A steady resurgence in demand for rubber tyred compactors for finishing work has seen manufacturers introduce new models - Mike Woof writes
The rubber tyred compactor looked for a time as if it might disappear from the market only a few years ago, when demand began to dip for these units. However a resurgence in interest from the marketplace prompted manufacturers to revamp their respective product ranges, delivering new models to meet demand. Typically used for tasks such as finishing work, rubber tyred
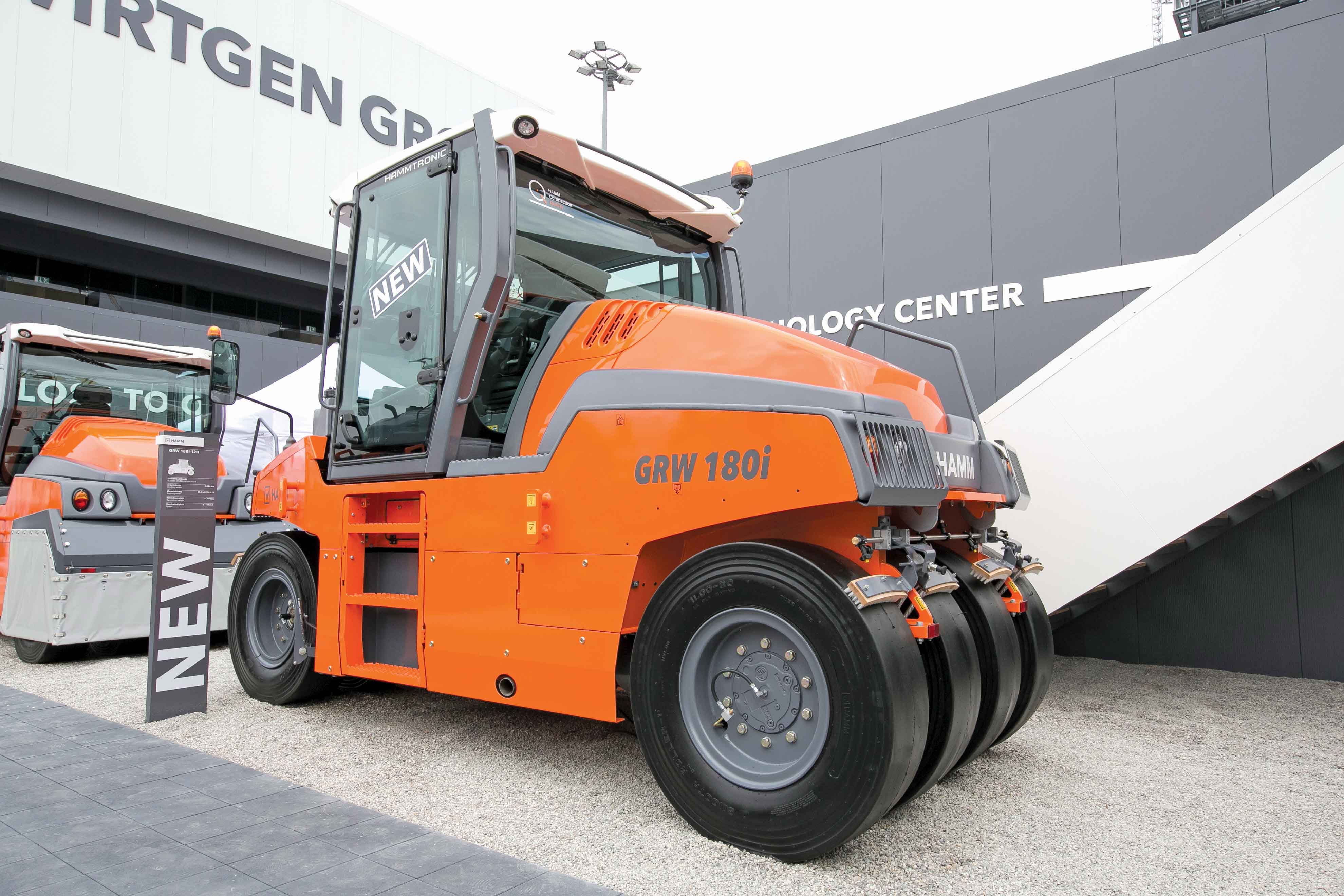
Hamm has widened its rubber tyred compactor range with the addition of a new model
A steady resurgence in demand for rubber tyred compactors for finishing work has seen manufacturers introduce new models - Mike Woof writes
The rubber tyred compactor looked for a time as if it might disappear from the market only a few years ago, when demand began to dip for these units. However a resurgence in interest from the marketplace prompted manufacturers to revamp their respective product ranges, delivering new models to meet demand. Typically used for tasks such as finishing work, rubber tyred compactors have regained their place in contractor’s equipment fleets, allowing the industry to deliver high-quality surfaces for roads, highways and runways. And the new models reflect the current thinking in machine design, allowing greater performance versatility while also being able to use the latest machine guidance and control technology.
