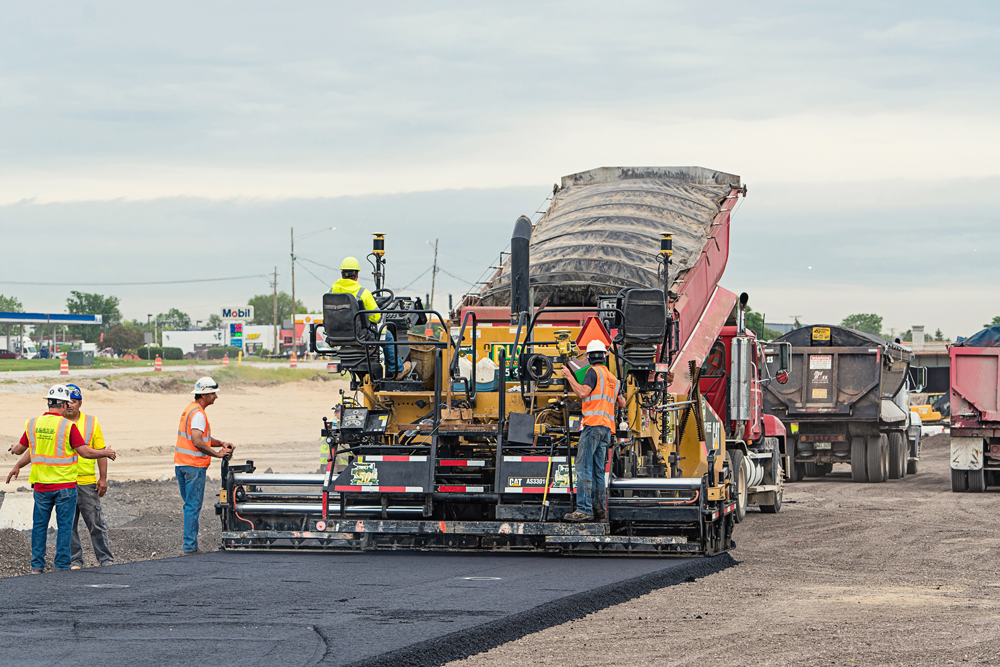
As bad weather and flooding continue to become more erratic, the problem will only get worse, with insurance giant Zurich predicting that the figure in the UK could rise to 650,000 if the government does not implement the £500 million promised to fix the current roadways.
A worrying number of roads worldwide have suffered from extreme neglect over the years and now pose major safety risks as they come to the end of their lifespan. Potholes, standing water, delamination – these are all common issues that have the potential to cause serious damage.
Some of these roads are in such bad condition that a complete redesign of the system is now needed. Naturally, such extensive and in-depth construction work incurs heavy costs and often long-term disruptions to traffic and travel – something both road owners and users want to avoid.
How to avoid extensive repairs
The majority of this complex work can be avoided in the future, but this is dependent on local authorities and governing bodies adopting a more agile paving and maintenance process.
For example, introducing more regular inspections will help to detect when minor maintenance is needed, which can in turn reduce the number of full repaving jobs required; an issue can be fixed simply and quickly before it worsens and becomes a real problem. By conducting regular preventative maintenance, replacing certain sections only or just the very top layer, engineers can avoid the headache and costs associated with entire redesigns at a later stage.
Using faster, more accurate road management systems helps to extend the lifespan of these vital infrastructure assets, improving safety and cost-effectiveness in the process. Regular maintenance does sound expensive – and indeed it is when using traditional methods. However, the key to making considerable savings through preventative maintenance lies in the adoption of modern paving workflows.
Benefits of modern paving workflows
One of the main and most beneficial changes that modern technology has brought to paving is the introduction of 3D scanning. The initial scanning process can be completed at speeds that were simply impossible before. Not only that, but even road closures are avoided as the 3D scanning kit can be attached to a vehicle that joins regular traffic flows, all while capturing pinpoint data that is processed to create an exact representation of reality within a 3D model. Typically, a surveyor would check the levels every 10-15m along the paving track, but this can of course lead to inaccuracies due to the lack of data for the distance in between. However, when using 3D scanning, the guesswork is eliminated, as the scanning process is able to collect infinitely more data, and more accurate data, than a human could in the same timescale.
