The improvements to articulated dump trucks (ADTs) have been substantial in recent years. Comparing a present day machine with one from 20 or even just 10 years ago shows how far design has come. Major improvements have been made in visibility, operator comfort levels, rough terrain performance, driveline efficiency and productivity, to name but a few key areas. All of the latest generation ADTs available on the world market now come with Tier 3/Stage IIIA compliant diesels that produce far lower noise and
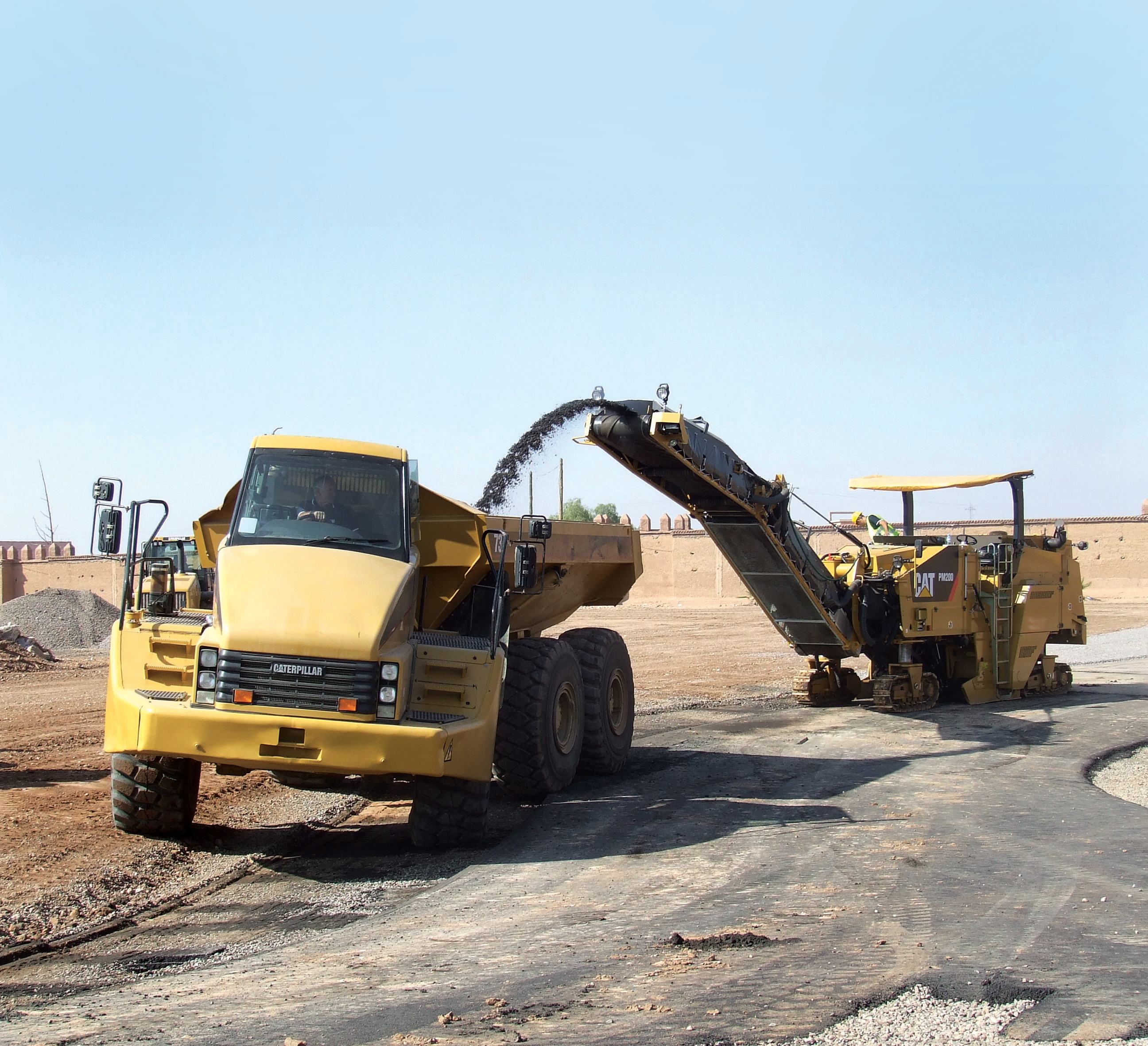
Caterpillar's current ADT range offers significant benefits over the firm's previous generation machines
The ADT continues to evolve and improve, Mike Woof reports
The improvements to articulated dump trucks (ADTs) have been substantial in recent years. Comparing a present day machine with one from 20 or even just 10 years ago shows how far design has come. Major improvements have been made in visibility, operator comfort levels, rough terrain performance, driveline efficiency and productivity, to name but a few key areas. All of the latest generation ADTs available on the world market now come with Tier 3/Stage IIIA compliant diesels that produce far lower noise and emission levels than fore, while also producing more power and in most (if not all) cases, consuming less fuel (and offering longer service intervals) than before.With the rapid price rises in fuel of late, ADT manufacturers are also taking on the issue of fuel costs. In the last 12 months the cost of a barrel of crude oil has doubled in price and is set to climb higher according to most analysts. Bell has long championed the low fuel consumption of its ADTs, a result of the firm's use of economical
By comparison though, some customers value availability and service support highest of all. One US contractor ran an exhaustive back to back trial of Caterpillar ADTs against a rival brand over six months. In the end, despite the comprehensive report that said there was little overall advantage offered by either machine (they each had their strengths and weaknesses against the other), the customer opted for the Cat truck. The reason for the choice was that the company already ran a fleet of Cat excavators, dozers and graders, had a good relationship with the local dealer and was unsure whether the rival brand would come with similar levels of support.
