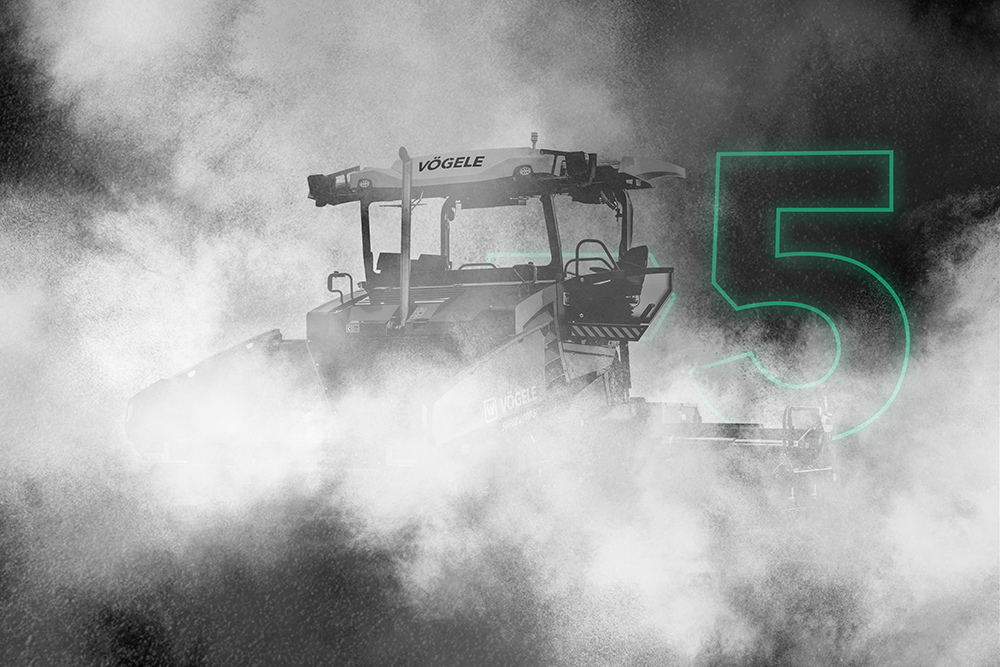
Asphalt paving machines have improved considerably in recent years. Manufacturers have made their equipment more efficient and more productive, as well as boosting the finish quality of the mat being paved. Powered by the latest generation engines, new pavers are more fuel-efficient and more productive, while producing lower levels of emissions. Visibility over the hopper and screed have been improved, while control stations have become more ergonomic. The use of systems to draw asphalt fumes away from the screed and hopper and vent these through high-placed exhaust systems have made the machines more pleasant to work on for long periods, in addition to the quieter and smoother operation.
Machine control technology is now available from all the main players in this segment, allowing contractors to include the paver as part of the BIM process. Design models can be used as the basis for operating programs for the pavers, ensuring an accurate outcome. Software can also integrate the paver into the material logistics and supply chain, with asphalt quality assured and tracked from the plant, through delivery by truck until it arrives at the paver. The machine control technology can be used to monitor compaction at the screed as well as monitoring the thermal profile of the mat. Using material transfer vehicles can also help to ensure both material and heat segregation is virtually eliminated from the mat.
For the road user this means that road surfaces will last longer and suffer fewer potholes, while providing smoother surfaces that are more comfortable to drive on.
There are key differences in the types of pavers contractors buy, however.The global market for asphalt pavers favours the European style machines, featuring tamper bar type screeds. These offer higher compaction levels than the vibration only screeds fitted to US-style pavers. But the US-style machines typically offer much higher levels of productivity than European pavers.
Globally, the European-style machines dominate and it is of note that Chinese manufacturers also chose to develop asphalt pavers featuring tamper bar screeds. But US-style machines are also used across Latin America, as well as in Australia.
