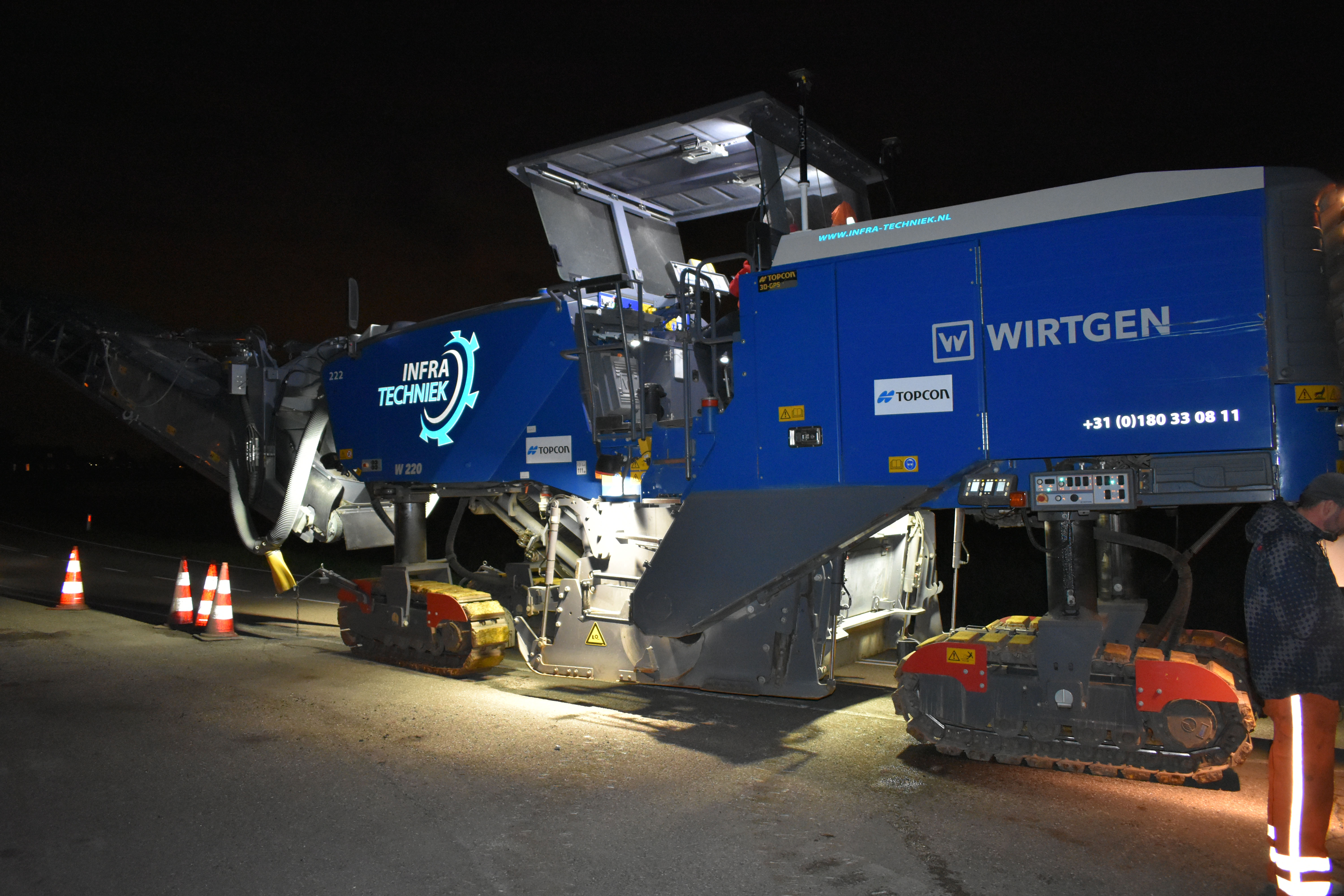
The firm, Van Gelder, was looking for a solution to survey, mill and resurface a 7km length of the N518 to the island of Marken more quickly, more safely and more accurately. Together with Infra-Techniek, the company opted to use the latest package developed by
The company opted to try the new technology, knowing that conventional methods can be expensive and high-risk. With standard methods, a worker manually measures the road at three points using a GPS pole every 5-10m. The road has to be temporarily closed to be able to measure the height, camber and slope. Road designers use the data to develop a new road design to the client’s specification. The road is then closed again for painting of markings on the road surface to guide the milling contractor. After the milling, a second measurement is carried out to determine how much asphalt is required to deliver the required height, camber and slope, requiring yet more road closures. Van Gelder realised that the new technology would deliver the job more quickly, more accurately, more cheaply and with a lower risk.
Van Gelder decided to use Topcon’s new RD-M1 scanner system, which has been introduced in Europe as part of the SmoothRide concept, for milling and paving. The RD-M1 scanner is at the core of this system and makes use of laser imaging detection and ranging (LIDAR). The RD-M1 is mounted on the tow hook of a vehicle, while the LIDAR system continuously measures the distance to the road surface. Height differences in the whole road surface in the length and width axes are mapped with a maximum of 100 measurements/second, even as the vehicle travels at 80km/h. The RD-M1 also has a GNSS receiver and an inertial measurement unit (IMU), which records data on vehicle speed, tilting and acceleration.
The point cloud then produced contains the GPS coordinates with the corresponding height differences in the existing road surface. Various reference points can then be measured with a GPS pole for verification. These are also used to georeference the point cloud in the width, length and height directions. The designers use the data to design the new road surface and calculate how much material needs to be milled off and where, taking into account the required minimum layer thickness, the camber and the slope of the new surface.
The 3D model developed is then entered into the control box of the planer for machine-controlled milling. A difference from milling without using the SmoothRide concept (or equivalent) is that the two milling machine operators do not need to read markings painted on the road surface. Automatic control of the milling drum is more accurate, while the operators are able to focus on the machine and filling trucks with cuttings. Using this method improves the milling tolerance from 10mm using conventional methods to 4mm for a road surface milled automatically. This cuts waste and material transport, lowers wear for the milling teeth and reduces the quantities of new asphalt. The companies also believe that the new asphalt layer has a more consistent thickness, boosting its lifespan.
A trial run was carried out on the N235 between Purmerend and Ilpendam in early 2017, which showed that it was necessary to keep the direct control sensor on the third or fourth ski of the milling machine. It also took some effort to calibrate the milling machine in combination with the 3D GPS machine controller. Another challenge is the range of the GNSS system of the RD-M1 scanner when used in urban areas or tunnels.
Using the new method required some training but the results have been successful and Van Gelder says it will be using this technology again.