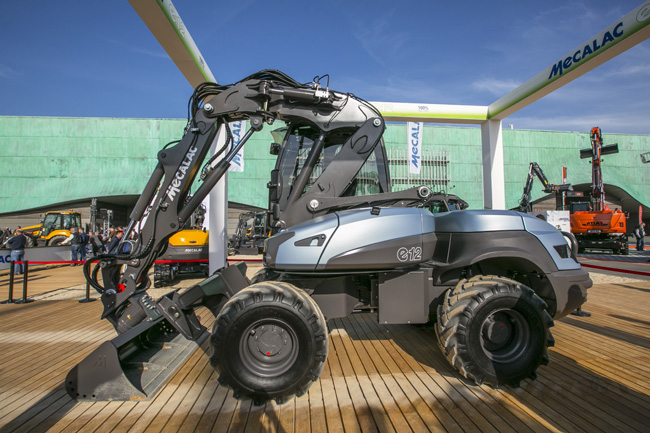
Major innovations in machine systems are being seen in the construction equipment sector. Several manufacturers are hedging their bets with regard to drive technology and introducing electric drive machines, which will suit use in urban ultra-low emission zones.
Meanwhile
Based on the proven Mecalac 12MTX model, this version is the world’s first all-electric compact wheeled excavator. The machine features Spicer 112 axles and a Spicer 367 shift-on-fly transmission. According to Mecalac, its e12 wheeled excavator delivers the range, performance, and compact size for use on urban construction sites and is designed to meet demand for equipment able to operate in low emission zones.
“As the European construction market embraces the trend toward zero-emission standards for small to mid-sized vehicles, our customers are demanding great strides in efficiency while also requiring reliable performance,” said Jean-Baptiste Rousseau, technologies manager at Mecalac. “Dana was able to adapt the 12MTX drivetrain to add electric drive capabilities within our existing vehicle architecture. With their technical expertise and open collaboration, we developed an optimal solution and accelerated the delivery of this vehicle to market.”
Dana has experience developing drivetrain systems for hybrid and electric vehicles. The company also offers patented battery and electronic cooling technologies, along with fuel-cell technology. In addition, Dana engineers had extensive experience with this particular application because the diesel-powered version of this vehicle also features Spicer drivetrain components.
“As a Tier-One supplier, we understand that the success of electrification in the off-highway industry is driven by performance. These technologies must support a smooth transition to fully integrated electric-drive technologies optimised within a single package, providing both electrified and conventional powertrain options,” said Aziz Aghili, president of Dana Off-Highway Drive and Motion Technologies. “Dana’s support for new energy vehicles has been considerable, and growing every year, as the importance of engineering for hybridisation and electrification is further elevated throughout the industry.”
The system has been fitted to a prototype backhoe loader from Huddig. This machine features a 104kW
Bonfiglioli claims that the system helps to increase driving precision and energy efficiency. The machine is equipped with four special traction drives, each driven by a 30kW electric motor and delivering a maximum output torque of 40,000Nm. The new 610X wheel drive from Bonfiglioli has been developed for heavy-duty machines requiring high torque. For the Huddig articulated backhoe loader, each wheel can be controlled, independently, controlled, providing better control on slippery surfaces. In addition, the machine can manoeuvre easily in confined worksites, while generating minimal noise.