Hydrostatic drives that offer more precise control have replaced the older mechanical drivelines, while manufacturers have taken care to improve features such as all-round visibility from the cab and also meet the latest emissions requirements. But it is worth noting too that deadweight (static) rollers are also still used by some contractors for finishing work, although market demand is lower. A number of firms also still offer these machines, with161 Atlas Copco and 2624 Sakai having recently updated their models to stay abreast of emissions requirements and meet the needs of customers looking for niche machines.
6791 Ammann has been offering rubber tyred asphalt compactors for some time, having first purchased and then integrated the Czech Stavastroj brand into its range. The revamped ART 240 is a much refined development of earlier designs and now meets the Tier 4 Final/Stage IV emissions requirements of North America and Europe. It is fitted with a large cab that is said to offer high working comfort and a seat that can be moved to suit requirements, while it has good all-round visibility due to large glass panels.
Novel features to maximise performance in different conditions include a front isostatic oscillating axle and a rear-drive system that provides the required power, regardless of tyre pressures or ballast weight. The machines are said to deliver high-quality compaction and suit finishing applications.
Atlas Copco’s206 Dynapac brand offers a range of rubber tyred rollers with the CP142 having been recently upgraded. A novel feature is its modular ballast system, with sealed ballast containers and which the firm claims allows a much closer control of the individual wheel loads. As with other machines on the market, the CP142 has a hydrostatic drive and an emissions compliant diesel. It also has a sloping front and rear, allowing greater all-round visibility for the operator.
172 BOMAG’s BW 27 RH-4i is a fairly recent addition to the range and features a three-speed hydrostatic drive, a system for which the firm was a pioneer in this type of machine. The layout of the suspension system is also designed so that the machine can best cope with undulating terrain, while tyre pressure can also be varied as required. Power comes from an emissions compliant 201 Deutz diesel rated at 95kW and the machine can compact widths of 2.04m. Operating weights vary from 8.8-27tonnes, depending on the quantity of ballast loaded in the 3.5m3 ballast compartment.
4018 Caterpillar Paving's CW34 pneumatic roller runs on eight wheels and offers compaction weights from 9-28tonnes. Users can adjust the weight using the varying quantities ballast, providing individual wheel loads from 1.07-3.38tonnes. Contractors can use modular steel, sand or water for ballast, depending on requirements. Oscillating wheels ensure even traction and weight distribution. Power comes from a Caterpillar C4.4 diesel that meets Tier 4 Final requirements and which drives the machine hydrostatically through a three-speed system and allowing a maximum speed of 19km/h.
The machine can be fitted with Caterpillar’s compaction control system as an option, which includes infrared heat monitoring and mapping technology to help deliver a high-quality surface finish. This system also records operating data for later analysis and quality control. Other important features include an automatic speed control, the ability to operate in temperatures up to 49ºC and an effective water spray system.
From228 HAMM comes the new GRW 180i, a pneumatic tyred roller aimed at finishing duties. This model can be ballasted up to 18tonnes and shares similar exterior dimensions to the existing top-of-the-range GRW 280 model, which can weigh up to 28tonnes. As with the existing GRW 280 model, the new GRW 180i features hydrostatic drives for precise operation and control.
