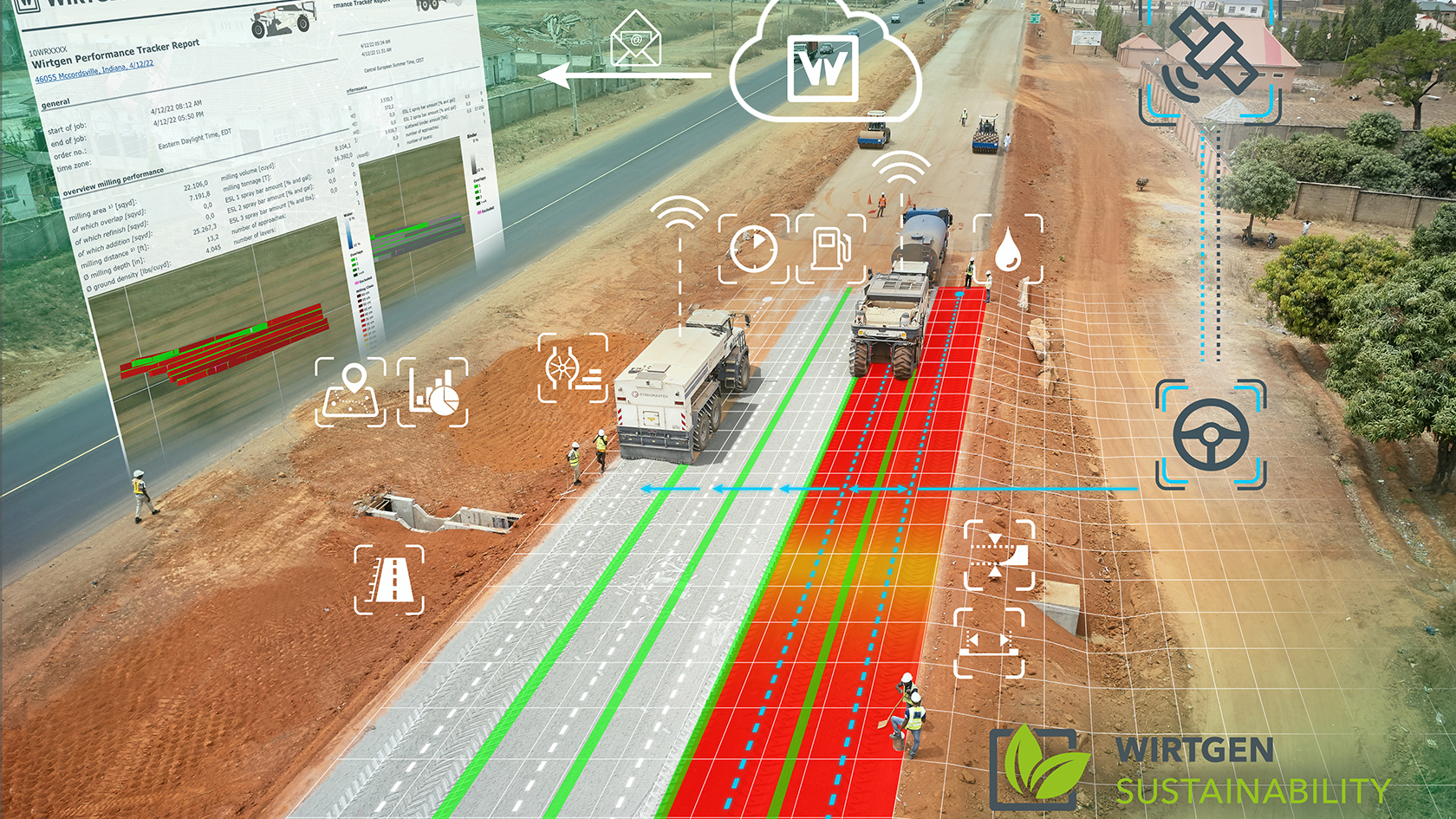
Road recycling traditionally covers a lot of areas and many different types of machines, from soil stabilisers to pavement planers. Whether its road profiling, reclaiming, milling or planning, the machines are getting smarter every year and with every update.
Many updates focus on making the recycling machine much more accurate and easier to position than before, thanks to refinements to GNSS, global navigation satellite systems. GNSS is a general term describing any satellite grouping that provides geo-location positioning, navigation and time information – PNT - services on a global or regional basis. While the US government-owned Global Positioning System (GPS), initially called Navstar GPS, remains the most prevalent GNSS, other countries are setting up similar systems that can complement GPS.
Improved positioning accuracy for road recyclers thanks to GNSS is saving road crews time and effort. Wirtgen - often in the forefront of new technology applications - continues to take advantage of GNSS. The German global manufacturer is now offering an innovative satellite-based AutoTrac steering system for its wheeled WR-series recyclers and stabilisers. According to the firm, this allows the machines to deliver efficient working, providing precision steering to centimetre accuracy. The system works uses a previously determined reference strip and a specified overlap of adjacent strips, allowing consistent use of the optimum working width, boosting efficiency.
