In Germany a high production paving operation has been achieved using the largest machine available on the market. This project is all the more notable as the operation has been carried out in a continuous process, without joints. The Vögele SUPER 3000-2 paver was able to advance continuously at a rate of almost 4m/min. The machine was preceded by a bustle of activity, for no fewer than 24 feed lorries were needed to ensure an uninterrupted supply of mix to the paver, which placed an even asphalt surfacing
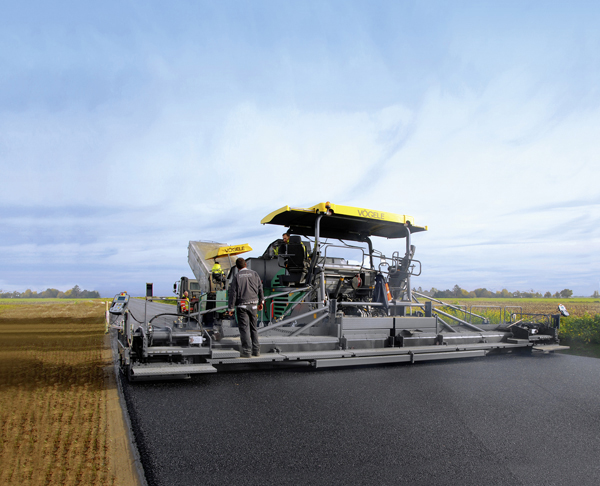
The huge Vogele Super 3000-2 machine was used to pave a mat 12m wide continuously without joints
In Germany a high production paving operation has been achieved using the largest machine available on the market.
This project is all the more notable as the operation has been carried out in a continuous process, without joints.The
The paver was complemented by a MT1000 Mobile Feeder, an arrangement strongly recommended by the manufacturer when working with the SUPER 3000-2 due to the quanities of feed required Since the feeder stocks a sufficient quantity of mix, paving can continue for several hours without a break even when feed lorries only deliver fresh material intermittently. In Selfkant, the paver remained in operation for many hours before stopping for the first time. The feeder has added benefits as the mechanical separation between paver and feeder ensures that the mix is transferred smoothly, as well as providing a more homogenous thermal gradient for the mat.
Frauenrath had to achieve efficient logistics with regard to material supply. The job site was served by 24 feed lorries with a turnaround time of one hour and the firm signed a contractual agreement with the asphalt mixing plant ensuring that the asphalt could be delivered without a break.
Two service technicians from the
The SUPER 3000-2 was in action in Selfkant for two days. During this time, colleagues from Frauenrath, members of staff from nearby construction firms and specialists from the highways authority all took the chance to see the paver, the largest on the market at present, in action.