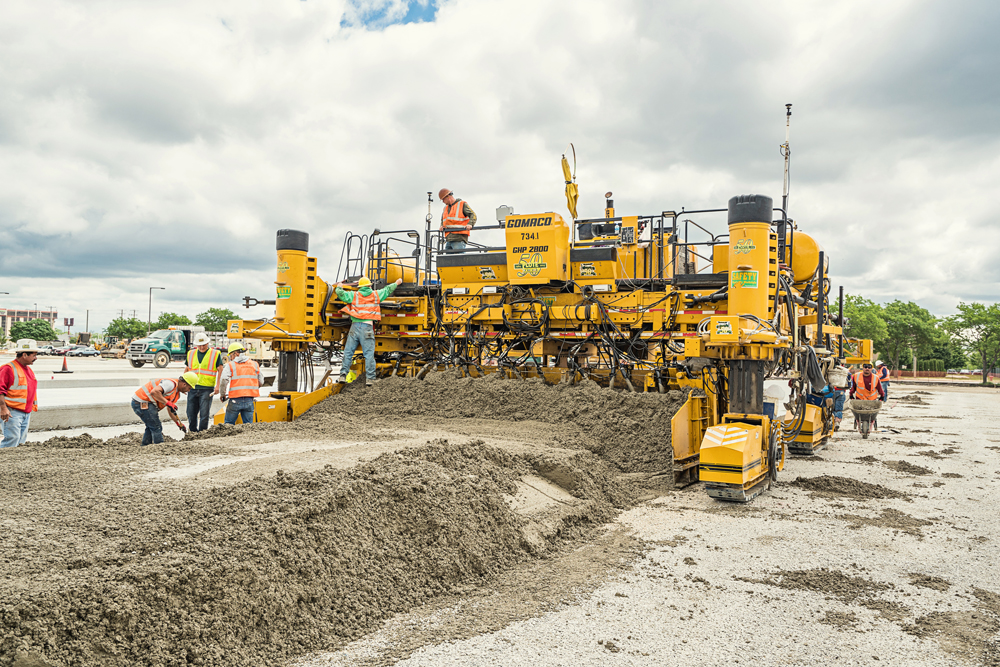
Analysing this data allows contractors to assess exactly which parts of the road need resurfacing and to what particular depth. They can then develop a design that has no wastage at all, be it materials, time or money and leading to a dramatically increased level of efficiency across the entire process. These designs also create much smoother roads, as well as fixing cross-sections, all while controlling quantities and layer thickness.
Intelligent milling and paving
Cost and time-effective technologies aren’t just reserved for the initial scanning and planning processes.
Once the scan is complete and a design has been finalised, the milling units, using machine control technology, can mill much more precisely. This means surfaces that have previously had to be completely redesigned can now just be repaired, as the machines can more accurately mill according to depth and location, and even modify according to different cambers. This same precision can also be implemented across the subsequent paving – again using the machine control technology – the result being a smooth, consistent surface with a vastly improved rideability quality due to an ensured constant layer thickness.
With these new advancements in milling and paving, machines can also automatically respond in real time, accounting for all surface changes. This is achieved by a complete, cohesive integration of design, control and execution.
Paving and mass haul optimisation
However, it is not just the actual resurfacing process that can be automated. When paving is involved in any kind of project, it is vital that there is a constant supply of asphalt, that there is the correct volume of it and, importantly, that this is kept at the correct temperature. Therefore, having oversight of the entire workflow is vital – live data asphalt production, the whereabouts of delivery trucks and estimated arrival times can enable paving crews to speed up, slow down or order more materials accordingly. Most importantly, this also maintains a consistent speed, which is key to avoid an inconsistent thickness. This foresight can revolutionise the way paving crews operate, enhancing efficiency, eliminating material wastage and reducing traffic delays by enabling a decrease in the amount of time a road has to be closed.
It is clear that these improvements to paving workflow deliver commercial, environmental and safety benefits, yet the adoption rate on the whole is slow. The industry has to do more to encourage road owners, local authorities and global governments to learn more about how optimised paving workflows can boost construction outputs.