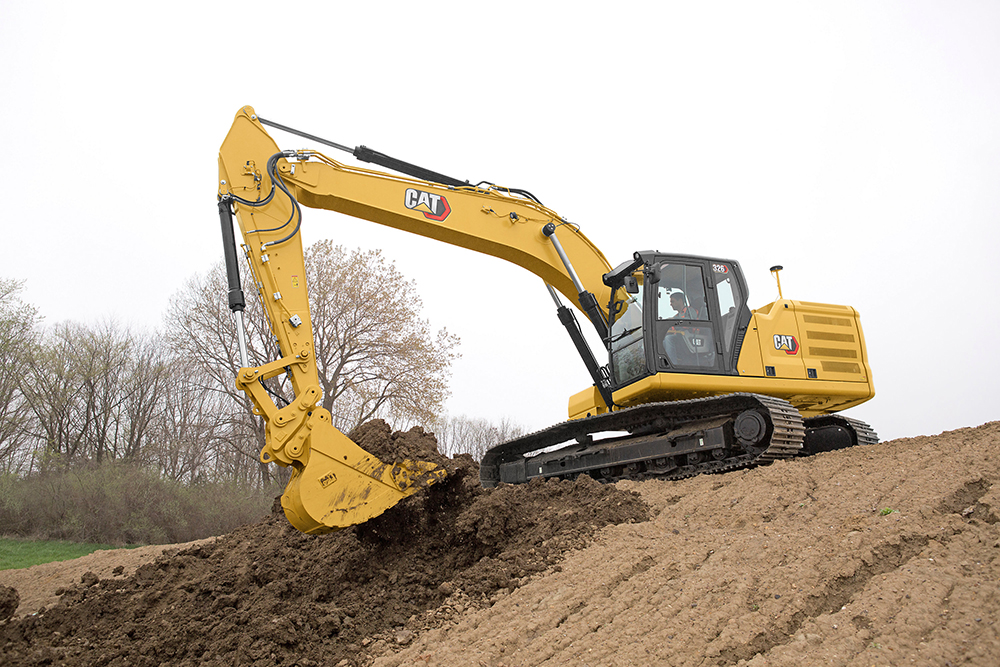
Several major manufacturers are improving and upgrading their excavator and wheeled loader offerings at present. These will meet the demands of customers in a range of markets around the world.
From Caterpillar comes the new 326 excavator, which the firm claims delivers premium performance that helps boost efficiency by up to 45% over previous models. This 26tonne class machine offers reductions in fuel consumption and maintenance costs, combined with high reliability at a low cost/hour performance.
The machine features remote starting using a Bluetooth key fob as well as an Operator ID function for programming of power mode and joystick preferences. The machine’s touchscreen monitor delivers navigation through the menus and includes a digital version of the operator manual.
Power comes from a 151kW Cat 7.1 engine that offers up to 15% lower fuel consumption than the F Series. The machine has three selectable power modes and one-touch low idle with automatic engine speed control. It also has a high ambient temperature operating capacity of 52°C and standard cold start capacity of -18°C.
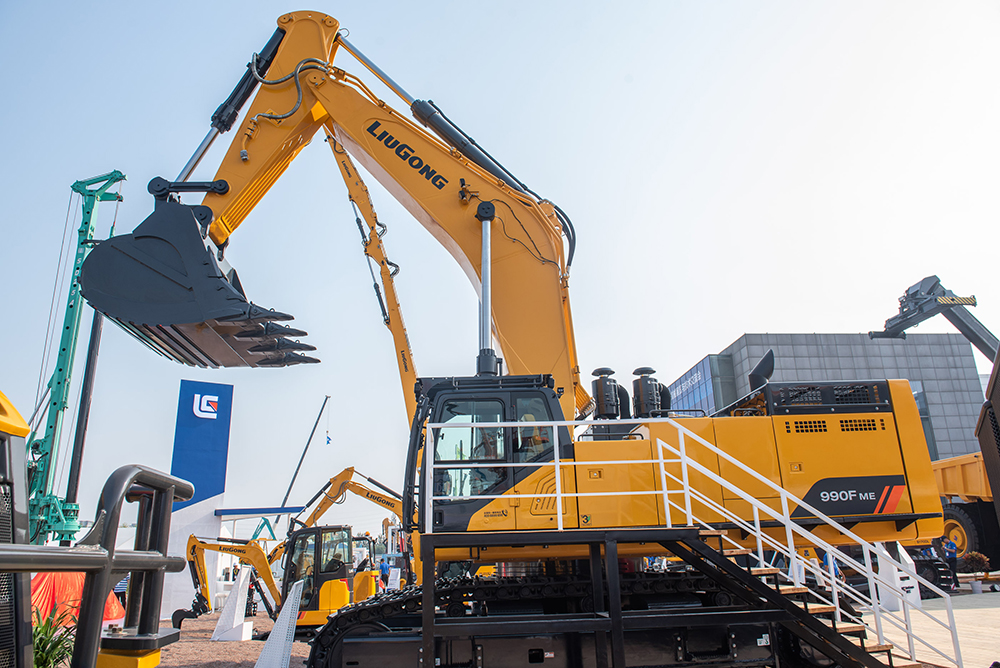
Important operating features include a 12% improvement in swing torque; SMART-mode operation that matches engine speed and hydraulic power to digging conditions; and an optional Smartboom that allows the boom to lower freely without using pump flow.