The market has changed substantially too. As recently as 10 years ago just five manufacturers, Bell, Caterpillar, Moxy, Terex and Volvo, made ADTs in any great numbers. While there were other firms in the sector such as
New metal Caterpillar has tweaked the performance of its top-of-the-line 740 to increase its payload and boost its overall productivity. The truck can now carry 39.5tonnes of material, and increase of 3tonnes from the earlier model and this move is of note as it gives the Caterpillar machine an advantage over its nearest competitors. The C15 engine is rated at 350kW (gross) and meets the relevant emissions standards for North America and Europe while it allows a top speed of 54km/h through a seven speed gearbox (which also has two reverse ratios). Body capacity is 24.6m3 (2:1 heaped) and the truck comes with high comfort cab and an array of options such as the firm's satellite-based ProductLink system.
Komatsu is now offering its upgraded HM250-2 ADT on the European market. The machine is being introduced due to rising demand for ADTs in this key size class and offers significant performance gains over the model it replaces, which Komatsu believes will make the truck a stronger competitor amidst the fierce rivalry of the market segment.
The new truck is based on the proven HM300-2 and like its stablemate, the HM250-2 has a higher top travel speed and improved manoeuvrability, aided by its shorter front. Komatsu is also offering high stopping power in the shape of a forced oil cooled multiple-disc system and this shares components with the larger machine, helping to reduce parts costs for fleet owners.
Power comes from an SAA6D125E-5 - ecot3 engine, which delivers a net horsepower of 232kW and meets Stage IIIA and Tier 3 emission regulations. Features of this new diesel include optimised combustion timing and ignition, as well as a specially designed combustion chamber, which all helps to reduce fuel consumption, NOx and particulates emissions, and noise levels. The improved ROPS/FOPS cab is wide and offers high visibility to the front, sides and rear while ride quality is maximised due to a combination of the truck's air, suspension seat, hydro-pneumatic suspension and viscous cab mounts. The truck offers a 24tonne payload and an SAE body capacity of 14.7m3, while it has a maximum travel speed of 57.6km/h.
