The latest road marking systems from leading manufacturers are in demand in Europe, Africa, the Middle East and South America. Guy Woodford reports
Ennis-Flint recently saw its Third Generation Waterborne Fast Dry Paint with low VOC applied on a Portuguese motorway by Trafiurbe and F.L Gaspar, two of the country’s leading contractors. The line marking is said to have been applied in response to demands from Portuguese authorities for higher specifications of line markings across the country’s highway net
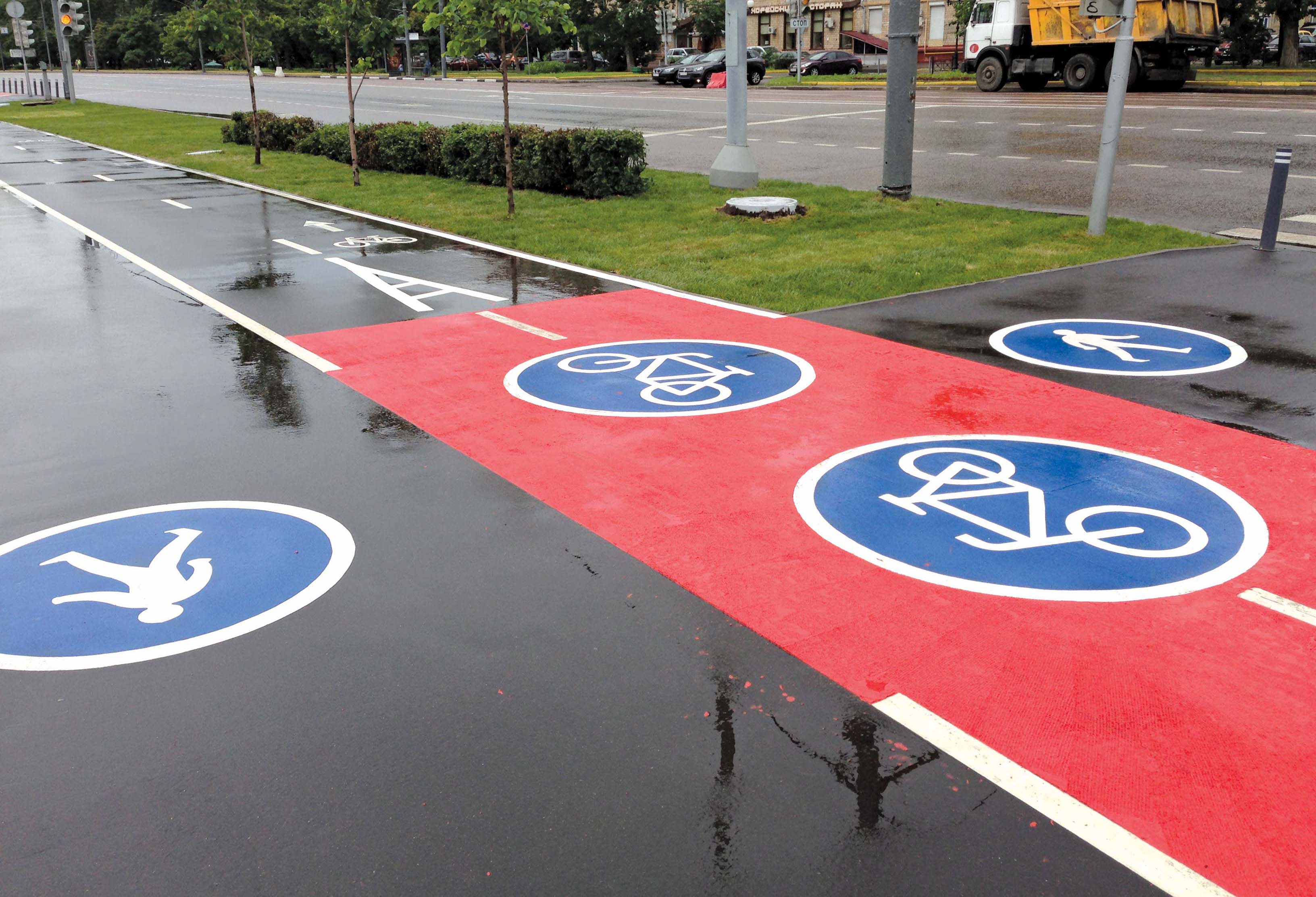
Geveko’s Premark thermoplastic bicycle signs, arrows and pedestrian signs are being used to improve conditions for cyclists and pedestrians in Moscow
The latest road marking systems from leading manufacturers are in demand in Europe, Africa, the Middle East and South America. Guy Woodford reports
Ennis-Flint recently saw its Third Generation Waterborne Fast Dry Paint with low VOC applied on a Portuguese motorway by Trafiurbe and F.L Gaspar, two of the country’s leading contractors. The line marking is said to have been applied in response to demands from Portuguese authorities for higher specifications of line markings across the country’s highway network; it was tested 30 days after first application by1408 Brisa, one of the world’s largest tolled motorway operators and the largest transport infrastructure company in Portugal. Ennis-Flint’s water-based paint measured at 400mc/lux/m². A type II result can also be achieved if the paint is applied with a different specified grade of glass bead.
