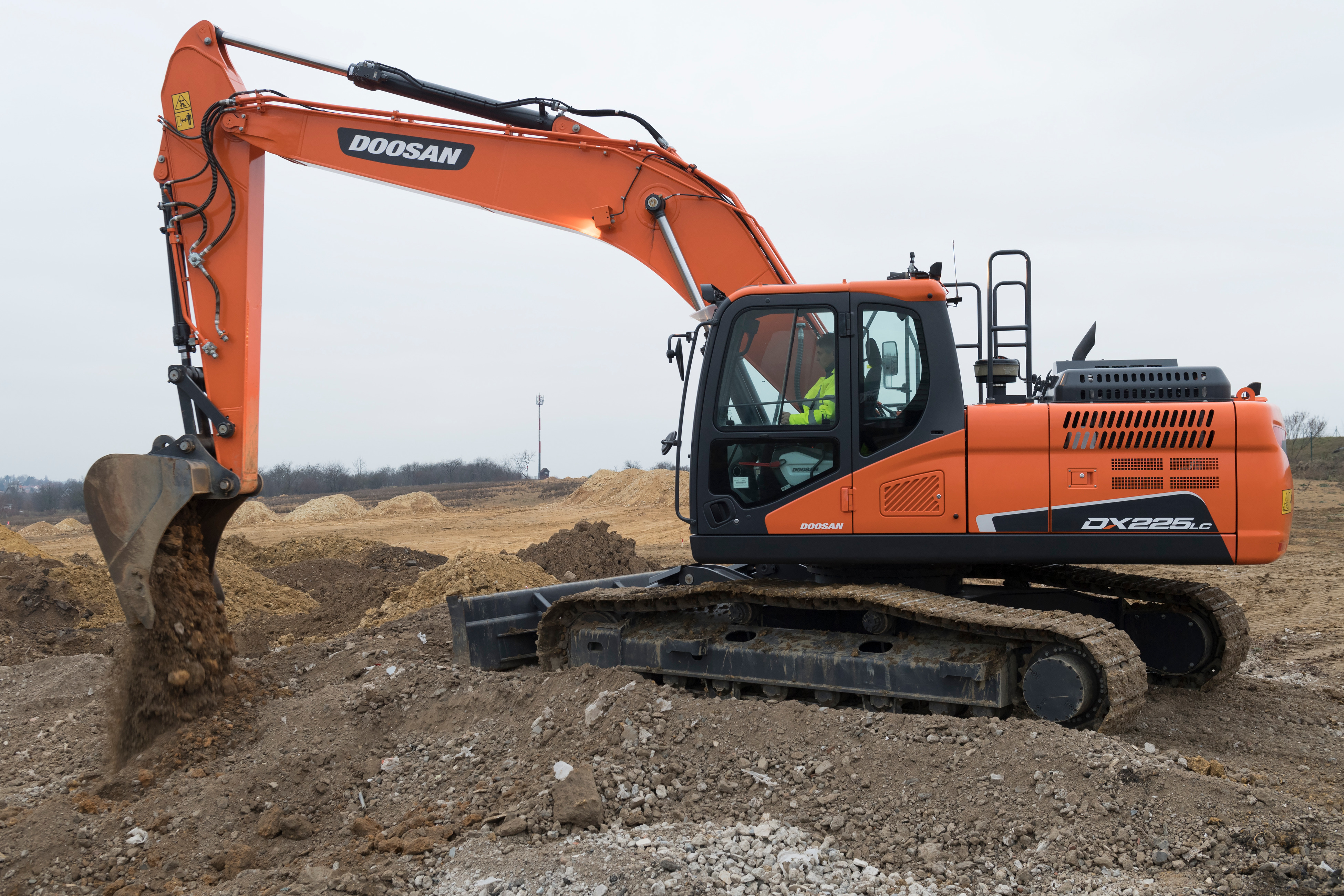
New developments in earthmoving machines continue to help improve working efficiency for contractors. The excavator market is the largest single segment of the construction machine sector, with competition being tough between the major players, and a steady stream of new models coming to market.
New features help deliver an overall 9% increase in fuel efficiency, such as the Smart Power Control (SPC), to optimise the balance between the pumps’ output and the diesel while an Auto Shut-Off saves on fuel and warranty hours.
The DX225LC-5 is factory-installed with the new DoosanConnect wireless fleet monitoring system, providing information about machine performance in a dual mode (satellite, GSM).
