Wacker Neuson has unveiled a range of new compactor tools – Nick Johnson writes. Staged in a gravel pit near Munich in Germany, an event called The Wacker Neuson Universe recently enabled customers to check out the latest machines in the company’s growing product portfolio. On the compaction front, the highlights included electric rammers, two new reversing plates, an improved trench roller, a new range of lightweight tandem rollers and two small self-propelled single drum vibrating rollers.
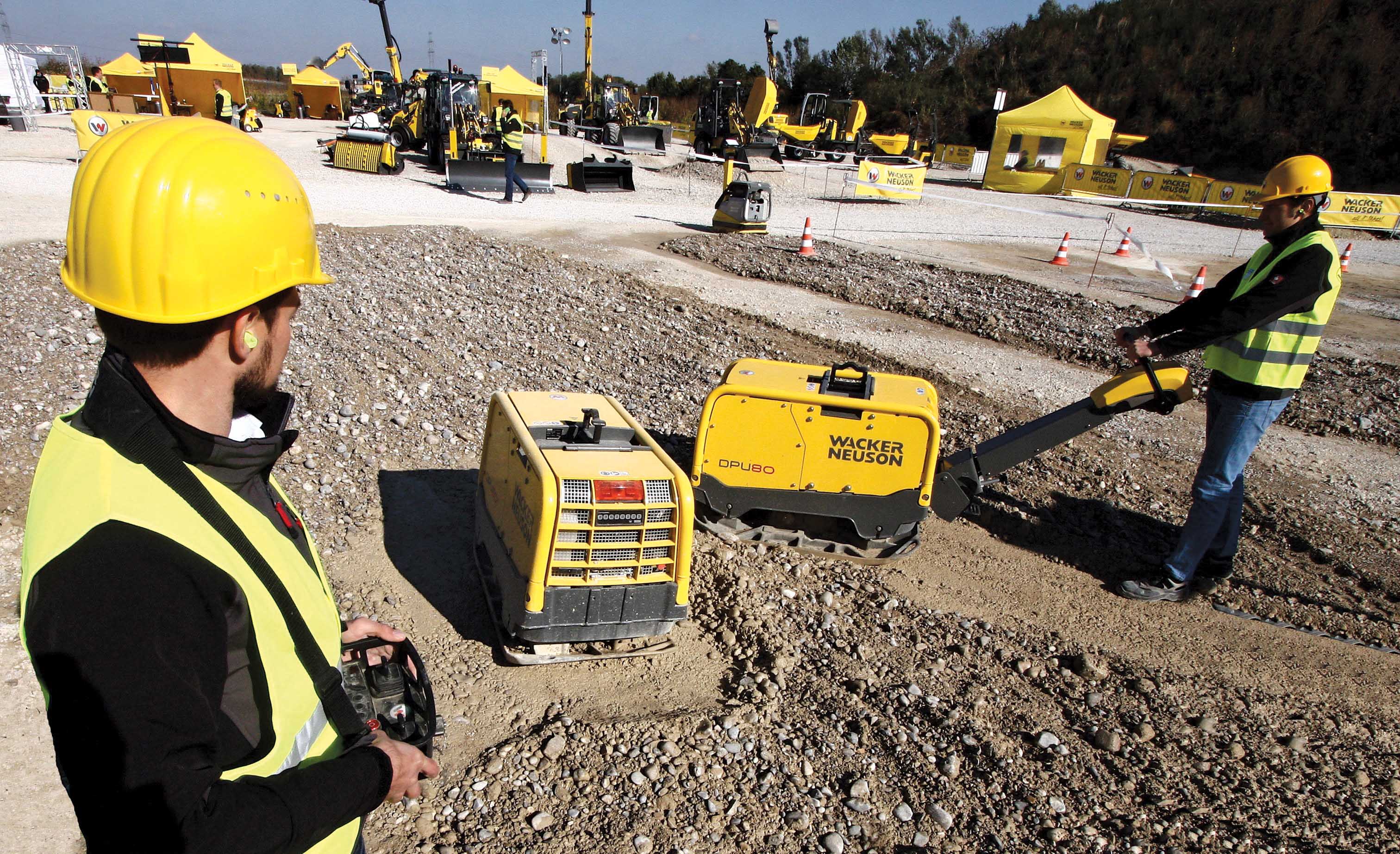
New DPU80 plates in action with the handle (right) and infrared remote control (left)
Wacker Neuson has unveiled a range of new compactor tools – Nick Johnson writes
Staged in a gravel pit near Munich in Germany, an event called The1651 Wacker Neuson Universe recently enabled customers to check out the latest machines in the company’s growing product portfolio. On the compaction front, the highlights included electric rammers, two new reversing plates, an improved trench roller, a new range of lightweight tandem rollers and two small self-propelled single drum vibrating rollers.
To expand and update its range of lightweight tandem vibrating rollers, Wacker Neuson has turned to364 Wirtgen Group member 228 Hamm for badge-engineered machines. The deal brings together two long-established German compaction equipment makers.
