Excavators and wheeled loaders benefit from new engine technology - Mike Woof reports. Competition is tough in the market for crawler excavators and wheeled loaders. These production machines account for a significant percentage of the entire construction equipment market worldwide and the segment also has the widest array of competing manufacturers. In the past, European, Japanese and US manufacturers dominated this sector but in the last 20 years South Korean companies have built significant market shares
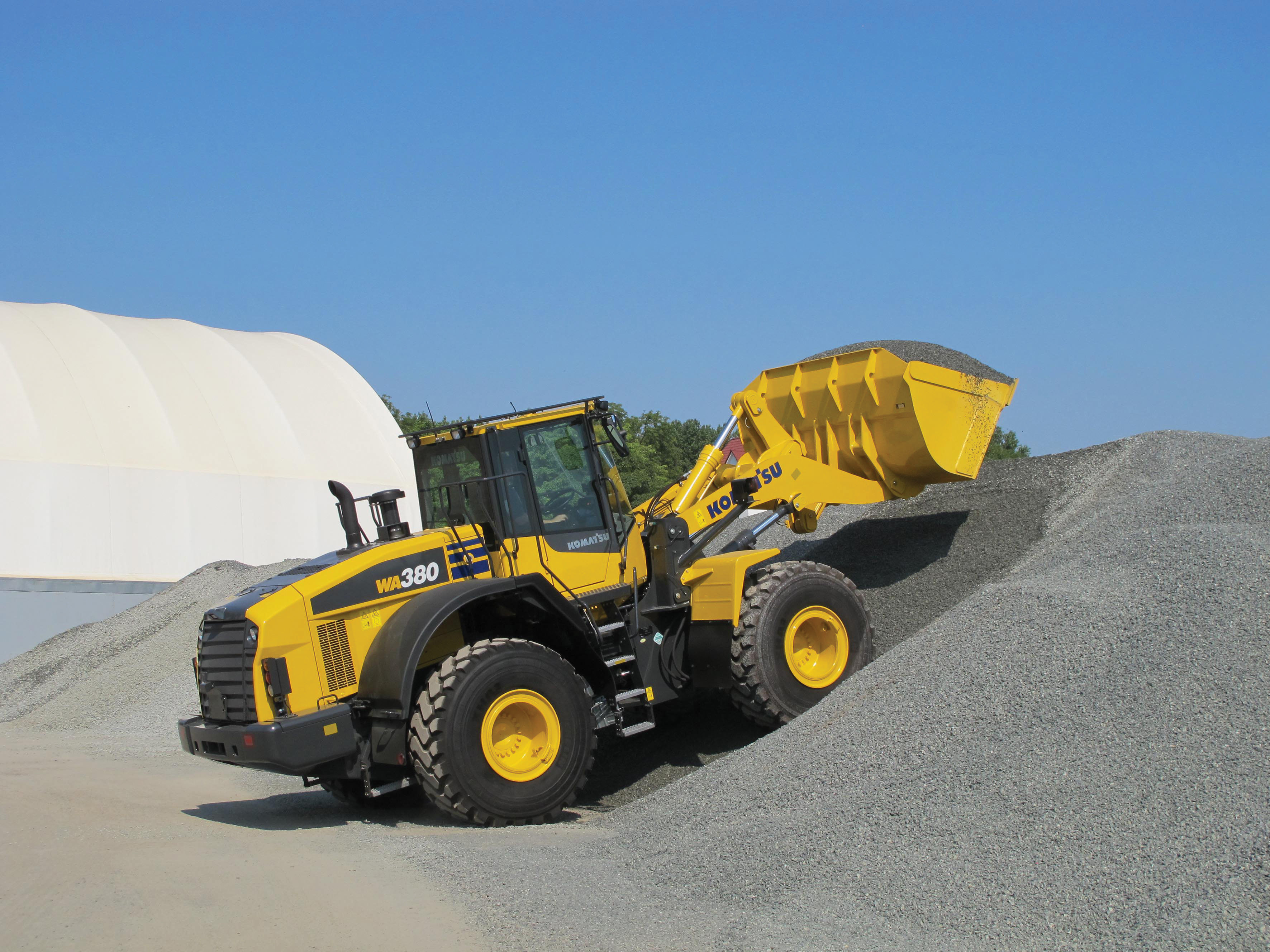
Improved operator comfort, and better serviceability are key features of Komatsu’s new WA380-7 wheeled loader
Excavators and wheeled loaders benefit from new engine technology - Mike Woof reports
Competition is tough in the market for crawler excavators and wheeled loaders. These production machines account for a significant percentage of the entire construction equipment market worldwide and the segment also has the widest array of competing manufacturers.In the past, European, Japanese and US manufacturers dominated this sector but in the last 20 years South Korean companies have built significant market shares, and in more recent times Chinese firms have joined the competition. The first generation of South Korean machines for export were basic but these were quickly improved. A similar process has been seen with Chinese machines, with the latest units from the major manufacturers now featuring components from leading brands as well as high build quality. Chinese manufacturers have a long history of building wheeled loaders but have also moved into the crawler excavator market in a big way.