The standard Cat Grade with 2D system allows operators to reach desired grade quickly and accurately. Customers can upgrade the standard 2D system to Cat Grade with Advanced 2D or 3D to fit application needs. The machine also has the Cat Payload onboard weighing system as standard, while VisionLink allows companies to manage production targets remotely through data gathered by Payload.
Doosan says that its new DX350LC-7 is the first Stage V model to feature Doosan’s innovative D-ECOPOWER technology. This package offers higher productivity and lower fuel consumption, as well as smoother controls.
As with the new DX300LC-7 30tonne Stage V model launched earlier, the 36tonne DX350LC-7 is said to provide better operator comfort, uptime and return on investment, along with increased power, robustness and versatility.
Doosan’s D-ECOPOWER technology uses an electronic pressure-controlled pump within a closed centre hydraulic system to provide gains of up to 26% in productivity and up to 12% in fuel consumption, depending on the mode selected.
To meet Stage V engine emissions regulations, the new DX350LC-7 excavator is powered by the latest generation Doosan DL08 diesel engine, providing 209kW. The DL08 engine exceeds Stage V regulations without exhaust gas recirculation (EGR). This is combined with super-efficient DOC/DPF+SCR aftertreatment technology to ensure minimal emissions. No maintenance of the diesel particulate filter (DPF) is required until the machine has operated for 8000 hours.
As standard, 360° cameras provide full visibility around the excavator and allow the operator to see a top-down view of the area outside the machine.
The new DX350LC-7 model also features the DoosanConnect wireless fleet monitoring system, which offers a web-based management solution for monitoring performance and the security of machines.
LiuGong’s new F-Series excavators are claimed to offer key performance gains over earlier generation machines.
Compared with the previous generations of excavators, the F-series excavators have more models and size classes, including standard variants for the Chinese market and short-tail and zero-tail swing versions for the Western European and North American markets. The products comply with the latest regulations of China and Europe on emissions. The series has platforms with weights ranging up to 90tonnes, which covers more than 90% of the global market demand.
The F series excavators are equipped with the latest electronically controlled hydraulic system consisting of a main pump with large displacement, a low-speed and high-torque engine and a main electro-hydraulic proportional control valve for better management of flow distribution. With these systems, the F-series excavators offer high operating efficiency and fuel savings of 15-20% over the previous generation.
Key model introductions are the 922F, 926F, 936F and 990F models. These weigh in at 22.5tonnes, 26.5tonnes, 37tonnes and 93tonnes and with engine power outputs of 125kW, 145kW, 240kW and 447.5kW respectively.
Loaders
Meanwhile in the wheeled loader sector, Hyundai Construction Equipment Europe (HCEE) is offering three Stage V compliant models for its HL900 wheeled loader A-Series. The HL940A, HL955A and the HL960A benefit from a range of improvements including better safety, performance and productivity.
The firm claims that these three models offer gains in fuel efficiency, safety, longer uptime and improved fleet management.
Key features include the latest diesel technology from Cummins, power smart modes, a new cab, an optional remote door control and an optional AAVM camera system (optional) and rear radar system. Other upgrades include a new engine hood design offering better visibility, upgrades to the axle, and linkage and MCV improvement.
Power comes from a Cummins B6.7 engine, with an all-in-one exhaust aftertreatment system. The engine is easier to maintain, due to its connected diagnostics to Hi-Mate. It offers long service intervals and a DPF soot reset function for cleaning. Notably, the exhaust aftertreatment system does not need a manual DPF regeneration and is EGR free.
The intelligent work mode (IWM) menu allows for three engine modes: Power, Power Smart and Economy, aiming for full engine power or reduced fuel consumption depending on the application.
The Hyundai A-series wheeled loaders are equipped as standard with a rear-view camera developed in-house. For increased safety on the jobsite, the advanced AAVM 4-camera system is available as an option. This four-camera system provides warnings when people or dangerous objects are detected. Four cameras film at each side of the machine which means the AVM system offers a 360° overview of the machine's surroundings. The IMOD indicates all movements around the machine. Movement is shown on the monitor by putting a rectangle around the moving object or by indicating the side at which there is movement by arrows.
