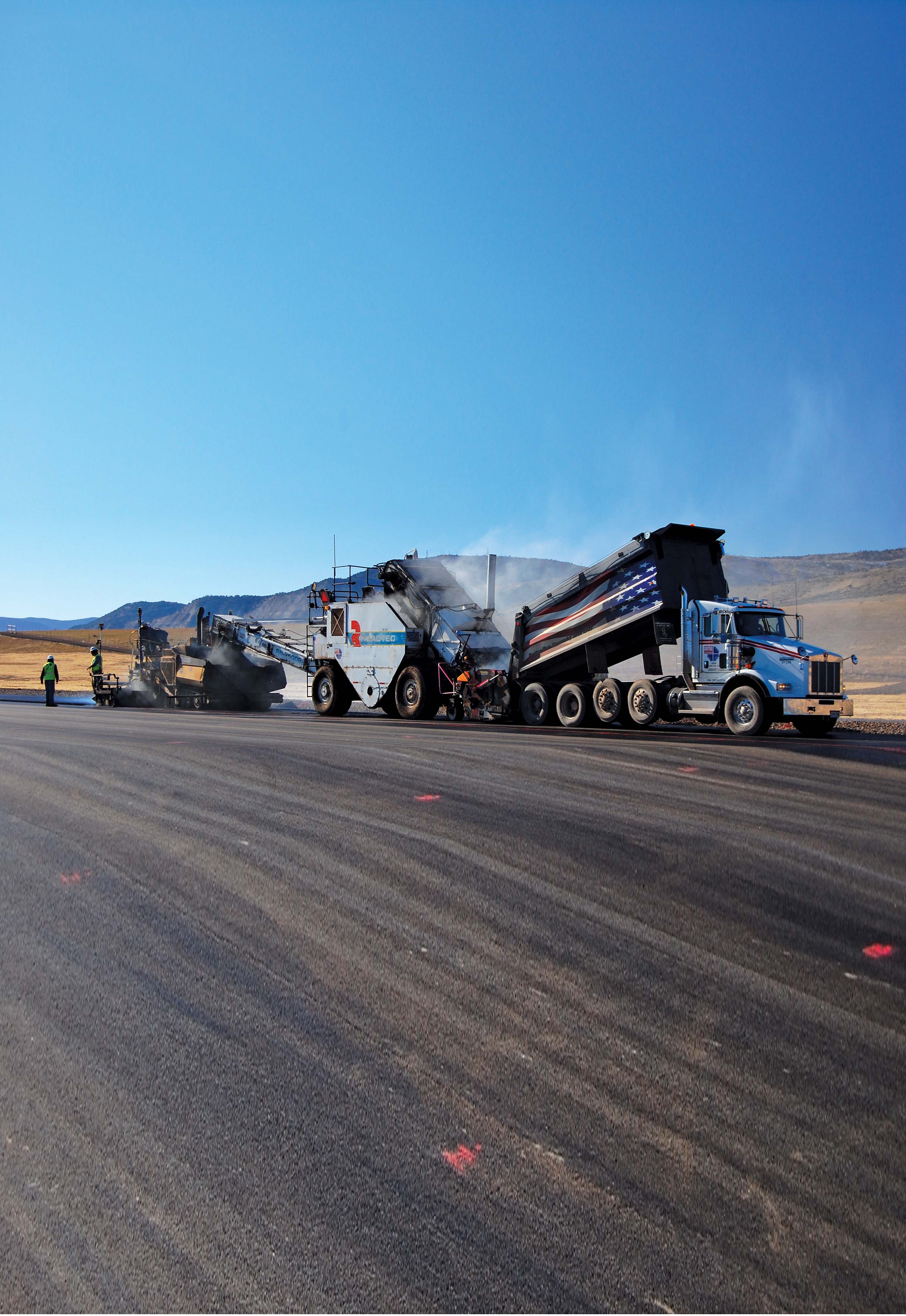
Airport construction projects provide paving challenges at jobsites around the world
Located in Meeker, Colorado and serving the area for air transportation is Meeker Airport, a C-II general aviation airport. The FAA designation of C-II means the airport can accommodate aircraft with wingspan of less than 24m.
