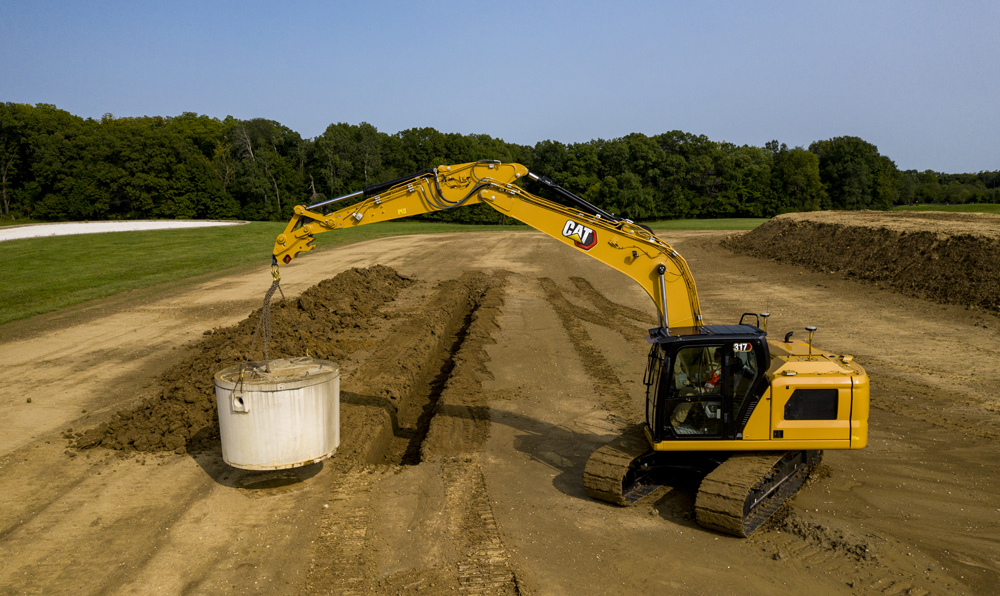
Hydraulic excavators remain the most popular types of construction machine worldwide, with manufacturers keen to deliver high performance. Improvements in output and technology are ensuring the latest units are more productive than ever before.
Caterpillar says its 317 and 317 GC Next Gen excavators offer improved performance, increased efficiency and lower owning and operating costs than previous models. The new 317 excavator features multiple Cat technologies to boost operating efficiencies by up to 45%. The versatile 317 GC lowers maintenance costs by up to 20%.
Three available engine operating modes can match performance to the job, resulting in fuel savings. Smart modes automatically match engine and hydraulic power to conditions to improve efficiency, while ECO mode minimises fuel consumption on less demanding applications. Available for the 317 Next Gen excavator, Power mode provides maximum power and productivity for demanding projects.
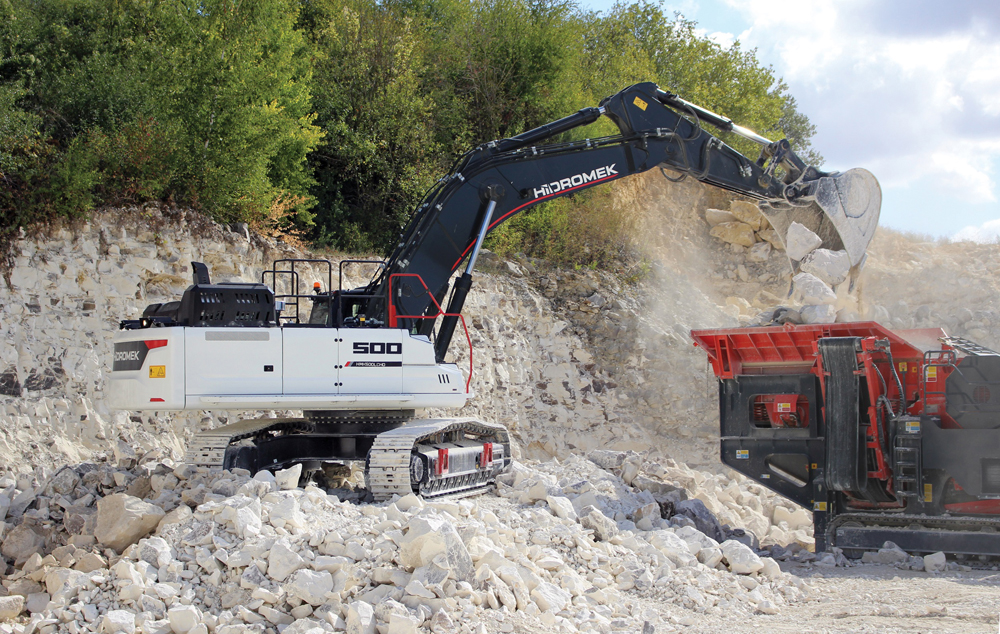
The hydraulics are said to offer power and efficiency for precise digging. Both the new Cat 317 and 317 GC models come standard with new Cat Advansys bucket tips, which offer improved wear life, retention and change out times.
