This month we report on two very different deals which see materials testing equipment companies in Italy and Australia joining forces and the result should be more competition, better machines and better prices for customers - Kristina Smith writes Italy’s CONTROLS Group has acquired Autralia’s IPC Global in a deal signed on 31 March this year.The first of two deals which see Italy and Australia joining forces came in March this year. CONTROLS Group acquired Australian material testing equipment manufactur
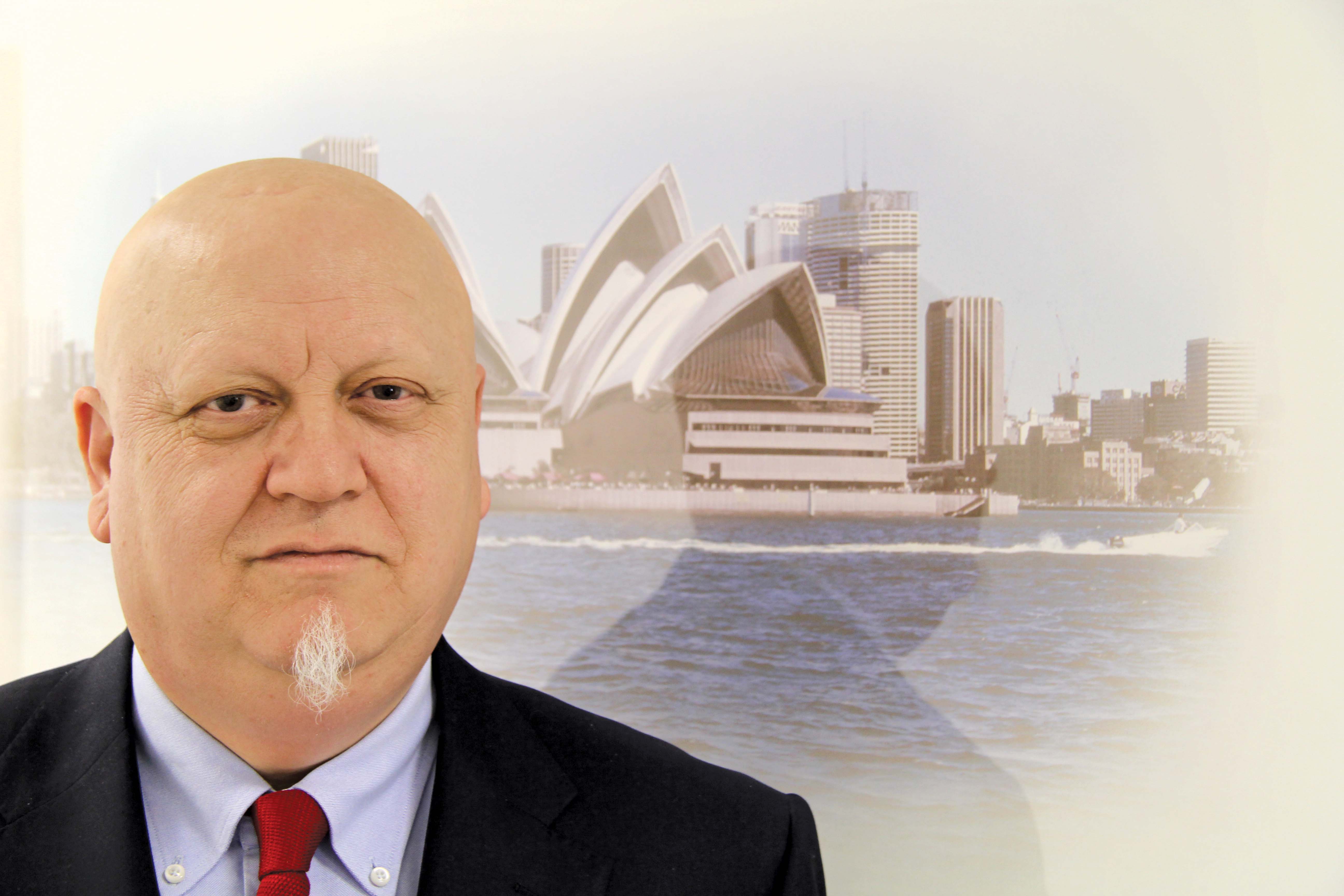
Pasquale Di Iorio CONTROLS
This month we report on two very different deals which see materials testing equipment companies in Italy and Australia joining forces and the result should be more competition, better machines and better prices for customers - Kristina Smith writes
Italy’s2139 Controls Group has acquired Autralia’s 3912 IPC Global in a Deal signed on 31 March this year.The first of two deals which see Italy and Australia joining forces came in March this year. Controls Group acquired Australian material testing equipment manufacturer IPC Global for an undisclosed sum in a move aimed to broaden the Italian group’s offering, according to president and majority shareholder Pasquale Di Iorio.
