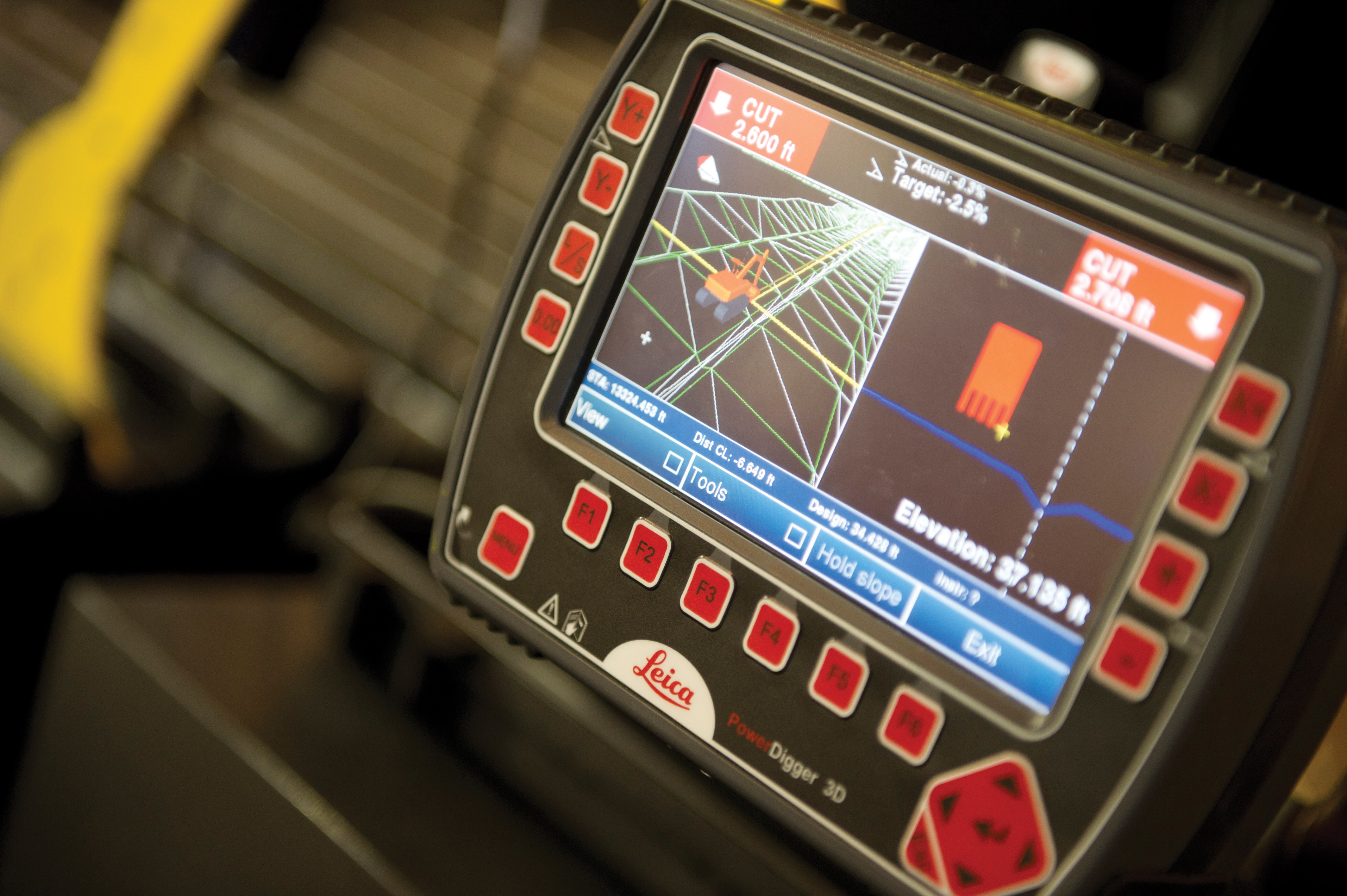
Leica Geosystems has introduced new products for paving, grading, and excavating.
Equipment for earthmoving ranges from entrylevel PowerBlade systems for formation and subgrade leveling applications to the PowerGrade 2D and 3D GPS systems for bulldozers, graders, and scrapers. Other products include Leica PaveSmart 3D, an automated 3D machine control system for curbs and gutters. It is designed to eliminate time-consuming traditional string lines and its operation is based on project design data.
Precision work
A CONTRACTOR in Germany has used a Bobcat T250 compact loader to help carry out a difficult road repair job. The firm, Strassing- Limes, used the Bobcat fitted with a new lasercontrolled precision grader attachment from Bobcat to replace the road surface on the high street of the village of Eppertshausen, close to Darmstadt. The village has a narrow high street, which also features tight curves and small traffic islands at crossroads. This made the use of heavy duty machinery impossible.