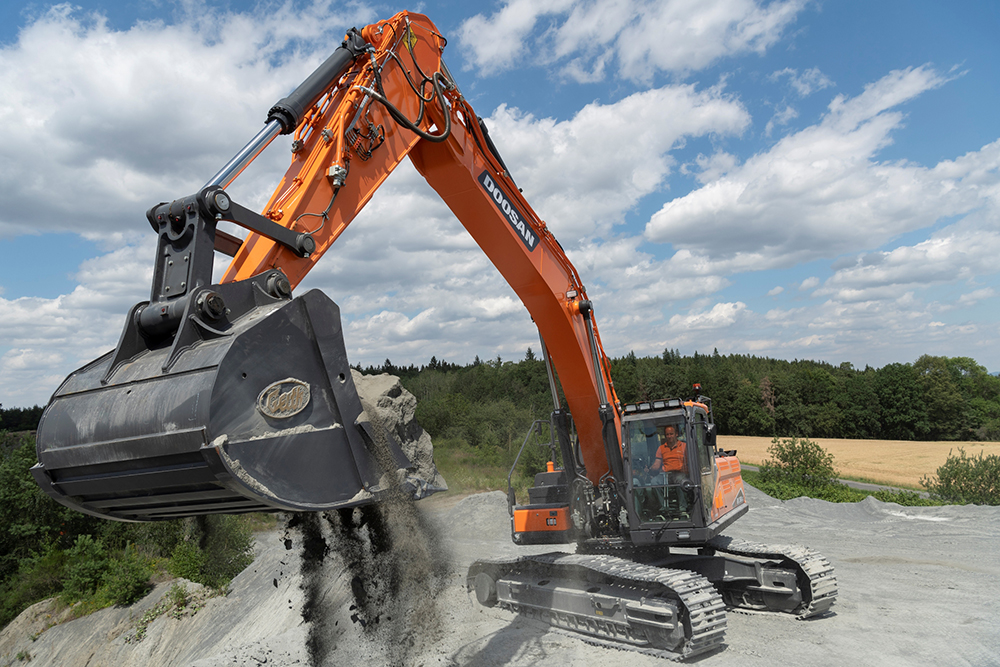
The HL955A and HL960A come with an increased rear axle capacity for better durability. Both machines can be ordered with an optional heavy-duty front axle. The HL940A and HL955A come with a new parallel Z-Bar linkage providing parallel lift.
Moving up the size scale, Komatsu is now introducing its high-performing WA475-10 wheeled loader, which replaces the previous generation WA475. Power comes from a diesel rated at 219kW and which meets the stringent Stage V emissions requirements for Europe, as well as the Tier 4 Final legislation.
First seen in prototype form at the bauma exhibition in Munich in Spring 2019, the machine’s key feature is its innovative, Komatsu-developed driveline. This K-HMT system utilises a combination of both hydrostatic and mechanical drive to deliver power smoothly and effectively. The combined powershift and hydrostatic transmission is integrated electronically with the engine to ensure effective moderation between the parallel drive systems. At low travel speeds the hydrostatic system allows precise control, while at high speeds the mechanical drive provides high torque. The system ensures that the engine runs in its optimum range and product manager Shayan Dadgar said, “We have a variable rate of output. The rpm is lower but we drive in the efficiency zone.”
He said that because of the efficiency of the integrated mechanical and hydrostatic transmission matched to the engine, fuel savings of up to €32,000 can be achieved over a five year/10,000 working hour operating life (based on average fuel prices across Europe). At low speed the hydrostatic system allows precise movements and Dadgar added, ”It’s also much smoother to operate.”
High efficiency is delivered through the power range due to the new transmission and Komatsu claims that the machine offers fuel savings of up to 30% over the outgoing model, predominantly due to its sophisticated driveline. Of note is that Komatsu has the confidence in its sophisticated new technology to offer the WA475-10 with a five year/10,000 hour warranty covering the driveline.
The engine itself benefits from performance gains in addition to its low emissions, providing a 15% increase in torque at lower rpm. The fuel filter system life is now 1,000 hours compared with 500 hours on the previous model while coolant does not need replacing until 6,000 hours, compared with 5,000 hours for the outgoing version. The DPF meanwhile achieves 98% passive regeneration and Dadgar claimed, “We have the best aftertreatment system on the market.”
The cab is larger than on previous models giving plenty of space for the operator, while large glass windows give a clear all-round view. Dadgar said, “It’s the biggest cab we’ve ever had on a wheeled loader.”
Novel control features include a function that raises the boom quickly without the operator needing to increase engine rpm. Another is the button that allows the operator to shake out any material retained in the bucket. And there is also a fast arm lower function to return the bucket to carry height. The bucket configuration has been refined to optimise filling when entering the muckpile.
As with other machines in the range, the loader is equipped with Komatsu’s remote monitoring package, KomTrax. This latest version allows more effective fleet management remotely allowing monitoring of operating parameters and providing alerts for service issues. In addition the system can track operator performance and highlight issues that may require amendments to working practices or additional training.