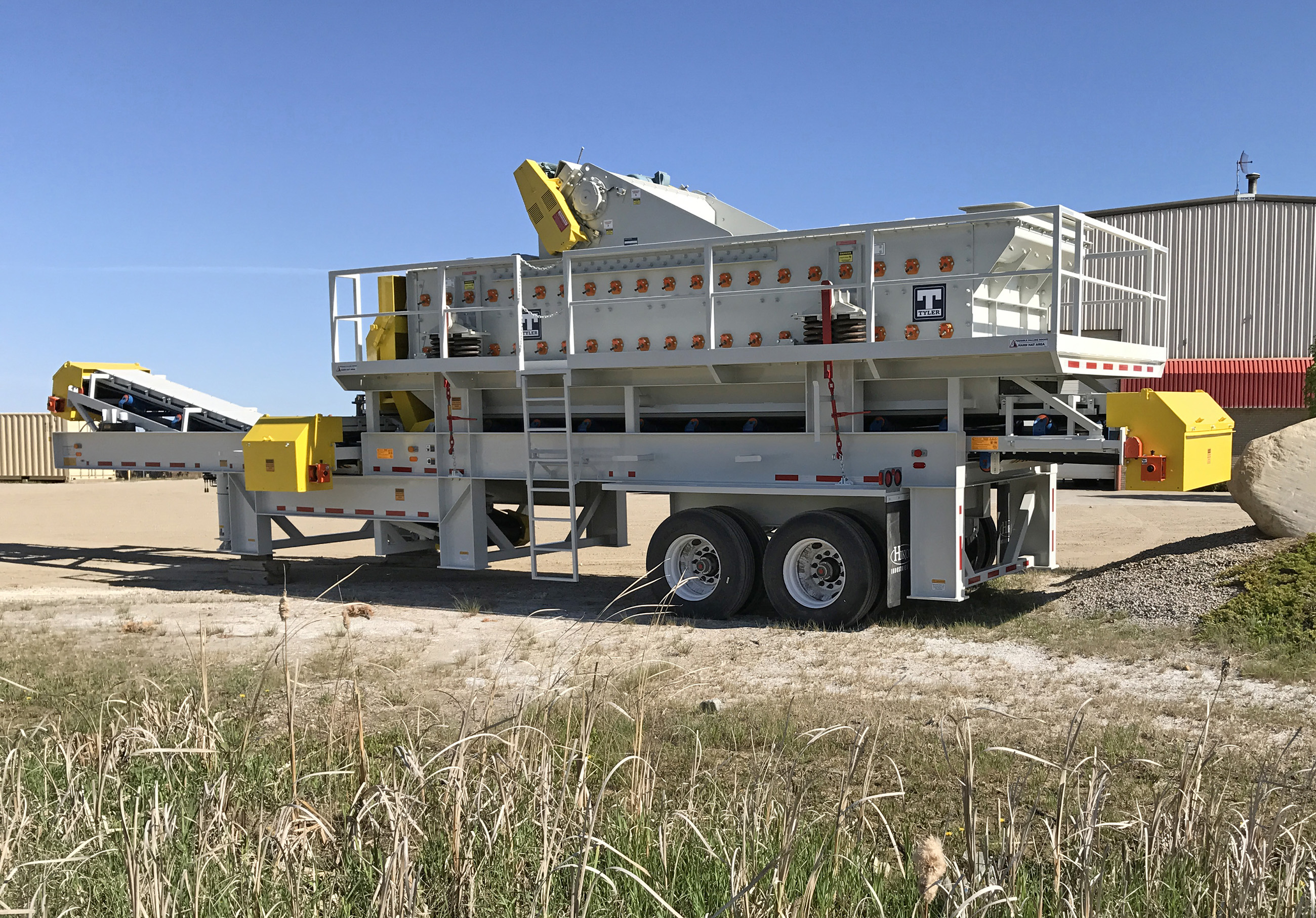
New developments are coming for the aggregate production sector, with a host of new technologies for the crushing and screening segment. These new machines are said to be more versatile, more productive, more efficient and offer a lower cost/tonne than any equipment available previously.
CDE claims that its new AggMax 163-SR scrubbing and attrition system features an efficient new RotoMax logwasher. The unit is designed to meet the demand for a plant that bridges the gap between the popular AggMax 80 and 250 models. According to the firm, the new RotoMax 163-SR is built to the same standard as the RX250, with a geometry refined for efficient scrubbing action at mid-range tonnages. The machine has a new Infinity D1-63 prescreen incorporated into the design, optimising sand removal prior to attrition process, while its new Infinity D1-43 screen dewaters organic and lightweight wastes liberated from the attrition process. The new Infinity H2-60 sizing screen separates material into three washed aggregates and allows the removal of sand liberated by the RotoMax’s attrition process. It is said to offer efficient screening, while allowing good access for maintenance between the decks.
