Advances in transmission technology will help to optimise machine performance – writes Mike Woof. As construction machines have become more sophisticated, so have the transmission systems used in items of equipment. Advances in electronics and software in particular have allowed the development of integrated transmissions. These operate more efficiently and help optimise power delivery from an engine, boosting torque response and cutting fuel consumption and emissions at the same time. The smart electronics
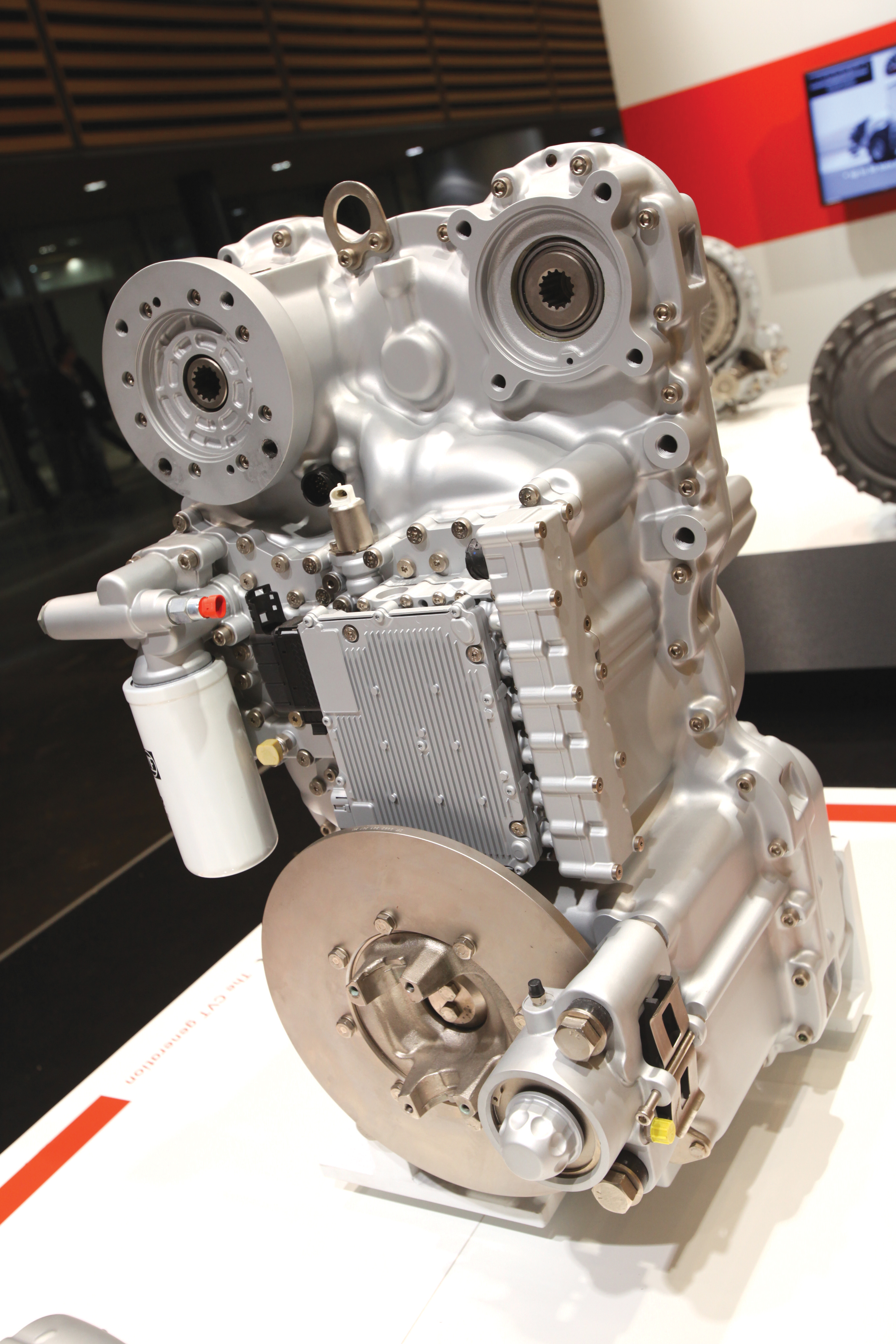
ZF is offering constantly variable transmissions that optimise performance
Advances in transmission technology will help to optimise machine performance – writes Mike Woof
As construction machines have become more sophisticated, so have the transmission systems used in items of equipment. Advances in electronics and software in particular have allowed the development of integrated transmissions. These operate more efficiently and help optimise power delivery from an engine, boosting torque response and cutting fuel consumption and emissions at the same time. The smart electronics and software also provide valuable data on operating parameters that can be used for machine health diagnostics and allow remote performance monitoring, with alerts when maintenance is due or faults need to be addressed. For fleet users this can deliver better utilisation and can also help drive down operating costs.The need for new low emissions engines in machines to meet EU and North American regulations has been aided by the developments in transmissions in recent generation machines. This development continues too, with key manufacturers offering major innovations to the sector.
Hybrid drives have been used in a number of construction machine prototypes in recent years, with various innovative systems having been developed, but few have reached series production.
Transmission specialist
The solution designed by Bonfiglioli in conjunction with CIFA-Zoomlion comprises a gearbox of Bonfiglioli’s 500 Series coupled to an AC electric motor that provides normal power, and a DC electric motor for emergency use. This new solution improves energy efficiency and reduces fuel consumption, but also helps cut cement mixer truck operating costs. Performance is improved too as rotation speed control is more accurate and operating noise levels are lower due to the electric motor and the helical tooth profile of the high speed gearbox stage. In the event of a failure, the back-up DC motor eliminates the risk of failure of the drum unloading system. The new Bonfiglioli solution is designed for use with medium/large mixer trucks that have medium/long delivery distances to travel. Drum rotation speed is from 15-22rpm and capacity of 6-14m3. The gearbox of the new solution has a reduction ratio of 1:220 (1:2200 in emergency mode) and can transmit a maximum torque of 35,000Nm (rated torque of 21,500Nm). The main motor has a power rating of 40kW and is liquid cooled.
Designed for more conventional purposes the new track drives from Comer Industries are said to be more compact, flexible and robust than the units they replace. The new series PGRF 7003, 9003 and 11003 track drives are said to have been extensively upgraded from the units they replace. In addition, the firm’s new S-228-238 rigid and steering differential axles have been developed using a similar concept to the smaller S128 axle. These are said to be more compact, easily installed and suitable for equipping machines with a gross vehicle weight up to 24tonnes and 100kW power.
From
Meanwhile Oerlikon Fairfield has new drive solutions for large track-driven equipment. The CT65, CT90 and CT130 Torque-Hub drives provide maximum output torque ratings of 65,000Nm, 90,000Nm or 130,000Nm and a choice of gear reduction ratios from 70:1 up to 147:1. These triple planetary drive solutions extend the range of the Fairfield’s commercially successful final drives into larger mobile equipment applications including excavators, track-driven trenchers, drilling machines, tool carriers and cranes.
ZF is unveiling its Ergopower efficiency package that combines the cPower continuously variable transmission with the ZF Hybrid module that should be commercially available in the future. The cPower unit is a hydromechanical variable transmission that combines hydrostatic drive pumps with a mechanical powershift gearbox. Available for use in a range of machines, including wheeled loaders, telehandlers, graders and wheeled excavators, ZF claims that HVT can save up to 25% in fuel costs. The firm’s hybrid system will be able to be used with all forms of ZF transmission and could be incorporated in the transmission or separately in the machine for additional fuel consumption benefits.