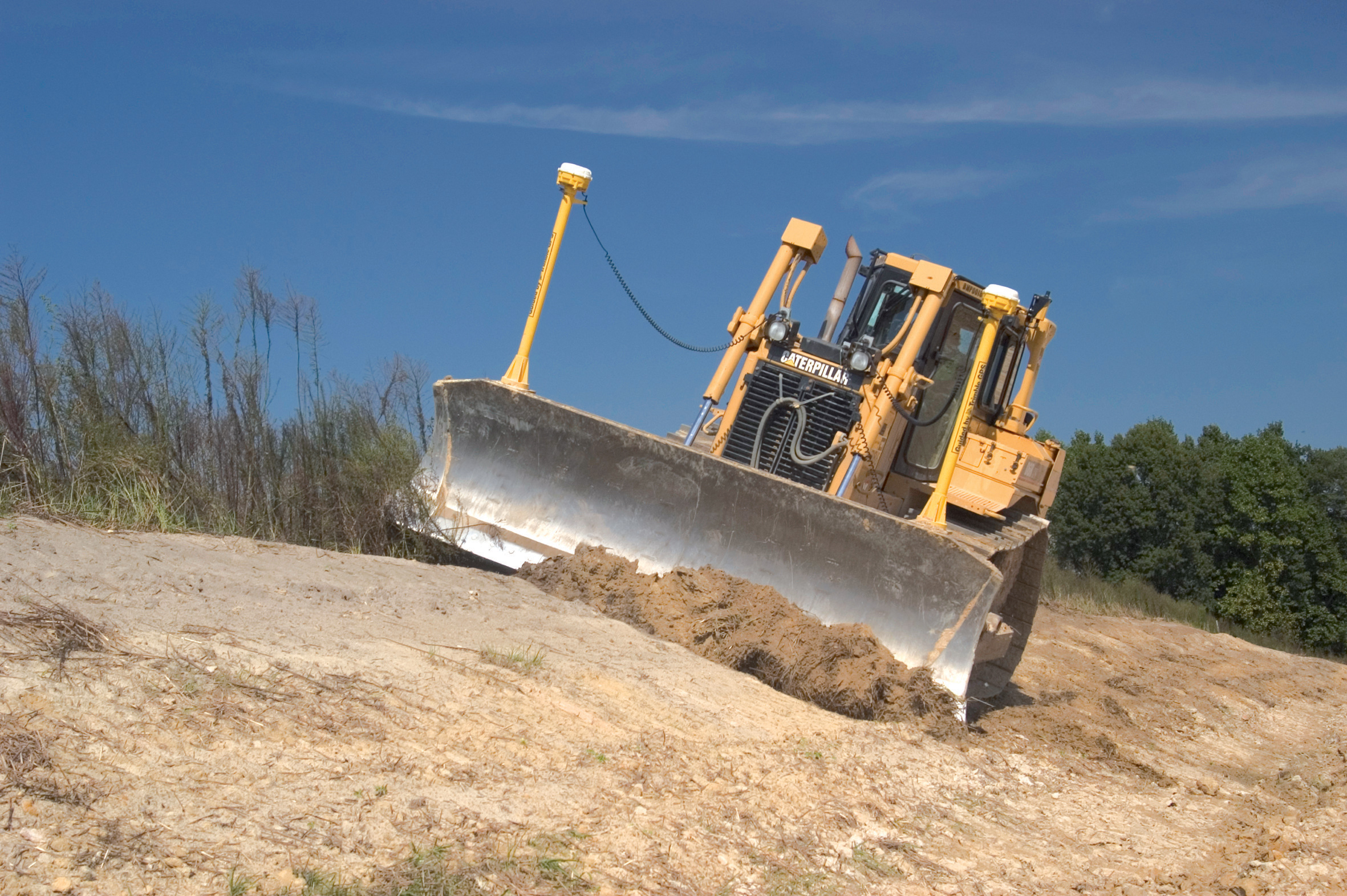
Modern satellite technology is making life easier for everyone on the construction site and in the office
Most major equipment manufacturers are now integrating GPS machine control systems into the design of excavators, bulldozers, pavers, and motor graders. For stake-less work it is a major component for automatic grading, surveying, and excavating systems, with contractors and construction companies using GPS machine control systems to improve operations.Indeed, GPS is in many instances allowing companies to manage their businesses from the office to the construction site. On site equipment using GPS machine control offers accurate grading and reduces work time while it can also be used for job management where it offers up-to-date, accurate, and complete job site information.
Daily reports and other data can be generated using GPS Machine Control systems: indeed it also makes billing much easier. An example of this is
As part of the Trimble Connected Site portfolio of construction solutions, the Trimble Connected Community allows contractors to build information portals, share information and collaborate between head office management, site office teams, field crews, subcontractors, suppliers, engineers and clients on a project.
Trimble says that Connected Site workflows on the modern construction job site involve two-way data transfer and real-time communications to increase productivity for site positioning, grade control, asset management, and the Trimble Connected Community.
For example, Connecting Site Positioning Systems offers real-time, two-way data flow between the office and GPS/GLONASS or total station positioning systems. "By eliminating trips back to the office to retrieve or download the latest design and work order data, the process is streamlined and enables field crews to have the most up-to-date information, reducing downtime and making field crews more efficient and productive," says Trimble.
