3D machine controls can optimise milling efficiency, Mike Woof reports. More efficient milling and recycling operations can be carried out by using the latest 3D control systems on the market. At the last Trimble Dimensions event in Las Vegas, the advantages of 3D controls for milling operations proved a key topic. The use of 3D control systems can offer huge advantages in milling operations. This technology helps increase productivity as the milling machine will only remove what is required, which also hel
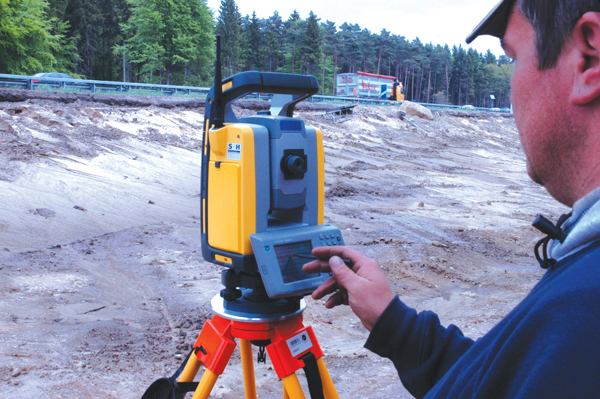
Accurate machine control was achieved using the Trimble package
3D machine controls can optimise milling efficiency, Mike Woof reports
More efficient milling and recycling operations can be carried out by using the latest 3D control systems on the market. At the lastThe use of 3D control systems can offer huge advantages in milling operations. This technology helps increase productivity as the milling machine will only remove what is required, which also helps minimise materials removal and haulage costs.
Sophisticated 3D milling control systems were used on a project to upgrade the E45 highway in Sweden. The work was carried out for
The 7km stretch of road links Brälanda with Erikstad and featured variable depth milling in the 0-100mm range, removing some 56,000m2 of material. An adjustable system helped account for wear in the milling teeth, so as to ensure that cut depth remained within the tight tolerances of the specification. A road profilograph was used to check the surface smoothness and make sure it remained to grade. For this project, the expected milling speed was 7m/min, however a real milling speed of 12m/min was achieved and this was due in part to the optimised cutting depth as the planer only removed the material required to meet grade specifications. However, had 2D controls been used milling advance speeds of 20-30m/min could have been reached. This is because planing work has to be carried out at lower speeds under 3D control, so as to minimise vibration.
Meanwhile 3D milling controls were also tried on a
Perhaps the most significant use of this new technology is in Germany, where 3D milling technology from Trimble has been employed on the A1 Autobahn widening project between the cities of Hamburg and Bremen. The A1 carries the heaviest traffic load of any highway in Germany and is being widened to six lanes. This is one of four pilot projects by the country's Federal Government, which is investigating long-term partnerships between the public and private sectors. Under the arrangement, private contractors provide and finance the costs to build, maintain, operate, and maintain the motorway for a 30 year contract. In return, the private contractors receive a monthly share of the tolls collected on heavy-goods vehicles by government for the section of the highway. Because of this deal, the contractor understandably wants to achieve the highest possible roadway performance and quality standards, as this will help deliver longer surface life and reduce maintenance needs, with a big impact on whole-life costs and profitability.
The A1 Hamburg to Bremen Autobahn was first built in the mid-1930s and is heavily used, requiring an investment of some €650 million and the work is being handled by a consortium called A1 mobil, which is comprised of
The A1 upgrade is being revamped over a 73km stretch and is divided into 26 work sections, each of around 6km long. Adjacent sections are being widened at different intervals so that any given time there is a construction-free stretch between those being upgraded. This is intended to avoid excessively long stretches of construction, improving traffic safety and as this is a busy highway connection, operations are being carried out with live traffic lanes running alongside. Different sections of the highway feature concrete, low noise asphalt and conventional high quality asphalt. The top wear-and-tear surface of the highway is being removed over the entire project to a 40mm depth. In addition, gradient optimisation is to be carried out over the full section and the cross-section adapted to the regulatory standardisation with a camber of at least 2.5%.
Sub-soil examination revealed that large parts of the existing roadbed substrate are still viable. The question facing ARGE A1 was whether to remove the road entirely and rebuild it completely, or retain and use stable parts of the roadbed substrate.
"We decided to reuse existing material, in order to save on expensive new material and also to have less old material to remove and recycle. Of course, the time we'd save was also an important factor," said ARGE A1 substrate coordinator Achim Huebschmann.
The challenge was to adapt milling depth to suit different substrate conditions and surface profile changes, which required a detailed milling plan. ARGE A1 surveyors re-surveyed the entire roadway, employing three terrestrial points within a 10m grid of each point. The points surveyed were placed in CAD software and converted to a
The issue was then to ensure that the milling equipment could precisely follow the milling plan. The traditional approach would be to paint points onto the road surface at 5m intervals, but this would have been costly to survey and introduce potential errors. Instead, milling subcontractor ABS Asphalt Beton Service offered a novel solution. "We knew that the advanced technology of an automatic 3D control system on our
Local Trimble distributor, Eilers & Droste, provided training to the two machine operators, Mark Reinecke and Sven Ungnade. ARGE A1 and the sub-contractor ABS both agreed that surface profile milling using a Trimble 3D system has helped achieve the complex milling profile and accuracy required over the cross-section and longitudinal sections of the highway. Reported savings of approximately 7,000tonnes of material/section of construction, with the average price of €50/tonne of material, means that the investment costs for the Trimble technology has been recouped. According to the contractor, using the 3D milling control meant that some 25% less surface had to be milled/day, boosting productivity and working efficiency. And because the surface level was so good, this allowed concrete paving or asphalt paving to be carried out directly on the planed surface, with no need for additional grade corrections.