The GRW 180i is offered in two versions, the GRW 180i-10 with a 10tonne basic weight and the GRW 180i-12H with a 12tonne basic weight to meet customer needs. Power comes from a Tier 4 Interim/Stage IIIB compliant Deutz diesel rated at 55.4kW, although a Tier 3 version is also due out shortly for use in developing markets.
The machine features the firm’s extended variable ballast concept, which is also offered on the larger GRW 280i. Like other asphalt compactors in the HAMM range, the machine can also be fitted with the firm’s sophisticated compaction monitoring and control technology, keeping track of work carried out, using heat sensors to determine mat temperature and showing areas still requiring compaction. Information on work carried out can also be stored and downloaded for later analysis or use in quality control.
Sakai’s GW751 is arguably the most notable of all the pneumatic tyred compactors available, which is offered in Latin America, Australia, Asia and the US, as well as its Japanese home market. This 9tonne machine is said to offer a similar compaction performance to a conventional pneumatic roller weighing up to 25tonnes, because it also is equipped with a patented vibration system. The GW751 runs on seven tyres, with three at the front and four at the rear and features a hollow shaft drive with an eccentric through axle configuration.
According to US sales manager Denver Weinstiger, “There’s no need for ballast so it’s easier to haul to site and it can be used in all applications.” He added, “It does an excellent job on RCC. It’s versatile and you can use it on dirt roads.”
Power comes from a Tier 4 Interim compliant1265 Kubota diesel rated at 80.5kW and the machine can compact widths of up to 2m.
The rubber tyred compactor looked for a time as if it might disappear from the market only a few years ago, when demand began to dip for these units. However a resurgence in interest from the marketplace prompted manufacturers to revamp their respective product ranges, delivering new models to meet demand. Typically used for tasks such as finishing work, rubber tyred compactors have regained their place in contractor’s equipment fleets, allowing the industry to deliver high-quality surfaces for roads, highways and runways. And the new models reflect the current thinking in machine design, allowing greater performance versatility while also being able to use the latest machine guidance and control technology.
Hydrostatic drives that offer more precise control have replaced the older mechanical drivelines, while manufacturers have taken care to improve features such as all-round visibility from the cab and also meet the latest emissions requirements. But it is worth noting too that deadweight (static) rollers are also still used by some contractors for finishing work, although market demand is lower. A number of firms also still offer these machines, with
Novel features to maximise performance in different conditions include a front isostatic oscillating axle and a rear-drive system that provides the required power, regardless of tyre pressures or ballast weight. The machines are said to deliver high-quality compaction and suit finishing applications.
Atlas Copco’s
The machine can be fitted with Caterpillar’s compaction control system as an option, which includes infrared heat monitoring and mapping technology to help deliver a high-quality surface finish. This system also records operating data for later analysis and quality control. Other important features include an automatic speed control, the ability to operate in temperatures up to 49ºC and an effective water spray system.
From
The GRW 180i is offered in two versions, the GRW 180i-10 with a 10tonne basic weight and the GRW 180i-12H with a 12tonne basic weight to meet customer needs. Power comes from a Tier 4 Interim/Stage IIIB compliant Deutz diesel rated at 55.4kW, although a Tier 3 version is also due out shortly for use in developing markets.
The machine features the firm’s extended variable ballast concept, which is also offered on the larger GRW 280i. Like other asphalt compactors in the HAMM range, the machine can also be fitted with the firm’s sophisticated compaction monitoring and control technology, keeping track of work carried out, using heat sensors to determine mat temperature and showing areas still requiring compaction. Information on work carried out can also be stored and downloaded for later analysis or use in quality control.
Sakai’s GW751 is arguably the most notable of all the pneumatic tyred compactors available, which is offered in Latin America, Australia, Asia and the US, as well as its Japanese home market. This 9tonne machine is said to offer a similar compaction performance to a conventional pneumatic roller weighing up to 25tonnes, because it also is equipped with a patented vibration system. The GW751 runs on seven tyres, with three at the front and four at the rear and features a hollow shaft drive with an eccentric through axle configuration.
According to US sales manager Denver Weinstiger, “There’s no need for ballast so it’s easier to haul to site and it can be used in all applications.” He added, “It does an excellent job on RCC. It’s versatile and you can use it on dirt roads.”
Power comes from a Tier 4 Interim compliant