“Controls Group can now cover all the market segments in asphalt testing,” Di Iorio told World Highways. “We now have a complete range of static and dynamic products and testing solutions, from characterisation of bituminous mixes, production, quality control and quality assurance through to advanced materials research.”
IPC Global, said Di Iorio, has established its reputation in the high-end testing market over its 30-year life. As well as asphalt testing equipment, IPC Global manufactures machines for dynamic soil testing, structural testing and high-pressure triaxial rock testing.
“IPC’s capacity to innovate and design new equipment and be at the forefront of technology has created a reputation and a position identified in the highest end of the market,” he said, “So IPC is the researcher’s choice for advanced testing equipment for testing materials.”
Customers will benefit, said Di Iorio, because CONTROL’s manufacturing know-how will allow the same quality of IPC machines to be produced more cost-effectively.
“There is enormous synergy, especially in the industrial section of the group,” he said. “The advantage for IPC will be huge, due to the fact that it can produce a top quality product at a better cost and more efficiently. As a result, it will be more competitive, offering a better price for the customer.”
Di Iorio emphasised that IPC Global will remain an autonomous member of the Controls Group, with manufacturing continuing in Australia.
New machines at Asphaltica-Samoter 2014
Controls Group’s asphalt testing division PAVELAB SYSTEMS revealed some new machines at the160 Asphaltica-323 Samoter exhibition in Verona.
A new model of automatic closed-system analyser, the 75-PV50A05/S, which has more functions and a more ergonomic design than its predecessor, according to Controls will be on show. The analyser separates bitumen, filler and aggregates from asphalt samples in order to determine the composition of a mix.
The DUCTIMETER model 81-PV10C02 will also be unveiled at the exhibition. This testing machine determines the ductility of bituminous materials.
Controls Group has three brands covering asphalt testing, concrete and cement testing and soil testing: PAVELAB SYSTEMS, Controls and Wykeham Farrance, respectively. Its relationship with IPC Global began in 1994 when Controls purchased UK-based soil testing specialist Wykeham Farrance. At that time, IPC was supplying advanced soil testing equipment to Wykeham Farrance.
In 1995, Controls and IPC Global signed an agreement which saw Controls promote and distribute IPC’s dynamic testing equipment for roads around the world. However in 2010, this agreement stopped. Two years later, Controls Group launched it specialist asphalt testing division PAVELAB SYSTEMS, unveiling several dynamic testing schemes.
According to Di Iorio, very few products overlap between the two companies, meaning that technology transfer from IPC Global to Controls will be limited. “We cannot say in general that there will be transfer of technology. Controls, that mainly covers characterisation of materials, mix design, quality, production and so on, already has its own technology,” he said. “There are some areas, for example in dynamic testing in which IPC is at the forefront, but limited to this sector.”
When asked which IPC testing equipment Controls most admired, Di Iorio identified four technologies. The AMPT/SPT (Asphalt Mixture Performance Tester/Simple Performance Tester) which was developed to ‘democratise’ asphalt performance tests by allowing a range of tests on one machine.
“The AMPT is absolutely exclusive to IPC world-wide,” said Mr Di Iorio. IPC Global’s AMPT is the most popular AMPT on the market, by a ratio over 10:1 according to Controls, used in over 20 countries.
IPC Global’s SERVOPAC is “the most advanced research specification gyratory compactor available on the market,” according to Controls. With four digitally controlled servo-pneumatic actuators, it has the ability to adjust axial stress, gyratory angle and the rate of gyration.
Controls also identified IPC’s PReSBOX, an asphalt shearbox compactor which produces asphalt beams and cylinders, aimed to produce more homogenous specimens than those made by gyratory or roller compaction; and IPC’s software system, IMACS (Integrated Multi-Axis Control and Data Acquisition Software).
Meanwhile, Italian manufacturer282 Matest announced a new division, Pavetest, which will supply dynamic testing systems. Based in Australia, Pavestest is the brainchild of Australian materials testing machines veterans Con Sinadinos and Alan Feeley who between them have 38 years of experience in the field.
Sinadinos, who was CEO of IPC Global until 2012, is heading up Pavetest. Feeley, Pavetest’s technical director, was head of R&D at IPC Global.
“We develop the equipment together with the control system and the software here and then it will be value engineered by Matest and produced in Italy,” said Sinadinos , speaking to World Highways from Melbourne.
Pavetest will be offering a range of universal servo-pneumatic and servo-hydrualic testing machines and associated jigs and fixtures, said Sinadinos, as well as stand-alone machines such as the four-point bending device and the AMPT. Some machines were seen for the first time at Asphaltica-Samoter in Verona (see box). “There will be more systems down the track,” said Sinadinos.
