Material transfer vehicles and remixing systems are crucial to delivering quality paving. Using material transfer vehicles (MTVs) can play a major role in delivering high quality road surfaces. These units can help boost quality by minimising the risk of material or thermal segregation. A major road paving project has been carried out in Germany using innovative paving methods. For the first time ever, binder and surface courses were paved over a width of 15.5m. This paving job was carried out on a 4.2km st
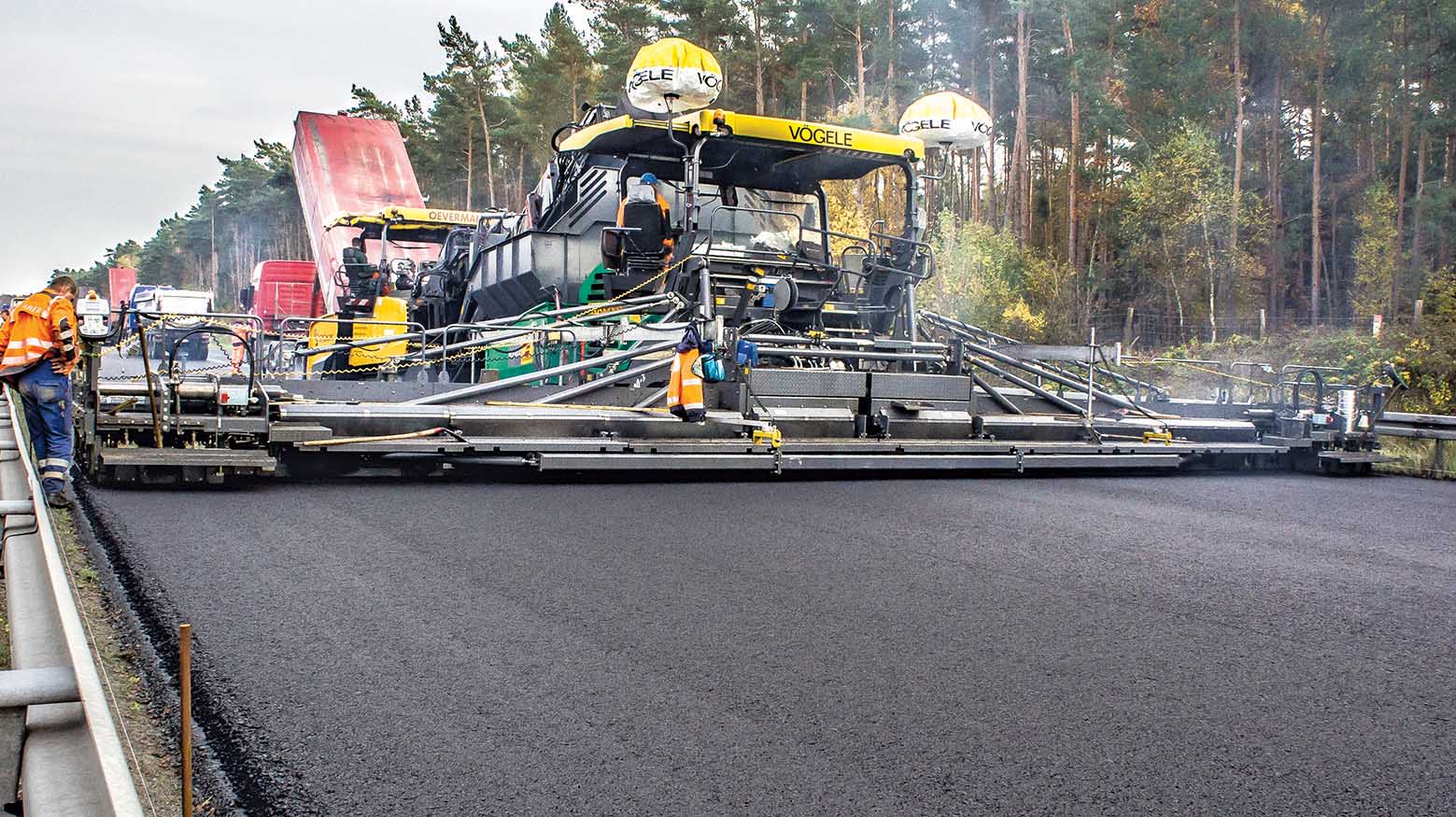
The massive Vögele paver was able to lay a mat 15.5m wide across the entire carriageway of the A10 Autobahn, without need for any joints
Material transfer vehicles and remixing systems are crucial to delivering quality paving
Using material transfer vehicles (MTVs) can play a major role in delivering high quality road surfaces. These units can help boost quality by minimising the risk of material or thermal segregation.
A major road paving project has been carried out in Germany using innovative paving methods. For the first time ever, binder and surface courses were paved over a width of 15.5m. This paving job was carried out on a 4.2km stretch of the busy A10 Autobahn ring road around Germany’s capital Berlin.
The tenders were called for by the German Federal Ministry of Transport, which specified jointless paving over the full 15.5m road width so eliminating potential problems of freeze thaw cracking originating from the joints, a major cause of early road surface failure. The aims of the project were to prove that high paving quality can be achieved over large widths and show that the temperature of the asphalt mix could be maintained from the asphalt plant to paving work.
