Manufacturers of excavators and wheeled loaders continue to roll out new models aimed at specific markets - Mike Woof writes
With tough emissions controls now in place in Europe and North America, manufacturers have developed an array of advanced solutions to meet requirements, while also developing parallel models for sale in other territories. In the earthmoving sector the latest round of requirements in Europe and North America has resulted in a flurry of new, low emission models equipped with Tier 4
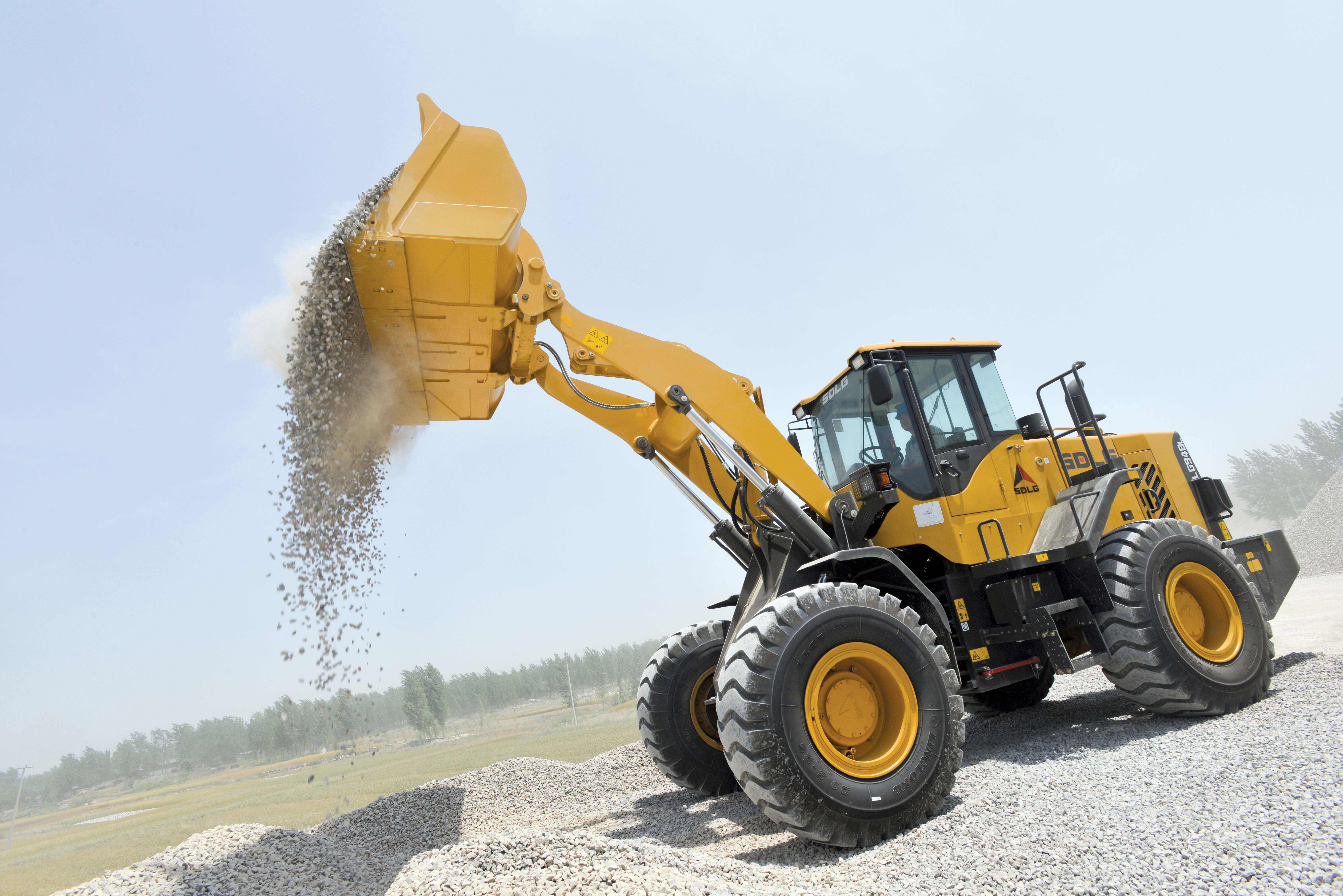
SDLG now has a special mid-range wheeled loader model developed for the North American market
Manufacturers of excavators and wheeled loaders continue to roll out new models aimed at specific markets - Mike Woof writes
With tough emissions controls now in place in Europe and North America, manufacturers have developed an array of advanced solutions to meet requirements, while also developing parallel models for sale in other territories. In the earthmoving sector the latest round of requirements in Europe and North America has resulted in a flurry of new, low emission models equipped with Tier 4 Final/Stage IV compliant diesels coming to market from the major European, Japanese, Korean and US firms. A number of leading Chinese manufacturers have also entered this market too with export models featuring the necessary low emission engines that are aimed specifically at Europe and North America, with the overall market becoming even more competitive than before.
