In Japan, major efforts are being made to both conserve energy and materials, while also delivering high quality airport runways. At Haneda Airport, as well as at the Fukuoka, Chitose and Sendai airports, innovative use is being made of asphalt paving equipment from Sumitomo. The latest model HA60W J paver from Sumitomo is being used to lay warm mix asphalt, while the contractors is also using sophisticated control technology. To minimise disruption to flight schedules, construction work at Haneda has been
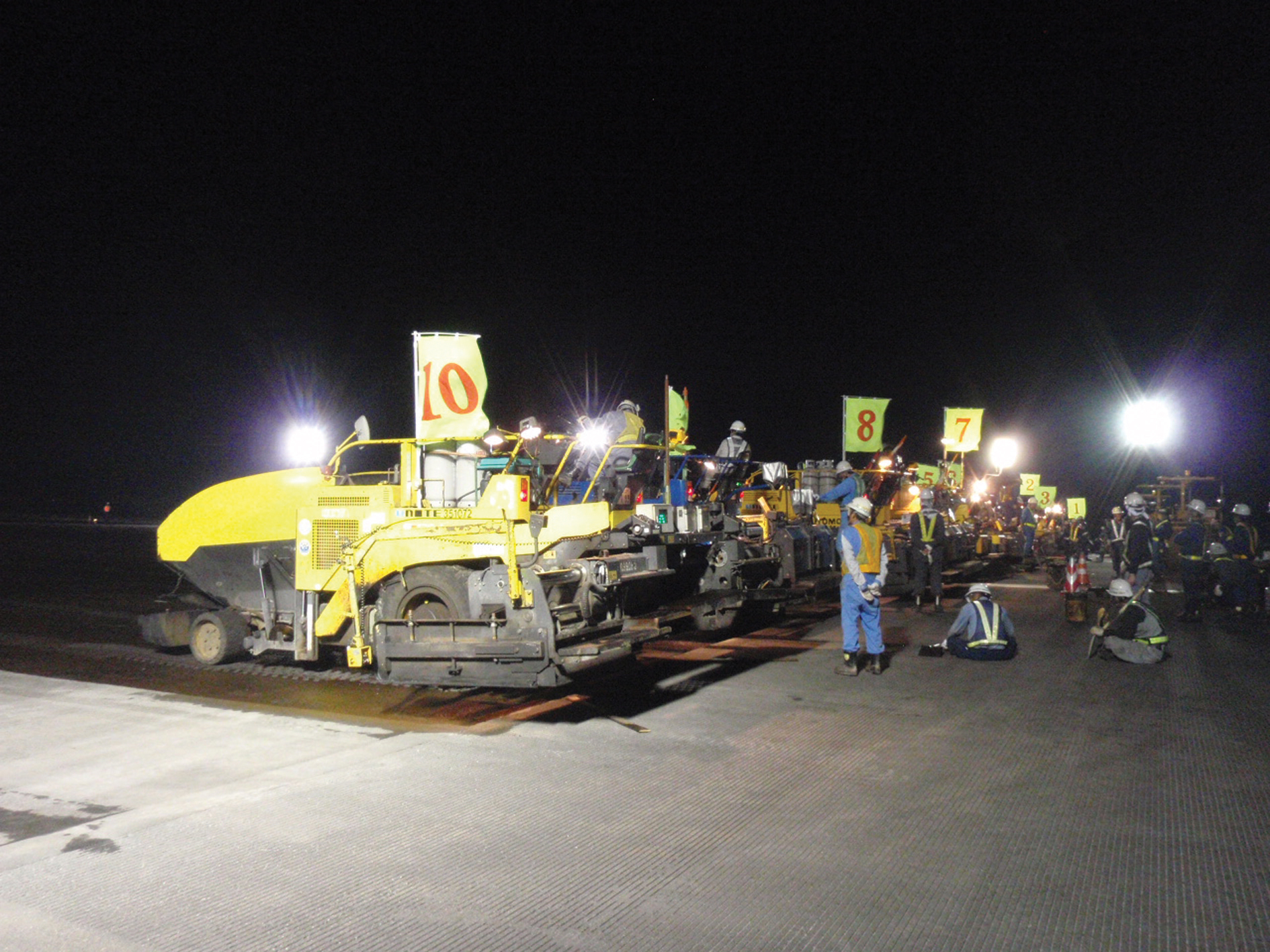
At Haneda airport 10 Sumitomo pavers were used simultaneously to lay the entire runway width and benefit from hot to hot joints for long surface life
In Japan, major efforts are being made to both conserve energy and materials, while also delivering high quality airport runways. At Haneda Airport, as well as at the Fukuoka, Chitose and Sendai airports, innovative use is being made of asphalt paving equipment from Sumitomo. The latest model HA60W J paver from Sumitomo is being used to lay warm mix asphalt, while the contractors is also using sophisticated control technology.
To minimise disruption to flight schedules, construction work at Haneda has been carried out during the night and this has included working at low temperatures on occasion. Work has started at around 11:00pm, with cutting out the areas for repairs, followed by laying of the binder course and surface course. Time constraints mean that by 5:00am in the morning, all of the work has to be complete and all machinery removed from the site to allow aircraft movements. For airport maintenance and repair work, punctual working is essential as heavy costs can be incurred should flights be delayed. With such constraints, warm mix asphalt combined with sophisticated paving controls are required to meet the efficiency, quality, cost reduction, and environmental conservation, needs of the application.One key to the work has been the use of
At Haneda Airport, up to 50m was paved simultaneously using a hot to hot joint technique, with 10 HA60Ws working at once. The screed is equipped with tamper, vibrator, and strike-off, allowing the use of various kinds of asphalt mix. In addition, the machine was used successfully in a thick lift pavement of binder course averaging 140mm at Fukuoka Airport. The material used was warm mix asphalt with 20mmT surface course and 30mmT binder course, resulting in an even surface finish without segregation. The paver can also be used with all of the latest paving controls, as well as advanced software tools, to maximise accuracy and efficiency.
For the airport work, screed height adjustment has been controlled automatically by a system combining either GNSS and laser guidance, or using positioning data obtained from a total station and 3D design information. Using this equipment has eliminated the need for conventional sensors, reducing the risk of human error and increasing accuracy, while removing the need for staking out the site and offering benefits for night-time working as a result.
Paving controls do away with preparation time needed for conventional sensors and provide more time for paving, while accuracy is increased, reducing material losses.
The use of warm mix asphalt (WMA) offers particular benefits for night-time working, which was why this material was used for these airport jobs. With warm mix, paving temperatures are reduced by 30-50°C when compared to conventional hot mix asphalt, while WMA can also be compacted effectively at lower temperatures, leaving a longer time window for paving crews. This reduces logistics problems for materials supply as well as increasing the paving period through the year.
Once laid, WMA can help reduce the incidence of rutting type deformations that can occur with conventional asphalt during hot weather under heavy loads. And importantly, the curing period is reduced after paving the binder course, while WMA also means that the site can be opened at an earlier stage after laying the surface course. Using WMA provides more time for paving and suits the use of the material to time-dependent airport construction operations. In addition, WMA also offers environmental benefits due to the lower energy profile required during its use.