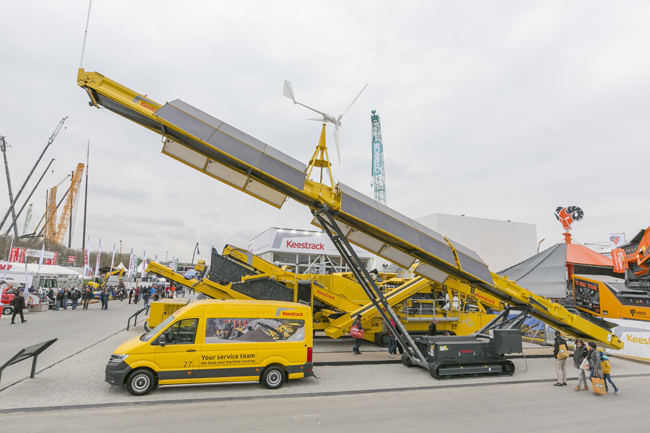
The latest crushing and screening machines offer major benefits for aggregates production. Greater efficiency is claimed, along with reduced environmental impact and optimised material quality.
The compact Cobra 290R closed-circuit impact crusher is versatile and can operate in demanding applications. The track and crush feature is standard, so the operator can move the machine using the optional remote control from an excavator cab without shutting down the crusher. Ground level access to the engine, hydraulics, service and refuelling points ensure serviceability. The rapid set-up from ground level allows the machine to be crushing in minutes.
The Cobra 290R uses a 235kW engine to power the fuel-efficient and high-performing direct drive system which gives potential throughput of up to 290tonnes/hour. The fully enclosed vibrating feeder incorporates an integrated pre-screen which can be configured to suit multiple applications by selecting from a range of interchangeable media. The chamber also features a hinged inlet lid which reduces the risk of material bridging at the feed point.
From
The four-bearing design is said to minimise structural vibration and maintain constant g-force even through fluctuating material feed rates.
Haver & Boecker Niagara’s N-Class offers one to three screen decks and features an advanced single-eccentric shaft design supported by four double-spherical roller bearings. It is balanced to minimise dynamic loads transferred into the structure and allows multiple screens to be placed side by side in the same building.
The N-Class optimises screening efficiency and is said to eliminate blinding and pegging by providing a consistent g-force in all operational modes, regardless of load consistency. A heavy-duty body design handles heavy loads in applications with extreme material sizes up to 2032 x 1016 x 1016mm.
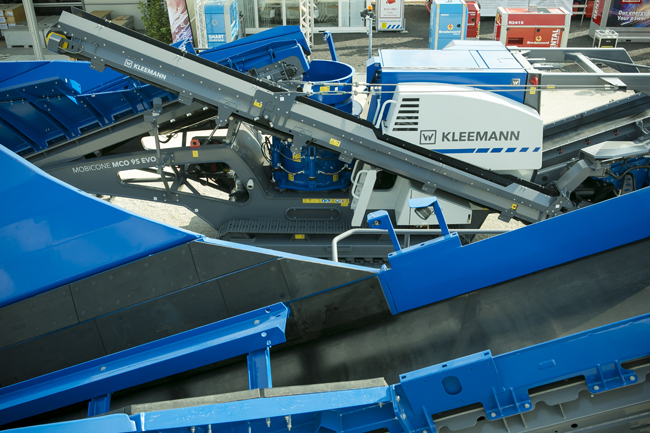
Keestrack says that its sophisticated track-mounted S5e Solar Stacker features photovoltaic panels over the conveyor belt. These provide a maximum 9kW and feed the 23kW system battery installed on the chassis. The conveyor belt (22kW) and the tracks (2 x 15kW) are directly electric-driven. Meanwhile, an electric pump unit (2 x 15kW) supplies the hydraulic lifting cylinders. The system can also be powered or recharged via available external sources, such as upstream diesel-electric crushers and screens, or via mains plug-in.
Keestrack claims its e-technology models can reduce energy costs by up to 80% compared to traditional diesel-hydraulic models. Noise levels can also be reduced during plug-in operation by around 30%, according to the firm. The manufacturer says there is a 10-15 % higher initial investment for ‘e-technology’ stackers and screeners and 15-20% for large mobile crushers. However, the company says that this additional investment quickly pays for itself.
Kleemann has launched several mobile crushing and screening units. With an output of up to 650tonnes/hour, the MOBICAT MC 120 Z PRO suits natural stone applications. The mobile machine has a feed opening of 1200mm x 800mm and an extra-long articulated crusher jaw. To optimise material flow, the Continuous Feed System (CFS) adjusts the conveying speed to the fill level. And the 470tonne/hour capacity MCO 11 PRO, is said to offer efficient secondary crushing when combined with the MC 120 Z PRO.
To lower noise and dust emissions, Kleemann now offers its new ECO Noise and ECO Dust features on the 450tonne/hour MOBIREX MR 130 Z EVO2 mobile impact crusher. This same plant features Kleemann’s SPECTIVE crusher control system, with a touch panel featuring clear symbols to identify functions, helping to simplify operation.
Maskin Mekano says its highly mobile ECO3 diesel-electric powered compact screening plant can be set up and fully operational in just four minutes. The Swedish family-run company is showcasing the up to 200tonnes/hour capacity plant this week.
