GPS systems for machine control can make massive reductions in operating costs for contractors. Using GPS systems for machine control can make massive reductions in operating costs for contractors and the pace of technology improvements from manufacturers has been rapid. This market segment is dominated by Leica Geosystems, Trimble and Topcon, all of which introduced an array of new products earlier this year. Topcon's dozer control system first seen in public at the Intermat show in Paris, offers notable c
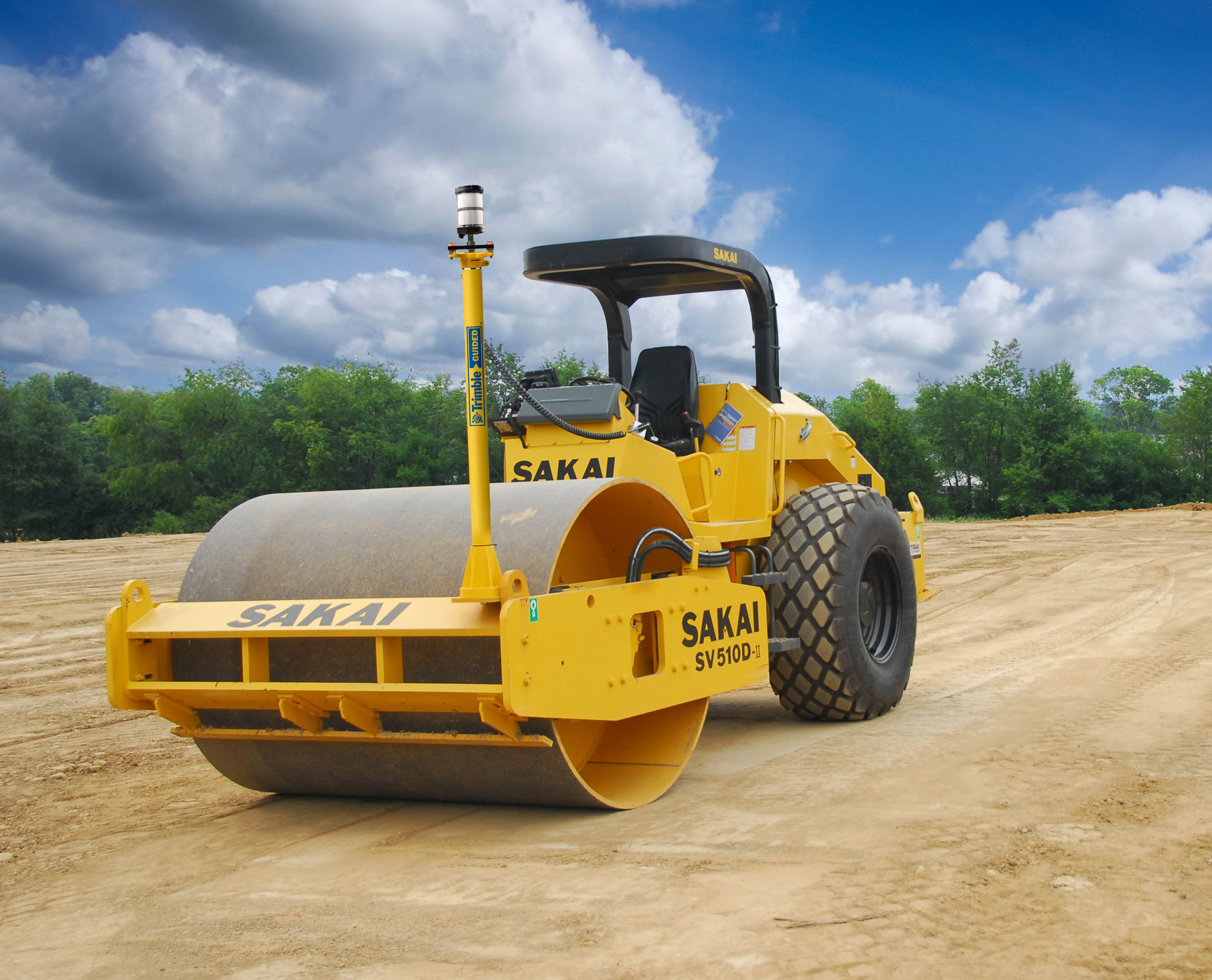
The new Trimble GCS900 v11.1 package includes new 3D configurations for soil compactors, broadening the range of machine types supported
GPS systems for machine control can make massive reductions in operating costs for contractors.
