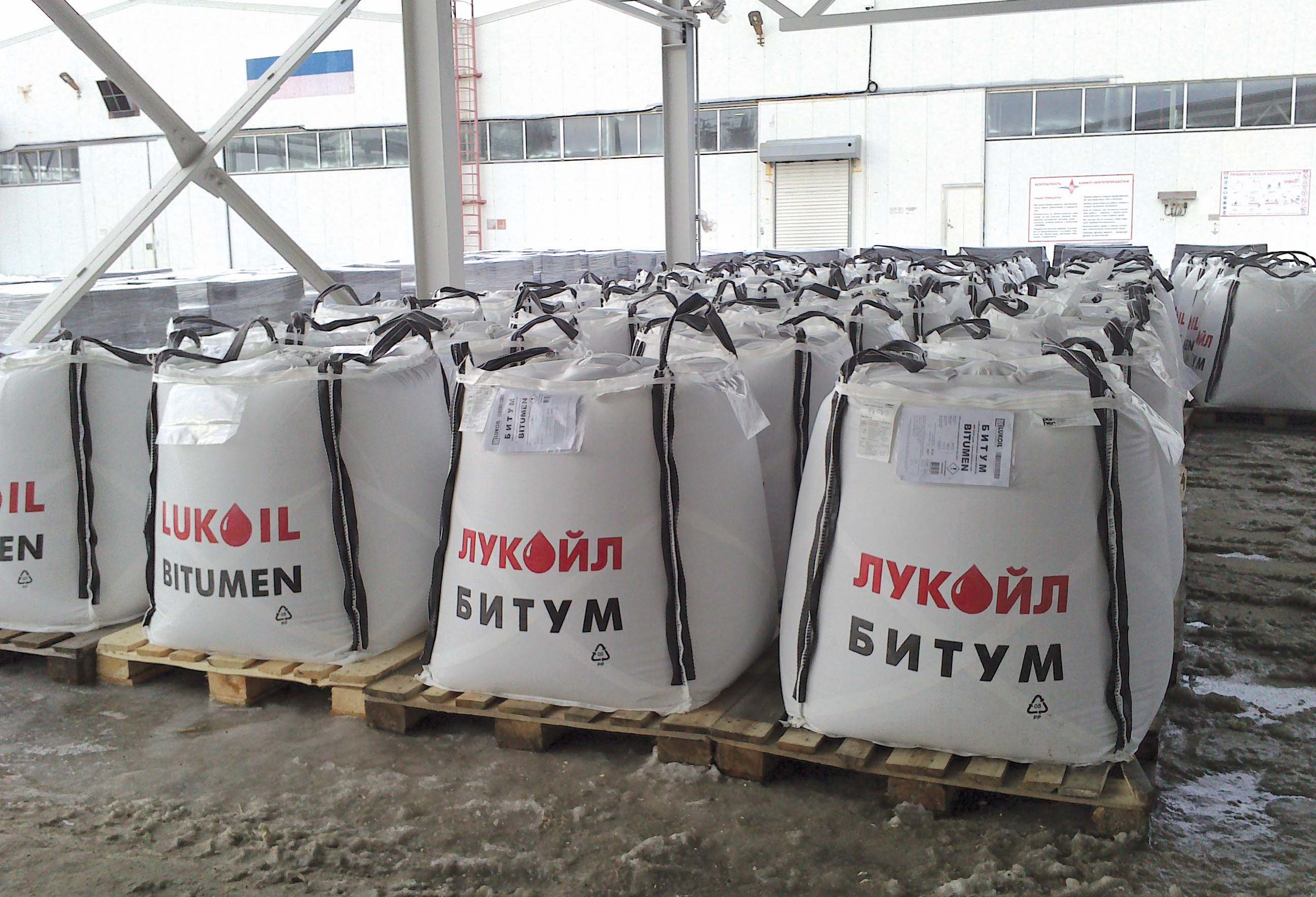
Attendees at the
One of the outcomes of these changes is that bitumen is travelling further, a trend which is likely to increase in the future. And that means new ways of transporting it over long distances are emerging.
