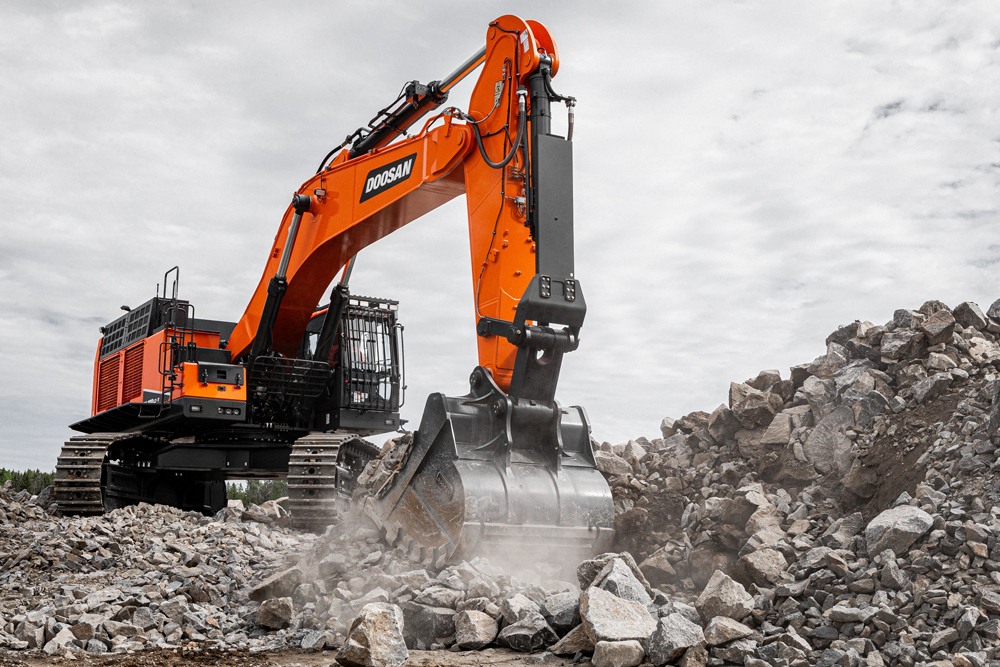
Hydraulic excavators top the bill in terms of sales for the construction machinery sector. With so much demand for so many machines, it should come as no surprise that this is also one of the most competitive segments for the suppliers. To ensure that their products retain a competitive edge, improvements and advanced features are being introduced from an array of firms.
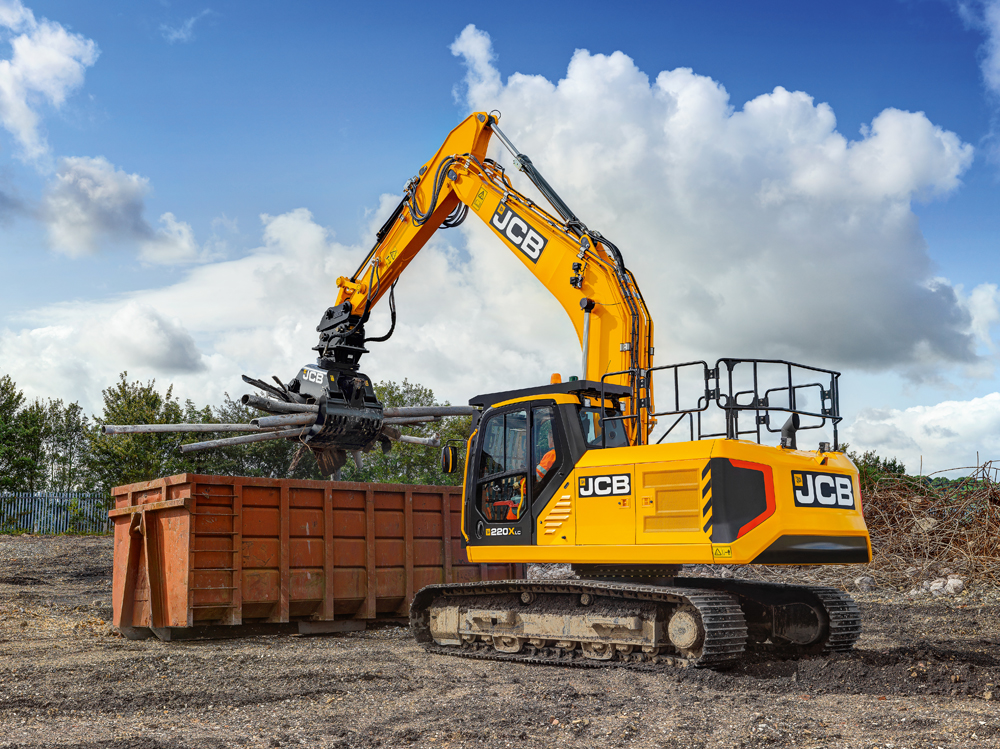
Doosan is offering two new high- performance excavators, the 50tonne class DX530LC-7 and the 80tonne class DX800LC-7.
