With a new wave of exhaust emission regulations coming shortly, engine manufacturers are well on track to develop new solutions as Mike Woof reports A wave of technological advances has made the current generation of diesels the cleanest industrial engines ever produced. Driven by tightening controls on emissions, manufacturers have had to develop an array of innovative solutions that will help cut particulate and NOx being emitted from the tailpipe. When the phased reduction in exhaust emissions was first
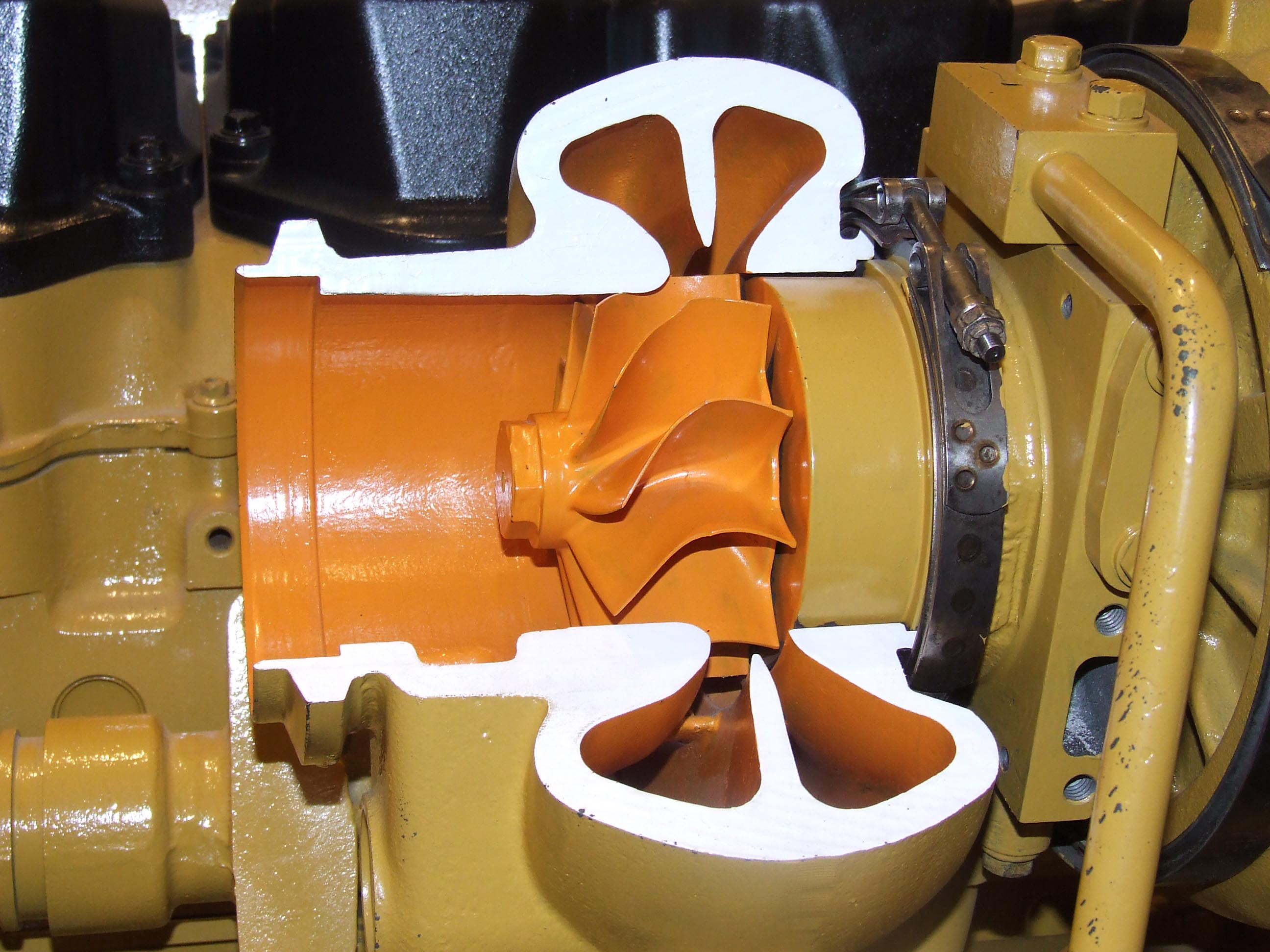
Not all the emissions reductions for engines will be achieved through after-treatment solutions however and further improvements to combustion, fuel injection and turbo-charging will also be made
With a new wave of exhaust emission regulations coming shortly, engine manufacturers are well on track to develop new solutions as Mike Woof reports
A wave of technological advances has made the current generation of diesels the cleanest industrial engines ever produced. Driven by tightening controls on emissions, manufacturers have had to develop an array of innovative solutions that will help cut particulate and NOx being emitted from the tailpipe.When the phased reduction in exhaust emissions was first announced, there was widespread comment from industry that the targets would be almost impossible to achieve. Engineers raised their eyebrows, wondering how the emissions reduction aims would be met. The targets were certainly ambitious. In the time period running from 1999 to 2014, the regulations called for NOx emissions from new diesel engines to be reduced by 95.7% while particulate emissions were to be reduced by 96.5%.