The Construction Manager solution, combining GPS and wireless communications, enables contractors to connect to their assets on heavy and highway projects while Trimble Connected Community shows how contractors can integrate head office, site office and field crew operations into a communication portal that can be accessed by construction project stakeholders, "allowing the efficient sharing of information and rapid resolution of site problems and requests for information."
Last year the company introduced the Trimble GCS900 Grade Control System, "a cutting-edge earthmoving grade control system that puts design surfaces, grades and alignments inside the cab."
Trimble says: "The system uses GPS, GPS and laser, or construction total station technology to accurately position the blade or bucket in real-time, significantly reducing material overages and dramatically improving the contractor's productivity and profitability." The GCS900 can be used on excavators, dozers, motor graders, compactors and scrapers.
Positioning calculations
According to the company, the 3DMC² technology can speed up positioning calculations by a factor of ten compared to conventional systems. The package allows for faster positioning in real time, which means the machine can be controlled to design grade at higher speeds than previously available systems.
Because the 3DMC² package uses both GPS+ and GLONASS technology, it provides a far higher rate of location checks and allows more precise positioning and accuracy. Increasing the speed of the dozer can reduce set-out time and make a huge reduction in costs, while providing the highest accuracy and ensuring work is carried out to grade, without the need for reworking.
This third generation 3D system also uses inertial guidance technology, with a three gyro package from a Swedish supplier. It allows a huge jump in productivity over conventional systems and could even eliminate the need
for a grader on site for finishing work, according to Sturm.
Topcon says it has used a combination of algorithms, satellite signal filters and arithmetic formulas and has used the experience of its scientists and engineers to offer a major advance in machine control. Sturm said: "Using Topcon's GX-60 controller, MC-R3 satellite receiver and a specially designed inertial sensor, you can operate a dozer at a higher gear with smoother results than possible with traditional grading methods. It changes the way contractors will look at the finish grading process. Of course, as the speed increases, we can do more work in less time. That means less operating time, less fuel, less wear on a machine and most importantly, more time that can be spent on other work in other areas. Fine grading with a dozer is typically done in first gear. You are trained to go at a slow rate. You go too fast and the ground looks like a wave pool. But having access to a system that allows you to grade faster, and at the same time achieve maximum smoothness is a major plus."
The company says its new 3DMC 9.06 software offers several benefits for both existing and new users of its proven 3D machine control packages. The new 3D machine control software offers a real-time, colour-coded cut/fill mapping tool that can display where material is located on the job site and where it needs to be moved to. By comparing the existing surface to the finish design, the operator can see on the control box cut, fill and on-grade areas in an array of selectable colours, which can be shaded so deeper cuts and greater fills are displayed in darker tones. As the operator moves across the site, the screen automatically changes shade to show the cut or fill needed to meet the grade requirements. When complete, the surface fill can be saved as an as-built for finish grade confirmation.
GPS-based compaction
The system links machine kinematics with job-integrated process measurement and control technology in the vibratory roller, thus establishing overall process control and monitoring.
"The basic idea of having a Continuous Compaction Control (CCC) on the job site is quite an old one. The application of controlled rollers such as Ammann's intelligence device ACE (Ammann Compaction Expert) in combination with GPS-equipped visualisation ACEplus is the key to achieving this goal," says the company.
"The data acquisition and visualisation processing system ACEplus enables the operator to increase compaction equipment performance. The real-time visualisation of the compaction data on a PC screen maximises compaction process control and the benefit of using an 'automatic controlled roller.' The CCC enables the operator to recognise non-compactable material or still non-compacted areas on a job site immediately."
Ammann says its GPS-based compaction control supports the guidance of the roller operator in achieving the optimal compaction result in a safe and efficient way, while ACEplus enables the supervisor on the job site to coordinate utilisation of all compaction machines on the site and to maximise productivity and output of his resources.
Control versatility
Using the CI-14 package is said to eliminate the cost and effort of installing add-on hydraulic valves when fitting control tools from Leica Geosystems to Caterpillar K and T Series dozers and M Series graders. The CI-14 system can be used in conjunction with laser, slope, ultrasonic or 3D GPS/GNSS as well as the Leica PowerTracker total station sensors, and adds plug and grade control capabilities.
The system is compatible with both ARO-prepared and non-ARO bulldozers and motorgraders with no CAT SEA licence activation fee to pay. According to the company, the hardware is field-proven and the software is fully field-programmable to allow for future upgrades, while it is CAN-Bus based to ensure reliable operation and simple diagnostics.
Meanwhile the company's PowerGrade system features the PowerSnap concept, with a docking station that allows for quick exchange of panels and transfer between machines. The PowerSnap device allows the user to swap the tool from one machine to another and also allows the system to be reconfigured from 2D to 3D capabilities as required. The PowerGrade system can be upgraded and is scalable from the basic 2D package to full 3D capability using the same control panel.
Meanwhile, the new Leica Rugby 320SG, 410DG and 420DG Grade Lasers are automatic, self-levelling tools for jobs of any size, and says the company, they can be used for virtually any application involving precise grade control. Offering long range, as well as high reliability and accuracy, the lasers were designed specifically for full compatibility with machine control systems in construction and agriculture. The long-range two-way remote control controls all Rugby functions, and allows the user to change the instrument settings 'on-the-fly.' In addition to the remote control, the Leica Rugby Grade Lasers are equipped with new, high-power laser diodes, offering an operating range of up to 1,100m, while maintaining high accuracy of 1.5mm per 30m.