A number of sophisticated emissions technologies have been used to meet the market requirements of the earthmoving sector, while manufacturers have also managed to achieve performance improvements by boosting power and torque, while simultaneously lowering fuel consumption. Because of the increased cost of the advanced engine technologies, manufacturers have been keen to try and lower ownership costs by cutting fuel consumption and extending service intervals.
However these low emission engines are also limited to being used in countries where high quality, low sulphur fuels are available. For emergent markets this has resulted in manufacturers developing entirely different model ranges. While basic designs may be similar, specifications and equipment are entirely different from models sold into Europe and North America resulting in very different products. These models have been developed with a combination of technologies, retaining some of the advanced electronics and hydraulics, but opting for engines capable of coping with lower fuel qualities and which meet the Tier 2 or Tier 3 emissions requirements.178 Caterpillar and 359 Volvo CE have been amongst the most active of the major manufacturers in this regard. Caterpillar has developed specific models for emergent markets only, while developing and manufacturing them in its Chinese operations. Meanwhile Volvo CE has developed its Chinese-made 5316 SDLG range as a lower cost brand that appeals particularly strongly to customers in emergent markets, though these models are also now being sold with the necessary emissions controls for developed markets.
Stability is optimised by a track length of 5.36m and a 3.34m track width (fitted with standard 600mm track shoes). The life of tracks and pin/bushings is said to be long and the chains are greased and sealed to reduce travel noise and to reduce operating costs. The machine is available with a 6.9m reach boom and a 3.35m reach stick. Meanwhile the 6.55m mass excavation boom is offered with a 2.55m mass stick for Africa, Middle East and CIS and a 3m mass stick for Turkey. The 349D2 L features a large cab with high visibility and ROPS for the Turkish market.
Sharing similar features, the 40.3tonne Cat 340D2 L replaces the earlier 340D L but benefits from a more refined hydraulic system and a fuel-efficient Cat C9 engine that meets Tier 2/Stage II, and China Tier 2 emissions requirements. The engine delivers 200kW and also offers a fuel saving of 7%, benefiting from sensors that respond to light load conditions. Fuel filtration allows the machine to be operated in areas where fuel quality is suspect while high power hydraulics optimise performance.
The standard machine features a 6.5m heavy duty front linkage designed for versatility, combining high productivity with adaptability. A mass excavation version of the machine is also available with a 6.18m boom, an 8.45tonne counterweight and bucket sizes of 2.6-2.69m3. Heavy duty undercarriage ensures long life in tough operating conditions. Other features include the firm’s advanced LINK telematics system, which helps fleet owners manage productivity and lower owning and operating costs through the online VisionLink interface. Users can track parameters such as location, hours, fuel usage, diagnostic codes, and idle time.
255 JCB however has developed its new JS300 for the European and North American markets, with the necessary low emission diesel. The 30tonne class excavator replaces the firm’s earlier JS290 model and offers increased power and productivity at the same time as cutting fuel consumption by 4%. Power comes from a six-cylinder 2724 Isuzu diesel rated at 161kW, which meets Tier 4 Interim/EU Stage IIIB standards. The engine drives twin variable displacement pumps, with control from a sophisticated hydraulic management system. This automatically adjusts the working mode as the operator increases engine speed.
The machine retains its high breakout and lifting forces, and with a 2.5m dipper arm and a standard 6.2m monoboom it delivers a bucket digging force of up to 253.6kN. The excavator is also equipped with a new tipping link geometry that provides increased vertical wall digging depth. The machine has the firm’s latest cab structure, with increased soundproofing and better structural rigidity, while a single control allows for selection of the various power modes. The firm’s LiveLink telematic system has been upgraded, offering fleet owners remote access to fuel consumption and operating data for the machine. In addition the LiveLink ECU can be matched with the engine’s ECU, preventing tracking the machine from being started if necessary and adding to security.
2300 Komatsu Europe is now introducing the firm’s highly sophisticated PC210LCi-10 excavator into the European market. This machine is equipped with in-built machine control technology that is said to help boost performance, productivity and efficiency. The machine control and guidance package is fully integrated with the excavator’s other systems and can be used for a variety of tasks from rough digging to finish grading, improving efficiency, precision and safety. A novel feature is the automatic limit that prevents the operator from digging beyond the target surface. The status is displayed on the colour monitor, which features a facing angle compass, a light bar and audio guidance, providing real-time as-built status, a magnified fine grading view or a 3D aerial view.
