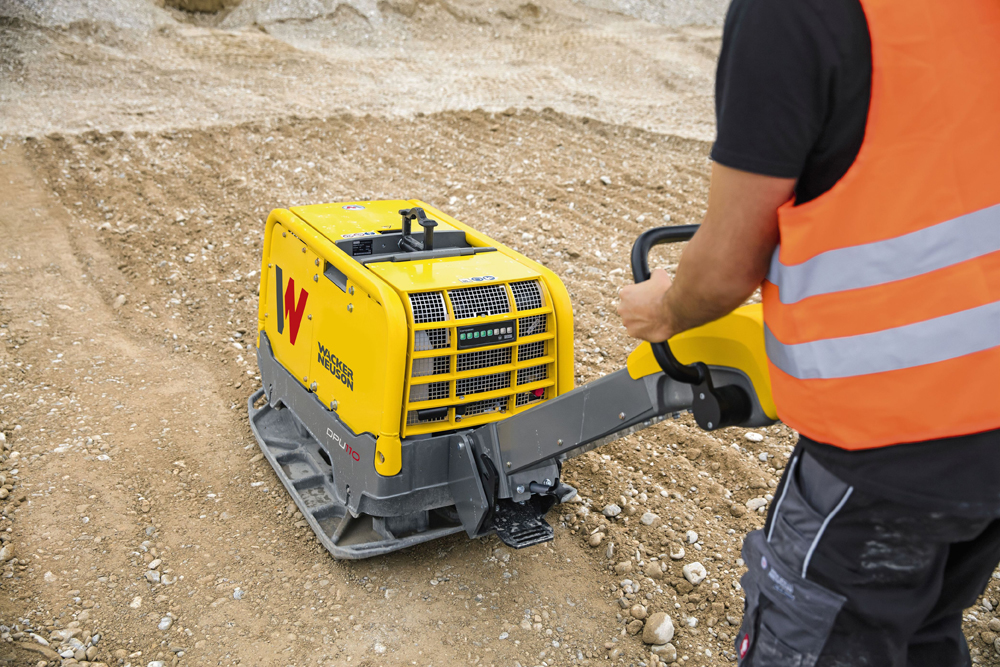
The Compamatic solution allows the proven compaction control to be linked with a telematics solution. The Compamatic package is now also available for the heavy-duty reversible and some of the heavy-duty remote-controlled vibratory plates. This is said to make compaction progress traceable and allows for completely documented quality control. The system shows where compaction has been carried out already, as well as the degree. Users can check whether all the work steps planned for the workday have been carried out; if the planned surfaces have been compacted; and also if the degree of compaction is sufficient. This allows the next steps, such as planning the asphalt delivery, to be initiated efficiently but without the project manager having to travel to the construction sites for quality control.
The system is a combination of the time-tested and proven Compatec compaction control by Wacker Neuson and a Telematics module. Wacker Neuson is offering the system for its DPU80, DPU90, DPU110 reversible plates and the remote-controlled versions DPU80r and DPU110r in the range from 80-110kN.
The firm says that Compamatic allows time savings on complex large construction sites, as quality assurance is enabled using the EquipCare Manager, therefore making fewer onsite inspections necessary. Even for small businesses, this provides time and cost savings.
A vibratory plate equipped with Compamatic sends data for quality control to the Wacker Neuson EquipCare Telematics solution. The exact machine location is recorded via GPS. At the same time, the Compatec compaction control reads out the compaction data at the relevant point in time.