Given the initial scepticism over these targets from industry, it is all the more impressive that the major engine manufacturers are well on track with their respective low emission projects. Huge investment has had to be pumped into this sector, with
This issue of exhaust after-treatment is presenting major engineering challenges to the sector as the units are bulkier and require more space than existing exhaust systems. In recent years operator visibility has become an important issue for equipment firms and sloping engine covers are now widely used to help boost safety. But there has been much debate on where coming machines will find space for the bulky exhaust after-treatment modules without spoiling sightlines.
One interesting business development at present is the tie-up between Fiat Powertrain Technologies (FPT) and
It is worth noting that this tie-up between two engine manufacturers also links two major manufacturers of off-highway machines. Perkins is part of Caterpillar’s engine division while FPT is part of the Fiat group, which also owns
As a major engine supplier, Caterpillar has been planning far ahead. Earlier this year Caterpillar unveiled its C7.1 and C9.3 ACERT equipped engines with power ratings of 130-225kW and 205-328kW respectively fitted with clean emissions modules that would meet the Tier 4 Interim/Stage IIIB emissions regulations. Mike Reinhart is marketing manager at Caterpillar for industrial power systems and he said, “The base engines haven’t changed in physical size.”
This last is a key point as it will reduce the workload for Caterpillar’s own designers when fitting the engines to new machines and also for engineers at other OEMs using these diesels. In addition, tweaks to the fuel injection system and combustion process for example will provide further fuel savings of around 5%.
To help tackle the issue of the large after-treatment units, Caterpillar is offering help to customers installing the engines to provide the best installation solution. This programme has included a series of Tier 4 Integration workshops, which are two and three day collaborative conferences for engineers from Caterpillar and various OEM customers, as well as representatives from Cat’s own dealers and sales teams. Reinhart said, “It has been really beneficial, not just for our customers but for us as we move towards Tier 4 Interim.”
The regenerative capability of the after-treatment package is another important point for long term performance. Caterpillar has developed a clean emissions module that minimises the impact on fuel efficiency during the regeneration process and the design of this unit means that it can be mounted in a number of locations. The unit is said to be highly efficient and Reinhart said, “The operator won’t even know it’s regenerating.”
He added, “It can be remotely installed and it doesn’t need to be right over the engine. We’re minimising the size of the package in installation. It does need some engineering to locate but we believe we have a good customer friendly solution.”
Another major player in the engine market is Deutz, which is tackling the new legislation with its Deutz variable emissions technology (DVERT) system. As with Caterpillar’s ACERT package, the DVERT system is not a single ‘one size fits all’ solution. Instead DVERT offers an array of technologies such as such as; selective catalytic reduction (SCR), diesel particulate filtration (DPF) and exhaust gas recirculation (EGR), which can be selected to suit each customer, the installation requirements and the specific application. Marketing manager Frank Wesolowski explained that the basic engine is a platform and the firm can select options to meet the needs of the application. The architecture of the engine is more or less the same and he said, “As a customer you can choose the modules you need. A big factor is the volume of the installation and Deutz can help with the design of the machine.”
He continued, “Tier 4 is a new ballgame compared with earlier emission regulations. One of our strength is that we can fulfil demands of our smaller customers. We will not only sell the engine but will work with the customer on installations and we don’t want to sell them a whole bucket of technology if they don’t need it. These smaller manufacturers cannot afford to redesign machines for Tier 4 Interim and then Tier 4 Final. There are many manufacturers out there that can’t afford research into emissions reduction.”
Fitting the necessary low emission technology does come at a price though and he added, “The cost of meeting Tier 4 Final is significantly higher.”
Wesolowski said, “We are offering an SCR solution for the next emission stage. We’ve good experience of it on road and it offers low fuel consumption. For Tier 4 Final you need SCR and EGR and DPF.”
Low sulphur fuels play an important role as these are required by low emission engines. Scania revealed that it has carried out extensive tests which have shown that using high sulphur fuels in certain low emission engines can trigger fast wear of injection systems and other components through corrosion. This can result in engines becoming virtually worn out after only a few hundred hours of operation, compared with a normal expected working life of 15,000 hours or so before rebuilds.
Wesolowski said, “It’ll take time to make low sulphur fuel available on-site.” However, he added that by the time the Tier 4 Final regulations come into play, low sulphur fuels will be widely available in Europe and North America. Testing is carried out continuously and the firm is running engines in Germany on fuel that is imported especially from the US to see if these diesels meet the US EPA regulations.
The firm continues to optimise the in-cylinder solutions because not all of the emission reductions will be achieved through after-treatment. Heat rejection is another issue that Deutz is tackling and Wesolowski commented, “Heat rejection is waste energy.”
Looking ahead, the next stage of emission legislation offers a further chance to reduce fuel consumption and this will prove commercially attractive as fuel prices will continue to increase. In addition the CO2 emissions of each engine will become another factor and Wesolowski said, “Everything in the passenger car segment will come into the off-highway market as well, driven by legislators. After Tier 4 legislators will look for CO2 reductions and fuel consumption reductions.”