Using GPS systems for machine control can make massive reductions in operating costs for contractors and the pace of technology improvements from manufacturers has been rapid. This market segment is dominated byProlec's sophisticated 2D and 3D Digmaster systems are said to offer productivity increases of up to 50%, while reducing reworking and these can be used in applications such as mass excavation, general earthworks, grading and trenching/ditching. Features of the Digmaster pro package include 3D real-time, multi-view machine guidance, multiple target indicators, auto zoom and view change for fine grading, progress map,, user defined offset, customisable machine and tool functions and a configurable GPS interface for use with all major brands of GPS equipment. According to the firm, operating in 3D mode allows a surveyed design to be uploaded into the cab and boosts productivity. In 2D mode the system can be used for level, slope or dual slope excavation or trenching, however the 2D package can also be upgraded to 3D capabilities if required.
The high specification version of the Prolec 3D system is the pcX-3D package, a system that can be custom tailored to suit the user's specific needs. Advantages for this more sophisticated version include actual versus target progress in real-time, material characterisation and material extraction/placement calculation.
Trimble continues to evolve its technology package and issues involving poor satellite reception can be tackled due to new features with Trimble GPS firmware 4.0, while the firm's GPS tools also come with other upgrades and benefits. The improved real time kinematic (RTK) engine of version 4.0, which powers Trimble R-Track technology, provides faster initialisation and improves receiver performance in areas with limited satellite reception, such as on jobsites where satellite signals are obstructed by tall buildings, high quarry walls, or tree canopy. When RTK correction signals are intermittent or marginal, the new RTK engine provides improved precision estimations. This allows a Trimble GPS receiver to continue working at reduced accuracy even after an RTK signal is interrupted. It suits jobsite positioning and measuring applications in locations where satellite signals are limited or obstructed and where the highest accuracy is neither achievable nor required. For contractors operating multiple jobsites with limited base station infrastructure availability, the new RTK engine allows SPS receivers operating at jobsites located at greater ranges from the base stations to have rapid initialisation and improved vertical accuracy. The system uses a new proprietary protocol, CMRx, for corrections transmitted by a GPS base station. Through this development, Trimble says it is pioneering improvements in the industry-standard RTK technology through a significant evolution of its existing CMR and CMR+ standards for correction message protocol.
Trimble continues to develop its sophisticated Grade Control System with the availability of version 11.1 of its GCS900 package. This further expands the mix of machines supported and provides improved wireless data transfer capabilities between the office and the operator. This includes new 3D configurations for soil compactors, broadening the range of machine types supported. Heavy highway contractors can use key Trimble machine control components on more machines and for more applications.
These new configurations for soil compactors allow contractors to implement total station-based machine control technology across more machines in their fleet. The Trimble SPS Series Universal Total Station is ideal for either high accuracy work or operating in areas with limited or no GPS coverage. Using GCS900 v11.1, contractors can now port their machine control positioning technology between dozers, graders, excavators, and soil compactors.
The GCS900 v11.1 supports a new generation of Trimble AS Series angle sensor designed for use on excavator roto-tilt bucket applications. The new angle sensor has been designed in a smaller form factor, which make it ideal for mounting in tight spaces on an excavator tilt-rotation attachment. The AS455 is gravity-referenced and measures angles in a full ±180 degree range. This capability provides the operator with the precise location of the tip of the bucket when working on tight area projects. In addition, the GCS900 v11.1 package includes support for the
Using the Trimble SNM930 cellular modem, Trimble GCS900 can be used with almost any type of Internet base station or network real time kinematic (RTK) service, such as a remote base station at the site office or a Trimble VRS network, or other network RTK services. This allows increased machine utilisation on smaller projects or where base station infrastructure may not be available.
Trimble is also offering a rugged new GPS locator unit designed for use in harsh construction site environments. The MTS400 features a ruggedised metal housing and mounting bracket for more permanent installation outside the cab on heavy construction equipment such as earthmoving machines and dump trucks. This system means that Trimble Construction Manager can now support three GPS data communication modules for versatility in tracking and managing heavy equipment. The new device joins the CrossCheck Global Locator and Trimble TrimTrac Pro Locator for use with hardware to manage a full range of construction equipment.
And a new feature in Trimble GPS receiver firmware 4.0 enables users to operate and manage Trimble GPS receivers through the new Trimble Connected Community. An optimised version of the popular Web User Interface (UI) of the SPSx81 Smart GPS Antennas and SPSxx1 Modular Receivers can be placed on a Trimble Connected Community site.