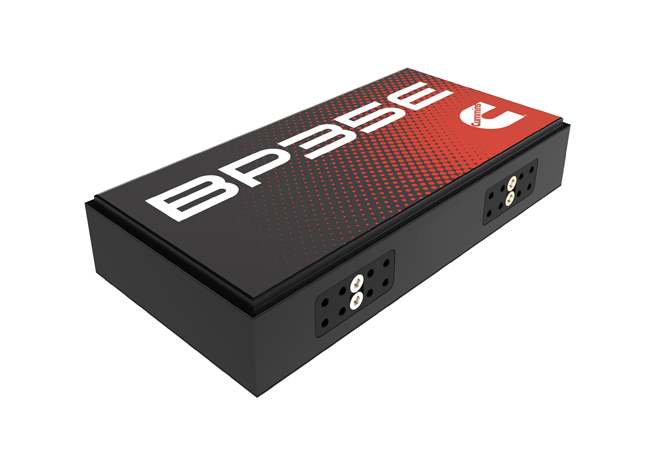
There has been strong pressure against internal combustion engines worldwide, with the scandal over the emissions from diesel powered private cars has strengthening opinion against these engines. Diesel engine firms are taking the long view by offering future power options such as alternative fuels and electric systems. The engine builders are also hard at work ensuring that power units for the industrial engine sector have emissions control equipment that remove pollutants from the tailpipe exhaust effectively, meeting tough legislation.
As clean combustion advocate Peter Kelly Senecal has pointed out, “The internal combustion engine holds a firm place in future transportation needs as well as in various industrial sectors. Specifically, for off-road applications.”
In Europe and the US, the emissions standards for off-road mobile machinery have become more and more stringent as Senecal has highlighted. And Senecal has also said that the reliability and durability of diesel engines and ever-improving emissions control systems mean that these units will continue to dominate in the off-highway market for many years to come.
The six-cylinder, 9.3litre engine has benefited from more than 200 million hours of testing by the firm on its range of diesels in real-world, off-highway applications. A key feature is its new high- pressure common rail fuel system and simplified air, electrical and aftertreatment technology. This means the C9.3B can produce up to 340kW and 2,088Nm of torque, delivering 18% more power and 21% more torque than its predecessor, while weighing 12% less.
Patented aftertreatment technology provides a compact, lightweight design, which is 39% smaller and 55% lighter than the Tier 4 Final product. Offered in a range of different configurations, the C9.3B industrial engine is available with engine-mounted aftertreatment and installed radiators from the factory.
The firm says that the C9.3B engine has undergone thorough testing to ensure it can meet the industry’s newest and most stringent standards. It offers increased power and torque, combined with a simpler, lighter package, and the firm says that users will benefit from better performance as well as a 3% reduction in fuel consumption. The engine also offers improved starting in cold climates.
In addition to the C9.3B, Caterpillar’s EU Stage V line-up also includes the 12.5litre C13B, incorporating technology similar to that of the C9.3B and with power ratings to 430kW.
Caterpillar also is certifying its existing C13, C15, and C18 Stage IV/Tier 4 Final engines to meet EU Stage V emissions standards. Stage V certification for these engines will be achieved with no changes to customer interface points and with only minimal changes to the DPF. In addition, dual-label certification - Stage V/EPA Tier 4 Final (and Japan 2014/Korea Tier 4 Final) - will be offered for the C9.3B and all other Cat products in the 250-597kW power range.
The two prototypes undergoing tests on the MTU test stand in Friedrichshafen feature an innovative new system. MTU has acquired the rights to this new technology from the G+L innotec company, and the partners will now be jointly developing the product. Market debut for the first engines with electrically assisted turbocharging is scheduled for 2021.
“Electrically assisted turbocharging is a significant milestone on the road to hybridisation,” explained Dr Johannes Kech, director, Turbocharging and Fluid Systems at MTU. “This technology will allow us to develop engines that deliver increased agility and lower consumption at the same time as enhancing ecological performance,” he added. All this is made possible by using an electric motor to smooth out weaknesses in turbocharging systems.
