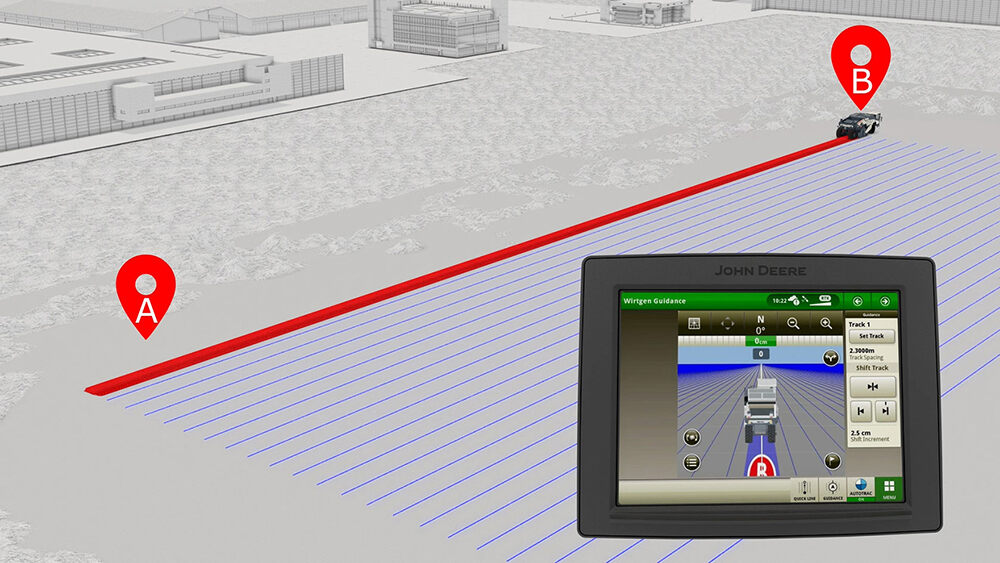
In view of growing demands for environmentally compatible processes, the need for responsible handling of valuable resources is also increasing in the areas of soil stabilisation and cold recycling. Cost-effective realisation of these processes is only possible when they are efficiently executed. With the launch of the AutoTrac system for the WR series, it now offers a technology that focuses on precisely this.
Pioneering technology for soil stabilisation and cold recycling
Soil stabilisers are used, for example, for the resource-friendly preparation of road beds in the course of traffic infrastructure projects. A sub-base with insufficient load bearing capacity is transformed into resilient ground that can withstand heavier loading. This process takes the existing soil material and simply adds and mixes in binding agents such as cement and/or lime. In the case of cold recycling with WR series machines, damaged asphalt layers are milled and resized in a single operation, re-bound by the addition of binding agents and water and then repaved. The new base layers produced on site then stand out due to their exceptional bearing capacity.
Automatic steering system for optimal overlaps
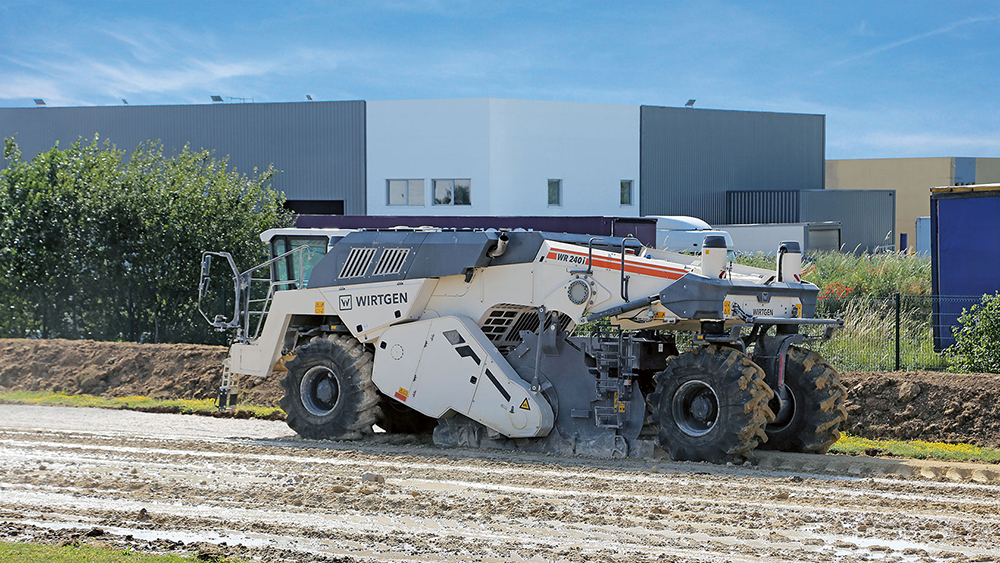
By enabling precise, automatic steering, the AutoTrac system helps Wirtgen wheeled recyclers to achieve greater process efficiency and, as a result of this, a high degree of environmental compatibility. It steers the machine precisely within tolerances reckoned in centimetres on the basis of a previously calculated reference strip and a specified overlap of adjacent strips, enabling consistent utilisation of the machine’s ideal working width. AutoTrac relies, among other things, on various global navigation satellite systems (GNSS) for precise determination of the machine’s position and direction of travel. The system is operated from an additional control panel that also enables the operator to view information about the position of the machine and previously completed strips.
Make the best of savings potentials and increase process quality
Considering the sum of the large, avoidable overlaps with neighbouring strips that can occur in manual operations and the corresponding wastage of resources, the potential savings the system can bring soon become obvious. Keeping to the pre-set overlaps reduces the consumption of binding agents, consumables and fuel, makes the carbon footprint smaller and shortens the project completion time. The outcome of this is increased process efficiency and, in consequence, greater cost-effectiveness and environmental compatibility. Manual steering of the machine always requires considerable effort when it comes to avoiding unprocessed gaps in the ground being worked. Here again, the automatic steering system assists the operator and reduces the workload. Maintaining the desired overlap avoids unwanted gaps in the final results. Knowing this allows the operator to concentrate fully on the mixing process and keep an eye on what’s going on around the machine.
Booth's S5020 & W40844
Content produced in association with Wirtgen Group