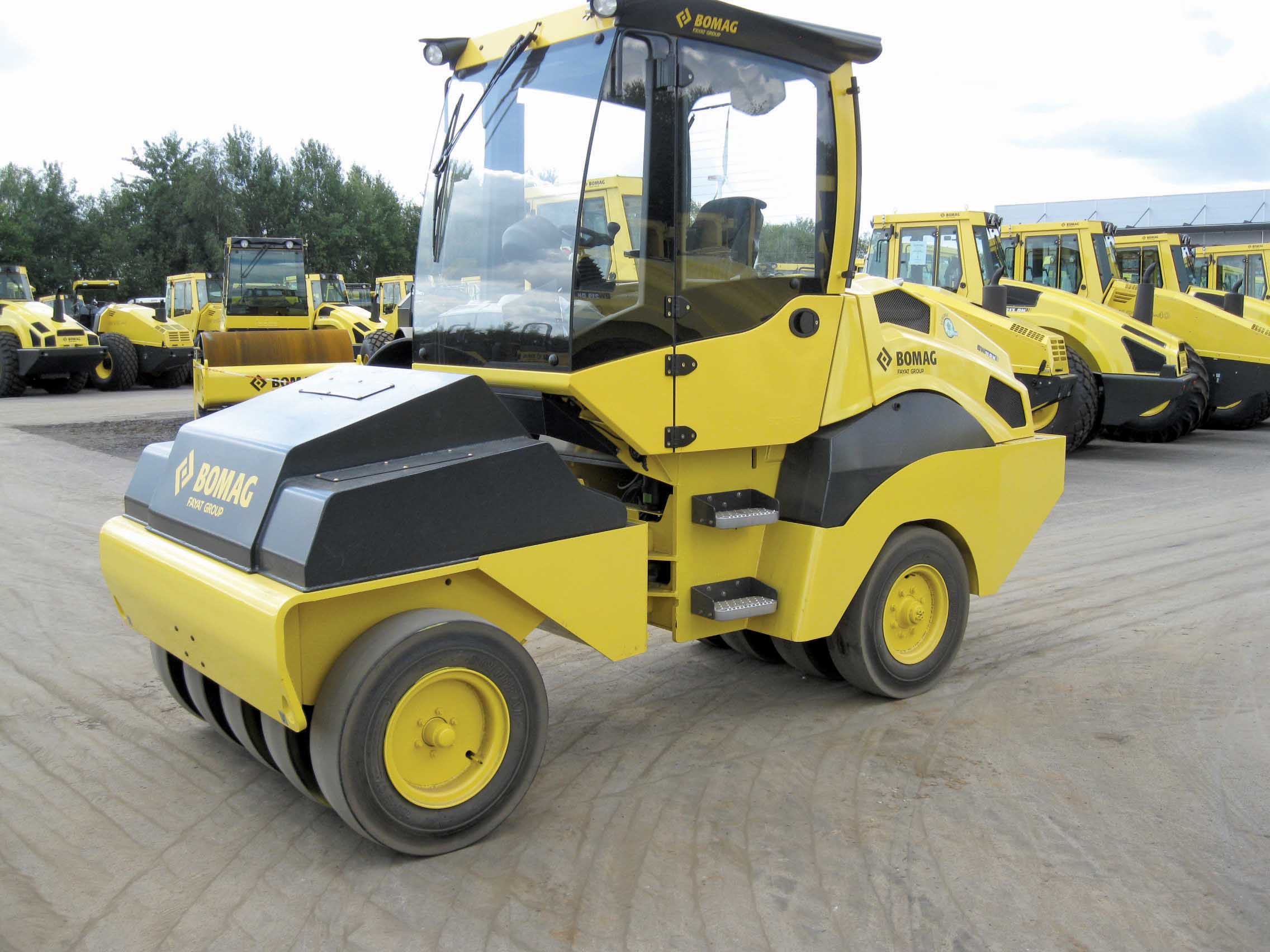
A series of new rubber tyred asphalt compactors are now coming to market from several key manufacturers - Mike Woof writes
Several of the major European compactor manufacturers are introducing new rubber tyred machines to meet demand. Pneumatic tyred rollers are often used for finishing work in road construction, due to the high quality surface they can deliver.