Technology is said to boost operator efficiency by up to 45%, increasing productivity. Standard Cat Grade Assist automates boom, stick and bucket movements, so operators can stay on grade with single lever digging. Cat Grade with 2D guides depth, slope and horizontal distance to grade through the touchscreen monitor. The system is upgradable to Cat Grade with Advance 2D or Cat Grade with 3D.
Operators receive on-the-go weighing and real-time payload through the Cat Payload technology fitted as standard. Critical operating data such as payload summaries, fuel usage and fault codes are captured by standard Product Link technology and accessed by fleet managers and office personnel via Vision Link and the Cat App to boost fleet management efficiency.
Remote Troubleshoot analyses machine operating data, allowing technicians to run diagnostic testing without affecting productivity. Remote Flash can deliver the most current version of onboard software remotely.
Extended maintenance intervals for the Cat 317 and 317 GC excavators lower maintenance costs by up to 20% over the previous series. A new hydraulic oil filter delivers improved filtration and a 50% longer, 3,000 hour change interval.
The 317 GC comes standard with the Cat comfort cab, while the 317 offers the choice between deluxe and premium cab designs. These Next Gen excavators come standard with rearview and right-hand sideview cameras to improve visibility of the operating area.
HIDROMEK’s new HMK 500 LHCD excavator is the biggest machine in the firm’s H4 Series. Durability is claimed due to its heavy duty undercarriage and structure. The 52tonne machine uses a 3.2m3 bucket as standard and is said to offer increased performance and productivity than the firm’s earlier model for this class. Improvements to the arm and boom structure, undercarriage and attachment groups suit operation in applications with severe operating conditions.
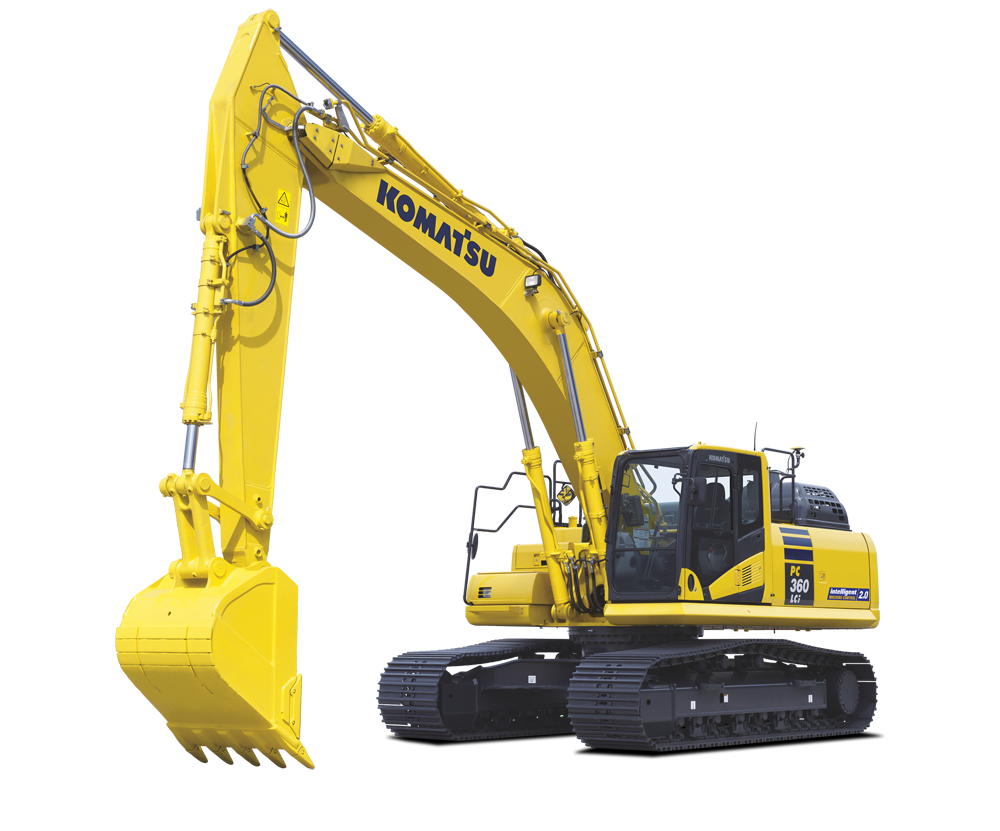