Linked to a conventional turbocharger, the electric motor ensures that boost is available when the engine needs it. This will eliminate delays in performance ramp-up according to MTU. In addition, MTU says that the system will help address another issue, as turbochargers are expected to achieve reductions in emissions by helping to prevent the generation of diesel particulates and nitrogen oxides during the combustion process.
“With electrically assisted turbocharging we marry a conventional MTU turbocharger with an electric drive motor,” explained Joachim Thiesemann, who is responsible at MTU for integrating the new system in the standard turbocharger landscape. Special units mounted in front of the compressor wheel house permanent magnets, the rotor of the electrical unit, and the electrical winding that is integrated in the compressor casing. “The electric motor makes it possible to virtually decouple the operating point of the turbocharger from the speed of the diesel engine,” explained Rudi Rappsilber, who is in charge of testing the new system at MTU. The firm says that delays in performance ramp-up can be addressed, allowing optimum turbocharging to be achieved in almost every operating state. The technology can be implemented with existing turbochargers without excessive complications, while the additional installation space required is limited according to MTU.
Electric avenue
For the electric power market,
Andrew Penca, general manager, Battery Systems at Cummins. “Cummins is committed to investing $500 million in electrification over three years. These investments include innovation of fully electric and hybrid power solutions that will serve our markets as they adopt electrification.”
The BP74E (74kWh battery pack), BP35E (35kWh battery pack), BM44E (44kWh battery module) and BM20E (20kWh battery module) are Cummins-designed and built units featuring Li-ion technology. The firm says the units offer a high energy density and proprietary control technology, allowing a high battery performance for a longer zero emission range. They benefit from a modular design and can be scaled and aligned with the capability and duty cycle of the application. The range includes low voltage packs (BM44E and BM20E) that power material handling applications to high voltage energy dense battery systems (BP35E and BP74E) that have the energy needed for long range buses and trucks.
Meanwhile,
The E-DEUTZ strategy combines its low-emission engines with electric drives and follows the firm’s 2017 acquisition of Torqeedo, a market leader and system solution specialist for integrated electric and hybrid drives for boats. The technology is now being developed for Deutz’s off-highway engine business, which is why it has developed the modular, scalable hybrid drive. Featuring the TCD 2.9 diesel engine and an electric motor, the combined system delivers 110kW. Its lithium-ion battery has a capacity of 40kWh at 400V.
And
This follows the success of hybrid and all-electric technology introduced by the
“We will take a full systems supplier approach, helping our customers in the transition to the new technology. This will happen application-by-application, on the basis that the business case for switching to electric will differ across our many customer segments.
However, he also added, “This is the start of a long-term transition. Diesel and gasoline-powered primary drive systems will remain the most appropriate power source for many applications for years to come.”
The firm has already developed prototype systems in-house. “Volvo Penta is already several years into its electrification journey,” said Johan Inden, chief technology officer.
“We have spent this time building competencies, experience and establishing the technologies required to deliver a sustainable power solutions road map. The advanced engineering projects we are currently running, and the performance data received gives us confidence that we are on the right technology path to offer customers a compelling business case for electrification.”
As part of this increased commitment, Volvo Penta has restructured its organisation to accelerate the switch towards electrified power and has committed to an ambitious ramping-up of its electrification investment program. An electromobility development-and-test laboratory has also been established at its Swedish headquarters.
While the power outputs and applications of the initial electric systems are being kept confidential for the time being, the company has announced that both hybrid and all-electric solutions will be offered at the outset. Volvo Penta is already field testing early prototypes and system validation is under way.
Petrol alternative
Kohler says that its compact, single cylinder Command PRO EFI ECH440 benefits from closed-loop electronic fuel injection technology (EFI). The 10.4kW petrol engine is said to offer better fuel efficiency, reliability, and easier starting in harsh conditions. It is suited to use in compact power solutions. The Command PRO EFI ECH440 controls and manages the exhaust through the closed-loop system, extending the life of the engines. The starter is one of the key features of this model: the Command PRO EFI ECH440 starts like a car, with no choking. The closed-loop electronic fuel injection system is also said to be highly fuel-efficient. In addition, the EFI diagnostic software provides quick and easy troubleshooting to minimise downtime.