For the customer there is now an almost bewildering array of machines available including equipment from well-known major manufacturers and the Chinese companies that are newer to the international export markets. For 2013 a considerable group of new and improved wheeled loader and excavator models are coming to market. For Europe and North America these feature the latest emissions control technologies, with some firms readying themselves for the introduction of the first phase of the Tier 4 Final/Stage IV regulations in early 2014. Many companies are also offering Tier 2/Stage II and Tier 3/Stage III compliant equipment for sale into some of the fast growing emergent markets.
Key business developments timed for the upcoming bauma show include the launch of
From a technical perspective,
Loaders
In the wheeled loaders segment there are several new machines coming to market andAs with larger Case F Series wheeled loaders, the 621F has its cooling pack directly behind the operator’s cab, moving the engine to the back of the machine to reduce the size of the counterweight. Cooling radiators are said to form a cube behind the cab around the cooling fan, providing clean air through each radiator. The increased cooling efficiency is said by Case to result in longer coolant life and reduced running costs.
From
The DL200-3 and DL250-3 are both powered by the Doosan DL06K, a common rail, six-cylinder diesel that meets Stage IIIB/Tier 4 Interim emissions regulations. This has been achieved through the use of exhaust gas recirculation (EGR) and diesel particulate filter (DPF) after-treatment technologies.
The operator has a choice of three working modes - Eco, Normal and Power. The operator can travel in normal mode and switch to power mode when it is needed and can also set a password for machine start. Load-sensing, variable hydraulic piston pumps help optimise performance and further reduce fuel consumption. As an option, customers can choose ZF axles with a hydraulic differential lock. There is also a wide choice of options for the DL200-3 and DL250-3 wheeled loaders, including electric steering.
The ZW250-5 wheeled loader complies with EU regulations on emissions standards and has an 181kW 7.8litre six-cylinder water-cooled turbo engine, and a 2.8-3.8m³ bucket capacity and 157kN breakout force. Operating weights range from 20.25-20.7tonnes depending on specification and the wheeled loader is also said to be easier to manoeuvre than before, boosting productivity.
In Standard mode, the engine speed is controlled, which allows for smooth and efficient acceleration during loading, regular operations and travelling on level terrain. Fuel consumption is also said to be reduced by up to 10%. A new clutch cut-off system allows for smooth operation during loading, while a quick power switch on the ZW250-5 boosts the power when required by changing work modes. The shift-up delay to third gear makes the wheeled loader safer to operate in confined spaces, because it can perform excavating and unloading tasks more safely in first and second gear.
An intelligent clutch cut-off system is standard with both transmissions, making the machines ideal for truck loading and tight site manoeuvring. The two loaders are available in parallel-lift HT specification, with a powerful Z-bar linkage or with High Lift and Super High Lift ZX arms.
Komatsu is introducing it Dash 7 generation of wheeled loaders with a range of models including the WA320-7 and WA380-7 and featuring new high visibility, low noise cabs. The new WA380-7 weighs in at 18tonnes and features improved efficiency and lower fuel consumption. Power comes from an SAA6D107E-2 Komatsu diesel rated at 143kW and which meets Tier 4 Interim/Stage IIIB emissions requirements. Power output and torque have been increased over the earlier generation engine used in the WA380-6, while fuel consumption has reduced by 10%. Other engine features include the new variable geometry turbocharger (KVGT) and an exhaust gas recirculation (EGR) valve.