The DX530LC-7 meets Stage V emissions requirements, with power from the new Scania DC13 Stage V compliant diesel engine, providing a higher power output of 294kW. Low emissions are claimed due to the efficient DOC/DPF+SCR after-treatment technology.
The performance of the DC13 engine is combined with a Virtual Bleed Off (VBO) hydraulic system (D-Ecopower+) and the new generation Smart Power Control Technology (SPC3), boosting fuel efficiency by 11%. Increased pump capacity and the higher power of the engine produces up to an 8% increase in productivity.
The DX800LC-7 is the largest excavator ever manufactured by Doosan and is powered by the new Stage V version of the proven Perkins 2506J diesel, delivering 403kW. The high output of the engine is also combined with the Virtual Bleed Off (VBO) hydraulic system (D-Ecopower+), providing a hydraulic flow of 1008litres/min and a high system pressure of 343bar, providing high performance and productivity. However, the machine is also said to offer low fuel consumption and smooth controls, featuring bucket sizes from 4.6-5.2m3. Other standard features include the 360° around view monitoring system and powerful LED work lights for night working, as well as the SKF auto greasing system, helping to reduce maintenance needs.
The operator can switch between boom or swing modes, allowing the machine to be matched to the application. Faster working speeds are claimed due to the two-spool boom down regeneration system, which helps lower fuel consumption. The two-spool hydraulic system for the bucket cylinder increases hydraulic flow and the working speed of the bucket, again reducing fuel consumption.
Hitachi says that its innovative TRIAS hydraulic system provides high performance, while also ensuring that fuel consumption is minimised. The system features three hydraulic pumps rather than the two as used in most machines. The third pump is said to help to maximise efficiency and productivity, without sacrificing fuel economy. The firm says that it achieves this by reducing the loss of hydraulic pressure, providing significant savings in fuel costs.
The firm’s latest TRIAS III and HIOS V hydraulic systems are fitted to its Hitachi Zaxis-7 excavators and is said to offer a number of new features for operators. According to the firm, the system can cut fuel consumption by up to 20%, while also boosting working efficiency.
The firm says that customers can control fuel efficiency using the new ECO gauge and the machines can also be monitored remotely with the Owner’s Site, ConSite and the ConSite Pocket app. Sensors monitoring engine and hydraulic oil are said to contribute to preventative maintenance and help to reduce downtime. The new Zaxis-7 excavators benefiting from this technology suit a range of duties and the three mid-size models weigh from 26.4-37.5tonnes, while the four large models range from 49.5-87.5tonnes. Power comes from engines rated at 140kW-210kW for the mid-size models and from 296-382kW for the large machines. All the machines are offered in Tier 4 Final/Stage V emissions compliant versions.
JCB is introducing Stage V compliant versions of the 140X, 150X and 220X excavators, all of which are powered by JCB’s 4.8litre DieselMax 448 engine. For the 140X and 150X this delivers 81kW and an increase in torque of 135Nm to 516Nm. The 448 engine in the 220X meanwhile is rated at 129kW and 690Nm of torque. Key features of the new machines include a combined SCR, DPF and DOC emissions control package that offers reduced service intervals. And Tier 4 Final models will remain available in non-Stage V territories. The new machines offer reduced daily checks and extended service intervals as well as the new X Series hydraulic system, offering speed and controllability. In addition, the machines feature automatic engine shutdown, to reduce fuel consumption and emissions when the excavator is not in use.
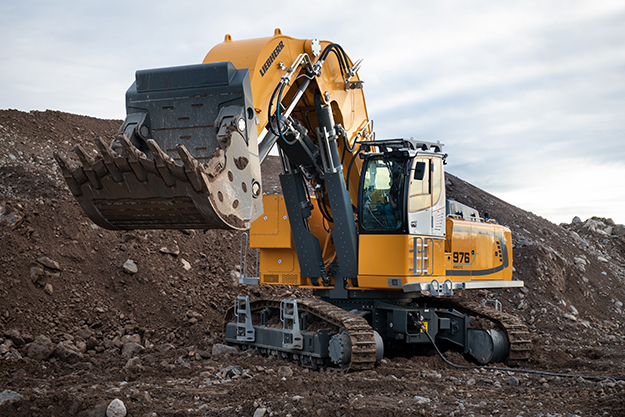
The excavators are equipped with a new Selective Catalytic Reduction Filter (SCR-F) that comprises a combined SCR, Diesel Particulate Filter (DPF) and Diesel Oxidation Catalyst (DOC) with a large soot holding capacity. There is no longer a requirement for Exhaust Gas Recirculation (EGR) and the system has been removed from the new inlet manifold. The machines require fewer daily checks than their predecessors, with extended hydraulic oil service intervals and ground level access to all inspection areas. The new 140X, 150X and 220X excavators can now be supplied GPS-ready from the factory, while bi-directional bucket hose burst check valves are available, to work with new attachments.