Runway 3-21 at the Rio Blanco county-owned Meeker Airport had reached a point of wear and deterioration that required full reconstruction and upgrades to remain compliant with the FAA’s C-II requirements. The US$12.5 million project was awarded to local firm Fiore & Sons and was handled in two stages. Construction consisted of the demolition of the existing 18.3m wide by 1.98km long runway and the construction of a new runway to meet C-II runway safety area and longitudinal standards. The new runway was widened to 30.5m but remained 1.98km long. The runway ties into the existing apron connector with a turnaround at the end of the runway.
Fiore & Sons completed the demolition and used milling to remove 35,953m2 of asphalt in preparation for the site conditioning, grading, and paving, which was carried out by local firm United Companies. “We were responsible for base course and paving of the new runway and the overall construction of the large apron and taxiway,” said Jeff Boone, project manager for United Companies. “We needed to complete our portions of the combined projects within the eight-month timeline for the whole project, so our timing was tight.”
United Companies had two major responsibilities in the project: the dirt and stone work to create the sub-base and the finish paving on the runway, apron, and the aircraft turnaround.
After Fiore & Sons completed the demolition of the old runway and moved 784,600m3 to rebuild the runway, United Companies came on site and moved the earth for the large apron and taxiway. Between the two projects the company placed 63,140tonnes of crushed aggregate base course and in 150mm lifts with the company’s three
“The Topcon system helped us achieve more accurate placement of the base materials at higher speeds and better tolerances,” said Jeff Gross, GPS machine control foreman for United Companies. “With a tight production deadline and stringent FAA requirements, it helped to have the technology.”
As part of the machine control system, the motor graders are equipped with the Topcon GX-60 Control Box that features Windows XP operating system, touch-screen interface, USB file transfer capability, and a colour LCD screen. Additionally, the system includes a GPS antenna, MC-R3 receiver, and the MC² sensor—an inertial sensor which combines gyroscopes and accelerometers to measure the X, Y & Z position as well as the roll, pitch, yaw and acceleration of the grader. The Topcon controlling software is designed to provide position updates up to 100 times/second.
GDA Engineers provided the project control points as well as the points for drainage and utilities for the Meeker Airport project. “A tremendous amount of time and money was saved because we didn’t need to be setting grade stakes,” said Ken Dobey, construction manager for United Companies. “United Companies created the 3D site model which our GPS machine control could use—thus, the job was virtually stakeless.”
Dobey points out that the company has been an early adopter of technology for the past 15 years, with GPS machine control in use for the past four years. “Our business approach is to be at the cutting edge of technology,” Dobey stated. “We’ve found that our investments in technology save us time and resources.”
In keeping with its technology adoption approach, United Companies recently added Topcon Millimeter GPS Asphalt Paver Systems to its three Cat AP-1055D pavers. The Topcon system uses what Topcon refers to as LazerZone technology, which uses GPS positioning together with a zone laser reference provided by a PZL-1A rotating laser, which is said to transmit a signal that creates a measuring area 10m in height.
United Companies consulted with Southwest Positioning, an authorised Topcon dealer, on the technology to acquire. Southwest Positioning installed the asphalt paver system and trained the United Companies machine operators. On the first day of paving, United Companies paved two 183m long test strips measuring 4.88m wide using FAA-specified HMA. Sample cores were taken from the 51mm thick lift to ensure compliance. The paver guided by the Topcon paving control system provided results well within compliance.
To pave the runway, United Companies arranged three PZL-1A rotating lasers spaced 152m apart and then leap-frogged them to maintain continuous production flow.
A
In addition to the main runway, United Companies paved a 198m by 97.5m apron and a 366m long by 15.2m wide taxiway. The complete Meeker Airport job required six layers that each needed to be checked for smoothness.
The first layer was a graded dirt layer followed by three 150mm lifts of the P-154 subbase course—which is a gravel that consists of hard durable particles or fragments of granular aggregates. The fifth layer was a 150mm lift of PT-209 base course. And the top layer is two, 51mm lifts of FAA-specified HMA.
“If we had needed to complete all of this work the old way using survey crews and pounding wood, it probably would have
taken us two to three times longer…the technology is that beneficial,” Boone said. Meanwhile the final International Roughness Index of the recently completed Meeker Airport runway surface is well within the FAA specifications.