Manufacturers are rolling out sophisticated machines for the European, North American and Japanese markets - Mike Woof reports. This year has been a pivotal period for the development of advanced, low emission earthmoving machines. During 2011 an array of manufacturers have introduced new models designed to comply with the latest Stage IIIB/Tier 4 Interim emissions regulations introduced for
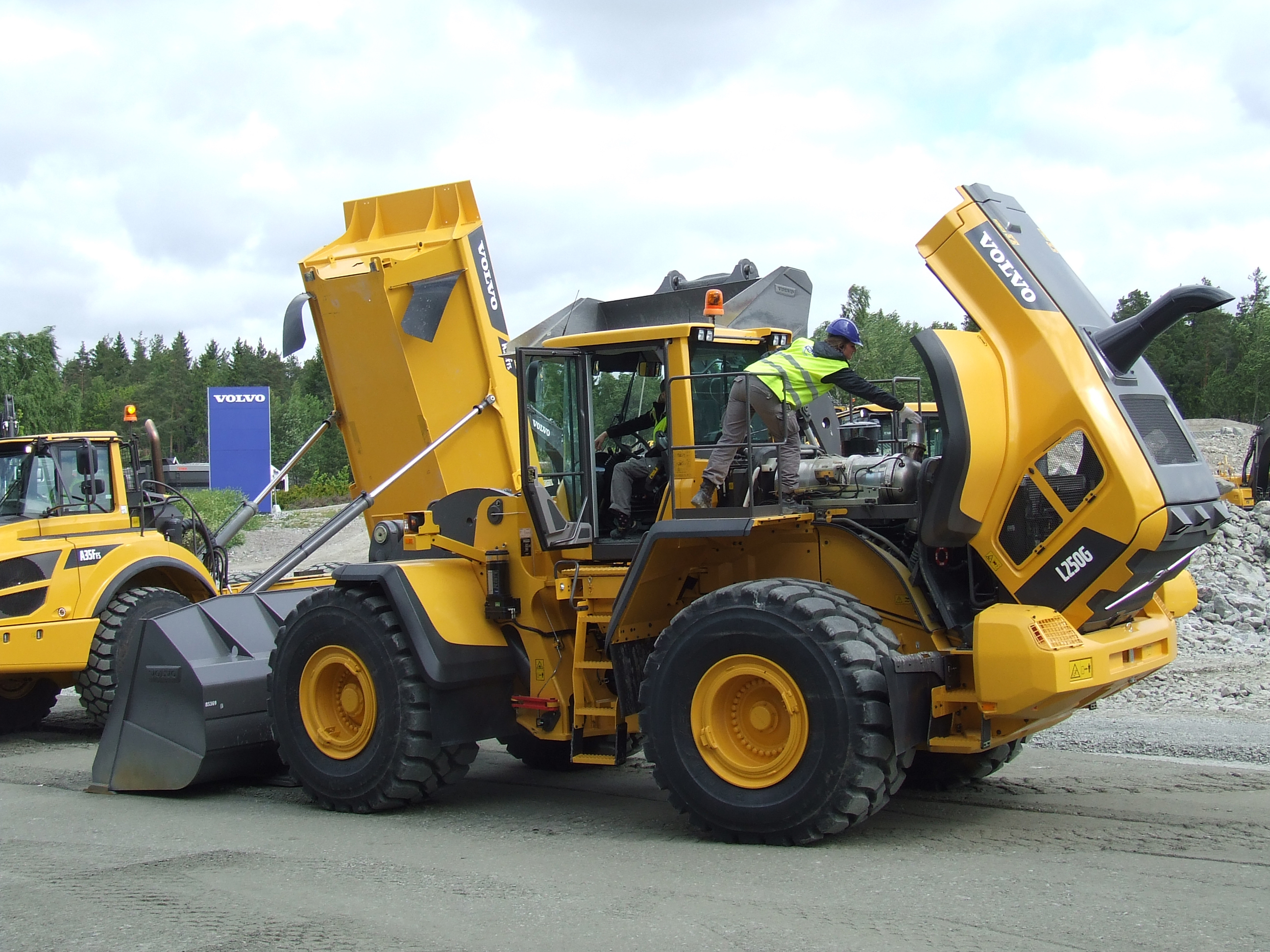
The Volvo L250G wheeled loader features the rear chassis from the L220 machine but is designed for high production loading
Manufacturers are rolling out sophisticated machines for the European, North American and Japanese markets - Mike Woof reports
This year has been a pivotal period for the development of advanced, low emission earthmoving machines. During 2011 an array of manufacturers have introduced new models designed to comply with the latest Stage IIIB/Tier 4 Interim emissions regulations introduced for North America, Europe and Japan. These developments represent a huge step forward technologically with firms employing an array of innovative systems that help reduce particulate and NOx emissions from the tailpipe.The major firms have all introduced new generation units to meet the regulations, with the likes of
From Caterpillar comes a series of new models including the all-new Cat 980K wheeled loader. The firm says the 980K offers high productivity, reliable performance and excellent fuel efficiency, while meeting the Stage IIIB emissions standards for Europe. Also new from Caterpillar are the 966K and 972K wheeled loaders and E Series 324E, 329E, 336E and 349E hydraulic excavators.
