Milling and paving work has helped restore the road surface on an important stretch of highway in the US state of Oklahoma. US Highway 62 is a key route, running 3,597km from to Niagara Falls, New York, at the Canada–US border to the Mexico-US border at El Paso in Texas. It is the only east-west United States numbered highway that connects Canada with Mexico through the US, making it a key transport route. A 12km section of US 62 where it runs through Oklahoma recently benefited from a much-needed rebuild,
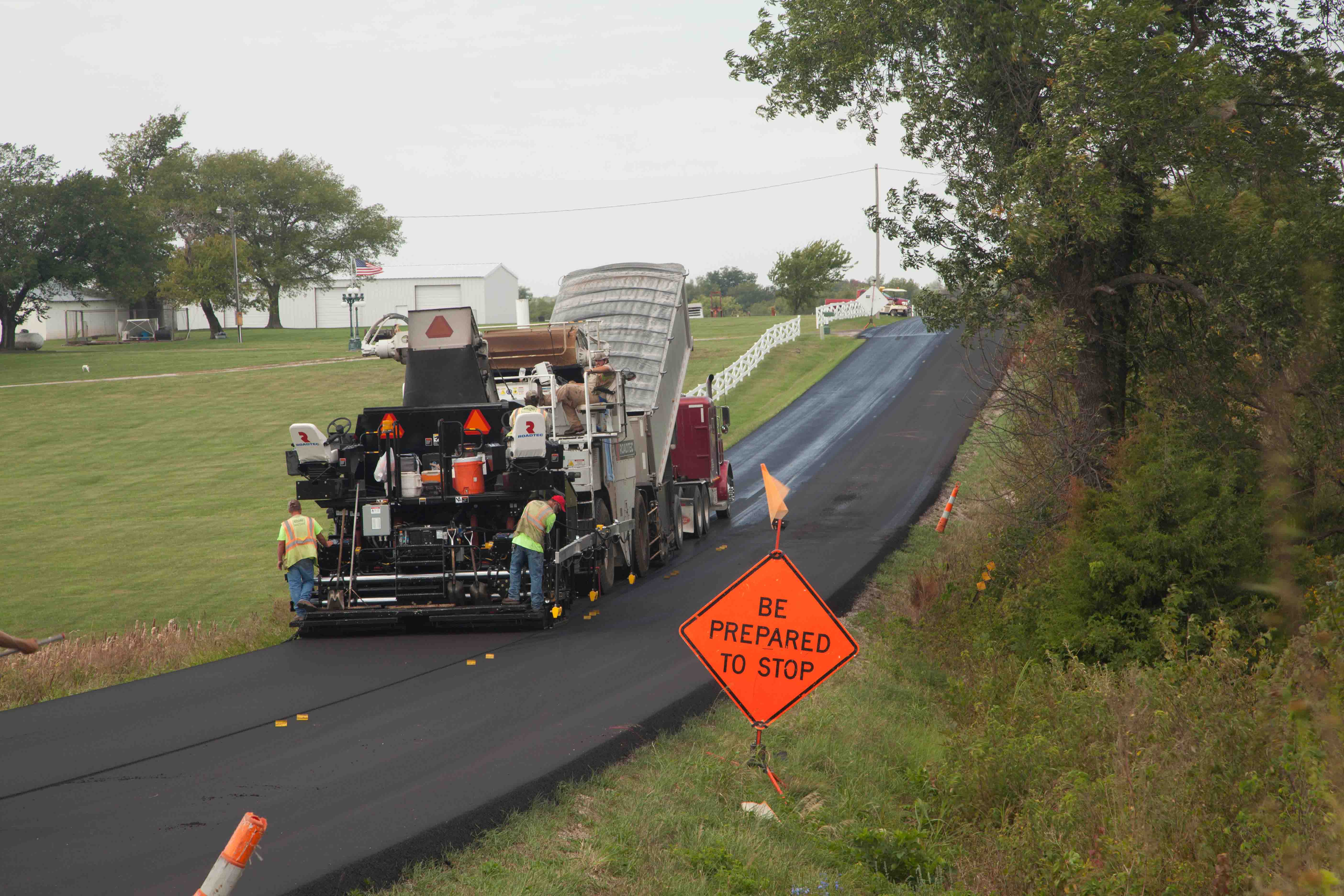
Oklahoma-based contractor Markwell Paving has used its Roadtec SP-100e Stealth paver and SB-2500e Shuttle Buggy to carry out paving work on US Highway 62
Milling and paving work has helped restore the road surface on an important stretch of highway in the US state of Oklahoma.
US Highway 62 is a key route, running 3,597km from to Niagara Falls, New York, at the Canada–US border to the Mexico-US border at El Paso in Texas. It is the only east-west United States numbered highway that connects Canada with Mexico through the US, making it a key transport route. A 12km section of US 62 where it runs through Oklahoma recently benefited from a much-needed rebuild, to improve a worn road surface.
