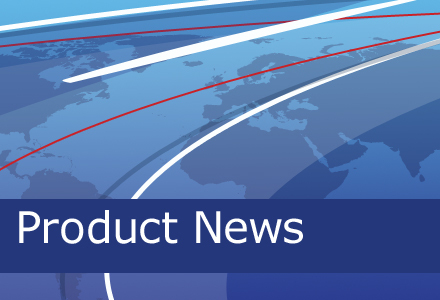
In Japan the latest machine control technologies are being used to help with earthquake reconstruction.
Three years after the major earthquake that devastated Miyagi Prefecture on Japan’s main island of Honshu, the clean-up and reconstruction work is far from complete. In addition to rebuilding infrastructure and buildings, the Japanese Government has had to build a series of major improvements to flood protection.
~
To help speed the rebuilding, sophisticated machine control systems were fitted to the earthmoving machines. Contractor Shimizu installed
First, the 3D model of the planned dyke, which had been previously created in the office, was transferred to the Xsite PRO system. This model provided the task specification for the excavator operator, along with the respective incline angle and depth specifications. Each work step had to be precisely recorded and represented on the display. Using sensors mounted on the boom, arm, bucket and chassis, the system was able to register the position of the bucket at all times. The machine position and orientation were determined by means of GNSS. The display showed the values in the terrain model, so the excavator operators could recognise when the desired incline angle and depth had been attained and where further material needed to be moved. This allowed the dyke to be built precisely according to the model.
According to the contractor, this resulted in time savings of 15%. Meanwhile there was no need to place stakes on the site, further reducing the time and expense of the job, while it was also possible to avoid having to hire two surveyors for the task of surveying.