Günter Papenburg has developed a cooling feature for asphalt plants that it says shortens the time normally needed for a plant’s coal dust-fuelled burners to reach operating temperatures. The cooling technology has been licenced from LOESCHE, a German producer of coal milling systems. GP managing director Carsten Weiss claimed that the firm’s burners consume more of the fuel than rival types, which only burn 90% of the coal dust. “We get an asphalt temperature of 170°C with low emissions and high efficiency
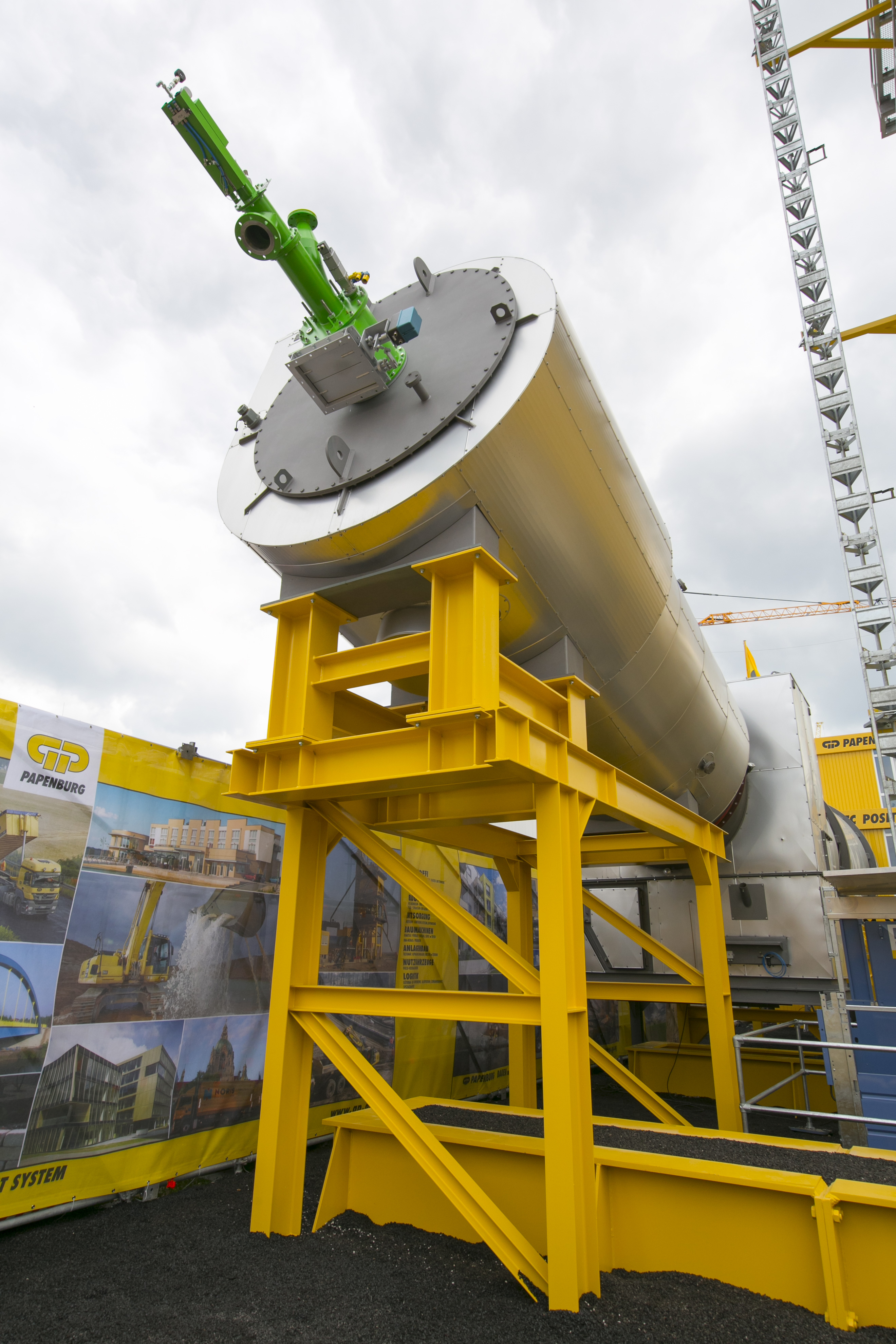
Asphalt plant engineering is rocket science, according to Günter Papenburg
The cooling technology has been licenced from LOESCHE, a German producer of coal milling systems.
GP managing director Carsten Weiss claimed that the firm’s burners consume more of the fuel than rival types, which only burn 90% of the coal dust. “We get an asphalt temperature of 170°C with low emissions and high efficiency,” he said.
The technology is already being used in a new asphalt plant in Germany for a major producer. It features a counter-flow drum and can handle a high percentage of RAP to produce a high quality mix. A sophisticated computer control package allows the use of different grades and quantities of RAP in the mix.
The computer adjusts the position of the flights inside the plant in order to control gas flow and optimise operating temperatures. The plant’s piping configuration minimises the build-up of material to reduce the risk of blockages.
Günter Papenburg’s range of mobile asphalt batching plants come in standard shipping containers and can be set up in just 1-2 weeks on site, according to the firm.
Products in the firm’s Rapid plant line are available in two basic variants, with outputs of 140tonnes/hour and 180tonnes/hour. Options include hot storage and different hopper configurations. The pants can be supplied with steel frames allowing them to be installed on sites that have only a minimum of preparation, although a concrete base may be required if the customer requests more materials storage capacity.
All videos