A challenging airport runway project in Alaska has been carried out with the help of Roadtec construction equipment equipped with Topcon machine control systems.
Anchorage-based Knik Construction carried out the work at the airport in Yakutat, located in the southeast corner of Alaska. Bounded by the Gulf of Alaska to the South, mountains to the North, and coastal glaciers to the East and West, Yakutat is remote even for Alaska. There are no roads leading in or out and all commerce and access is by air o
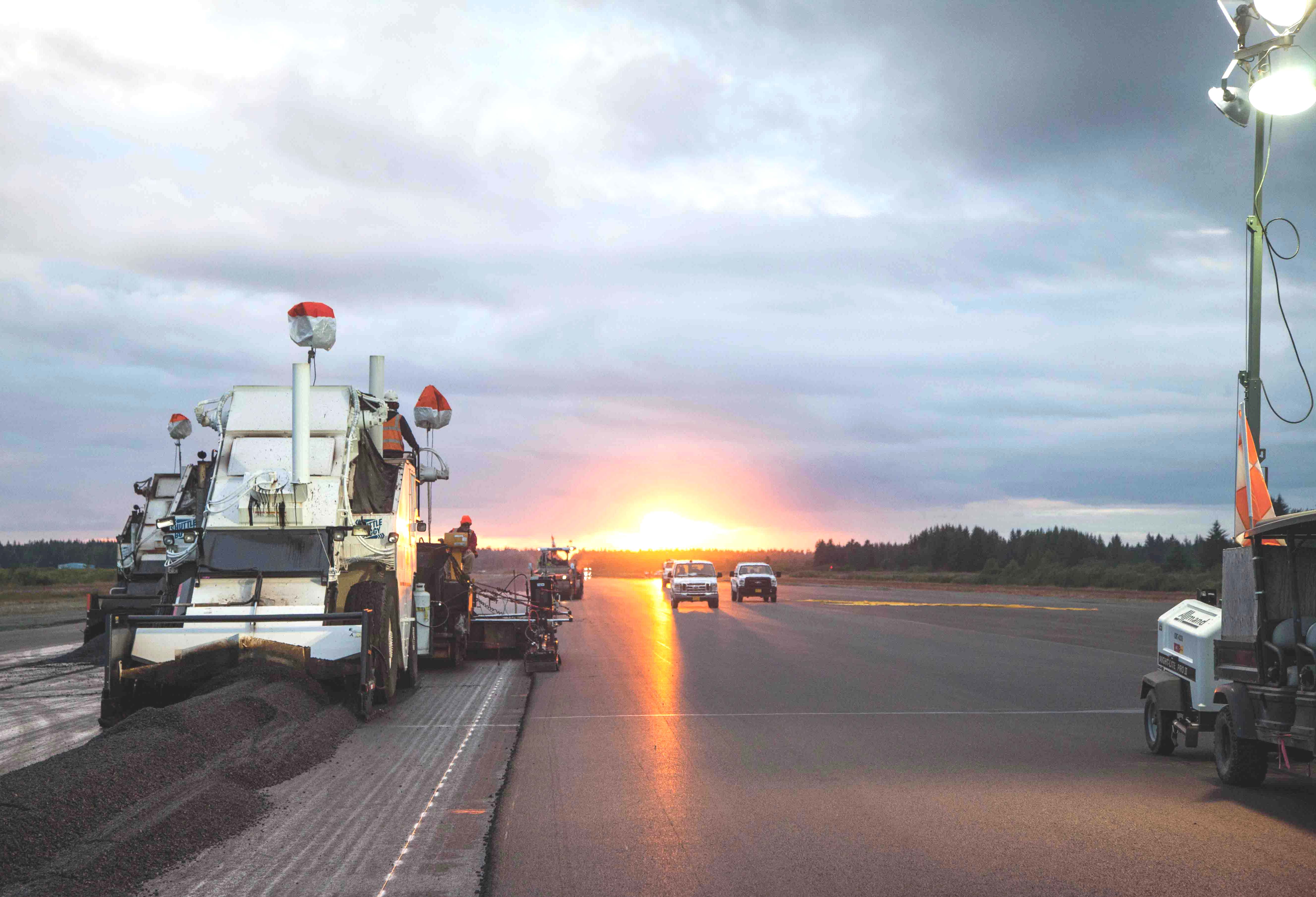
Windrow techniques were used when necessary
A challenging airport runway project in Alaska has been carried out with the help of Roadtec construction equipment equipped with Topcon machine control systems.
Anchorage-based Knik Construction carried out the work at the airport in Yakutat, located in the southeast corner of Alaska. Bounded by the Gulf of Alaska to the South, mountains to the North, and coastal glaciers to the East and West, Yakutat is remote even for Alaska. There are no roads leading in or out and all commerce and access is by air or sea.
For the contractor, rebuilding the runway facility for the5247 Alaska Department of Transportation and Public Funding (ADOT&PF) provided many challenges. The Yakutat Airport Runway Pavement Rehabilitation project required the resurfacing of the 2.48km long by 59m wide runway, as well as resurfacing the 91m taxiway. The work was carried out for the state DOT, which has responsibility for all the airports. The Yakutat Airport (YAK) is a state owned, airport located 6km southeast of the central business district of Yakutat. For the 600 residents of Yakutat, this two-runway facility is critical.