Initially introduced into German speaking countries and now being sold through Wacker Neuson outlets across more of Europe, the Hamm derived vibrating rollers include lightweight tandems with drum widths of 800mm, 1m, 1.2m, 1.3m and 1.38m. Compared to the orange Hamm machines, the yellow Wacker Neuson units have subtle differences including a changed engine hood, a new lifting eye and a different control panel.
Typical of the new line is the RD27-120. With a drum width of 1.2m, this machine is powered by a 22.9kW (31.1hp) Kubota D1503 engine. It has crab steering to aid compaction alongside walls and there are versions with two vibrating drums and combinations with one vibrating drum teamed with either one set of pneumatic tyred wheels or a drum with oscillation.
Hamm is also the source for Wacker Neuson’s first self-propelled single drum vibrating rollers. Designated the RC50 and RC70, these 5tonne and 7tonne class Kubota engined machines can be supplied with a ROPS frame or a fully enclosed cab. Rolling widths are 1.37m and 1.68m and there are smooth or padfoot drum options. The larger roller can be supplied with oscillation (as with the model RC70VO).
Moving down in size, Wacker Neuson has improved its own RTSC3 articulated padfoot trench roller. This machine, which offers compaction widths of either 560mm or 820mm wide drums, gains a third infrared receiver (mounted on top) as standard and a1265 Kubota engine is now an option to the standard Kohler. The machine can also now be equipped with the Compatec compaction monitoring system.
The latest additions to the Wacker Neuson vibratory plate line-up are the heavy reversible models DPU80 and DPU110. Available with either a hinged, low HAV control handle or infrared remote control, these plates weigh from 776kg to 837kg and have plate sizes of 670mm by 770mm and 870mm by 970mm. They feature sturdy tubular frames, steel panels and a central lifting eye. The Compatec compaction monitoring system is available as an option.
At the Universe event, Wacker Neuson was also highlighting its growing range of zero emissions machinery which includes two battery-driven rammers. Designed specifically for use in small pipe trenches, the AS30e weighs 45kg and has a shoe measuring 298mm by 150mm. The more general purpose AS50e is a 70kg rammer with a 340mm by 280mm shoe.
Powered by electric motors, both the new e series rammers are powered by electric motors and they utilise the same easily removable battery which is said to retain 80% of its capacity after 1,500 charge cycles. This battery can be charged by Wacker Neuson’s standard battery charger in four hours or by the optional fast charger in only one hour. Running time on a full charge is 30 minutes for the AS30e and 20 minutes for the AS50e.Wacker Neuson
Staged in a gravel pit near Munich in Germany, an event called The
To expand and update its range of lightweight tandem vibrating rollers, Wacker Neuson has turned to
Initially introduced into German speaking countries and now being sold through Wacker Neuson outlets across more of Europe, the Hamm derived vibrating rollers include lightweight tandems with drum widths of 800mm, 1m, 1.2m, 1.3m and 1.38m. Compared to the orange Hamm machines, the yellow Wacker Neuson units have subtle differences including a changed engine hood, a new lifting eye and a different control panel.
Typical of the new line is the RD27-120. With a drum width of 1.2m, this machine is powered by a 22.9kW (31.1hp) Kubota D1503 engine. It has crab steering to aid compaction alongside walls and there are versions with two vibrating drums and combinations with one vibrating drum teamed with either one set of pneumatic tyred wheels or a drum with oscillation.
Hamm is also the source for Wacker Neuson’s first self-propelled single drum vibrating rollers. Designated the RC50 and RC70, these 5tonne and 7tonne class Kubota engined machines can be supplied with a ROPS frame or a fully enclosed cab. Rolling widths are 1.37m and 1.68m and there are smooth or padfoot drum options. The larger roller can be supplied with oscillation (as with the model RC70VO).
Moving down in size, Wacker Neuson has improved its own RTSC3 articulated padfoot trench roller. This machine, which offers compaction widths of either 560mm or 820mm wide drums, gains a third infrared receiver (mounted on top) as standard and a
The latest additions to the Wacker Neuson vibratory plate line-up are the heavy reversible models DPU80 and DPU110. Available with either a hinged, low HAV control handle or infrared remote control, these plates weigh from 776kg to 837kg and have plate sizes of 670mm by 770mm and 870mm by 970mm. They feature sturdy tubular frames, steel panels and a central lifting eye. The Compatec compaction monitoring system is available as an option.
At the Universe event, Wacker Neuson was also highlighting its growing range of zero emissions machinery which includes two battery-driven rammers. Designed specifically for use in small pipe trenches, the AS30e weighs 45kg and has a shoe measuring 298mm by 150mm. The more general purpose AS50e is a 70kg rammer with a 340mm by 280mm shoe.
Powered by electric motors, both the new e series rammers are powered by electric motors and they utilise the same easily removable battery which is said to retain 80% of its capacity after 1,500 charge cycles. This battery can be charged by Wacker Neuson’s standard battery charger in four hours or by the optional fast charger in only one hour. Running time on a full charge is 30 minutes for the AS30e and 20 minutes for the AS50e.Wacker Neuson