The PC210LCi-10 weighs from 22.6-23.5tonnes depending on the configuration, with power from a diesel rated at 123kW. The machine also has latest KOMTRAX telematics technology, which delivers operating information to a secure website using wireless technology. Data such as operating hours, fuel consumption, location, cautions and maintenance alerts can be relayed to the web application for analysis. The fleet monitoring system can be used to boost machine availability as it allows remote diagnosis. The machine also comes with the Komatsu CARE maintenance programme, offered as standard for the first three years or 2,000 hours for every Tier 4 Interim/Stage IIIB and Tier 4 Final/Stage IV machine.
233 Hitachi Construction Machinery Europe (HCME) has introduced the ZW140-5 and ZW150-5, two productive wheeled loaders featuring reduced fuel costs combined with powerful engines. The 11tonne class ZW140-5 and 12tonne class ZW150-5 wheel loaders wield buckets of 1.5-2.1m3 and 1.9-2.3m3 respectively and use significantly less fuel than previous models, while maintaining the same high levels of performance and productivity. The 5.2litre engine delivers 113kW for effective bucket filling and travel speeds while also delivering good fuel consumption. The fuel economy is further improved due to the firm’s HST system, which makes the machines more economical when moving and digging into the pile, as well as from the auto engine shutdown. The HST system allows the machines to operate in two different modes for regular operations on level terrain or where power is needed for greater traction in heavy-duty excavation. In addition a traction control system prevents tyre slippage where underfoot conditions are poor, further improving fuel consumption as well as reducing tyre wear.
Komatsu Europe is also offering the WA100M-7 compact wheeled loader, which is driven by a 66kW Komatsu SAA4D95LE-6 engine that is Stage IIIB/Tier 4 Interim certified. The 7tonne machine offers a 10% fuel saving over the model being replaced, while it features improved operator comfort and visibility. Suited to tough construction applications, the WA100M-7 delivers high torque at low rpm, and has high rimpull, driving through a fully automatic, hydrostatic transmission to all four wheels. A 100% differential lock can be fitted to the two LSD axles as an option.
Other features include the latest KOMTRAX telematics technology, providing operating information through a secure website to the fleet manager for analysis. Highly versatile, the machine has a hydraulic quick-coupler and a delta boom and also features the firm’s easy fork configuration for high breakout force and parallel movement during forklift applications.
Finally SDLG is now launching a new model wheel loader in North America – the SDLG LG948L. This new loader lies in a key capacity class for the region, with its 2.35m³ bucket capacity, as some 62% of new wheel loaders purchased in North America are in the 1.96m³ to 2.75m³ range.
This model has been introduced following customer demand for a machine with a capacity in between the existing 1.88m3 LG938L and the 3.13m3 LG959. As with other SDLG models, the LG948L is aimed at wheeled loader customers that do not require the features seen on premium-priced machines but which need a productive and durable machine with good quality. Power for the 13.7tonne machine comes from a201 Deutz diesel rated at 129kW and which meets Tier 4 Interim emissions requirements and which drives through a proven 2304 ZF transmission.
With tough emissions controls now in place in Europe and North America, manufacturers have developed an array of advanced solutions to meet requirements, while also developing parallel models for sale in other territories. In the earthmoving sector the latest round of requirements in Europe and North America has resulted in a flurry of new, low emission models equipped with Tier 4 Final/Stage IV compliant diesels coming to market from the major European, Japanese, Korean and US firms. A number of leading Chinese manufacturers have also entered this market too with export models featuring the necessary low emission engines that are aimed specifically at Europe and North America, with the overall market becoming even more competitive than before.
A number of sophisticated emissions technologies have been used to meet the market requirements of the earthmoving sector, while manufacturers have also managed to achieve performance improvements by boosting power and torque, while simultaneously lowering fuel consumption. Because of the increased cost of the advanced engine technologies, manufacturers have been keen to try and lower ownership costs by cutting fuel consumption and extending service intervals.
However these low emission engines are also limited to being used in countries where high quality, low sulphur fuels are available. For emergent markets this has resulted in manufacturers developing entirely different model ranges. While basic designs may be similar, specifications and equipment are entirely different from models sold into Europe and North America resulting in very different products. These models have been developed with a combination of technologies, retaining some of the advanced electronics and hydraulics, but opting for engines capable of coping with lower fuel qualities and which meet the Tier 2 or Tier 3 emissions requirements.