The project represents something of a precedent for Germany following the introduction of new asphalt paving regulations for 2015. Thermally insulated dump boxes are now mandatory in Germany when transporting asphalt by truck. The asphalt now has to feature a uniform temperature, without cold spots forming in corners, bends or along the sides of the tipper truck body. A separate requirement that came into effect in January 2015 covers the use of material feeders for building or rehabilitating federal trunk roads. This applies to projects involving the paving of 18,000m² or more of road surface.
Laying a jointless pavement 15.5m wide called for large equipment so WMH Werwie Maschinen-Handels supplied a1194 Vögele SUPER 3000-2, able to pave widths up to 16m wide and 500mm deep. This features a 24tonne hopper capacity and maximum throughput of 1,600tonnes/hour, and was equipped with an SB 300 fixed-width screed for the job. The TP1 version of this screed was used, featuring a tamper and a pressure bar, so as to deliver the necessary high compaction.
In order to deliver a constant feed, another firm, Oevermann, provided a Vögele MT 3000-2i material transfer vehicle (MTV) with a 45tonne mix capacity, equipped with an offset conveyor and able to provide 1,200tonnes of mix/hour. By using this equipment the paving crew could ensure that the paver was continuously supplied with asphalt, allowing work to continue without needing to halt the paver.
A reliable sensor-based distance control was also important so as to prevent the MTV from touching the paver during the job, as this could have caused problems with the mat. The Vögele MTV is equipped with three laser sensors located on the underneath of the pivoting conveyor. This ensures that the distance between material feeder and paver remains constant even when one or more sensors are blocked. The sensors also allow the machine operator to concentrate on transferring the mix.
As with most large paving contracts, the paver was guided using automated steering, with a sonic system following a stringline installed along the safety barrier to ensure the machine followed the necessary path. This allowed the paver operator to focus on the paving operation. For the job, the SB 300 fixed-width screed was configured for its maximum width, while additional versatility was provided by hydraulic extensions fitted on the right- and left-hand sides, each capable of being extended by 750mm. The screed had the Vögele TP1 system to help optimise compaction, while it also featured effective heating across the full screed width.
This was the first time that such a wide mat had been paved using a high compaction screed system. Before paving was complete, thermal imaging showed an even and homogenous temperature of the mat over its full 15.5m width, without any segregation.
This project has shown that high quality pavements can be paved to large widths, without the need for joints. The work also shows that such operations can deliver homogeneous, resilient and durable road surfaces.
Using material transfer vehicles (MTVs) can play a major role in delivering high quality road surfaces. These units can help boost quality by minimising the risk of material or thermal segregation.
A major road paving project has been carried out in Germany using innovative paving methods. For the first time ever, binder and surface courses were paved over a width of 15.5m. This paving job was carried out on a 4.2km stretch of the busy A10 Autobahn ring road around Germany’s capital Berlin.
The tenders were called for by the German Federal Ministry of Transport, which specified jointless paving over the full 15.5m road width so eliminating potential problems of freeze thaw cracking originating from the joints, a major cause of early road surface failure. The aims of the project were to prove that high paving quality can be achieved over large widths and show that the temperature of the asphalt mix could be maintained from the asphalt plant to paving work.
The project represents something of a precedent for Germany following the introduction of new asphalt paving regulations for 2015. Thermally insulated dump boxes are now mandatory in Germany when transporting asphalt by truck. The asphalt now has to feature a uniform temperature, without cold spots forming in corners, bends or along the sides of the tipper truck body. A separate requirement that came into effect in January 2015 covers the use of material feeders for building or rehabilitating federal trunk roads. This applies to projects involving the paving of 18,000m² or more of road surface.
Laying a jointless pavement 15.5m wide called for large equipment so WMH Werwie Maschinen-Handels supplied a
In order to deliver a constant feed, another firm, Oevermann, provided a Vögele MT 3000-2i material transfer vehicle (MTV) with a 45tonne mix capacity, equipped with an offset conveyor and able to provide 1,200tonnes of mix/hour. By using this equipment the paving crew could ensure that the paver was continuously supplied with asphalt, allowing work to continue without needing to halt the paver.
A reliable sensor-based distance control was also important so as to prevent the MTV from touching the paver during the job, as this could have caused problems with the mat. The Vögele MTV is equipped with three laser sensors located on the underneath of the pivoting conveyor. This ensures that the distance between material feeder and paver remains constant even when one or more sensors are blocked. The sensors also allow the machine operator to concentrate on transferring the mix.
As with most large paving contracts, the paver was guided using automated steering, with a sonic system following a stringline installed along the safety barrier to ensure the machine followed the necessary path. This allowed the paver operator to focus on the paving operation. For the job, the SB 300 fixed-width screed was configured for its maximum width, while additional versatility was provided by hydraulic extensions fitted on the right- and left-hand sides, each capable of being extended by 750mm. The screed had the Vögele TP1 system to help optimise compaction, while it also featured effective heating across the full screed width.
This was the first time that such a wide mat had been paved using a high compaction screed system. Before paving was complete, thermal imaging showed an even and homogenous temperature of the mat over its full 15.5m width, without any segregation.
This project has shown that high quality pavements can be paved to large widths, without the need for joints. The work also shows that such operations can deliver homogeneous, resilient and durable road surfaces.