The5295 Oklahoma Department of Transportation (ODOT) project started in Blanchard, Oklahoma, and headed west. The project section of US 62 is special because the road was built in 2000 when ODOT was switching from conventional HMA to Superpave. But the original contractor was still new to using Superpave and the mix used was less than optimal, so the surface suffered premature wear. In addition, the area where this section of US 62 is located has experienced population growth so the road has been handling a greater traffic load than originally expected.
Local firm Markwell Paving was selected as the contractor for the road repair project due to its experience in the field. The firm used its1252 Roadtec RX-700e heavy-duty milling machine, equipped with a special 3.2m width cutter drum. The half lane cold planer features a four-track suspension, dual water spray bars, and 120° conveyor swing, which allows feeding a truck in an adjacent lane or around a tight bend.
The ride quality road of the road had deteriorated and required milling to a depth of 52mm to establish a base, according to Markwell. The firm used a five-worker milling crew to complete the road milling portion of the project but found this portion of the work challenging.
For the paving team, Markwell used a crew of eight and the team placed a 52mm lift of a locally-sourced ridge intermediate layer (RIL) course directly on top of the uniformly level milled surface. This 12,628tonnes of base course contains oils and additives to bind the milled surface with the top two layers of HMA.
The contractor said that this was carried out successfully, despite the RIL mix being tricky to work with regarding ambient temperature. The firm added that weather delays for the project were mostly during the RIL paving, due to temperatures falling outside the material’s application comfort zone.
The company used its gravity-fed Roadtec SP-100e Stealth paver on the US 62 highway rehab project. This unit has a gravity feed of material directly to the auger from the mass flow hopper, without slat conveyors, hopper wings, push rollers and tandem front bogies. This reduces maintenance costs and initial purchase price over a conventional paver, a key reason why the firm opted to buy this unit. The paver worked in tandem with a Roadtec SB-2500e Shuttle Buggy material transfer vehicle (MTV), which provided a steady flow of HMA to the paver.
Markwell placed a 52mm lift of Oklahoma S4 Superpave mix surface course on top of the base course, using some 12,628tonnes of material. The SP-100e Stealth paver then placed 7,360tonnes of Oklahoma S5 Superpave HMA as a mainline finish course on the highway stretch.
ODOT has studied and tested the thermal cracking resistance of the Oklahoma S4 and Oklahoma S5 HMA mixes and found them to be stiffer, as indicated by higher creep compliance and indirect tensile strength values. Markwell Paving used the HMA mixes specified by ODOT to meet their requirements.
ODOT smoothness requirements are stringent but after testing, it was clear that the contractor had beaten the requirement by some margin. In fact, the firm believes its newly repaved stretch of US 62 to be the smoothest along the length of the entire highway.
US Highway 62 is a key route, running 3,597km from to Niagara Falls, New York, at the Canada–US border to the Mexico-US border at El Paso in Texas. It is the only east-west United States numbered highway that connects Canada with Mexico through the US, making it a key transport route. A 12km section of US 62 where it runs through Oklahoma recently benefited from a much-needed rebuild, to improve a worn road surface.
The
Local firm Markwell Paving was selected as the contractor for the road repair project due to its experience in the field. The firm used its
The ride quality road of the road had deteriorated and required milling to a depth of 52mm to establish a base, according to Markwell. The firm used a five-worker milling crew to complete the road milling portion of the project but found this portion of the work challenging.
For the paving team, Markwell used a crew of eight and the team placed a 52mm lift of a locally-sourced ridge intermediate layer (RIL) course directly on top of the uniformly level milled surface. This 12,628tonnes of base course contains oils and additives to bind the milled surface with the top two layers of HMA.
The contractor said that this was carried out successfully, despite the RIL mix being tricky to work with regarding ambient temperature. The firm added that weather delays for the project were mostly during the RIL paving, due to temperatures falling outside the material’s application comfort zone.
The company used its gravity-fed Roadtec SP-100e Stealth paver on the US 62 highway rehab project. This unit has a gravity feed of material directly to the auger from the mass flow hopper, without slat conveyors, hopper wings, push rollers and tandem front bogies. This reduces maintenance costs and initial purchase price over a conventional paver, a key reason why the firm opted to buy this unit. The paver worked in tandem with a Roadtec SB-2500e Shuttle Buggy material transfer vehicle (MTV), which provided a steady flow of HMA to the paver.
Markwell placed a 52mm lift of Oklahoma S4 Superpave mix surface course on top of the base course, using some 12,628tonnes of material. The SP-100e Stealth paver then placed 7,360tonnes of Oklahoma S5 Superpave HMA as a mainline finish course on the highway stretch.
ODOT has studied and tested the thermal cracking resistance of the Oklahoma S4 and Oklahoma S5 HMA mixes and found them to be stiffer, as indicated by higher creep compliance and indirect tensile strength values. Markwell Paving used the HMA mixes specified by ODOT to meet their requirements.
ODOT smoothness requirements are stringent but after testing, it was clear that the contractor had beaten the requirement by some margin. In fact, the firm believes its newly repaved stretch of US 62 to be the smoothest along the length of the entire highway.