To maximise uptime and minimise servicing costs for the customer, the HM250-2 is equipped with the firm's KOMTRAX satellite-based monitoring system as standard. The KOMTRAX
package can make significant gains in fleet management efficiency and reduce running costs by monitoring service schedules and performance parameters. In addition this package offers features such as machine tracking, remote engine lock, travel alarms and fleet maps.
Moxy Engineering says that its MT26 and MT31 ADTs now offer significant increases in performance due to several key upgrades. These Series lll machines come with weight-saving body and rear drive designs, allowing increased payloads. In addition oil immersed front and rear disc brakes improve stopping power while the reconfigured tail end of each body means that there is no longer a need for a tailgate even when carrying wet or loose materials. Production of the new models is already underway and machines are now being made available.
With these upgrades, Moxy has managed to boost the power to weight ratios for the machines to 5.03kW/tonne and 4.95kW/tonne for the MT26 and MT31 respectively and the firm claims that the machines now set standards in their respective weight classes. The upgraded MT26-lll offers a heaped capacity of 15m3 and a payload of 24tonnes, some 600kg more than its predecessor. Similarly, the MT31-lll now offers a 28.5tonne payload, a gain of 500kg as well as a heaped capacity of 18m3.
Both trucks are powered by the proven Tier 3/Stage IIIA compliant
As with all the Moxy ADTs, these models have permanent six-wheel drive, a free-swinging rear tandem bogie, articulated hinge system and independent front wheel suspension. The firm claims that this driveline and suspension set-up provides good driving stability in uneven terrain, allowing equal power and weight distribution to the wheels. The dual circuit hydraulically operated brakes have enclosed oil-cooled wet multiple discs all round and will reduce maintenance needs in comparison with the dry discs fitted to the previous models. The parking brake has a disc brake on the rear transmission shaft with spring actuated hydraulic release.
The sloping heavy-duty body has a wide bottom section and is designed for exhaust heating. The two tilt cylinders are single stage, double acting type enabling a raised tipping time of 11 seconds and a down time of 10 seconds.
The improved, rubber-mounted cab comes with air conditioning and an air-suspension seat, good visibility to the front and rear, good ride characteristics and a low interior noise level. Meanwhile the transmission allows the operator to drive the truck in either automatic or manual mode, both offering smooth gear shifting.
Successive upgrades to Volvo Construction Equipment's ADTs are making them more efficient and productive. Volvo CE has long dominated the ADT sector and its machines have a strong reputation for reliability, durability and good resale vales, which has helped maintain this range in its market leading position.
Volvo CE has made a determined effort to retain the perception of its ADTs as a premium brand. The smooth shifting transmissions on the latest models are a world apart those fitted to earlier generation machines, while highly effective retardation minimises the wear and tear on the service brakes (fully immersed disc braking to all six wheels is a feature of the A35 and A40). Traction is improved to with limited slip differentials that can be engaged on the move to minimise wheel-slip in poor ground conditions. And for the operator, the layout of the cab and overall comfort levels mean that working for a full shift will be less tiring than on previous models.
However, the recently-introduced full suspension option for the A35 and A40 models has further added to the reputation of the Volvo CE ADTs as quality machines, as a drive around the firm's test track area proved. The new trucks offer a substantial 250mm of suspension travel. While the full suspension option adds a premium pricetag to the A35 and A40 ADTs, the system does help to increase output/machine. The firm claims that for a long haul operation this can boost productivity by up to 40%, although for most normal cycles the productivity gain will be around 25%.
The overall benefits could be substantial and further cut payback times for machines equipped with full suspension technology.
These systems may cost more but help reduce wear and tear on the machine, lowering maintenance needs and costly downtime. Furthermore, it seems likely that tyre life will be extended, an important consideration given the current poor availability of tyres for off-highway machines such as ADTs. And with the thorny issue of whole body vibration becoming an important consideration in Europe in particular, the full suspension system offers the potential to extend operator hours in comparison with conventional trucks.