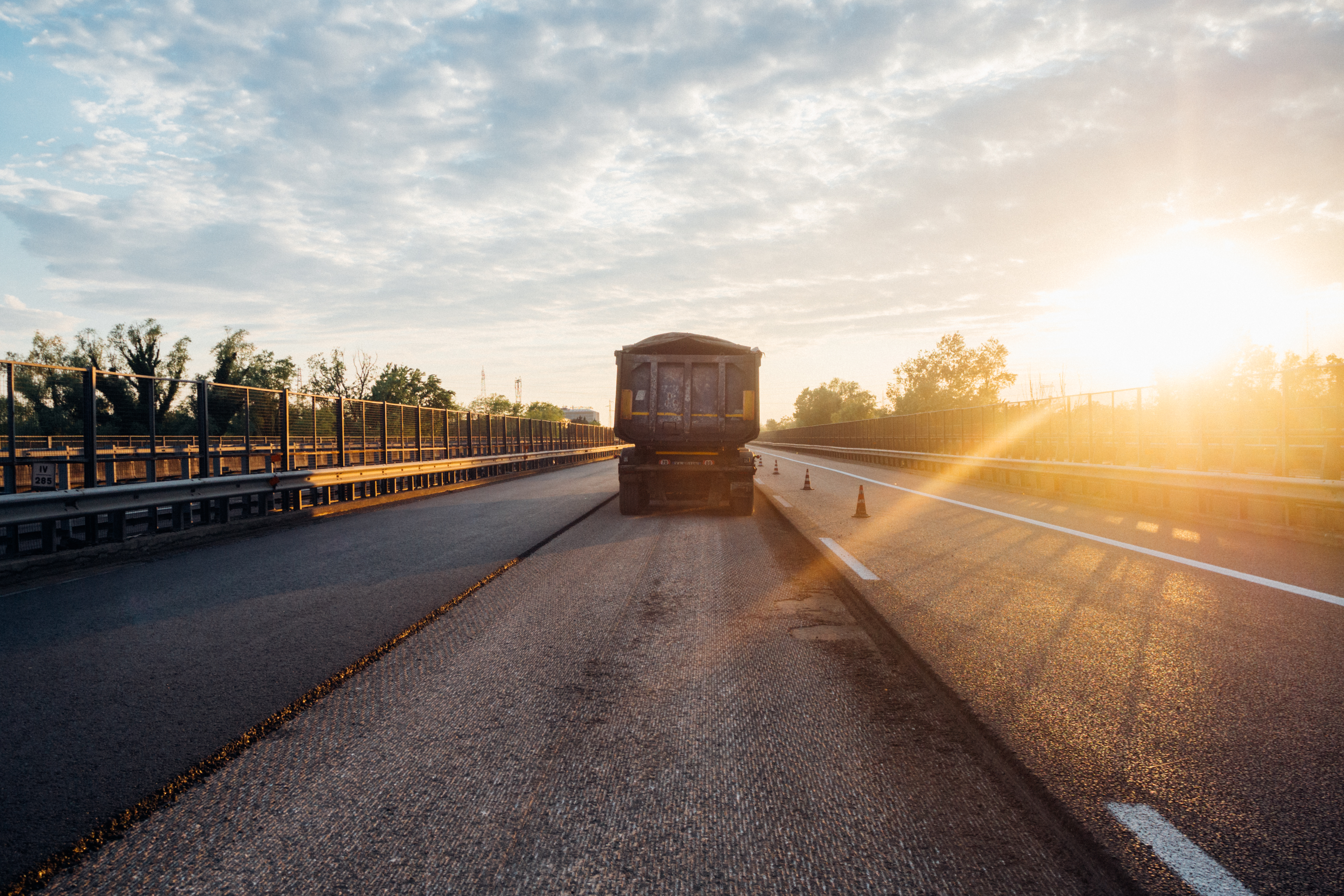
Graphene-enhanced Gipave additive, developed by Italian specialist Iterchimica, has been used in the binder layers of Italy’s A4 motorway in a rehabilitation intervention designed to last for 28-years. The goal is to lower maintenance costs and carbon emissions as well as conserve resources.
Motorway operator Autostrada Brescia-VeronaVicenza-Padova is responsible for the A4 motorway which runs between Brescia and Padova in Italy. This is a route carrying very heavy traffic - an average of 95,000 vehicles daily, of which 25% are heavy goods vehicles. On a 5.5km-long section of the eastbound motorway towards Padova, the operator is trialling an approach that aims to deliver a higher performance highway, with different materials and interventions used on the different lanes.
For the slow lane, the contractor milled and removed the entire depth of asphalt, stabilised the ground beneath to a depth of 300mm and then laid a 120mm modified bitumen base, a 70mm-thick binder layer modified with Gipave and a 50mm layer of soundabsorbing porous asphalt.
For the middle lane, only the asphalt layers were replaced and for the third one, only the surfacing layer. Gipave technology was selected due to its superior performance compared to mixes made with standard polymer modified bitumens.
Gipave combines graphene with polymers extracted from carefully selected waste hard plastics, which would not normally be recycled. Iterchimica developed Gipave in a six-year research and development programme, working with graphene supplier Directa Plus, G.Eco and the University of Milan Bicocca. The first trial section was laid in Italy in 2018 and further trial sections laid in the UK and Brazil.
To plan repairs and other interventions on the motorway, Autostrada Brescia-VeronaVicenza-Padova uses a pavement management system into which survey information and other data can be fed. The software then uses algorithms and models to forecast what interventions will be needed when. The main parameters that are monitored and entered into the system are the Sideways Force Coefficient, Roughness Index of Roads, Wearing Course Permeability, layer thickness using a GPR georadar and deflection analysis.
For the rehabilitation project, a software design package was used to determine the layer thicknesses needed. Using inputs including traffic volumes, climate and the properties of various materials, the pavement design was produced to give a design life of 28 years with a reliability index of 99%.
Should the life expectancy of the reconstructed pavement be as designed, the operator has calculated that the savings due to reduced maintenance will result in 42% fewer carbon emissions per km, 33% less bitumen and 34% less energy consumption.