The AggMax 163-SR features a modular design to allow upgrades, while also having modular GRP walkways, good access to the pump for easy maintenance and a new tensioning mechanism for quick and efficient pump set up.
Also new from CDE is its novel connected plant technology. This is said to allow pre-emptive maintenance and support, operational efficiencies and simplicity for plant customers, through a console hub.
From
Customers can select the 1.82m-wide machine in two lengths of 4.9m and 6.1m. Primarily mounted horizontally, the L-Class can also be inclined or declined as much as 3°. The linear L-Class handles up to 360tonnes/hour and features a 45° mounted double-shaft overhead drive system with direct-mounted motors. Producers can access multiple speed and stroke options by changing the pulleys and plate weights. The application-specific body design offers simplified maintenance with a one-piece removable head and shaft assembly. In addition, unlike most linear-stroke machines, the L-Class does not require timing belts or gears.
The L-Class also suits separating water from product in dewatering applications. When positioned at a negative incline of about 3°, the vibrating screen’s g-force moves wet material uphill on the screen. Gravity and the natural operation of the equipment help screen out water before the material reaches the discharge end. The thick layer of material on the screen also acts as a filter cake and presses water out, as well as traps fine particles that would be lost in a thin layer screening process.
For operations requiring a level of portability, Haver & Boecker engineers pair the L-Class with the Hydro-Clean 1000 Wash Plant on a skid structure. This combination allows a customer to purchase the three components together, instead of designing and building a skid structure for a wash plant.
The innovative Belgian crushing and screening equipment manufacturer
The mobile impact crusher suits a broad range of applications, from short-term construction site operations to flexible semi-stationary production in medium-sized recycling and production companies.
The R3e and redesigned R3, which offers the same 20% productivity gains as the R3e, are said to offer fast loading and short set-up times on site. They also feature a high level of mobility thanks to a support-less frame construction and rugged undercarriage track frame. Extensive coverings and wide-opening doors and flaps offer easy accessibility to all operational components and satisfy the requirements for operational reliability and maintainability.
They are powered by a 235kW Tier 4 Final
The R3e and redesigned R3’s new optional single-deck afterscreening unit offers almost 4.4m², corresponding to around 30% more screening area than the previous model, optimising machine performance for producing high-grade final grains.
The MC 120 Z PRO is equipped with Kleemann’s SPECTIVE control system, currently available for PRO series crushing plants and the latest impact crusher in the MOBIREX MR EVO2 series. It uses clear symbols that make all plant functions identifiable at a glance. The touch- screen only displays information that is relevant to machine operation. The operator is guided through the control system in a similar manner to a smartphone, which considerably reduces the number of operating errors. In addition, data on machine operation can be called up in the plant cockpit.
Also being introduced are Kleemann’s mobile impact crusher MOBIREX MR 110 Z EVO2 and the mobile classifying screen MOBISCREEN MS 952 EVO, both said to be highly efficient, productive and easy to use machines that are ideal for quarrying and recycling applications.
McCloskey International is launching a new compact jaw crusher, the J35, as well as its AGG STORM 150 from
The J35 compact jaw crusher is said to be a versatile and mobile crusher, which can continue to track while crushing. The J35’s small footprint is suited to demolition and asphalt recycling, aggregates and smaller scale construction projects. Less than 2.5m wide, the crushers can be transported easily from site to site.
Meanwhile, the McCloskey AGGSTORM range is said to be robust and reliable equipment in challenging applications. This modular plant can be used to remove harsh, clay-bound material from natural and crushed gravel, stone and ore feeds that cannot be removed by rinsing or screening alone. The log shafts rotate in opposite directions and are timed to obtain an overlap of the paddle shoes for maximum scrubbing action.
From
The heart of the 883+ triple shaft is the new triple shaft screenbox, featuring two large screening decks. The screenbox’s triple-shaft design employs an oval motion stroke to generate an aggressive screening action, reducing plugging and blinding over the screen decks to provide a quality product with high tonnage output.
Terex Finlay says that even when under heavy load during its testing phase, the new triple shaft screenbox produces high tonnages across a range of difficult and challenging applications. Some of the in-built features of Terex Finlay’s current 883+ screener have been retained, including the ability to hydraulically raise the discharge end 500mm to facilitate easy and efficient media changing.
The new plant now has a wider fines conveyor, which benefits from increased hydraulic power. The plant also has an engine that runs at lower speed, reducing wear and tear and fuel consumption.