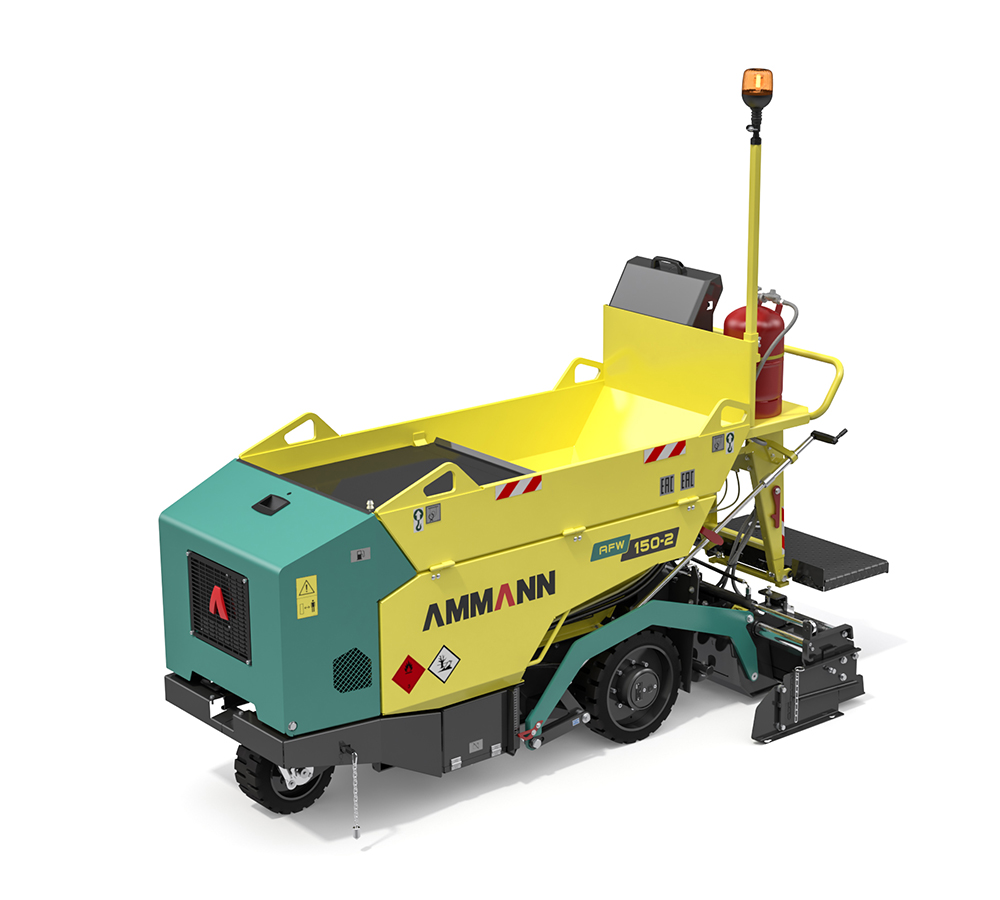
The World of Asphalt exhibition earlier this year was held in Nashville and the new pavers being launched were US-style machines with vibration screeds. But the upcoming bauma exhibition in Munich, Germany will understandably see new tamper bar type pavers coming to market.
Many of the firms are still keeping quiet over what they will unveil, but Ammann, Bomag, Caterpillar, Dynapac, Sumitomo and Vögele are amongst the paver manufacturers exhibiting at the event. Chinese manufacturers will also be present at the event, although they have focussed on cranes, concrete equipment or earthmoving machines for the European market in the past, keeping their road machinery for the home or emergent markets.
One firm that has announced new highway class pavers is Vögele. The firm is offering two improved asphalt pavers for the highway class in the shape of its new SUPER 1900-5(i) and SUPER 2100-5(i) models. These are the first pavers in the firm’s latest Dash 5 generation and are benefit from having the latest-generation AB 500 and
AB 600 Extending Screeds. A quality finish and high productivity are said to be key features of the new screeds, along with durability and reliability.
The firm says that its new pavers benefit from the latest technology so as to meet the increasing need for digitalisation in construction. The units can use the latest machine control systems and process optimisation tools from the Wirtgen Group, as well as from the main suppliers of machine control technology. Flexible, modular systems are featured that meet needs for process automation and sustainability, as well as user-friendliness and economy.
According to Vögele, user requirements have been a key focus during the development of these machines, making the pavers easier to operate. Improved control systems but with familiar layouts are used as with other equipment from the Wirtgen group. This reduces the amount of training required for paving crews that have used earlier generation construction machines from the company. For the paving crew, the familiar control layouts allow easier machine handling, maximum operating convenience and safety on the job site.
Reduced setup times, improved logistics and greater machine availability are said to deliver ensure fuel economy and reduce material wastage, helping address increasing fuel and materials costs. New automation and control technology provides operator assistance and has been optimised to prevent errors and to increase efficiency and paving quality according to Vögele.
The machines are equipped with the latest generation engines that meet the Stage V emissions requirements. At the same time, the new engines powering the Dash 5 pavers offer lower noise emissions and better fuel consumption, while maintaining the same performance helps meet sustainability targets for contractors.