This development is good news for the market, said Sinadinos. “The advantage for all customers is that there will be increased competition and a bigger choice. Hopefully it will drive innovation higher and prices lower. And everyone will have to lift their game in terms of service.”
One distinction between Matest’s existing equipment and its dynamic testing equipment will be the way data is captured, processed and displayed. “Matest has a fantastic system which is good for monotonic or low cycle testing, which is capable of recording 200 readings/second,” said Sinadinos. “The control and data acquisition system for the dynamic machines can sample 200,000 readings per second across 24 channels.
“That requires a huge investment in software that is capable of recording, displaying and analysing that volume of data.” Sinadinos and Feely have written the software.
Sinadinos agreed to join forces with Matest, which owns half of Pavetest, because he felt that there was a good cultural fit between the two companies. “I have always been impressed with the quality of their equipment,” he said. “And a lot of their distributors speak highly of them which is always an indication that they are ethical and good people to work with.”
IPC’s new AUSTRACK can take 1m-diameter tyres allowing full scale wheel-tracking in the lab]
IPC Global’s new AUSTRACK is an accelerated pavement tester, wheel tracker and slap compactor which allows full-scale wheel tracking performance tests to be done in the laboratory for the first time.
“This will allow researchers to perform the same tests as a full-size Accelerated Pavement Tester but at a fraction of the cost required to buy and operate one,” says IPC Global marketing executive Craig Alexander.
The AUSTRACK (Asphalt Unbound Slab compactor and wheel TRACKer) replaces a previous version of the machine which used tyres up to 550mm diameter. This one, which has been totally re-designed and re-engineered, can accommodate full-size 1m-diameter wheels.
The AUSTRACK exceeds the specification for Extra-Large and Large wheel tracking to EN 12697-22 and for Extra-Large and Large roller compaction to EN 12697-33. It can perform full-scale wheel tracking tests on specimens 700, long, 500mm wide and up to 300 mm deep. Multi-layer unbound, chip sealed and asphalt pavement specimens can all be tested at temperatures up to 60°C.
A large-diameter pneumatic tyre – either 400mm, 550mm or 1000mm – performs the wheel tracking at loads up to 3 tonnes. The machine can be programmed to take a series of measurements at specified time intervals, allowing the AUSTRACK to run unmanned for long periods of time, according to IPC Global.
IPC Global’s IMACS controller Controls the application of axial loads of up to 30kN. And test, set-up, monitoring and analysis are all managed through the firm’s UTS software.
Italy’s
“Controls Group can now cover all the market segments in asphalt testing,” Di Iorio told World Highways. “We now have a complete range of static and dynamic products and testing solutions, from characterisation of bituminous mixes, production, quality control and quality assurance through to advanced materials research.”
IPC Global, said Di Iorio, has established its reputation in the high-end testing market over its 30-year life. As well as asphalt testing equipment, IPC Global manufactures machines for dynamic soil testing, structural testing and high-pressure triaxial rock testing.
“IPC’s capacity to innovate and design new equipment and be at the forefront of technology has created a reputation and a position identified in the highest end of the market,” he said, “So IPC is the researcher’s choice for advanced testing equipment for testing materials.”
Customers will benefit, said Di Iorio, because CONTROL’s manufacturing know-how will allow the same quality of IPC machines to be produced more cost-effectively.
“There is enormous synergy, especially in the industrial section of the group,” he said. “The advantage for IPC will be huge, due to the fact that it can produce a top quality product at a better cost and more efficiently. As a result, it will be more competitive, offering a better price for the customer.”
Di Iorio emphasised that IPC Global will remain an autonomous member of the Controls Group, with manufacturing continuing in Australia.
New machines at Asphaltica-Samoter 2014
Controls Group’s asphalt testing division PAVELAB SYSTEMS revealed some new machines at the
A new model of automatic closed-system analyser, the 75-PV50A05/S, which has more functions and a more ergonomic design than its predecessor, according to Controls will be on show. The analyser separates bitumen, filler and aggregates from asphalt samples in order to determine the composition of a mix.
The DUCTIMETER model 81-PV10C02 will also be unveiled at the exhibition. This testing machine determines the ductility of bituminous materials.
Controls Group has three brands covering asphalt testing, concrete and cement testing and soil testing: PAVELAB SYSTEMS, Controls and Wykeham Farrance, respectively. Its relationship with IPC Global began in 1994 when Controls purchased UK-based soil testing specialist Wykeham Farrance. At that time, IPC was supplying advanced soil testing equipment to Wykeham Farrance.
