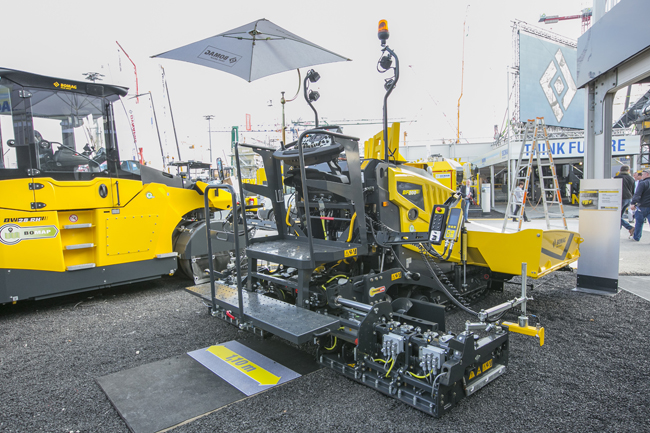
A wide array of new asphalt paving systems is now coming to market. Various manufacturers from Europe, Japan and the US have introduced new models offering increased performance and capacity. Many of these latest pavers are high production units that can utilise advanced machine control technology, delivering higher quality and production rates, as well as full data recording.
One of the smallest asphalt pavers on the market,
The company has also made upgrades to its larger pavers, such as fitting new screed control panels and installing LED lighting at the side of the screed to allow the operator to see the joint edges during night-time paving. The top-of-the-range machines now come with the firm’s advanced PaveManager 2.0 control system, which provides continuous data feedback over paving operations and allows adjustments to be made in real time. This package can be integrated with paving technology from other suppliers, such as
The smallest paver from
Another new development now being offered on the firm’s larger pavers is its latest control system. First available on the BF700 model, this features paver controls mounted on the seat arms. According to BOMAG, the new layout offers better comfort and ergonomics by preventing the operator from hunching forward in the seat to use the control panel. Without a control panel in front of the operator’s eyeline, forward visibility over the hopper is also said to be improved, assisting truck loading.
US screed specialist
Colwell said, “We’ve leveraged a lot of technology from our other screeds in this.” He added that it has special bushes inside the extension system that allow the user to take up any wear in the system. Meanwhile, the design of the extension system is said to ensure optimum paving accuracy even as the screed ages.
The ECZ34 TV screed offers hydraulic extension from 1.8-3.4m, with a maximum paving width of 4.5m when equipped with bolt-on extensions, while a minimum pave width of 750mm can also be achieved. A vibratory only variant of the screed, the ECZ34 V, is also available for the North American market, fitted to the more basic CP60 version of the paver with 2x6 drive. Both the ECZ34 TV and ECZ34 V screeds offer maximum paving thicknesses of 200mm. The machine weighs 9.35tonnes and can deliver up to 250tonnes/hour.
Power comes from a TCD 2.9 L4
The control panel is said to be simple to use even for an inexperienced operator. The controls for setting layer thickness and the dosing of the material are said to provide an ergonomic and precise working environment in narrow spaces.
Meanwhile, robust components are said to extend service life and deliver high up time. The machine has a hydraulically extendable screed, allowing working widths ranging from 0.25-1.3m, and with optional extensions up to 1.65m. In addition, Dynapac’s MF2500CS material transfer vehicle has been upgraded with several new features, intended to improve performance.
Roadtec is now offering a new material transfer vehicle (MTV) in the shape of its MTV 1105e model. The machine weighs in at 21.7tonnes unladen and features power from a
The machine does not have the remixing capability of its stable mate, the Shuttle Buggy, and instead utilises the proven chassis of the firm’s wheeled MTV 1100 model. Also the proven tracked undercarriage system from the firm’s own RP 195e asphalt paver has been married to the MTV 1100 chassis, to deliver this new model variant.
Operating weight of the prototype HA60C-11 is 15tonnes and it is just under 2.5m wide, making it ideal for the European market. The machine is powered by a Yanmar diesel delivering 110kW that is Stage V compliant, a notable increase over the previous generation machine, which featured a diesel rated at 92kW. The paving speed is 20m/min while travel speed is 3km/h.
The paver HA60C-11 comes with Sumitomo’s successful J-Paver 2360 screed, said Weichao. The paving width is variable from 2.3-6m without the need for any bolt-ons. Updates to the screed have also made it more rugged and rigid, improving paving accuracy.
The machine is said to be easy to use, with a new wide deck design and twin seats that can be swung over either side, allowing better visibility of the screed edges. Other general features include lower running costs and ease of maintenance.
Weichao said the HA60C-11, along with a wheeled version, will be available commercially by mid-2020. The firm will be introducing an upgraded version of its larger HA90 paver featuring similar improvements in due course although this is still in development. As part of Sumitomo’s strategy, the company is looking to expand its European dealer network. Sumitomo’s strategy is to encourage its current client base to try the HA60C-11 in order to develop market confidence in its pavers, said Weichao.
Making a big impression on the market is the giant SUPER 3000-3(i) paver from
Another innovative feature of the SUPER 3000-3(i) is the design that provides the operator with infinite height adjustment at the rear of the chassis. This is important for paving thick asphalt layers, as it allows the operator to ensure that the auger is not too deep in the asphalt, which can increase material segregation.
As with other Vögele pavers, the SUPER 3000-3(i) features the firm’s sophisticated AutoSet Plus package that offers automated functions, PaveDock Assistant communication system and VÖGELE EcoPlus low-emissions package. However, despite it high throughput and 18m maximum paving width, the SUPER 3000-3(i) paver offers a transport width of just 3m and its canopy can also be folded down, reducing overall height and making it easier to transport.
In addition, the latest version of the WITOS package from Vögele is now being offered as an option for its asphalt pavers. The WITOS Paving Docu system provides an option for automated documentation of onsite operations carried out with a paver. This is a new software-based process-management solution.
This new system comes in addition to the two options currently available from Vögele for recording and evaluating jobsite data. These existing systems are the RoadScan non-contacting temperature measurement system, which allows a site manager to monitor paving temperature and the WITOS Paving Plus telematics solution, which allows the coordination and optimisation of processes from mixing plant to paving. The latest innovation is WITOS Paving Docu and has been developed for contractors that want to record and evaluate data, in addition to the paving temperature, but do not need the full range of WITOS Paving Plus functions and process optimisation tools. The system also comes with a specially developed app.
The new WITOS Paving Docu system allows site managers to initiate jobs directly on the jobsite without prior planning, recording all the paver and paving data. In addition, delivery notes can be scanned in using a QR code or entered manually. At the end of each day’s operations, the system can send out automated jobsite reports. The app and pavers are networked via WLAN, allowing information to be transferred without a GSM connection.
Volvo Construction Equipment’s (
The firm says that the P2820D ABG and P2870D ABG are quiet in operation, suiting them to inner-city projects, such as cycle tracks and parking lots. Highly efficient, the new machines also promise low fuel consumption and low CO² emissions. With their 55kW Volvo engines and well-matched hydraulics, the pavers have efficient drives.
Customers can choose between the more common dual conveyor or Volvo’s novel single conveyor. Adding to the pavers’ versatility are options that include individually operated hopper wings, enabling each unit to pave closer to obstacles, and an electro-hydraulic foldable roof.