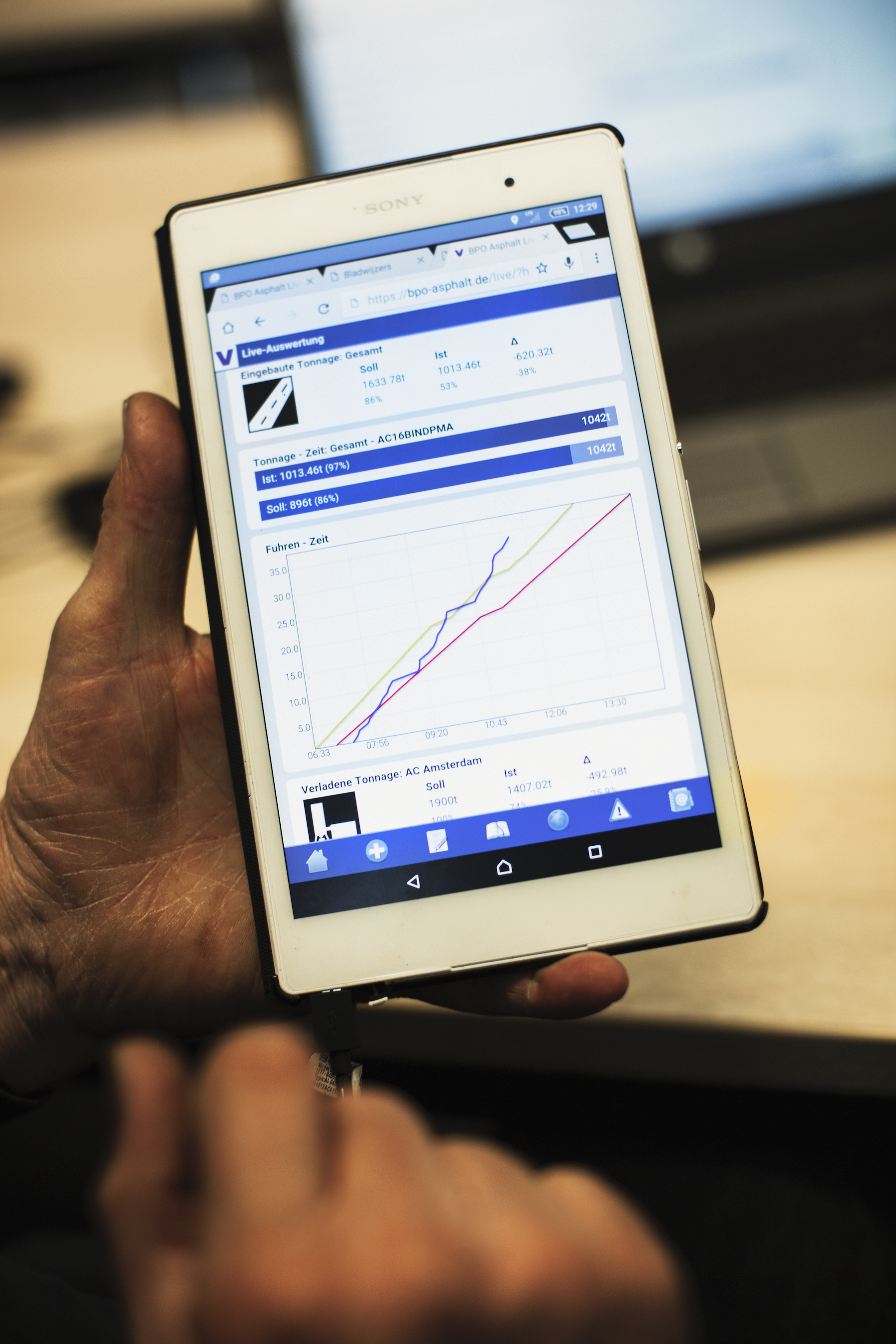
A damp and foggy morning at Amsterdam’s Schiphol Airport in the Netherlands. Some of the five runways are in normal use, but one of them shows a different kind of activity.
At a slow but steady pace, a small army of bright yellow machines is repaving the surface. The project is being carried out by
The seven-week refurbishing the runway includes stripping the top layer, resurfacing the entire length with asphalt and reinstalling gutters and runway lighting.
Heijmans is a listed company that was established in 1923 and operates primarily in the Netherlands, Belgium and Germany. The company has more than 6,500 employees and had revenue of €2 billion last year. Its road division’s fleet of pavers, road rollers and other equipment is around 40%
“Since 2010 we have constantly been upgrading aspects of our business,” says Peter van Hinthem, innovation manager for roads at Heijmans. “In 2014 we finalised a navigation system for road rollers. Next we turned our attention to the logistics chain.”
He and his team went searching for any available resource management systems and they found three candidates. One of those was a software solution called BPO - Building Process Optimisation- that has been developed by the German company
BPO delivers a comprehensive solution for planning projects, allocating resources, calculating material requirements, following up on projects in real time, monitoring truck locations, communicating and handling and change management. It also generates reports for later reference.
The system is web-based, meaning it can be run on tablet PCs, iPads and smartphones. BPO creates a totally transparent platform by which supervisors on site, drivers of asphalt delivery trucks and staff at the asphalt plant are constantly kept informed about the progress of the work. They can communicate with one another and make last-minute adjustments.
BPO takes its cues from sensors on the road-paving equipment and from GPS receivers on the delivery trucks. This enables close monitoring of logistics and of quantities used, which in turn facilitates just-in-time delivery of asphalt on site.
As van Hinthem explains, this is a crucial advantage of the program. “The asphalt leaves the mill at a temperature of over 150°C. For a smooth operation, it is essential to process it as hot as possible. If the asphalt cools down to below 80°C, it becomes useless. So waiting time on site should be kept to a minimum. And since the sensors tell you exactly in real time how much asphalt is being used, you can make on-the-spot adjustments of the amounts ordered, so the delivery of expensive surplus quantities can be avoided.”
Because
Atlas Copco road construction equipment works well with BPO and if required it can be delivered with all the necessary sensors, including a server-to-server connection from Atlas Copco’s FleetLink fleet management system.
Heijmans has been testing BPO for several weeks. “Since 20 years’ warranty on pavement is not uncommon any more, it is getting essential to be able to trace the origins of any given patch of asphalt,” says van Hinthem. “Moreover, quality is more important than ever, since construction contractors will nowadays be fined for any traffic jam caused by extra repair work made necessary because of a flawed job.”