The HMK 500 LCHD is said to offer ease of control, a high comfort cab with all-round visibility, OPERA Control System and touchscreen control panel. The electronics in the H4 Series excavators are said to be designed to optimise engine and hydraulic performance, providing fuel savings and high output. An eco-mode will stop the engine if it runs at idle for a set period. The safe fuel transfer pump stops the pump automatically when the tank is full and is also activated when the pump does not transfer fuel for 30 seconds. Power boost technology is activated automatically when the machine needs extra power, providing the performance for the job in hand.
Kobelco is aiming its next generation SK210LC-11 at one of the most competitive segments in the excavator class. Two versions are offered, the SK210LC-11 and SK210NLC-11, with the latter being the narrow undercarriage variant.
The highly sophisticated SK210LC-11 is said to offer high performance, efficiency and productivity and uses Kobelco’s PERFORMANCE X DESIGN concept for improved operability and comfort in this competitive class.
The machine is equipped with the Stage V emissions compliant Hino diesel, delivering 124kW. The machine offers 143kN digging force (157kN with power boost) and 228kN drawbar pulling force. Smooth and steady operation is claimed even when moving heavy objects across the jobsite due to the independent travel function, which dedicates one hydraulic pump to travel and one to the attachment on a continuous basis. The machine offers operating weights of 21.9-23.5tonnes, depending on specifications. This increased weight over the earlier model is said to boost stability and lifting capacity. When fitted with the standard 4.3tonne counterweight, the SK210LC-11 suits general construction duties. The optional 4.9tonne counterweight can be fitted for heavy-duty work such as handling heavy or complex attachments including tilt rotators.
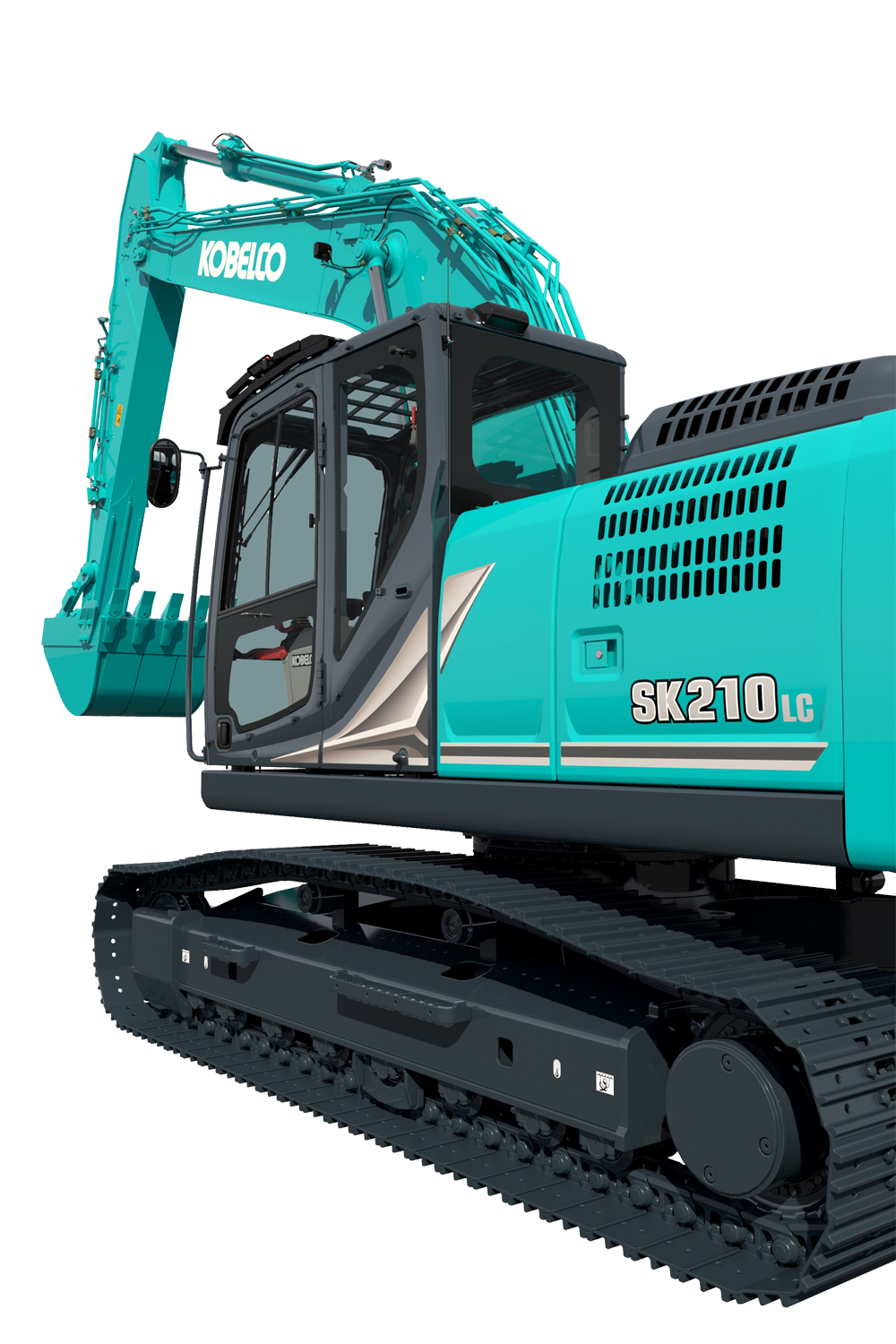