Knik explained that for the project, the runway was divided into three sections. At one end the runway tapered to an elevated 760mm, there was a middle section where two runways intersect that required varied profile milling, and a final section that needed 12.7mm surface milling to remove the texture grooves.
However the four-month project presented a logistical challenge to the contractor. All the heavy equipment, asphalt plant, supplies, and asphalt concrete material had to be shipped via barge, which came to Yakutat once/month, while over 3,000tonnes of asphalt also had to be shipped to the site.
Knik started processing aggregate in March 2016 and began work on the runway on May 1st, with the runway being ready for use at the end of August 2016. However the firm had to carefully plan its shipments, because if anything was forgotten, it would either had to wait for the next barge or be brought in by air. The firm also needed reliable machines, as component failures and machine downtime would have caused further problems.
Knik had a milling crew of three, which operated a1252 Roadtec RX900e with 3.81m cutting drum. A total of 6,000tonnes of cuttings were removed, which was mixed with 50% D-1 locally-produced aggregate base and reused as fill on the section of the runway that required elevation to alleviate water issues.
Knik explained that because of the remote location, it was beneficial to reuse the cuttings immediately rather than using stockpiling, as otherwise the material might sit for years before it would be used as fill or RAP. To ensure accurate milling depth, the cold planer was equipped with a342 Topcon GPS machine control package. This system played a crucial role in delivering the precision needed.
For the Yakutat Airport runway, Knik shipped over to the remote location a 400tonne/hour portable double drum Astec asphalt plants, eight belly-dump haul trucks, two Blaw-Knox PF4410 tracked pavers, and two Roadtec SB-2500e Shuttle Buggy MTVs. The MTVs were paired up with the pavers and their use on the project had been specified by the ADOT&PF, so as to ensure the runway would meet specifications.
There were two paving crews with six workers on each, plus eight locally-hired truck drivers. For the most part, the existing runway served as the base for the paving. The asphalt plant was located near the shipping docks. The haul trucks would collect loads and transport them 13km to the material transfer vehicles (MTVs) at the runway site.
According to Amanda Gilliland, project manager with Knik Construction, the two MTVs prevented segregation and kept both pavers productive. In instances where there was insufficient space for the trucks to dump, the belly dump trucks could offload in another area and the Shuttle Buggy would then pick up the piles and transport these back to the paver.
The Yakutat Airport project required 62,000tonnes of HMA, making it the biggest paving project in Alaska for 2016. On a good production day, Knik Construction paved up to 6,000tonnes, leaving the top lift of the runway with few transverse joints. The company also used infrared cameras to scan the freshly paved mat, to confirm that there were no cold spots.
Despite the high rain fall at times, the work was completed to specification and within the tight time schedule required.
Anchorage-based Knik Construction carried out the work at the airport in Yakutat, located in the southeast corner of Alaska. Bounded by the Gulf of Alaska to the South, mountains to the North, and coastal glaciers to the East and West, Yakutat is remote even for Alaska. There are no roads leading in or out and all commerce and access is by air or sea.
For the contractor, rebuilding the runway facility for the
Knik explained that for the project, the runway was divided into three sections. At one end the runway tapered to an elevated 760mm, there was a middle section where two runways intersect that required varied profile milling, and a final section that needed 12.7mm surface milling to remove the texture grooves.
However the four-month project presented a logistical challenge to the contractor. All the heavy equipment, asphalt plant, supplies, and asphalt concrete material had to be shipped via barge, which came to Yakutat once/month, while over 3,000tonnes of asphalt also had to be shipped to the site.
Knik started processing aggregate in March 2016 and began work on the runway on May 1st, with the runway being ready for use at the end of August 2016. However the firm had to carefully plan its shipments, because if anything was forgotten, it would either had to wait for the next barge or be brought in by air. The firm also needed reliable machines, as component failures and machine downtime would have caused further problems.
Knik had a milling crew of three, which operated a
Knik explained that because of the remote location, it was beneficial to reuse the cuttings immediately rather than using stockpiling, as otherwise the material might sit for years before it would be used as fill or RAP. To ensure accurate milling depth, the cold planer was equipped with a
For the Yakutat Airport runway, Knik shipped over to the remote location a 400tonne/hour portable double drum Astec asphalt plants, eight belly-dump haul trucks, two Blaw-Knox PF4410 tracked pavers, and two Roadtec SB-2500e Shuttle Buggy MTVs. The MTVs were paired up with the pavers and their use on the project had been specified by the ADOT&PF, so as to ensure the runway would meet specifications.
There were two paving crews with six workers on each, plus eight locally-hired truck drivers. For the most part, the existing runway served as the base for the paving. The asphalt plant was located near the shipping docks. The haul trucks would collect loads and transport them 13km to the material transfer vehicles (MTVs) at the runway site.
According to Amanda Gilliland, project manager with Knik Construction, the two MTVs prevented segregation and kept both pavers productive. In instances where there was insufficient space for the trucks to dump, the belly dump trucks could offload in another area and the Shuttle Buggy would then pick up the piles and transport these back to the paver.
The Yakutat Airport project required 62,000tonnes of HMA, making it the biggest paving project in Alaska for 2016. On a good production day, Knik Construction paved up to 6,000tonnes, leaving the top lift of the runway with few transverse joints. The company also used infrared cameras to scan the freshly paved mat, to confirm that there were no cold spots.
Despite the high rain fall at times, the work was completed to specification and within the tight time schedule required.