The latest asphalt testing equipment brought onto the market is both innovative and highly accurate as Kristina Smith reports Advanced pavement design requires advanced test equipment. And advanced test equipment takes time and money to design, engineer and produce. But if your expensive testing machine could perform a few more tricks, buying one would make financial sense to more organisations. This is the thinking behind IPC Global’s new Uniaxial Fatigue Test Kit for its Asphalt Performance Mixer Tes
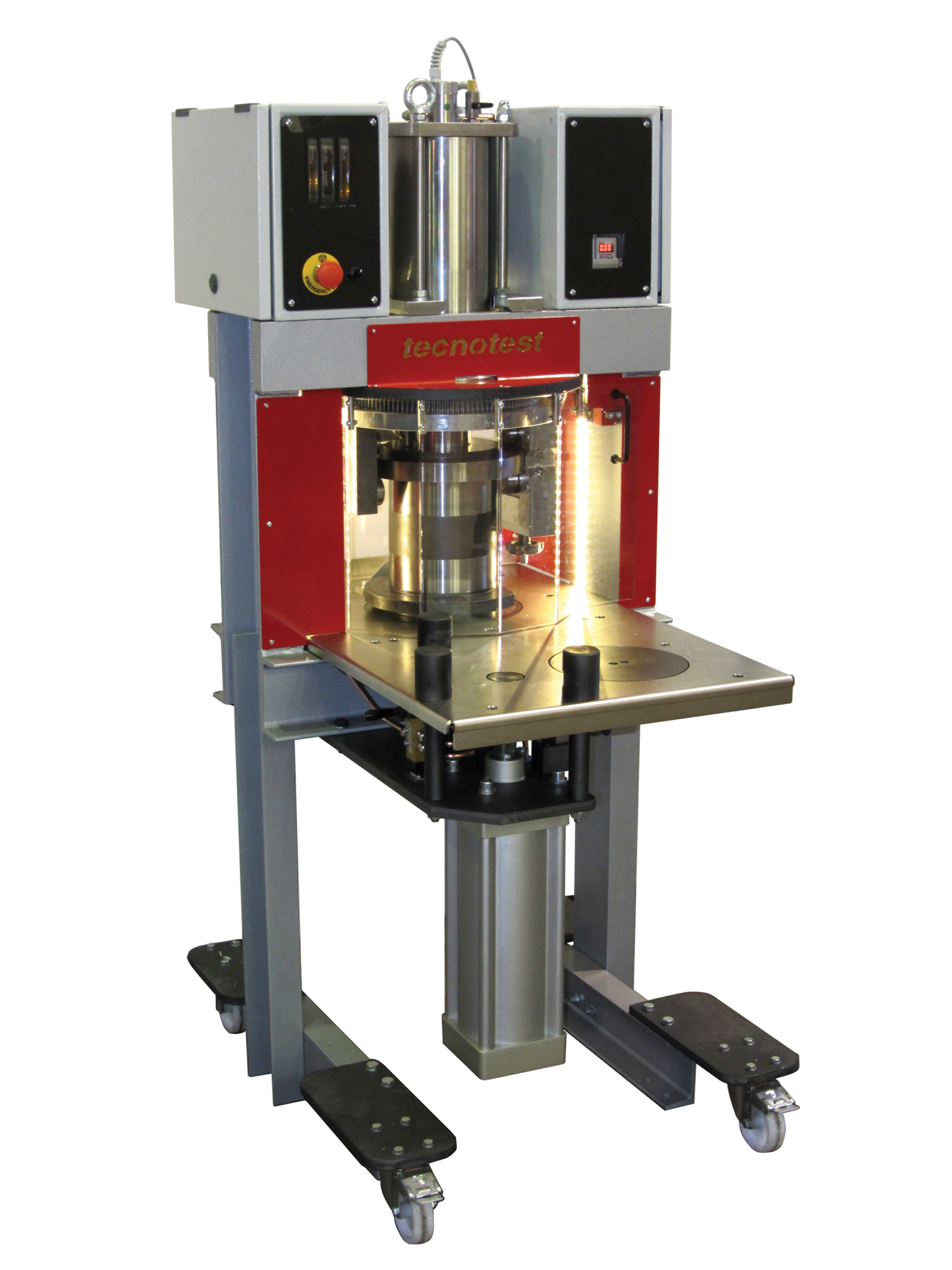
Tecnotest said that its new gyratory compactor is the first to be designed for ease of use with emulsified and foamed mix asphalts
The latest asphalt testing equipment brought onto the market is both innovative and highly accurate as Kristina Smith reports
Advanced pavement design requires advanced test equipment. And advanced test equipment takes time and money to design, engineer and produce. But if your expensive testing machine could perform a few more tricks, buying one would make financial sense to more organisations.This is the thinking behind
IPC Global has also developed for its AMPT an indirect tensile test jig and an overlay tester, the latter said to be able to determine the resistance of an asphalt overlay to cracking. Building on an original test developed by Texas Department of Transport, the overlay tester is attracting a lot of interest in the US, said IPC Global’s sales and marketing manager Kieran McGrane.
These additional tests, which increase the capability of the AMPT, are making sophisticated tests accessible to a much wider audience, said McGrane: “This is the democratising of very advanced tests. Previously such tests were the domain of research universities.”
The add-on tests are currently subject to an evaluation process in the US. Research is underway to work out how the tests can be performed so that they can eventually be written into standards. IPC Global’s approach is to get involved early in new tests. “We partner with the research community,” said McGrane. “They have an idea and they need someone to develop the equipment.”