The 980K’s improvements over the earlier 980H include a new cab; load-sensing hydraulics; a 25% increase in lift force and a 16% increase in tilt force. The loader can use buckets from 4-12.2m³ and is said to be a productive and cost-effective tool in high-volume applications.
The improved loader also features new electro-hydraulic steering with either joystick or steering wheel control, plus performance series buckets and an optional lock-up torque converter. At the heart of the machine is the new Cat C13 ACERT engine, which delivers 274kW at 1,600rpm. The drive train has been optimised with the new engine to deliver efficient digging power, acceleration, performance and fuel efficiency. To boost productivity in load-and-carry applications and on ramps and to minimise traction loss in tough operating conditions, the 980K can be equipped with a new optional lock-up clutch torque converter. It is automatically activated in second through fourth gear, and when locked, operates like a direct-drive system.
The system improves performance and reduces fuel consumption in load-and-carry and ramp-duty cycles.
Safety and operator comfort have been priorities during the development of the new generation machines and on the 980K new steps that have a greater inclination angle
than the H Series provide easy access to the cab; there is a wider door opening and well-placed grab bars and a new front-hinged door that can be opened and closed while seated allow for easy entry and exit. Interior noise level has been reduced 50% compared to the previous model.
Visibility to the side and front has been improved as well as to the rear, despite the extra technology packed under the engine cover, while a rear-facing camera is fitted as standard to further boost the rearward view as well as operating safety.
The new low-effort electro-hydraulic joystick steering system is standard on the 980K, while an optional electro-hydraulic steering wheel system will also be available, and it also senses ground speed and automatically adjusts steering effort to improve controllability and comfort at higher speeds. Performance series buckets, developed especially for production loading, are standard.
The company says that a new load-sensing hydraulic system boosts working efficiency as it automatically directs the right amount of flow based on operating conditions, and fuel consumption is reduced. This system also allows parallel flow to lift, tilt and auxiliary hydraulics, so the functions can be performed simultaneously. In addition, the 980K’s lift and tilt forces have been increased by 25% and 16% respectively.
Doosan is developing a new series of ADTs that meet the Stage IIIB/tier 4 Interim emissions requirements, as well as launching new excavators. The company bought the
The move comes as demand grows for construction machines in key markets such as the Middle East, North Africa and Asia. Doosan Infracore’s CEO Tony Helsham said, “In North America we are starting to see ADT business pick up as well.”
The DA30 offers a power increase of 8% and its
The trucks feature
The larger MT51 is not being replaced for the time being and Helsham said, “There was no commonality with the other machines as it had an Allison transmission and a
He added that in the future the firm may revisit this class of machine but for the moment the focus is on the DA030 and DA40. The trucks retain the sloping rear chassis and the turning ring mounted in front of the articulation joint, which are said to improve weight distribution and body stability respectively, according to the firm. The articulation joint uses the same bearing set as the casings for the rear bogie drive, further reducing parts stocks. Rear view cameras are fitted as standard and these are switched on automatically when the operator engages reverse, a system that makes backing up to a tipping point considerably safer.
Competition is now tougher in the ADT sector than it has ever been however. In the mid 1990s the Moxy brand ADTs accounted for some 10% of the annual market for these machines with the firm building and selling around 400 units/year of the 4,000 in total sold worldwide. Rivals
The market has changed considerably with annual ADT sales having hit a peak of 10,450 units in 2007. While the worldwide market for 23-36tonne capacity machines was supplied by just five volume manufacturers in the mid 1990s: Bell, Caterpillar, Moxy, Terex, Volvo (the Brazilian
Doosan has high hopes for the DX300LC-3 excavator, which comes with a new cab, power modes and joystick controls amongst other upgrades. Power comes from a Tier 4 Interim. Stage IIIB compliant Doosan diesel rated at 150kW and this features EGR and DPF technology. Cooling capacity has been increased 10-15% over the previous generation models while the larger radiator and oil coolers have been separated to improve efficiency and maintenance access. This is the first of the new generation machines available and it will be followed in due course by the DX340, DX380, DX420, DX490 and DX530 during next year, which will share similar features.
Doosan also hopes to boost market share with its DL300-DL350 and DL420-DL550 wheeled loaders. Like the trucks, these feature Scania engines using SCR emissions technology with DC9 units in the smaller loaders and DC13s in the bigger machines. The cabs offer better visibility while the machines have new closed centre, load sensing hydraulics that boost efficiency.