Compact machines
Improvements in asphalt paving technology are by no means restricted to the top end of the market for highway class machines. Contractors are increasingly switching to the use of compact pavers for tasks such as reinstatement for utilities works, paving pedestrian walkways and cycle lanes and also in between tram lines.
The traditional method of laying asphalt by hand for reinstatement work for example often results in a sub-standard finish, with uneven surfaces. Heavy traffic causes uneven asphalt surfaces to fail and unless the edges have been properly sealed, potholes can develop in a comparatively short time.
Using mini pavers however ensures that reinstatement works can be carried out more quickly, as well as allowing much better surface quality that is less likely to fail. The mini pavers are compact and versatile and can achieve high utilisation for contractors as they can also be used for installing high pedestrian walkways or cycle lanes.
One of the key machines for this compact paver market is the Ammann AFW 150-2 Mini Paver, which the firm claims continues to grow in popularity.
The AFW 150-2 is able to pave extremely narrow widths, from 250mm up to 1650mm. According to Ammann, it can produce a mat that has the appearance and quality of asphalt placed by a large paver. The firm emphasises that its machine offers a significant upgrade over manual paving in terms of labour.
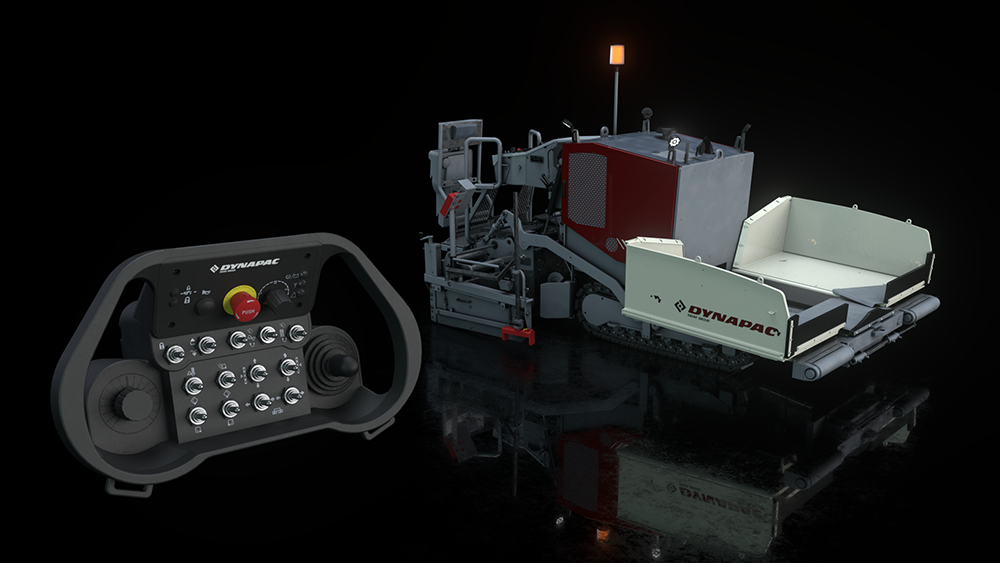
Meanwhile, Dynapac is now offering the RC360 remote control unit as a customer option along with its well proven F1250CS compact paver. According to Dynapac, the F1250CS delivers the best-in-class screed quality and now can offer additional versatility for customers when supplied with the optional RC360 remote unit. Small, yet powerful, the Dynapac F1250CS suits use where high-quality paving is required with widths of 500mm to 3.5m. The remote unit allows the user to stand in a position affording the best view of the working area and also of the screed, helping optimise quality.
The F1250CS has a high-quality screed that is offered with the choice of gas as well as electric heating. Dynapac claims that the V2400 delivers the same quality and performance as its larger stablemates and this screed has an extension box allowing greater paving widths. As an added benefit, the Dynapac F1250CS can pave below the zero point, increasing refurbishment job efficiency. This means that the paver can drive out of the milling cut, allowing the screed to pave a smooth finish.
Multiple adjustments are available such as for angle of attack while the deep bottom plates help to deliver high pre-compaction and a smooth surface, even with thick layers. The quick coupling means setup and operation are easy to use. The RC360 remote unit improves safety and also allows operators to control the paver from a point that offers the lowest asphalt fumes while providing maximum visibility and results. The remote unit is supplied with a case and charging devices, as well as a mechanical connector for external supply.
Ensuring safety during remote operations is important so when the operator is more than 10m from the paver, the machine will stop automatically. The paver will also stop automatically should the remote be tilted at higher than a 45° angle.
Power for the F1250C comes from a 54kW Deutz engine and this is available in either Tier 3/Stage III or Tier 4/Stage V versions to suit local emissions requirements.