“There is going to be a change in the marketing, logistics and consumption of bitumen,”
Pörner has invested several years in developing bitumen bags, together with an associated cooling and packing system, which can hold 1tonne of bitumen. The bags can be transported using standard trucks and ships, and stored indefinitely before being melted, whereas liquid bitumen has to be heated during transportation and can travel limited distances.
Pörner has already supplied its bagging system to refineries in Iran, Bosnia, Bahrain, and Russia. The Lukoil facility in Russia (see the story below) is the most recent one and began operation in December 2013.
Russian oil giant Gazprom has a different solution for the same challenge. It uses wooden crates to store and transport blocks of its polymer modified bitumen.
The picture to emerge from the Argus conference is one of two, contrasting situations in Europe. Christophe Nikodeme, director general of the
Speaking of France’s situation, Eric Gosse,
Colas’ Etienne Le Bouteiller, executive director of the International Bitumen Emulsion Federation called for more sophisticated technologies for road repairs and maintenance. “High-tech solutions need high quality materials, specifically bitumen,” he told the conference.
Some Eastern European countries have ambitious road-building plans, according to Michal Sobanski, head of export at Lotos Asfalt, but funding has been a problem. However, he predicted a rising market for bitumen in Poland between now and 2020 with PLN 60 billion (€14.5 billion) earmarked by the government for new roads.
The most positive outlook came from Tayfun Ozatalay, general manager of Energy Pro Investment Petrol who spoke about the market in Turkey. With 23,000km of roads now, Turkey has plans to grow that by 61% to 37,000km by 2023 according to Ozatalay.
Given the decline in demand in much of Europe, it is perhaps not surprising to learn that since 2010, 12 European refineries have shut down: four in France, four in Italy, three in the UK and one in Romania. Lloyd Thomas, vice president, Argus Consulting Services told the conference that more closures seemed inevitable; he identified seven further refineries which are under threat of closure or have only been operating for part of the year.
Though the global financial crisis and Europe’s slashed road building and maintenance budgets have not helped,
Thomas pointed to the US as a major factor in the European refineries’ demise. The huge rise in production of shale oil and the US ban on exports of crude oil, mean that the US must refine its oil at home and export the products.
There is a further threat looming for Europe’s refineries, according to Peter Ross,
The refinery closures do not mean we are facing a shortage of bitumen, however, because demand as well as supply has fallen. “There’s less bitumen production coming from fewer refineries but supply is still adequate,” Nasreen Tasker, vice president of asphalt at Argus Media, told the conference. Europe’s share of that demand is decreasing, from 23% in 2005 to 17% in 2012, according to Argus.
It remains a tough market for everyone involved in bitumen at the moment, according to Tasker. Refineries must prove the business case for producing bitumen, as new technologies mean that other products can now be produced from the residue which becomes bitumen; resellers are struggling to make decent margins; and contractors are being forced to cope with fluctuating prices.
Tasker highlighted big price differentials globally in recent years, making it viable for resellers to go further afield to source their bitumen. Differences in price, which Argus tracks in its reports, can be over $100/tonne, with the lowest global price spots moving from month to month.
Another big change is contractors buying direct from suppliers. “Now there are more contractors coming to the market, building their own storage and bypassing the resellers,” said Tasker. This is definitely a market that Pörner is planning to serve with its bitumen bags. “Our final aim is to supply road construction companies,” said Traxler. This is already starting to happen: one bitumen bag customer is a small Nigerian contractor who uses them to make asphalt mixes for himself and his customers.
Argus Media holds four international bitumen conferences a year. Next is the Argus Asia-Pacific and Middle East bitumen conference at the Pan Pacific Hotel, Singapore, 24-26 September 2014.
Bitumen in bags
The latest of Pörner’s bitumen cooling and packing units to be installed at
Pörner supplied the packing plant in pre-fabricated modules and advised Lukoil on how to integrate it with the neighbouring bitumen production plant. Bitumen travels through pipes to the filling stations where the bags are automatically filled and the exact quantity, around 1m3 of bitumen, recorded.