The firm claims that while this size class is highly competitive, the new Kobelco SK210LC-11 holds its own against the competition. It is said to offer both performance and stability, with high lifting performance and low fuel consumption.
The new Komatsu PC360LCi-11 and PC360NLCi-11 with iMC 2.0 are excavators that are claimed to offer high productivity earthmoving and precision grading. These new models further expand the range and benefit from the sophisticated iMC technology, which boosts performance for a range of duties including grading as well as truck loading.
Operating weights of the PC360LCi/NLCi-11 range from 35.77-36.85tonnes, depending on the specification, while the machine has a maximum recommended bucket capacity of 2.66m3. Power comes from a fuel-efficient Komatsu diesel with a power output of 202kW at 1950rpm and which meets Tier 4 Final/Stage V5 emissions requirements. The firm is equipped with the latest KOMTRAX telematics and Komatsu CARE maintenance package, which are said to offer optimum efficiency and uptime, improved fleet management and support, while also protecting against misuse.
Komatsu says that its sophisticated Machine Control 2.0 package is a factory-integrated intelligent machine control system. This offers proven, automated digging control as well as high quality, reliability, accuracy and performance, according to the firm.
The PC360LCi-11 and PC360NLCi-11 offer advanced, intelligent features that boost machine and jobsite productivity and efficiency. The new Komatsu Auto Tilt Control for tilting buckets makes operations on slope and ditch work easier, limits under-digging and increases bucket fill. The bucket automatically tilts to the design surface with no need for the operator to intervene. With new Bucket Angle Hold, the operator no longer needs to use the lever to maintain bucket angle through grading pass. Once the desired angle is selected, this feature automatically maintains it as the arm moves in.