All current options including narrow tracks, short and long arms, shoes and hydraulic lines are available for the new DX225LC-5. A new Trimble Ready option is also available, enabling a faster and simplified installation of
The company says that this system allows the engine to meet Tier 4 Final without having to use a Diesel Particulate Filter (DPF), reducing cost and service complexity for the customer. Their introduction means fuel savings for customers of up to 10% on the JS370 and 5% on the JS300 and JS330.
The machine uses a three-pump hydraulic system to provide faster cycle times and increased hydraulic flow for attachments. The rear section of the upper structure has been designed with side-by-side cooling cores, to deliver maximum cooling efficiency within the reduced tailswing.
For high-load operation, the electricity accumulated in the lithium-ion battery allows the generator motor to assist the engine, reducing fuel consumption. During low-load operation, the engine is used to generate electricity in the generator.
Komatsu says the new HB365LC-3 hybrid excavator can reduce fuel consumption by up to 20%. The 36tonne class model features improved hybrid and total-vehicle-control systems, generating that impressive double-digit reduction in fuel consumption, while matching or beating the performance of conventional excavators.
Komatsu’s innovative, fully-electric hybrid system uses an electric swing motor, which captures swing deceleration energy, which is stored in an ultra-capacitor that supplies energy for the swing system. The diesel engine also has a motor/generator for fast charging the capacitor when required, and to increase engine RPM from an ultra-low idle, for quick hydraulic response when boom, arm and bucket controls are activated.
Komatsu says its fully-electric hybrid system is a first due to its 100% electric swing system. The hydraulic power normally needed by the swing system is now completely available for boom, arm and bucket power, improving digging and production.
Moving up the size scale, Komatsu is also offering its PC700LC-11, which weighs from 67.5-69.5tonnes, depending on specification. Power comes from a 327kW diesel that meets Tier 4 Final/Stage IV requirements due to advanced systems such as variable geometry turbocharging and EGR technology. Sophisticated Komatsu hydraulics and electronics help boost efficiency and reduce fuel consumption according to the firm, while the machine also benefits from the company’s equipment management monitoring system (EMMS), which continuously monitors all critical systems, enables preventative maintenance, and helps minimise diagnosis and repair time.
LBX Company has introduced the 72tonne Link-Belt 750 X4 excavator for the US and Canada, with power from an electronically-controlled 382kW
The machine is equipped with the firm’s RemoteCARE GPS-enabled telematics system, which tracks and records routine and major service intervals, as well as machine health, providing more flexibility and control when determining when and where servicing is needed. Flashing diagnostic codes on the monitor quickly alert the operator to potential trouble and an e-mail alert is automatically sent. The system also provides machine location in real time for better job supervision and remote security monitoring.
New wheeled loaders
New hydraulics and electronic controls optimise performance, while the engines are said to be highly responsive as well as being fuel-efficient. According to Case CE, the loaders offer a significantly lower cost/tonne than the models they replace.
Four operating modes improve efficiency in a range of applications while the Case ProCare package is said to minimise operating costs. Offered as standard as a three-year package, ProCare offers the latest telematics technology to make fleet maintenance more efficient and manage running costs.
The wheeled loader features the Volvo fully-automatic power shift system, which helps ensure operation in the optimal, fuel-efficient gear according to speed, kick-down and engine braking.
ADT offering
The ADT market has change considerably in recent years, with far more firms now offering machines. The technical developments continue, with Doosan, John Deere and
The Geofence system can be used to ensure the machine cannot leave a prescribed area, as well as to set speed limits. This forms part of the machine software and can be set up using a Doosan ADT diagnostic tool, allowing adjustment of the boundaries.
The Doosan DA30-5 and DA40-5 ADTs are powered by
John Deere has added to its articulated dump truck (ADT) range, with the introduction of the 260E and 310E trucks. The E Series models have updated styling, new cabs, upgraded chassis and more robust axles.
The 260E has a 23.5tonne payload, while the 310E offers a 28tonne load-carrying capability. Both trucks are powered by Deere 9 litre Tier 4 Final engines driving through ZF eight-speed transmissions, which include a high-capacity retarder. This retarder is said to provide 125% more braking force than previous models. A revised automatic differential lock offers both cross-axle and inter-axle locking, for maximum traction in difficult terrain.
Auto shutdown is included, to stop the engine after a pre-set period of inactivity. The trucks also feature auto dump, descent control, shuttle shifting, hill hold and load assist functions.
Top of the range is the TA400, with power from an EU Stage IV/Tier-4 Final emissions-compliant diesel. The machine is said to offer all-terrain durability and increased performance. To ensure productivity in all haul conditions, the Gen10 TA400’s engine and drivetrain have been optimally matched, utilising automatic adaptive shifting and a pre-selected two-speed transfer box.