Liebherr is now offering electric excavators, the R 976-E and the R 980 SME-E, for high-output extraction operations. The R 976-E replaces the ER 974 B. The excavators and their electric power system were designed and produced entirely by Liebherr. The machines weigh 90tonnes and 100tonnes respectively and are available in backhoe and shovel versions, offering low working noise and zero exhaust emissions in operation.
Both machine benefit from tried and tested electric systems, developed within Liebherr. The 400kW electric system in the Liebherr
R 976-E 400 kW crawler excavator is supplied with 6000V power via a cable connection, with the cable inlet in the centre of the undercarriage, or on the sides if requested. A motor cable drum is also available as an option. The machine is powered by a high- voltage 6000V/50Hz current collector. A switch cabinet transformer (high voltage/low voltage) and a low voltage cabinet for power distribution and control of 690V, 230V and 24V networks are located on the upper carriage.
The technology used in the R 976-E and R 980 SME-E offers advantages. An electric motor offers a longer service life and also allows high productivity. The R 976-E’s low-voltage electric squirrel-cage engine drives the hydraulic system. The engine features heat shielding on bearings and motor windings. Reduced maintenance and lower operating costs also make an electric excavator more cost-effective than a comparable diesel machine.
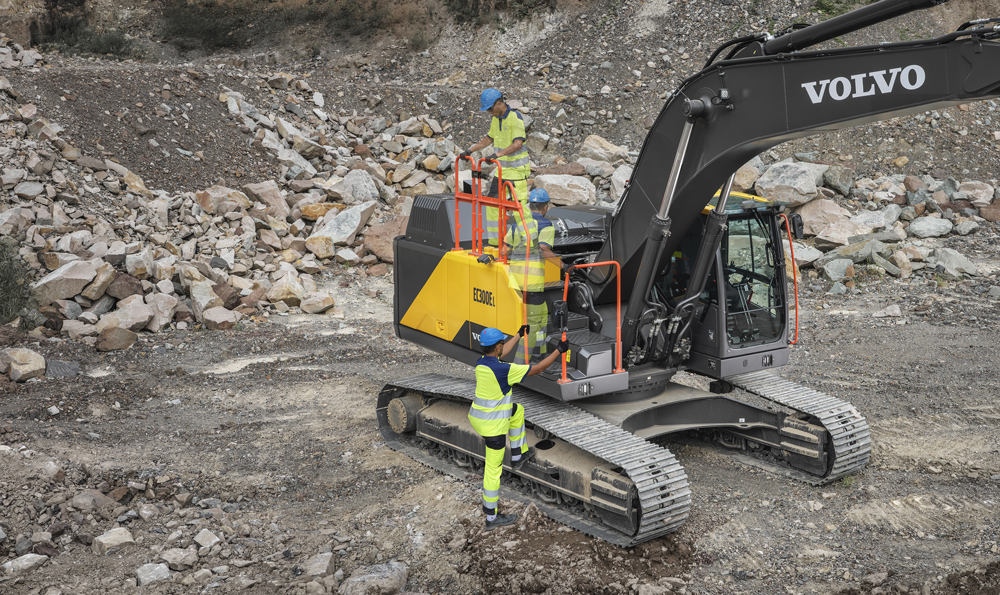
Volvo CE says that its new EC250E and EC300E excavators are heavy-duty machines that, depending on specifications, weigh 26-31.5tonnes and 30.2-36.8tonnes respectively. These machines offer up to 10% improvements in fuel efficiency, due to intelligent electro-hydraulics, the ECO mode and selectable work modes, and the new D8M Volvo engine. This upgraded engine reduces rpm, while delivering a 5% increase in power. The EC300E also has a 700kg heavier counterweight, providing greater stability and a 5% increase in across lifting capacity.
Both machines benefit from performance gains due to new priority functions, which increase. Boom-down speed control is adjustable for precision tasks, while jack-up speed has been increased. Operators benefit from improved response times due to an electric control joystick and electric travel pedals, as well as the optional Dig Assist apps, powered by the Volvo Co-Pilot in-cab tablet. These include 2D, In-Field Design, 3D software packages and On-Board Weighing. Volvo
Active Control also boosts digging accuracy, allowing jobs to be completed up to 45% faster due to automated boom and bucket movements. Operators can set a swing fence, height limit, and depth limit to avoid contact with side and overhead obstacles such as power lines, and underground hazards such as pipes and cables.
With the new Steelwrist Auto Connect Quick Coupler, operators can easily connect hydraulic attachments from the comfort of the cab. And thanks to compatibility with Steelwrist, Engcon, Rototilt, SMP and OilQuick tiltrotators. The factory-fitted tiltrotator preparation system allows operators to control the excavator and tiltrotator using the joysticks.
The new D8M Volvo engine offers reliability, lower service requirements and an auto engine regeneration, delivering 168kW in the EC250E and 189kW in the EC300E. The updated hydraulics have fewer hoses, which increases reliability. Time and maintenance costs are reduced due to the engine oil and filter change intervals being doubled to 1,000 hours.