Tracks
New models in the excavator market are being aimed at specific territories, perhaps even more so than other types of machines. Caterpillar’s 349D2 L excavator is a heavy duty machine that weighs from 44.4-47.3tonnes depending on the specification and is said to offer low owning and operating costs. The machine is available with either long reach or mass excavation front linkage designs and is powered by a Cat C13 diesel featuring the ACERT technology that delivers 301kW while also being fuel-efficient. The machine features a system that switches to the economy mode during starting, no matter which mode has been selected previously and this cuts fuel consumption by up to 9%.Stability is optimised by a track length of 5.36m and a 3.34m track width (fitted with standard 600mm track shoes). The life of tracks and pin/bushings is said to be long and the chains are greased and sealed to reduce travel noise and to reduce operating costs. The machine is available with a 6.9m reach boom and a 3.35m reach stick. Meanwhile the 6.55m mass excavation boom is offered with a 2.55m mass stick for Africa, Middle East and CIS and a 3m mass stick for Turkey. The 349D2 L features a large cab with high visibility and ROPS for the Turkish market.
Sharing similar features, the 40.3tonne Cat 340D2 L replaces the earlier 340D L but benefits from a more refined hydraulic system and a fuel-efficient Cat C9 engine that meets Tier 2/Stage II, and China Tier 2 emissions requirements. The engine delivers 200kW and also offers a fuel saving of 7%, benefiting from sensors that respond to light load conditions. Fuel filtration allows the machine to be operated in areas where fuel quality is suspect while high power hydraulics optimise performance.
The standard machine features a 6.5m heavy duty front linkage designed for versatility, combining high productivity with adaptability. A mass excavation version of the machine is also available with a 6.18m boom, an 8.45tonne counterweight and bucket sizes of 2.6-2.69m3. Heavy duty undercarriage ensures long life in tough operating conditions. Other features include the firm’s advanced LINK telematics system, which helps fleet owners manage productivity and lower owning and operating costs through the online VisionLink interface. Users can track parameters such as location, hours, fuel usage, diagnostic codes, and idle time.
The machine retains its high breakout and lifting forces, and with a 2.5m dipper arm and a standard 6.2m monoboom it delivers a bucket digging force of up to 253.6kN. The excavator is also equipped with a new tipping link geometry that provides increased vertical wall digging depth. The machine has the firm’s latest cab structure, with increased soundproofing and better structural rigidity, while a single control allows for selection of the various power modes. The firm’s LiveLink telematic system has been upgraded, offering fleet owners remote access to fuel consumption and operating data for the machine. In addition the LiveLink ECU can be matched with the engine’s ECU, preventing tracking the machine from being started if necessary and adding to security.
The PC210LCi-10 weighs from 22.6-23.5tonnes depending on the configuration, with power from a diesel rated at 123kW. The machine also has latest KOMTRAX telematics technology, which delivers operating information to a secure website using wireless technology. Data such as operating hours, fuel consumption, location, cautions and maintenance alerts can be relayed to the web application for analysis. The fleet monitoring system can be used to boost machine availability as it allows remote diagnosis. The machine also comes with the Komatsu CARE maintenance programme, offered as standard for the first three years or 2,000 hours for every Tier 4 Interim/Stage IIIB and Tier 4 Final/Stage IV machine.
Wheels
The wheeled loader market is also highly competitive at present and new models are also coming to market worldwide.Komatsu Europe is also offering the WA100M-7 compact wheeled loader, which is driven by a 66kW Komatsu SAA4D95LE-6 engine that is Stage IIIB/Tier 4 Interim certified. The 7tonne machine offers a 10% fuel saving over the model being replaced, while it features improved operator comfort and visibility. Suited to tough construction applications, the WA100M-7 delivers high torque at low rpm, and has high rimpull, driving through a fully automatic, hydrostatic transmission to all four wheels. A 100% differential lock can be fitted to the two LSD axles as an option.
Other features include the latest KOMTRAX telematics technology, providing operating information through a secure website to the fleet manager for analysis. Highly versatile, the machine has a hydraulic quick-coupler and a delta boom and also features the firm’s easy fork configuration for high breakout force and parallel movement during forklift applications.
Finally SDLG is now launching a new model wheel loader in North America – the SDLG LG948L. This new loader lies in a key capacity class for the region, with its 2.35m³ bucket capacity, as some 62% of new wheel loaders purchased in North America are in the 1.96m³ to 2.75m³ range.
This model has been introduced following customer demand for a machine with a capacity in between the existing 1.88m3 LG938L and the 3.13m3 LG959. As with other SDLG models, the LG948L is aimed at wheeled loader customers that do not require the features seen on premium-priced machines but which need a productive and durable machine with good quality. Power for the 13.7tonne machine comes from a