The market for ADTs has developed considerably in the last 20 years while the number of manufacturers active in this segment has also grown
Volvo CE was a pioneer of the ADT; the first firm to mass manufacture an articulating, tipper truck with all-wheel-drive in the 1960s, although it is not correct to say that the firm actually invented the ADT as some may claim.
Performance has increased considerably in the ADT sector in recent years, with many trucks now featuring low maintenance, oil-immersed d
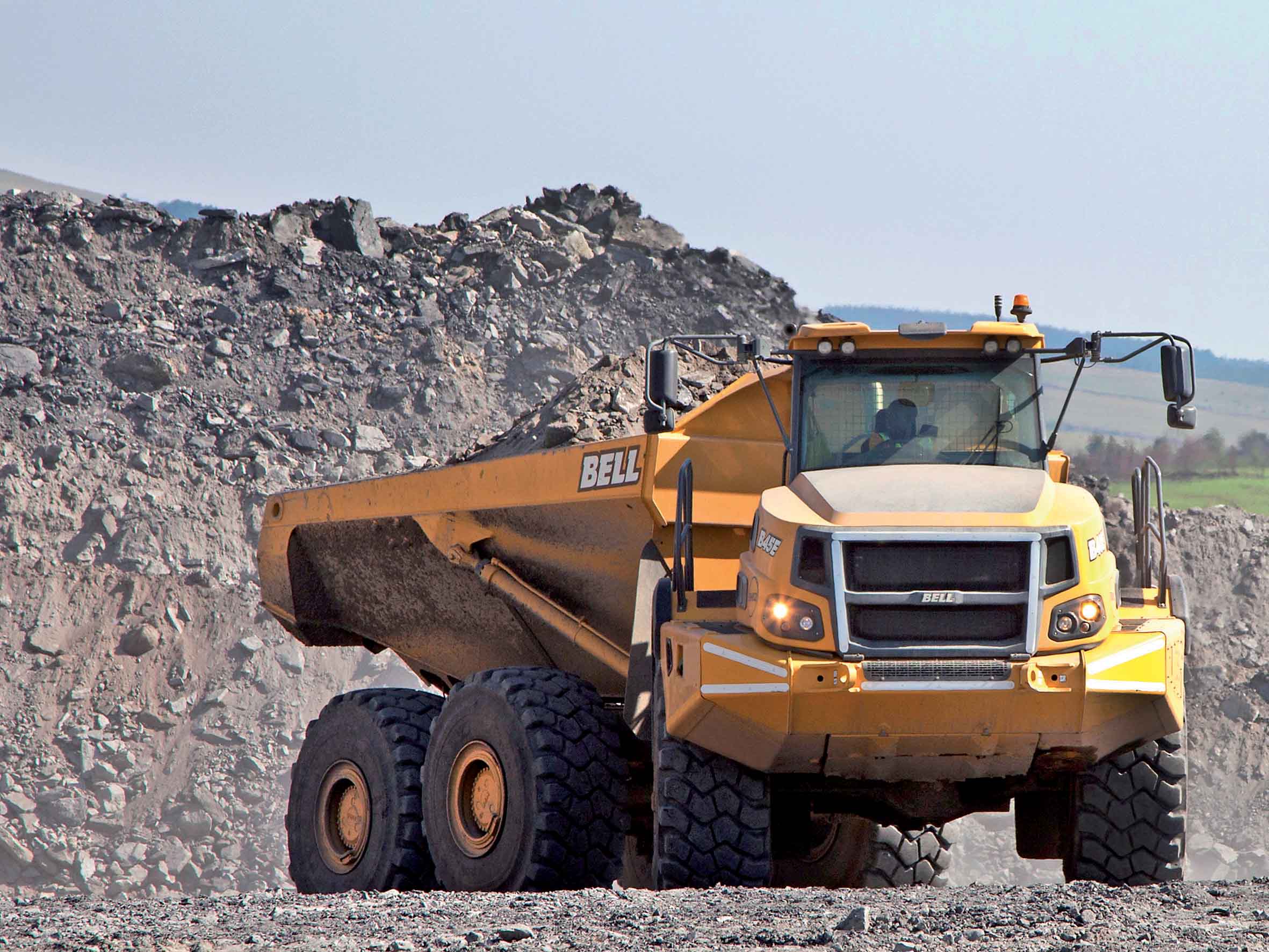
Bell’s new ADT range offers increased load capacity
The market for ADTs has developed considerably in the last 20 years while the number of manufacturers active in this segment has also grown
359 Volvo CE was a pioneer of the ADT; the first firm to mass manufacture an articulating, tipper truck with all-wheel-drive in the 1960s, although it is not correct to say that the firm actually invented the ADT as some may claim.