Equipped with Maskin Mekano’s proven STE 2-26 screen, the ECO3 has a hook lift frame said to ensure the lowest possible moving cost. The robust vibration feeder means it can be used for all types of material sorting. The compact mobile screener’s diesel-electric operation ensures low diesel consumption and CO2 emissions. The ECO3 is also said to offer the lowest noise levels in its class, adding to its urban application suitability. For stockpiling, the screening plant is fitted with three hydraulically folded onboard conveyors. All drive drums are rubberised for safe operation even in less favourable weather conditions.
Metso has a new Urban LT96 aggregates processing plant. Offering advanced protection features, the Lokotrack Urban model range lowers noise and dust emissions. The Metso Urban solution was developed to enable crushing operations in highly regulated urban areas, while actively protecting employees on-site.
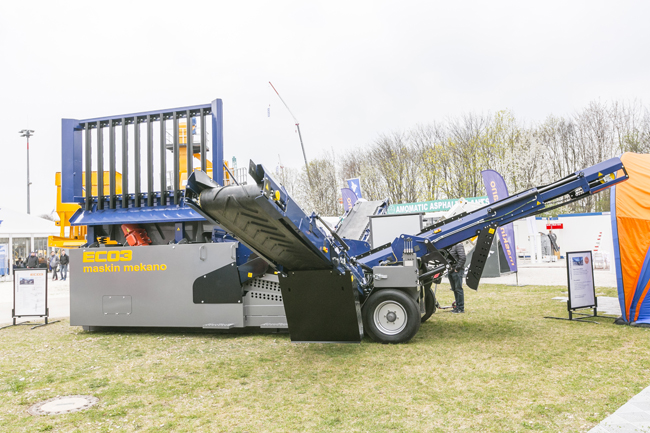
The Metso Urban solution combines the firm’s proven crushing technology with modern environmental and safety features. The latest addition to the series, the Urban LT96 suits small to mid-sized contractors crushing and recycling materials on-site. The Urban solution is also available for the electrically-driven LT130E model, LT120 and the LT106/S.
With the Urban plant technology, noise protection distances can typically be reduced by 50-60% compared to traditional crushing plants operating in hard rock applications.
RUBBLE MASTER is bringing innovation to its RM GO! range of compact mobile materials processing plants. The firm’s crushers and screens can be coordinated using a central control unit, optimising overall performance and making them safer. The RM GO! NEXT models also have fully integrated hybrid drives and advanced digital features.
RM and Maximus have jointly developed the RM MSC8500e, a fully-electrified hybrid screen. Modelled on the proven RM MSC8500M, this features electric drives instead of hydraulic drives, except for the crawler gear. The MSC8500e hybrid screen is said to be a powerful and robust hybrid machine and can be powered through the new RM 120GO! hybrid crusher. The crusher’s generator supplies power, without the need for an additional diesel, reducing exhaust emissions and noise. This offers versatility as the hybrid screen can also be driven by a diesel or other external power sources. When the crusher’s discharge belts start, the screen also starts automatically. If blockages or faults occur, the screen also stops automatically. For the RM MSC8500e, a radio remote control system is also available, further boosting safety.
SBM Mineral Processing is introducing the Remax 200 mobile impact crusher, its smallest ever unit. Featuring a new user interface, it is targeted at the rental market in the road construction sector and can crush up to 250tonnes/hour. A key feature is said to be the easy user interface and the machine has been developed to meet growing demand for smaller machines on the rental market. The firm claims that the machine can be fine-tuned for specific applications by experienced operators. Meanwhile, it also offers a more basic preset for less experienced operators.
Powerscreen and
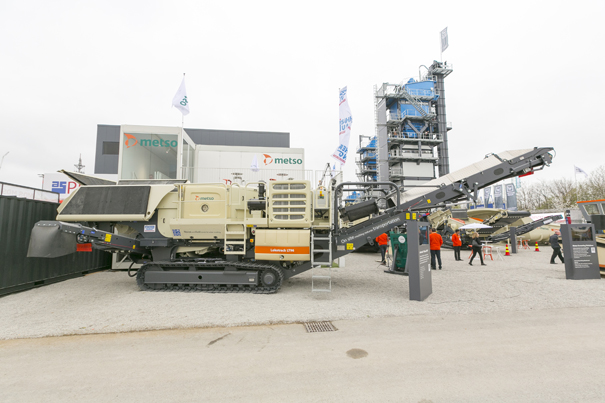
Fitted inside the cab of a material feed excavator, the system provides centralised remote access to multiple machine control systems within a crushing and screening train. It has been designed for improved control and ease of operation, offering information and views of the entire machine train.
The system allows the excavator operator to view information from each machine that is connected to the system; make informed decisions about each machine’s operation; and remotely manage the entire machine train. This helps maintain high efficiency and produce the required material specification.
The operator can adjust individual machine metrics or use global features, such as pausing the material flow across the train with one action, all from the excavator cab.
Additional features include alerts that indicate when someone on the ground is making process adjustments and a camera view of up to two cameras/machine, from vantage points such as material transition points, chamber inlets, and material choke level on cones.
The system offers an option for other personnel on the jobsite (such as the wheeled loader operator) to have read-only system access, boosting efficiency by offering a remote view of the operation and the ability to interact.
According to the company, this system provides a level of central control, better safety, connectivity and multiple-user support for the jobsite.