For a time development of these machines stalled but in recent years there has been a resurgence of interest in their use. Contractors have realised these machines do offer considerable benefits in terms of maximising production in asphalt finishing and sealing applications, while the machines are also being used in some markets for compacting dirt roads.
From
Power for the larger CP2700 comes from a Tier 4 Interim compliant diesel with low exhaust and noise emissions. Meanwhile the drive system offers a smooth start/stop system, which helps deliver a high-quality finished surface. A dual-circuit braking system is fitted for safety when the machine is working on inclines and declines.
As with other road machines from Atlas Copco, the new machines are built along modular lines and share components and sub-systems with other models in the line-up. This lowers parts holding costs as well as downtime for servicing.
The larger CP2700 offers a compaction width of 2.3m and a maximum operating weight of 26.76tonnes. This is said to suit it to a wide variety of finishing and sealing asphalt work and soil compaction applications. An optional feature is the firm’s DCA-A compaction analyser that reduces the risk of over compaction, as this can damage the roller and lower the quality of the work being carried out. This system also ensures the operator makes sufficient passes to meet the finish specification.
Also optional is a temperature sensor system, which works with the DCA-A analyser and helps achieve optimum density and surface texture. The system also provides full statistics and documentation and can be used to playback the rolling pattern and produce a printout of all relevant information. This can be delievred either on paper or as a PDF file for later analysis. The system allows contractors to replicate the same parameters on similar projects or readily supply for Federal Highway Department inspections.
Another key option is the air-on-the-run system, allowing users to adjust tyre pressures during compaction.
From
The machine is also said to offer good compaction and even surface quality, while its compact dimensions and tight turning radius of 2.7m means it can operate where space is tight. The machines have a new operator platform that benefits from single drum roller design. Meanwhile power comes from a
The new machine is available in two versions, the GRW180i-12H and the GRW180i-10, with basic weights of 12 and 10tonnes respectively. The larger GRW280 meanwhile is powered by a large six-cylinder engine and offers a maximum weight of up to 28tonnes, while the new model offers a maximum ballasted weight of 18tonnes.
The firm introduced the GRW180i to meet European and North American demand for a smaller and less powerful rubber tyred compactor. For the moment at least the machine is only offered with a Tier 4 Final compliant diesel as a result. However the existing GRW280 is available both in Tier 4 and Tier 2 variants, depending on local requirements.
Intelligent compaction initiative
Agencies, engineers, and contractors using intelligent compaction on pavement construction projects can now take advantage of a new document produced by the
The Sitka Airport document provides a practical resource for contractors looking to improve asphalt pavement construction operations. The intelligent compaction technology can be used to track compaction progress.
For the Alaskan airport project, the construction team used two Hamm IC rollers to record roller passes, asphalt surface temperature, and the stiffness of compacted materials, then display it to the roller operator in real time.
Contractor Knik Construction (Knik) used that real-time feedback to guarantee full coverage of the asphalt mat and to combat limited visibility during nighttime paving. The project’s IC operations were so successful that the final measured mat densities qualified the contractor for full bonus under the project requirements. Agencies, engineers, and contractors can use the Sitka Airport document to learn from Knik’s IC experience.
In the report, Knik describes the IC training, implementation, and data collection processes for the project. To display, analyse, and report the data collected by IC, Knik used Veda, a data management tool created by the Minnesota Department of Transportation, FHWA, and pavement engineering firm The Transtec Group.
Knik identifies the greatest benefits and limitations they experienced using IC on the Sitka Airport project. While the technology’s relative newness can be a limitation, intelligent compaction proved to be of benefit for the project by collecting records of roller settings and by providing real-time information about compaction progress. Knik says that it intends to continue implementing IC on their project