AMPTs came out of the US’s Superpave (Superior Performing Asphalt Pavement System), which takes into consideration the properties of the asphalt binder, aggregate type, traffic loading and climate in mix design – rather than a more conventional recipe-type approach. They measure dynamic modulus (E*), flow number and flow time, properties that research in the US has shown correlate most closely with real-life pavement performance.
The specification for the AMPTs is demanding, identifying which elements are most important to the accuracy of the tests and setting performance goals accordingly. “AMPTs are not easy to produce,” said McGrane. “It has taken a lot of innovative design and engineering to produce the AMPT. It is something we are very proud of.”
IPC Global has sold over 100 AMPTs, many of which have gone to Departments of Transport in the US. IPC Global is the main supplier to the Federal Highway Administration (FHWA), according to McGrane.
However, interest in the machines is far wider. “Superpave is a US project, but the world is watching what is happening with it,” says McGrane. “We have supplied AMPTs to many countries outside the US.”
Controls Group’s latest development also comes in response to the performance-based design methods introduced by Superpave. The Italian group’s new range of DYNAPAVE dynamic machines conduct automatic cyclic tests on bitumen mixture specimens.
“The asphalt paving on a road is typically subject to cyclic stress due to the traffic, therefore it has to be subject to tests that simulate this stress and measure the effects it produces,” explained Andrea Morotti, Controls’ director of product and marketing. The test results guide the design of the pavement mixture to optimise its performance for that particular road.
Typical tests investigate strength and deformability in bending and indirect tension, rigidity in confined conditions, creep and permanent deformation properties.
“The DYNAPAVE range satisfies all these purposes,” said Morotti. “It generates dynamic stresses that simulate the real conditions of use and measures with high precision the behaviour of the sample.”
Compliant to US and European standards, there are three models in the DYNAPAVE range: a 15kN servo-pneumatic machine and two servo-hydraulic models, 30kN and the 130kN. The machines come with a climatic chamber so that the temperature can be varied to mimic the geographical area under consideration, with the DYNAPAVE 130 offering a temperature range between -40°C and -100°C.
The DYNAPAVE range comes with accessories so that it can be used to perform a wide range of other standard tests.
Controls expects its DYNAPAVE machines to have a market amongst public and private testing laboratories, contractors, asphalt producers and raw materials suppliers.
The DYNAPAVE 130 will be particularly useful for research purposes, says Morotti, as it can perform non-standard tests thanks to its higher maximum load, wider frequency range and extended temperature capabilities.
Meanwhile
What makes this test an attractive commercial proposition for Cooper is that Russia is likely to adopt it: “In Russia, the effect of studded tyres on roads is one of the biggest problems,” said Andrew Cooper, Cooper’s director of research.
“They are looking to incorporate EN 12697 [covering abrasion by studded tyres in Part 16] into their GOST standards.
The Prall Tester, said to be the first commercial machine of this type, will also find a market in Canada and North America, says Cooper.
It took six months for Cooper to improve on the original testing machine. One of the biggest changes was to transform it into a two-headed machine which, as well as doubling its capacity, means that the specimens being rotated at high frequencies counter-balance one another. This change is said to allow the machine to provide more reliable results.
Another recent development from Cooper aims to meet the demand created by the need to CE mark bitumen. The firm has updated Vialit’s cohesion tester, adding specially developed software that runs the tests and stores the results. “This fully automates the tests so that it takes out any element of user error or any fiddle factor,” said Cooper managing director Peter Grafton.
Designed to be user-friendly and intuitive, the Windows' software displays results for the binder under test across the pre-determined temperature range and displays them in real time, storing the results in a single
There is interest in the machine from labs globally, said Grafton.
The latest gyratory compactor from Matest can be used with standard or perforated moulds for tests on cold emulsified asphalts, and can be supplied with an automatic specimen extruder. The operator can choose whether to compact the mixture for a certain number of rotations, or until a target mixture density is reached, or until a selected height (measured by a linear transducer) is reached.
The machine has an integrated, full-colour, touch-screen control unit based on the Windows' operating system for managing and displaying test data. Test results can be saved onto a Universal Serial Bus (USB). This is said by Metest to give the machine an effectively unlimited memory, said the manufacturer, avoiding problems relating to the maximum capacity of internal memory.
The operator can communicate remotely with Matest technical staff for immediate help with any problems or for software updates, using a direct connection to the Internet or an intranet. Matest has extended the warranty period on this machine from 12 months to two years.
Existing gyratory compactors, because they were designed for hot mix asphalt samples, can be damaged when they are used to test mixes with higher liquid content, as the liquid squeezed out during compression can damage some of the machine’s components. This means that additional precautions are needed to protect the machine.
“This is the first machine optimised for emulsified asphalts and foamed asphalt mixes,” said Pierpaolo Viola, a Research and Design (R&D) engineer for Tecnotest. “These materials are getting more and more important for recycling reasons.”
Where other machines have some or all of their electrical, electronic and mechanical components underneath the worktop, Tecnotest said that it has moved all the critical elements above the test chamber.
Compliant with both US and European standards, Tecnotest’s gyratory compactor is said to be easily switchable from one configuration to the other, as the angle of gyration is set by simply turning a knob. The American test method requires an external angle gyration of 1.25°, and an internal angle gyration of 1.16°, whereas the European test method requires an internal angle gyration of 0.82°. “This switching feature is not easy or even impossible on other machines,” said Viola.
The machine can be linked to a customer’s PC or can be supplied complete with PC and installed software.