Service and maintenance costs are addressed by the Komatsu CARE maintenance program for Komatsu customers, which comes as standard with every new Komatsu machine that meets the Tier 4 Interim/Stage IIIB emissions requirements. For the first three years or 2,000 hours it covers factory-scheduled maintenance and includes up to two complimentary Komatsu diesel particulate filter (KDPF) exchanges and a KDPF warranty for the first five years or 9,000 hours. Also fitted is the latest KOMTRAX technology on the WA380-7, which sends machine operating information such as operating hours, fuel consumption, location, cautions and maintenance alerts to a secure website using wireless technology. This sophisticated fleet monitoring system increases machine availability, reduces the risk of machine theft and allows for remote diagnosis by the distributor. The large capacity torque converter has lock-up as standard, boosting acceleration and performance on gradients, as well as allowing a higher maximum speed of 40km/h and also reducing fuel consumption.
Excavators
Weighing in at 42-43.3tonnes depending on specification, the new Doosan DX420LC-3 excavator is Stage IIIB/Tier 4 Interim emissions compliant and is said to offer significant benefits over the model it replaces. Improvements include an increase in power, boosting overall productivity, and the machine can be used in heavy-duty applications.Power comes from an Isuzu AL-6UZ1X diesel engine that features exhaust gas recirculation (EGR) and diesel particulate filter (DPF) after-treatment and delivers 19% more power at 270kW and a 6% increase in torque over the engine in the previous machine from the firm in this size class. A new travel device in the DX420LC-3 excavator contributes to an increase in drawbar pull by 10%, a 5% increase in swing torque and a 10% increase in the travel speed. Improved hydraulic pumps and valves have increased main pump flow by 6%, providing a combination of higher overall pressures and hydraulic flow for increased comfort, travelling performance, smoothness, power and improved attachment work. Increased operator comfort is claimed for the ROPS and OPG certified cab, while all functions can be controlled both from the instrument panel. As a standard feature, the operator has access to a new attachment select and setting function, with multiple recordable preset values.
The machine has been beefed up to further boost longevity, with the extra steel increasing overall weight by 1tonne and this also includes a counterweight that weighs 8.2tonnes instead of the previous 8tonnes, maximising stability. A heavy-duty undercarriage is fitted and the service life of the machine has been extended.
The ZX290LC-5 is one of eight new Zaxis-5 model excavators from Hitachi and like its fellow new machines, has been designed to meet the requirements of European customers. The powerful new-generation 140kW Isuzu Stage IIIB/Tier 4 Interim compliant engine can deliver higher productivity with greater fuel efficiency. The integral muffler filter captures air pollutants, which are automatically burnt thanks to an oxidation catalyst and exhaust temperature control. The model’s variable geometry turbocharger and high volume-cooled EGR (Exhaust Gas Recirculation) also help to reduce nitrous oxide levels.
Hitachi says its ZX290LC-5 is able to operate quicker with lower fuel consumption than the previous Zaxis-3 model using the Hitachi TRIAS hydraulic system. The excavator weighs up to 30tonnes and features a reinforced undercarriage and strengthened front attachment for added durability in tough working conditions. Meanwhile, an attachment support system integrated within the ZX290LC-5’s design has 11 modes for easy fitting of different attachments.
The ROPS pressurised cab of the new model prevents dust ingress and features a user-friendly control panel, air-suspension seat, expanded leg room and all-round visibility. To reduce downtime, the ZX290LC-5 the air conditioning unit can be easily opened for the condenser and radiator to be cleaned. The full range of Zaxis-5 models includes the ZX160LC-5; ZX180CL-5; ZX210LC-5; ZX225USLC-5; ZX225USRLC-5; ZX250LC-5; ZX290LC-5; and ZX350LC-5.
Like its fellow new 9A series hydraulic excavators with engines above 130kW, the engine on the Robex R380NLC-9A hydraulic crawler excavator from
Meanwhile, the joystick consoles and operator’s seat in the R380NLC-9A and the other new 9A series hydraulic excavators are said by Hyundai HI to form an ergonometric unit. The firm hopes that operators will benefit from the machine’s smart key and in-cab touch displays. In addition, the engines can also be turned on with a start button and activated at any time with a password. The large, movable in-cab display allows the operator to select working modes quickly.
A Bluetooth mobile phone connection is also available with the new 9A series hydraulic excavators, allowing the operator to communicate with colleagues outside the excavator using the optional hands-free device. Maintenance intervals for the new 9A generation of machines have been increased to 500 hours for all components and 1,000 hours for hydraulic filters. The models’ hydraulic oil is said by Hyundai HI to have a service life of 5,000 hours due to the very fine inflow and return flow filters.
LiuGong is following up the introduction of its first E series excavator, the 922E, with a whole new range. The top-of-the-line model is the 945E, which competes in the 45tonne class, features a 2.2m3 bucket and is powered by a