Performance has increased considerably in the ADT sector in recent years, with many trucks now featuring low maintenance, oil-immersed disc brakes at the rear. The new generation machines also have full suspension systems for higher cycle speeds and greater operator comfort, as well as larger cabs with a wider field of view than in earlier generation machines.
Payload capacity and productivity are the watchwords for the ADT market in 2016.1240 Bell Equipment says it is expanding its E Series articulated hauler line-up with the introduction of its B45E. This machines offers a rated payload of 41tonnes and like other models from the firm, retains the use of a Mercedes-Benz off-highway diesel, driving the truck through an 3713 Allison transmission. Increases have been made for capacity across Bell’s truck range, while the machines all benefit from reductions in the cost/tonne of 6-7%, compared to the previous D series trucks.
To accommodate the larger seven-speed transmission, Bell has removed the automatic retarder on the transmission and opted to incorporate this feature into the wet brake system. The trucks also have a new engine brake, which is said to offer greater retardation than the engine braking produced by the outgoing V6 and V8 engines on the previous D-series trucks. Retardation is operated automatically; as before the new location of the system is designed so as not to adversely impact on brake life. The firm has carried out extensive testing, which has shown that at the low pressures generated in the brakes during retardation, there is always oil between the wet brake plates, avoiding wear.
178 Caterpillar claims that its new C2 Series ADTs offer increased performance for the 24tonne and 28tonne payload classes. The new models are the 234kW 725C2 and the 274kW 730C2, also available as the special 730C2 EJ with the firm’s novel ejector-body. The machines are fitted with automatic traction control as standard, a system said to provide better performance in poor conditions. Other key benefits include lower operating costs, and added rimpull/retarding capability, as well as durability, high availability, high resale value, and good rental value.
Customers can select the engine type to suit local emissions regulations with versions available in Tier 2, Tier 3 or Tier 4 Final variants. The engines drive through Cat 6F/1R power-shift transmissions with electronically modulated clutch engagement pressures that are said to allow smooth shifting. The transmission has the Caterpillar advanced productivity electronic control strategy (APECS) system, which is said to boost acceleration, maintain torque converter lock-up and ground speed during shifting, allow automatic speed holding, and modify shift points to match the conditions. The firm claims that this APECS technology helps raise productivity, improve control, and deliver better fuel economy.
An engine compression brake system helps control speed on descents for the 730C2 and 730C2 EJ models, while the 725C2 has a multimode fluid retarder. All three trucks have six-wheel drive, wet disc clutch locks in cross axle and interaxle differentials as well as wet plate disc brakes on all axles.
The trucks retain the same rugged structural components used in the previous generation machines as well as the proven oil/nitrogen type suspension at the front and walking beam type suspension layout at the rear. The new dumpbody is made from a more wear resistant steel while its design is also said to ensure clean dumping and minimal carryback.
The two-seat cab offers good ergonomics and an all-round view as well as improved controls.
The engine cover is raised electrically giving access for maintenance and the trucks have grouped service points. Maintenance is further aided by the fitting of Caterpillar’s Product Link system, which allows the owner to track performance remotely and monitor functions such as operating hours, oil and coolant levels and temperatures.