The WR-series machines are also available with the Wirtgen Performance Tracker. The system registers location-specific working parameters to provide a database for site analysis and documentation. For soil stabilisers, data includes working width and depth, area and distance worked and fuel consumption.
The technology is available for the firm’s latest WR series wheeled recycler/stabilisers. The WR-series recyclers have all-wheel drive and have working widths of up to 2.4m and high milling and mixing performances.
Meanwhile, the top-of-the-recycler -range W 380 Cri is a tracked rear loader with a mixing capacity of up to 800tonnes/hour and can be used for both cold in-place recycling (CIR) and full-depth reclamation (FDR) for the rehabilitation of wide roadways.
Caterpillar is another cold planner manufacturer that has taken GPS into the heart of its machinery and upgraded its technology to take advantage of it. Cat GRADE technology for cold planers allows for better accuracy, less rework and lower costs in rough-, fine- and finish-grade applications. Whether a 2D grade and 3D grade system, self-contained or using laser or GPS guidance, Cat GRADE control systems improve grading efficiency. Milling operators can achieve accurate and repeatable cutting results to create a smooth base for any project. The integrated system uses automated features to take the guesswork out of producing a consistent cut every time.
Operators can gain full control over grade and slope from any of the control boxes located on the operator platform or at ground level. Grade and Slope enhances other features on the machine such as automated transitions into or out of a cut, adjustable plunge velocity, obstacle jump and the standby-and-resume function.
There are easily set and executed grade and slope transitions for tapered start or end cuts over a specified distance. Cat GRADE can adjust the speed at which the rotor drops into the cut for optimal machine control. Obstacles in the cutting path can be cleared easily thanks to the obstacle jump feature. There is also a seamless swap between multiple grade sensors for uninterrupted accuracy during milling. For the operator, control boxes can be repositioned without the need to reconfigure settings.
As always, recycling is about reusing the road material just planed from the highway surface, meaning the material to be recycled must be in useable form.
The new CBA asphalt granulator bucket from Italian manufacturer Simex, is ideal for recovering milled asphalt material, classified in national regulations as bituminous conglomerate granulate (or RAP – recycled asphalt pavement). It reduces asphalt slabs to certifiable grain size thanks to the configurable rear grid. Simex says that the CBA bucket has the dual advantage of combining reduced construction site costs - less supply of new raw materials - while at the same time offers the possibility of reintroducing the milled material into the production cycle of new asphalt.
Simex’s R&D department has combined the concept of milling drums with rotor crusher bucket technology, creating the three-model CBA asphalt granulator bucket range: CBA 20, CBA 30 and CBA 40 for 12-40tonne excavators. The equipment features a cylindrical drum of asymmetric teeth driven by large displacement radial piston hydraulic motors in direct drive. The rear grid determines the grain size of the material output. It is available in several configurations to meet the regulations covering milled material in varying countries.
Simex says the CBA asphalt granulator buckets aim to ensure broad autonomy for operators engaged daily in road maintenance works, crushing aggregates and filling excavations for laying underground utilities. Cutting down the time and costs related to transport and minimising the purchase of new raw materials means optimising your site's logistical and economic dynamics while reducing environmental impact by recovering materials considered a reusable resource rather than waste.
RAP has always been part of the sustainability agenda. Its increased use across the globe means RAP machine manufacturers are continually having to improve the green credentials of their products. CAMS, another equipment manufacturer based in Italy, has risen to this challenge with the recent launch of the Centauro XL 150 APR series – APR standing for asphalt pavement recycler.
CAMS’ APR series combines one primary shredder supported by patented pre-crushing technology, one iron separator, a screening unit and a secondary shredder. All these elements are combined in a single mobile plant powered by a powerful Diesel Cat C9.3 Stage V engine, ensuring the recovery of all removed slabs and milled asphalt while preserving the original bitumen content.
Importantly, for clients where sustainable worksite practices are paramount, the Centauro XL 150 APR series - as well as all the other mobile CAMS machines - can operate in hybrid or full electric mode without a diesel engine. This premium mobile recycling plant is equipped with biodegradable lubricants and, says CAMS, guarantees minimal noise and dust emissions. The technology is also said by CAMS to greatly reduce fuel consumption and can supply electricity to work-site equipment using its integrated genset, thus ensuring optimum sustainability.
The Centauro APR series’ secondary shredder characterises the APR version differently from those units designed for recycling materials other than asphalt. Other highlights include automatic programmes for shredding various material sizes, the ability to process wet materials, a single genset for supplying all components, high wear-resistance and compact transport dimensions.
The APR series is available in two models: Centauro XL 150.56 APR, which can process up to 250 tonnes per hour. It is equipped with a primary shredder with a 1,500mm x 900mm surface and a two-deck screen (4,300mm x 1,300mm). The top-of-the-range Centauro XL 150.69 APR also offers up to 250 tonnes per hour production and a 1,500mm x 900mm surface primary shredder. Its two-deck screen is larger than the Centauro XL 150.56 APR, coming in at 5,300mm x 1,300mm.