A fast dry no pick up time at 25°c (1 minute) was said to have allowed Trafiurbe and F.L Gaspar to apply long runs of the material resulting in less disruption on the highway and reduced traffic management costs.
The Third Generation Waterborne Fast Dry Paint is manufactured by Ennis-Flint in compliance with TTP-1952E. The paint is also suitable for use in airports as it is approved by the2423 Federal Aviation Administration (FAA) and is also in compliance with International Civil Aviation Organisation (ICAO) specifications.
In August 2013, Ennis-Flint opened a new warehouse in Lisbon which now stocks large volumes of waterborne paint and other road marking products allowing quicker distribution to the European and North African markets.
PROMAX has been busy over recent months selling its SP60, CF03, and CFO2 thermoplastic road marking manufacturing plants to customers in Brazil (SP60), Iran (CF03 and SP60), Qatar (CF03), USA (SP60), Saudi (CF02), Turkey (CF02), Lithuania (CF02), and Romania (CF02). Some of the plants have been delivered, while others remain in production.
The Danish firm has also been busy installing a number of its SP60, CF03, CF02 factories in other customer facilities in Spain, Romania, Ghana, Kenya and the US.
The PROMAX CF02 plant is said to be aimed at firms looking for a rapid return on their investment through the production of up to 1.5tonnes/hour of quality thermoplastic road marking. Designed as a modular system so it can be installed and put into operation in just two working days, the CF02 factory’s compact design means that it can be installed in the smallest manufacturing facilities.
Basco Products, based in Nairobi, Kenya recently took delivery of a CF02 factory. Company director Bipin Shah said, “We have been importing the thermoplastics and still do so, however the costs and managing the demand and supply issue was a challenge, so we decided to manufacture locally. This enables us to offer a locally manufactured product according to requirement.”
Bipin said that the thermoplastic road marking produced by the CF02 factory would be ideal for customers across the African continent. “Initially we are focussing on the Kenyan and the Ugandan market, later on, once we enhanced the capacity, we will be entering the markets of Rwanda, Burundi, Democratic Republic of Congo and Tanzania.”
Said to be installable and made operational by specialist PROMAX staff within a fortnight, PROMAX’s SP60 factory can manufacture up to 1,200 ready-made thermoplastic sheets over an eight-hour period. To reach this output level, PROMAX has developed a generation of thermoplastic preheaters. The inner top and bottom surface temperature of the heater are said to be kept equal, without any use of mechanical oil circulation in the transfer oil jacket. This innovative preheater coupled with advanced thermoplastic chemistry makes it possible to blend and apply the thermoplastic at a consistent low temperature. The concept, says PROMAX, allows the SP60 to produce 14m of thermoplastic sheets a minute, significantly increasing production capacity by doing away with wasted time for extra heating requirements and inconvenient cooling of the thermoplastic prior to application.PROMAX's CF03 thermoplastic plants are said to be equipped with the latest production equipment to ensure a minimum 6tonnes/hour production. PROMAX claims its batch production control and registration systems are the most modern available, guaranteeing stable production of more than 500 various thermoplastic 'recipes'.
A2447 Geveko-DILART-produced 1278 Decomark preformed thermoplastic city map of Barcelona is now guiding tourists and visitors. The culture-rich Catalonian capital’s main streets and main attractions are shown on the 17.9m x 13.4m city map, which uses nine different colours of preformed thermoplastic.
Decomark is a preformed thermoplastic described by Geveko as a durable anti-slip material that provides endless possibilities for creating colourful and creative designs. Decomark is also often used for playground markings, company logos, art and other decorative markings.