In 1995, Controls and IPC Global signed an agreement which saw Controls promote and distribute IPC’s dynamic testing equipment for roads around the world. However in 2010, this agreement stopped. Two years later, Controls Group launched it specialist asphalt testing division PAVELAB SYSTEMS, unveiling several dynamic testing schemes.
According to Di Iorio, very few products overlap between the two companies, meaning that technology transfer from IPC Global to Controls will be limited. “We cannot say in general that there will be transfer of technology. Controls, that mainly covers characterisation of materials, mix design, quality, production and so on, already has its own technology,” he said. “There are some areas, for example in dynamic testing in which IPC is at the forefront, but limited to this sector.”
When asked which IPC testing equipment Controls most admired, Di Iorio identified four technologies. The AMPT/SPT (Asphalt Mixture Performance Tester/Simple Performance Tester) which was developed to ‘democratise’ asphalt performance tests by allowing a range of tests on one machine.
“The AMPT is absolutely exclusive to IPC world-wide,” said Mr Di Iorio. IPC Global’s AMPT is the most popular AMPT on the market, by a ratio over 10:1 according to Controls, used in over 20 countries.
IPC Global’s SERVOPAC is “the most advanced research specification gyratory compactor available on the market,” according to Controls. With four digitally controlled servo-pneumatic actuators, it has the ability to adjust axial stress, gyratory angle and the rate of gyration.
Controls also identified IPC’s PReSBOX, an asphalt shearbox compactor which produces asphalt beams and cylinders, aimed to produce more homogenous specimens than those made by gyratory or roller compaction; and IPC’s software system, IMACS (Integrated Multi-Axis Control and Data Acquisition Software).
Matest
Meanwhile, Italian manufacturer
Sinadinos, who was CEO of IPC Global until 2012, is heading up Pavetest. Feeley, Pavetest’s technical director, was head of R&D at IPC Global.
“We develop the equipment together with the control system and the software here and then it will be value engineered by Matest and produced in Italy,” said Sinadinos , speaking to World Highways from Melbourne.
Pavetest will be offering a range of universal servo-pneumatic and servo-hydrualic testing machines and associated jigs and fixtures, said Sinadinos, as well as stand-alone machines such as the four-point bending device and the AMPT. Some machines were seen for the first time at Asphaltica-Samoter in Verona (see box). “There will be more systems down the track,” said Sinadinos.
This development is good news for the market, said Sinadinos. “The advantage for all customers is that there will be increased competition and a bigger choice. Hopefully it will drive innovation higher and prices lower. And everyone will have to lift their game in terms of service.”
One distinction between Matest’s existing equipment and its dynamic testing equipment will be the way data is captured, processed and displayed. “Matest has a fantastic system which is good for monotonic or low cycle testing, which is capable of recording 200 readings/second,” said Sinadinos. “The control and data acquisition system for the dynamic machines can sample 200,000 readings per second across 24 channels.
“That requires a huge investment in software that is capable of recording, displaying and analysing that volume of data.” Sinadinos and Feely have written the software.
Sinadinos agreed to join forces with Matest, which owns half of Pavetest, because he felt that there was a good cultural fit between the two companies. “I have always been impressed with the quality of their equipment,” he said. “And a lot of their distributors speak highly of them which is always an indication that they are ethical and good people to work with.”
IPC Global
IPC’s new AUSTRACK can take 1m-diameter tyres allowing full scale wheel-tracking in the lab]
IPC Global’s new AUSTRACK is an accelerated pavement tester, wheel tracker and slap compactor which allows full-scale wheel tracking performance tests to be done in the laboratory for the first time.
“This will allow researchers to perform the same tests as a full-size Accelerated Pavement Tester but at a fraction of the cost required to buy and operate one,” says IPC Global marketing executive Craig Alexander.
The AUSTRACK (Asphalt Unbound Slab compactor and wheel TRACKer) replaces a previous version of the machine which used tyres up to 550mm diameter. This one, which has been totally re-designed and re-engineered, can accommodate full-size 1m-diameter wheels.
The AUSTRACK exceeds the specification for Extra-Large and Large wheel tracking to EN 12697-22 and for Extra-Large and Large roller compaction to EN 12697-33. It can perform full-scale wheel tracking tests on specimens 700, long, 500mm wide and up to 300 mm deep. Multi-layer unbound, chip sealed and asphalt pavement specimens can all be tested at temperatures up to 60°C.
A large-diameter pneumatic tyre – either 400mm, 550mm or 1000mm – performs the wheel tracking at loads up to 3 tonnes. The machine can be programmed to take a series of measurements at specified time intervals, allowing the AUSTRACK to run unmanned for long periods of time, according to IPC Global.
IPC Global’s IMACS controller Controls the application of axial loads of up to 30kN. And test, set-up, monitoring and analysis are all managed through the firm’s UTS software.