The8081 Terex Trucks brand is now owned by Volvo CE and the firm has rolled out its flagship 38tonne capacity TA400 articulated dump truck, the largest of the new generation hauler line-up. A key development is the installation of a new Stage IV/Tier 4 Final compliant diesel. The firm claims that improvements have been made to ensure increased durability and protection of truck components, including upgraded hydraulic hoses, electrical interfaces, transmission mountings and brake pipes.
To prolong hydraulic component lifecycles, Terex Trucks has introduced magnetic pressure filters that reduce the risk of contaminants entering the system. They also improve the cleanliness of the hydraulic oil. Force-cooled multidisc brakes lower operational costs and increase safety. Supported by an electronic activated exhaust brake and a six-stage modulating transmission retarder, the TA400 benefits from longer brake component lifecycles.
The transmission now features high-performance oil that extends time between service intervals to 6,000 hours. The drivetrain maintains traction even in difficult terrain due to longitudinal and limited slip transverse differential locks, while the engine and drivetrain have automatic adaptive shifting.
The Stage IV emissions control system used on the truck features the latest generation Selective Catalytic Reduction (SCR), combined with Exhaust Gas Regeneration (EGR) technology and a Variable Geometry Turbo (VGT). However the truck does not have a Diesel Particulate Filter (DPF), lowering maintenance needs and running costs.
The firm can supply its trucks in Stage IV/Tier 4 Final variants for regulated markets, as well as Tier 2 versions for non-regulated markets.
Improvements have also been made to operator comfort, with anti-vibration mounts for the engine and cabin, as well as cushioned stops on the steering cylinders that have been integrated. Machine performance information has also been improved, including transmission diagnostics that informs the operator on the status of the machine, including the oil quality, oil level, filter life, and fault codes/service indication. The firm says that further upgraded ADT models are due later in the year and that these will have similar features.
For the Volvo CE brand, the firm is introducing its A60H truck, the largest ADT the firm has built for a number of years. This features a payload of 55tonnes, around 40% more than the previous top of the range A40G. The machine offers a payload comparable with many rigid trucks and will suit operations in sites with steep ramp hauls unsuited to rear drive only machines. The firm claims that there is an increasing demand for ADTs with larger capacities than that offered by the machines previously available on the market. The truck shares similar features with the smaller units in the Volvo CE range including matched drivetrain, automatic drive combinations (with 100% differential locks), all-terrain bogie, hydro-mechanical steering and active suspension.
It is worth noting though that the A60H is not, as claimed elsewhere, the biggest ADT the firm has ever built. The company manufactured a series of A70 units with 65tonne payloads in the late 1990s. These were based around the current A40C model, but with an extended rear dumpbody as well as three axles at the rear. The A70 was built to meet the needs of Norwegian coal producer SNSK, which wanted an all-wheel-drive hauler to carry material on an ice road over a glacier from a mine on the Spitsbergen archipelago and this model remains the largest series-built ADT ever constructed.
Performance has increased considerably in the ADT sector in recent years, with many trucks now featuring low maintenance, oil-immersed disc brakes at the rear. The new generation machines also have full suspension systems for higher cycle speeds and greater operator comfort, as well as larger cabs with a wider field of view than in earlier generation machines.
Payload capacity and productivity are the watchwords for the ADT market in 2016.
To accommodate the larger seven-speed transmission, Bell has removed the automatic retarder on the transmission and opted to incorporate this feature into the wet brake system. The trucks also have a new engine brake, which is said to offer greater retardation than the engine braking produced by the outgoing V6 and V8 engines on the previous D-series trucks. Retardation is operated automatically; as before the new location of the system is designed so as not to adversely impact on brake life. The firm has carried out extensive testing, which has shown that at the low pressures generated in the brakes during retardation, there is always oil between the wet brake plates, avoiding wear.
