Tight deadlines, inclement weather, long travel times and inadequate tank capacity are a few of the challenges facing road marking contractors. But with the right equipment and careful planning, road marking contractors can optimise their investment and uptime, says Borum Industri. "Timing plays a key role in every road marking job. On new roads it is the last part of a project, and if there have been delays along the way, road marking contractors are under pressure to complete the job fast. On existing roa
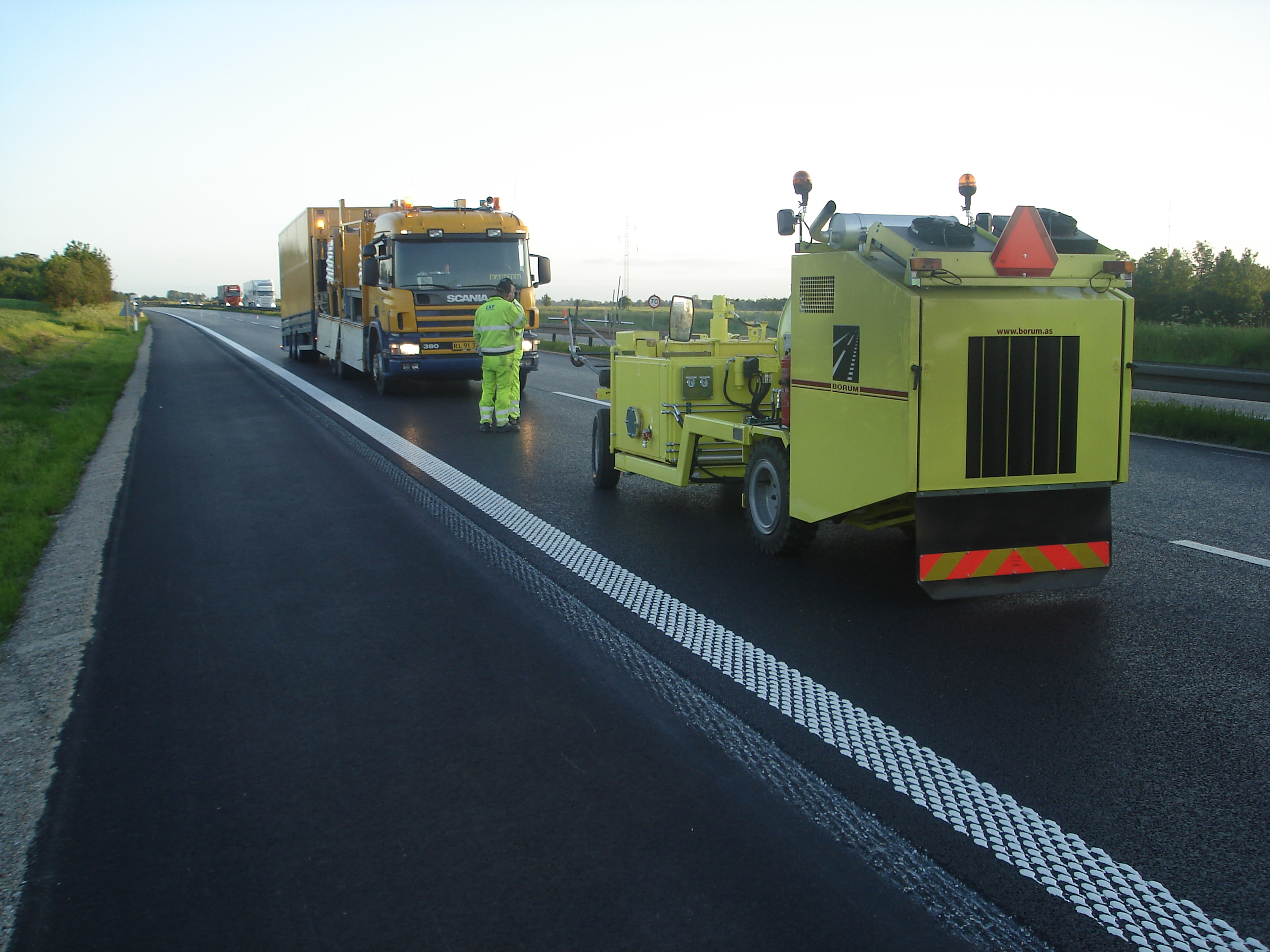
Borum is now making more machines with a new dot and line system in response to demand
Tight deadlines, inclement weather, long travel times and inadequate tank capacity are a few of the challenges facing road marking contractors.
But with the right equipment and careful planning, road marking contractors can optimise their investment and uptime, says173 Borum Industri.
"Timing plays a key role in every road marking job. On new roads it is the last part of a project, and if there have been delays along the way, road marking contractors are under pressure to complete the job fast. On existing roads, remarking can mean diversions for motorists, and at worst temporary road closures," says the Danish road marking equipment manufacturer.
With today's high traffic density, completing the job quickly is a must.
"To help my customers choose the right equipment, there are a number of important points to consider. One of the first, maybe surprisingly, is maintenance, which is a very important uptime parameter," says Lisbeth Knudsen, area sales manager at Borum.
In early 2010, Borum launched its LineMaster road marking computer, which is "designed to help operators control all road marking tasks, from line application and pre-marking to reporting and invoicing." Borum points out that tank capacity is alpha and omega for uptime and profitability, with road marking machines now so effective that they can empty a material tank very quickly.
"If using thermoplastic, this can mean having to wait for more material to melt and reach the correct temperature if the heating tank capacity for feeding the machine isn't large enough.
"Operators have told us that they can spend up to 25% of their daily working hours waiting for material to melt. But there are many small things that can be done do to help optimise investments." These include buying more melting capacity if the appropriate melting capacity is not on the feeder truck, and maximising current melting capacity, for example, by half emptying the tank and using the remaining hot material to melt incoming cold material.
But with the right equipment and careful planning, road marking contractors can optimise their investment and uptime, says
"Timing plays a key role in every road marking job. On new roads it is the last part of a project, and if there have been delays along the way, road marking contractors are under pressure to complete the job fast. On existing roads, remarking can mean diversions for motorists, and at worst temporary road closures," says the Danish road marking equipment manufacturer.
With today's high traffic density, completing the job quickly is a must.
"To help my customers choose the right equipment, there are a number of important points to consider. One of the first, maybe surprisingly, is maintenance, which is a very important uptime parameter," says Lisbeth Knudsen, area sales manager at Borum.
In early 2010, Borum launched its LineMaster road marking computer, which is "designed to help operators control all road marking tasks, from line application and pre-marking to reporting and invoicing." Borum points out that tank capacity is alpha and omega for uptime and profitability, with road marking machines now so effective that they can empty a material tank very quickly.
"If using thermoplastic, this can mean having to wait for more material to melt and reach the correct temperature if the heating tank capacity for feeding the machine isn't large enough.
"Operators have told us that they can spend up to 25% of their daily working hours waiting for material to melt. But there are many small things that can be done do to help optimise investments." These include buying more melting capacity if the appropriate melting capacity is not on the feeder truck, and maximising current melting capacity, for example, by half emptying the tank and using the remaining hot material to melt incoming cold material.