Instead, the firm used the laser control and ultrasonic sensors on the new precision grader attachment and the Bobcat T250 loader to carry out the work in these confined spaces.
With this equipment the firm was able to deliver a high precision surface but in a shorter time than using previous methods. The company previously used an excavator fitted with a hydraulic swivel bucket. However, the company said that this method required the crossfall on the road to be measured manually.
The loader-grader system, developed by Bobcat Bensheim in cooperation with Mössinger Lasertronic, combines two control systems to create a highly efficient system. The T250 compact loader is equipped with a lasercontrolled front grader and an ultrasonic sensor. The ultrasonic sensor takes the upper edge of the kerb as a reference height and the crossfall of the road is determined by the sensor integrated in the laser receiver.
A notable development from Leica Geosystems is its new SP Technology, which boosts versatility and productivity when grading with a dozer. The package provides machine control using total stations, providing high precision and increased grading speed in environments where GPS is not available. The firm says that the system provides improved hydraulic control and allows faster grading, giving smoothness and precision at high speeds and boosting machine utilisation. Bulldozers can now provide fine finishing and help contractors to finish projects ahead of schedule and under budget.
The package combines inertial guidance with responsive hydraulic controls, boosting grading performance. The firm claims that the system compensates for weaknesses that GPS and total stations have in normal machine control applications, allowing operators to achieve precise results even under difficult conditions.
Equipping machines with SP Technology reduces the need for rework and increases machine uptime during poor satellite coverage, or when there is a temporary loss of correction signals or interrupted prism tracking.
Working in combination with GPS or a total station, SP Technology allows fast and precise grading even on challenging job sites. If GPS is not usable, such as when working in deep cuts or in tunnels, the operator can swap the GPS sensors with a total station and can keep working with the 3D machine control system.
This system is offered as an upgrade or option for the Leica PowerGrade platform.
Meanwhile Topcon is now offering a version of its innovative 3D-MC2 system, originally aimed at use on bulldozers, for use on graders. As with the earlier package for the dozer market, this new version allows a contractor to run a grader at much higher speed than before, boosting productivity considerably. The earlier dozer system allows the operator to drive the machine at high speed in top gear while making a finish cut and the new grader version offers similar benefits. Using this, an operator can drive a grader to operate at speeds well above those possible using conventional 3D controls, while delivering tighter tolerances.
Topcon claims that with a grader, an operator can provide a finish cut on up to 69,675m2/shift, a major increase from the 3,716-14,864m2 achieved using conventional tools. The system uses a combination of satellite position signals and location data from total stations set up around a site to allow precise finish cuts to be made with the machine's blade, even at high travel speed.
Ray O'Conner, president and CEO of Topcon said, "With a single dozer and a grader both equipped with 3D-MC2 a contractor can accomplish more with greater accuracy than ever before." Fitting the 3D-MC2 package to a grader allows the system to make corrections to the blade position at up to 100 times/second. The package also uses Topcon's existing slope sensor to boost working accuracy when a machine is making a cut, on sites ranging from flat grades to steep slopes. The system is equipped with built-in tilt compensation to automatically adjust blade position so as to maintain the correct grade.
Topcon says that the 3D-MC2 system is built along modular lines and is compatible with its existing sensor technology, allowing it to be used in 2D applications running from conventional sonic units and lasers when GPS is not available.
Another key development from Topcon is its new SiteLINK 3D package, which provides a sophisticated communications management solution that can be used with the firm's 3DMC grade control range. The SiteLINK 3D package can connect working machines in the field with the office and handle two-way data flow in realtime.
By using the system, contractors and site engineers can recover working data from machines to monitor operations, calculate productivity and have an accurate picture of operations on-site, without having to leave the office.
Trimble has key machine control updates, the GCS900 and GCSFlex grade control systems.
Trimble's sophisticated GCS900 grade control system is said to offer a wide range of grading options for contractors carrying out earthmoving and excavation work. The system can be integrated with other tools from the firm through the Trimble Connected Site portfolio and allows contractors to streamline workflows and meet tighter project requirements while staying on deadline and under budget. The latest features include a new control box that provides operators with more power, more memory and a large screen displaying 3D profile information, grade guidance and warnings.
The Trimble GCSFlex grade control system is designed for use on excavators and is aimed at use by owner operators and small to mid-sized contractors carrying out earthmoving work.
Designed for use with small to mid-sized excavators, the system is rugged, easy to install, easy to learn and easy to use and features an array of sensor options that allow the contractor to use the system for a variety of tasks.
Contractors can start with a low cost solution and add sensors when they need to increase the capabilities of the system. Installation can be done by the owner in a few hours and the system can even be used on rental machines.
In addition, Trimble has also integrated its Connected Site grade control systems with Vision Link advanced telematics and asset tracking, allowing contractors to make better informed decisions, optimise asset productivity and reduce operational costs. The system also includes a new smart antenna and new wireless communications.