Meanwhile, in Moscow Geveko’s Premark is being used as part of efforts to improve conditions for cyclists and pedestrians in Russia’s capital. Premark preformed thermoplastic bicycle signs, arrows and pedestrian signs have been installed on the first recently opened 2kms of an 18km bicycle lane between the city’s two biggest parks - Gorky Park and Park Kultury. The bicycle markings are used to guide road users in the traffic. Premark is also due to be used on some of the rest of the 18km route.
Innovative Borum
173 Borum has introduced a new air dryer system for all its line marking machines ensuring proper glass bead application for enhanced retroreflectivity during line marking works.
The Danish firm’s system removes moisture from the air before it enters the bead tank, preventing the beads from blocking in the tank. This is said by Borum to be particularly useful in geographical areas that experience high humidity levels.
The air dryer system is said to be adapted from truck/bus brake and suspension air supply. It’s made to cope better with ‘polluted’ compressor air than standard industrial air filters and water separators.
Turning on a control valve via a signal from the Borum LineMaster computer allows the bead tank’s air dryer filter to regenerate over a five to 10-second period, before it is ready to use again.
Borum has also incorporated a new bead alarm on all its line marking equipment. It consists of a sensor mounted on the bead gun, which triggers the alarm when bead flow is disrupted. The bead alarm can be connected to the Borum LineMaster computer – with software likely to require updating during retrofitting.
The LineMaster will show an alarm when the bead gun is on and no beads are leaving it. If one of the bead guns is supposed to open and the sensor does not detect bead flow within 0.5 seconds, the alarm will start. Machine operators will be able to hear a beep from the horn in the LineMaster and see the alarm in the display. You can also set the alarm to stop line marking automatically when the alarm has been active for more than 1.5 seconds.
Philippe Lambert, manager of ETS Lambert Marquage, a road construction and public works company based near Liege in Belgium, is awaiting delivery of a Borum Master (BM) 3000 road marking machine with new air dryer system and bead alarm technology, to replace the firm’s BM 350-2 machine model.
“We had the air dryer system fitted onto the BM 350-2 and it worked well,” said Lambert. “Before that we often had problems with moisture getting into the bead tank. The glass beads were getting really wet.
“I think the bead alarm on the BM 3000 will be very useful. As a road marking machine operator you have to make sure that you put a good quantity of glass beads onto the marking. You may be distracted, and if there’s a block in the bead gun, you might not be aware that no beads are coming out without the alarm going off.”
Lambert said that the BM 3000, like the company’s BM350-2 machine, would mostly be used on road marking projects in southern Belgium.
The latest innovations for Borum road marking machines were due to be presented at244 Intertraffic in Amsterdam, 25-28 March 2014. Equipment on show on the company stand was set to include the Borum LineMaster computer; the BM 5000 SP DL line marking machine for Dot'n'Line as well as spray-plastic application; the BM CP 250-2 line marking machine for application of two-component material 98:2, multifunctional for spray, extrusion, agglomerate and dot application; a Borum trailer with thermoplastic preheater, power station and filling system to be used for manual work or filling of a small machine; and a Borum line eraser.
Ennis-Flint recently saw its Third Generation Waterborne Fast Dry Paint with low VOC applied on a Portuguese motorway by Trafiurbe and F.L Gaspar, two of the country’s leading contractors. The line marking is said to have been applied in response to demands from Portuguese authorities for higher specifications of line markings across the country’s highway network; it was tested 30 days after first application by
A fast dry no pick up time at 25°c (1 minute) was said to have allowed Trafiurbe and F.L Gaspar to apply long runs of the material resulting in less disruption on the highway and reduced traffic management costs.
The Third Generation Waterborne Fast Dry Paint is manufactured by Ennis-Flint in compliance with TTP-1952E. The paint is also suitable for use in airports as it is approved by the
In August 2013, Ennis-Flint opened a new warehouse in Lisbon which now stocks large volumes of waterborne paint and other road marking products allowing quicker distribution to the European and North African markets.
PROMAX has been busy over recent months selling its SP60, CF03, and CFO2 thermoplastic road marking manufacturing plants to customers in Brazil (SP60), Iran (CF03 and SP60), Qatar (CF03), USA (SP60), Saudi (CF02), Turkey (CF02), Lithuania (CF02), and Romania (CF02). Some of the plants have been delivered, while others remain in production.
The Danish firm has also been busy installing a number of its SP60, CF03, CF02 factories in other customer facilities in Spain, Romania, Ghana, Kenya and the US.
