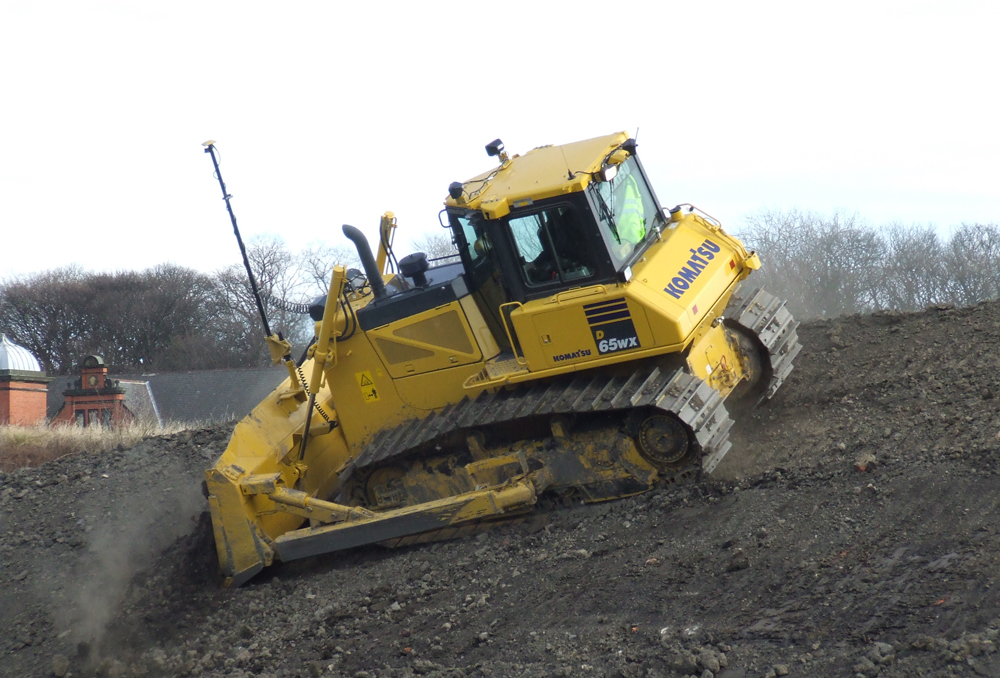
The capabilities of machine control technology have evolved dramatically over the years. At a time when skilled operators are getting older and fewer drivers are coming into the profession, the industry must look at how machine control technology can be taken further to ensure the industry can meet demand, while improving safety and sustainability. The implementation of automated machine control is the first step in achieving this.
It is no secret that the construction industry is facing challenges when it comes to recruiting machine operators. Stereotypically viewed as having tough working conditions and less job security, the sector has particular trouble attracting young people and, as a result, there are fewer and fewer operators entering the profession. In fact, in 2016 the European Centre for the Development of Vocational Training (CEDEFOP) estimated that around one million new and replacement workers will be needed in the European construction sector by 2025 to fill vacancies like these.
Due to this lack of fresh talent entering the industry, the essential skills that experienced operators have honed over the years are being lost as they retire. Should this trend continue, the sector will experience a shortage of good operators and the quality and productivity of projects will be impacted by a significant skills gap.
Despite this predicament, it is not all doom and gloom. Upskilling current operators and those in training using machine control technology can help the industry to address the skills shortage. By placing the responsibility for accuracy and speed in the hands of performance enhancing machine control technology, new or less-skilled operators can perform like a professional and even the most experienced operators can work better and faster.
Using satellite data and 3D models, machine control technology enables operators to accurately position machinery, check grade, automate equipment functions and collect data. Used on earthworks equipment since the late 1990s, the technology allows decisions to be made based on data, rather than relying on fallible traditional methods or the skill and experience of the operator which, as mentioned, is often in short supply. What’s more, it actually increases operators’ productivity and accuracy, while shaving vast amounts of time and money off projects.
With the demand for new infrastructure high and a desperate need to address the skills gap, the construction industry has taken steps to tackle these challenges through automated machine control.
Traditionally not as prevalent on construction sites as it is in other industries like manufacturing, in recent years, automation has been used on construction equipment like graders and dozers to improve project efficiency. Now, with an increased need for productivity across all areas of construction, and with technology advancing, automated machine control is also being adopted across excavators to increase productivity.
Through the use of automatic machine control systems, operators can automatically control digging depth and the bucket angle, guaranteeing that they are on grade every time and avoiding over-digging. Consequently, both new and experienced operators have estimated an increase in productivity of around 30% – saving time and money. By only moving the earth that operators need to, and through avoiding over-digging, operators also save fuel and unnecessary transportation of materials – saving additional costs, while improving sustainability onsite.
Thanks to modern-day onboard connectivity, these automated machine control systems can also receive data files from the office and send back up-to-date information on performance, ensuring that teams can monitor onsite progress and make amends to designs in real time, even when working remotely.
Automated 3D machine control systems offer the most advanced and precise GPS positioning technology and use the latest sensors to ensure that operators receive real-time, dynamic, on-screen bucket location and design views. With access to real-time designs, operators can cut more accurately and check against complex designs in the cab, removing the need for someone to check the grade from the trench – a huge safety benefit.
Undoubtedly, machine control has come a long way. However, automation is just the first step for this technology. In the future, as well as automated angle and depth control, the whole excavation process looks set to become automated, improving productivity across the entire construction workflow.
Using automated machine control technology and digital management tools, machines will be able to act as sensors, monitoring the progress of projects and sharing accurate reports on productivity. These reports will then feed into the wider construction workflow, synchronising with other functions within the project and associated equipment, such as trucks, to streamline the construction process and avoid delays. For example, currently, on most sites you can generally only tell that more excavators are needed if there is a queue of trucks onsite waiting. In the future, thanks to automated construction workflows, project managers will be able to send the right number of trucks based on the volume of earth that has been dug using reports from the machines – reducing inefficiencies through synchronisation of all equipment, improving safety and minimising impact on the environment.
As the demand for productivity grows, so too does the demand for automated machine control and upskilled operators in the industry. Increasing speed and productivity on projects, improving safety and turning good operators into great ones, modern automated machine control systems can help alleviate some of the challenges the construction industry currently faces. And, with the right level of adoption, soon entire workflows will be automated, dramatically increasing productivity and giving the industry a fighting chance at meeting global construction targets.