From Komatsu comes the first of its new generation excavators, the PC240-10, which replaces the firm’s previous -8 machine. Also new to Europe is the HB215 hybrid excavator, which Komatsu first unveiled at the CONEXPO-CON/AGG 2011 exhibition in Las Vegas earlier this year, as well as the D65-17 bulldozer that Komatsu introduced at the same time.
The PC240-10 is an important machine for Komatsu as the company’s excavators form the core of its worldwide sales. According to the firm it is the global market leader for crawler excavators, a position it obviously wishes to retain so the build quality and performance of the new PC240-10 are seen as crucial. A redesign of the cab makes it more comfortable and quieter to operate.
Göksel Güner is managing director of the KOHAG facility in Hanover and he said, “It’s the first of a new generation of machines from Komatsu.” And he explained that performance capabilities have been improved across the board. He added, “You get a 10% saving on fuel consumption on this model.”
Both cooled EGR and DPF systems are fitted to reduce emissions, with these packages already having been proven in Komatsu’s other machines. The system warns the operator when the filter needs regenerating and should the machine be running in an environment where the extra heat this cycle produces is not desirable, it can be delayed until later. The regeneration process burns a little extra fuel to clean the filter, but Komatsu says that this only a small amount and that the fuel savings offered by the engine still result in major reductions in running costs overall.
Power for the machine comes from a Komatsu SAA6D107E-3 diesel rated at 141kW and the PC240-10 weighs from 25.2-26.1tonnes, depending on specifications such as boom and dipper length, bucket size and track pads fitted. Buckets with capacities of up to 1.89m³ are available and the firm offers various application-specific booms and dippers, however a 3m arm and 1m³ bucket are standard. Economy and attachment modes allow the machine to be optimised to its application. The owner can programme the machine to store the operating parameters of up to 10 different attachments (including five breakers), making it easy and quick to switch between work tools.
For the firm’s 90th anniversary year Komatsu’s presence in Europe is strong with its crawler excavators being produced at the Birtley plant in the UK and wheeled loaders and wheeled excavators being manufactured at its KOHAG facility in Hanover, Germany. The plant has itself benefited from a €50 million investment to boost capacity and quality for the products, with new machine tools and a revamp of the production processes.
Komatsu bought a 64% stake in the Hanomag wheeled loader business in 1989 and finally bought out 100% of the business in 2002. Güner said, “Our machines are produced on a regional basis and our plant is the only production facility for wheeled excavators.”
Sales hit US$22 billion for Komatsu in 2010, with turnover boosted by the firm’s strong presence in the growing Chinese market. The firm’s hybrid excavator is a key machine, particularly in China where fuel costs are high. Over 1,000 hybrid excavators have now been built by Komatsu, the majority of which have been the first generation model. The hybrid excavator comes into its own for applications such as truck loading, where the regenerative slew braking system charges up the capacitor and Güner said that as a result, the HB215 offers distinct performance gains over comparable 21tonne class excavators in such operating cycles. He said, “In this machine you’re saving 25% on fuel.”
The HB215 has a smaller engine than a comparable 21tonne excavator and supplements its power for high speed slewing in truck loading applications by using electrical power stored in the capacitor. Güner said that the machine is at its most efficient in loading applications with 90-180° slew cycles, “You regenerate power every time you stop slewing.”
Katsumi Kano is Komatsu’s product specialist in charge of the HB215 for Europe and he said that the capacitor holds sufficient charge for the motors to power around four slew cycles. Sourcing a suitable capacitor was a problem and he said, “No manufacturer makes one in this size so we make all the hybrid components ourselves.”
The system is designed to operate in climates ranging from -25°C up to 45°C and these purpose-built components are well-proven. Some of Komatsu’s first generation hybrid machines have clocked over 10,000 operating hours and are still running with no problems. A capacitor was used in the HB215 to store electrical power as it allows for efficient and fast discharging and recharging and is also far more compact and longer lasting than a battery pack. The diesel delivers 110kW and the machine weighs in at 21.2tonnes in standard configuration, while it can be fitted with buckets of up to 1.36m³ capacity.
The new D65 dozer comes with a DPF system to help it meet the emissions standards, which regenerates at around 4,500 operating hours.
Hydrostatic steering and a large colour monitor help to make the machine easy to operate. Connections for the
All the new Komatsu machines have the latest version of the KOMTRAX satellite monitoring package also. This allows machine owners to track operating parameters remotely, employ geo-fencing if required and even track stolen machines. Service schedules and machine functions can be tracked remotely and maintenance intervals planned more effectively, so as to reduce downtime and maximise utilisation. Users can also identify problems before they become serious, download software upgrades, troubleshoot and order replacement parts from main dealers when required.
The 35tonne L250G wheeled loader features much of the rear chassis components from the existing L220 but has a 6.9m³ bucket as standard, z-bar linkage and a higher breakout. Designed for face working or truck loading, the machine offers increased productivity over Volvo CE’s own L220 or other rival models according to the firm.