Customers can select the engine type to suit local emissions regulations with versions available in Tier 2, Tier 3 or Tier 4 Final variants. The engines drive through Cat 6F/1R power-shift transmissions with electronically modulated clutch engagement pressures that are said to allow smooth shifting. The transmission has the Caterpillar advanced productivity electronic control strategy (APECS) system, which is said to boost acceleration, maintain torque converter lock-up and ground speed during shifting, allow automatic speed holding, and modify shift points to match the conditions. The firm claims that this APECS technology helps raise productivity, improve control, and deliver better fuel economy.
An engine compression brake system helps control speed on descents for the 730C2 and 730C2 EJ models, while the 725C2 has a multimode fluid retarder. All three trucks have six-wheel drive, wet disc clutch locks in cross axle and interaxle differentials as well as wet plate disc brakes on all axles.
The trucks retain the same rugged structural components used in the previous generation machines as well as the proven oil/nitrogen type suspension at the front and walking beam type suspension layout at the rear. The new dumpbody is made from a more wear resistant steel while its design is also said to ensure clean dumping and minimal carryback.
The two-seat cab offers good ergonomics and an all-round view as well as improved controls.
The engine cover is raised electrically giving access for maintenance and the trucks have grouped service points. Maintenance is further aided by the fitting of Caterpillar’s Product Link system, which allows the owner to track performance remotely and monitor functions such as operating hours, oil and coolant levels and temperatures.
The
To prolong hydraulic component lifecycles, Terex Trucks has introduced magnetic pressure filters that reduce the risk of contaminants entering the system. They also improve the cleanliness of the hydraulic oil. Force-cooled multidisc brakes lower operational costs and increase safety. Supported by an electronic activated exhaust brake and a six-stage modulating transmission retarder, the TA400 benefits from longer brake component lifecycles.
The transmission now features high-performance oil that extends time between service intervals to 6,000 hours. The drivetrain maintains traction even in difficult terrain due to longitudinal and limited slip transverse differential locks, while the engine and drivetrain have automatic adaptive shifting.
The Stage IV emissions control system used on the truck features the latest generation Selective Catalytic Reduction (SCR), combined with Exhaust Gas Regeneration (EGR) technology and a Variable Geometry Turbo (VGT). However the truck does not have a Diesel Particulate Filter (DPF), lowering maintenance needs and running costs.
The firm can supply its trucks in Stage IV/Tier 4 Final variants for regulated markets, as well as Tier 2 versions for non-regulated markets.
Improvements have also been made to operator comfort, with anti-vibration mounts for the engine and cabin, as well as cushioned stops on the steering cylinders that have been integrated. Machine performance information has also been improved, including transmission diagnostics that informs the operator on the status of the machine, including the oil quality, oil level, filter life, and fault codes/service indication. The firm says that further upgraded ADT models are due later in the year and that these will have similar features.
For the Volvo CE brand, the firm is introducing its A60H truck, the largest ADT the firm has built for a number of years. This features a payload of 55tonnes, around 40% more than the previous top of the range A40G. The machine offers a payload comparable with many rigid trucks and will suit operations in sites with steep ramp hauls unsuited to rear drive only machines. The firm claims that there is an increasing demand for ADTs with larger capacities than that offered by the machines previously available on the market. The truck shares similar features with the smaller units in the Volvo CE range including matched drivetrain, automatic drive combinations (with 100% differential locks), all-terrain bogie, hydro-mechanical steering and active suspension.
It is worth noting though that the A60H is not, as claimed elsewhere, the biggest ADT the firm has ever built. The company manufactured a series of A70 units with 65tonne payloads in the late 1990s. These were based around the current A40C model, but with an extended rear dumpbody as well as three axles at the rear. The A70 was built to meet the needs of Norwegian coal producer SNSK, which wanted an all-wheel-drive hauler to carry material on an ice road over a glacier from a mine on the Spitsbergen archipelago and this model remains the largest series-built ADT ever constructed.