The new iMC 2.0 monitor is slimmer, lighter and more compact, has increased memory capacity and fast processing speed. Komatsu iMC 2.0 also boosts versatility due to the new IMU sensor for tilt buckets. Easily mounted and calibrated, it increases attachment and machine utilisation, allowing different tilting buckets to be integrated to the excavator’s control system. The machine has the sophisticated Komatsu intelligent Machine Control features: Auto Stop Control; Grade Assist; and Minimum Distance Control.
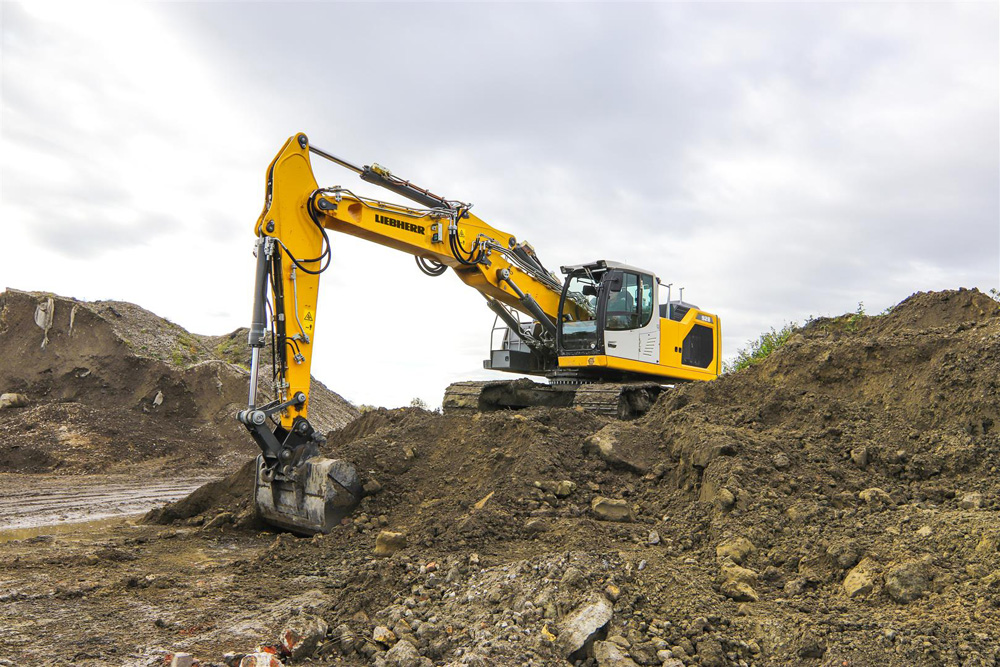
Liebherr’s R 928 G8 is the latest addition to the firm’s generation 8 excavator family meanwhile. It uses the modular technology of the firm’s new range and has a weight less than 30tonnes in various configurations, while it offers a high drawbar pull and load-bearing capacity according to the firm.
The new model fits into the range between the R 926 G8 and the R 930 G8 models in the Generation 8 series, which includes models with weights of 22-45tonnes. This new model is based on existing, high-performance components. This new, weight-optimised combination should reduce the transport problems of many customers.
The R 928 G8 has several features in common with the R 926 G8 and R 930 G8: The same superstructure and equipment as the R 926 G8 and the same LC or NLC undercarriage as the R 930 G8. The performance of the R 928 G8 lies between the R 926 G8 and the R 930 G8.
The firm claims that the machine has a high drawbar pull, good load-bearing capacity and a large bucket. Optimised weight makes it easier to transport. The performance of the R 928 G8 allows it to compete against machines that are heavier than the R 926 G8 and lighter than the R 930 G8 according to Liebherr.
The firm says that its Generation 8 models develop higher tear and breakout forces compared to the previous generation. The new crawler excavators achieve higher levels of performance under site conditions, while a new equipment concept enables the load curve to be optimised and the inertia in the rotary drive to be improved, reducing fuel consumption. The new, robust X-form undercarriages boosts stability.