The project to upgrade Kassel-Calden Airport in Germany is providing a much improved facility. Opened in 1970, the original airport had a short runway that was not suited to predicted traffic volumes and current standards so a complete reconstruction of the facility has been carried out. The €271 million investment in the facility is expected by the developers to provide a strong economic benefit to the area.
The original airport was built on an area of over 200ha and a new and longer runway has been con
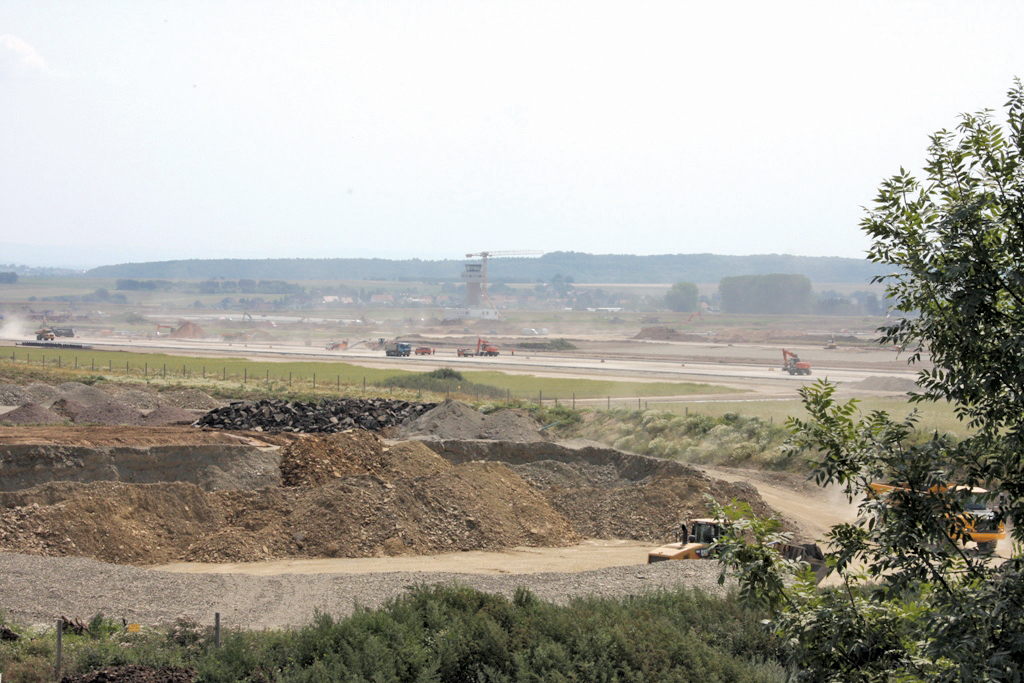
Kassel-Calden Airport is benefiting from a newly repaved runway that is 2,500m long
The project to upgrade Kassel-Calden Airport in Germany is providing a much improved facility. Opened in 1970, the original airport had a short runway that was not suited to predicted traffic volumes and current standards so a complete reconstruction of the facility has been carried out. The €271 million investment in the facility is expected by the developers to provide a strong economic benefit to the area.
The original airport was built on an area of over 200ha and a new and longer runway has been constructed next to the existing 1.5km long by 30m wide runway so as to help expand capacity. This new runway is 2.5km long by 45m wide, with over 250,000m² of asphalt having to be paved in a very short time frame, so as to minimise flight delays.Contractor MKW has handled asphalt production as well as paving for this huge project and because of its specific needs, the firm approached
The work called for the production of some 200,000tonnes of high quality asphalt, and in a tight time frame to match the demanding construction schedule. In addition, the contractor wanted to be able to move the asphalt plant after the airport work was complete. The firm opted for a Benninghoven Mix Mobile MBA300+ mobile plant and the two companies then began discussing the specifications for this equipment. The Mix Mobile MBA300+ has an output of 240tonnes/hour and can deliver the volumes of asphalt required, as well as the quality of material. However the contractor was keen to minimise the cost of the fuel also by using pulverised brown coal dust and this had not been previously used in a mobile plant
The asphalt plant was installed in a quarry belonging to Transkal, and within a few days most of the plant components had been installed into position or were partly erected. The plant features a five bin cold feed unit and fived deck screens, as well as a 30tonne hot aggregate bin to provide a sufficient flow of material.
The airport paving contract also called for the use of recycled asphalt pavement (RAP) so as to lower material costs and also meet carbon reduction targets, which called for the plant’s dryer to be fitted with a middle ring feed system. The patented Benninghoven dosing system was also selected. All of the generated coarse filler from the filter is brought onto the RAP material in order to cover it, addressing problems of stickiness and also reducing emissions.
A fleet of