The PROMAX CF02 plant is said to be aimed at firms looking for a rapid return on their investment through the production of up to 1.5tonnes/hour of quality thermoplastic road marking. Designed as a modular system so it can be installed and put into operation in just two working days, the CF02 factory’s compact design means that it can be installed in the smallest manufacturing facilities.
Basco Products, based in Nairobi, Kenya recently took delivery of a CF02 factory. Company director Bipin Shah said, “We have been importing the thermoplastics and still do so, however the costs and managing the demand and supply issue was a challenge, so we decided to manufacture locally. This enables us to offer a locally manufactured product according to requirement.”
Bipin said that the thermoplastic road marking produced by the CF02 factory would be ideal for customers across the African continent. “Initially we are focussing on the Kenyan and the Ugandan market, later on, once we enhanced the capacity, we will be entering the markets of Rwanda, Burundi, Democratic Republic of Congo and Tanzania.”
Said to be installable and made operational by specialist PROMAX staff within a fortnight, PROMAX’s SP60 factory can manufacture up to 1,200 ready-made thermoplastic sheets over an eight-hour period. To reach this output level, PROMAX has developed a generation of thermoplastic preheaters. The inner top and bottom surface temperature of the heater are said to be kept equal, without any use of mechanical oil circulation in the transfer oil jacket. This innovative preheater coupled with advanced thermoplastic chemistry makes it possible to blend and apply the thermoplastic at a consistent low temperature. The concept, says PROMAX, allows the SP60 to produce 14m of thermoplastic sheets a minute, significantly increasing production capacity by doing away with wasted time for extra heating requirements and inconvenient cooling of the thermoplastic prior to application.PROMAX's CF03 thermoplastic plants are said to be equipped with the latest production equipment to ensure a minimum 6tonnes/hour production. PROMAX claims its batch production control and registration systems are the most modern available, guaranteeing stable production of more than 500 various thermoplastic 'recipes'.
A
Decomark is a preformed thermoplastic described by Geveko as a durable anti-slip material that provides endless possibilities for creating colourful and creative designs. Decomark is also often used for playground markings, company logos, art and other decorative markings.
Meanwhile, in Moscow Geveko’s Premark is being used as part of efforts to improve conditions for cyclists and pedestrians in Russia’s capital. Premark preformed thermoplastic bicycle signs, arrows and pedestrian signs have been installed on the first recently opened 2kms of an 18km bicycle lane between the city’s two biggest parks - Gorky Park and Park Kultury. The bicycle markings are used to guide road users in the traffic. Premark is also due to be used on some of the rest of the 18km route.
Innovative Borum
The Danish firm’s system removes moisture from the air before it enters the bead tank, preventing the beads from blocking in the tank. This is said by Borum to be particularly useful in geographical areas that experience high humidity levels.
The air dryer system is said to be adapted from truck/bus brake and suspension air supply. It’s made to cope better with ‘polluted’ compressor air than standard industrial air filters and water separators.
Turning on a control valve via a signal from the Borum LineMaster computer allows the bead tank’s air dryer filter to regenerate over a five to 10-second period, before it is ready to use again.
Borum has also incorporated a new bead alarm on all its line marking equipment. It consists of a sensor mounted on the bead gun, which triggers the alarm when bead flow is disrupted. The bead alarm can be connected to the Borum LineMaster computer – with software likely to require updating during retrofitting.
The LineMaster will show an alarm when the bead gun is on and no beads are leaving it. If one of the bead guns is supposed to open and the sensor does not detect bead flow within 0.5 seconds, the alarm will start. Machine operators will be able to hear a beep from the horn in the LineMaster and see the alarm in the display. You can also set the alarm to stop line marking automatically when the alarm has been active for more than 1.5 seconds.
Philippe Lambert, manager of ETS Lambert Marquage, a road construction and public works company based near Liege in Belgium, is awaiting delivery of a Borum Master (BM) 3000 road marking machine with new air dryer system and bead alarm technology, to replace the firm’s BM 350-2 machine model.
“We had the air dryer system fitted onto the BM 350-2 and it worked well,” said Lambert. “Before that we often had problems with moisture getting into the bead tank. The glass beads were getting really wet.
“I think the bead alarm on the BM 3000 will be very useful. As a road marking machine operator you have to make sure that you put a good quantity of glass beads onto the marking. You may be distracted, and if there’s a block in the bead gun, you might not be aware that no beads are coming out without the alarm going off.”
Lambert said that the BM 3000, like the company’s BM350-2 machine, would mostly be used on road marking projects in southern Belgium.
The latest innovations for Borum road marking machines were due to be presented at